Ever wonder how much 3D printing materials cost? Read on to learn all about different materials and their prices.
In any production process, the choice of the material not only is the key to creating a suitable and durable product but also ensures successful fabrication. Moreover, the cost of the material can have the most significant impact on the final cost of the product.
3D printing is known to be employed for diverse purposes, and this is only possible due to the various materials and techniques available. This availability, however, comes at a cost, which can be quite steep.
In this article, we’ll provide an overview of common materials used across three different 3D printing technologies, giving you a sense of the typical price range for each along the way.
Technology & Material Overview
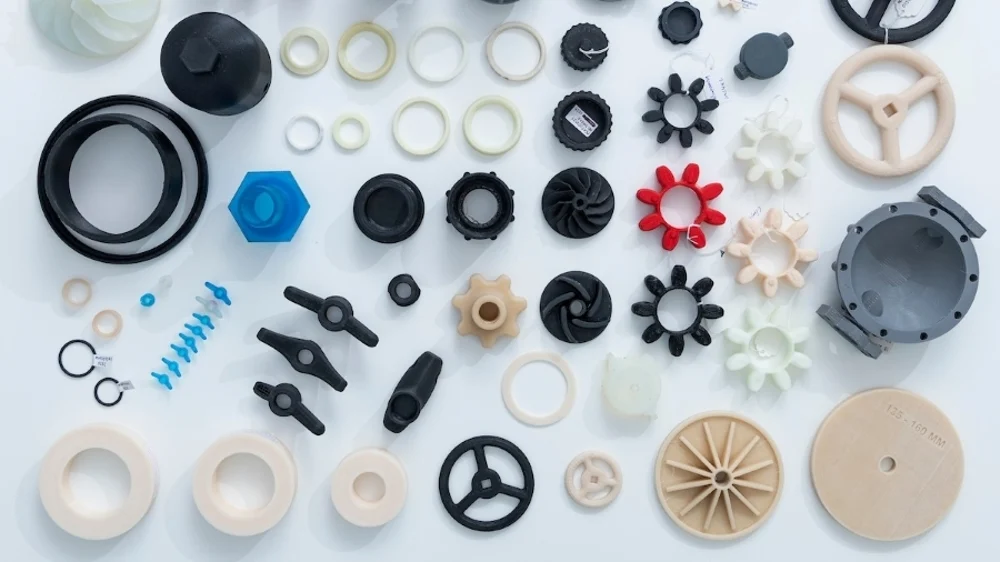
3D printing comprises many different technologies, and each technique processes materials in different ways. For this reason, the feedstock materials vary greatly in nature and formats: filaments, metal wires, resins, powders, paper, and even living cells.
The current selection of 3D printing technologies and materials is larger than ever and continues to grow. However, for this article, we’ll focus on three popular 3D printing technologies:
- Material extrusion (FDM)
- Vat photopolymerization (SLA, DLP, LCD)
- Powder bed fusion (SLS, SLM, DMLS, EBM)
In the next sections, the most common materials employed by each technique will be described and rough cost estimations will be given.
FDM Printing
FDM, or fused deposition modeling, is the most popular material extrusion process in 3D printing. In almost all cases, it uses thermoplastic materials as feedstock in long filaments that are rolled up and packed in spools.
Generally speaking, the cost of filament material for FDM is mostly affected by the type of polymer used. The overall quality of the material, which includes color and dimensional stability, is also decisive in the final cost of each filament spool.
PLA
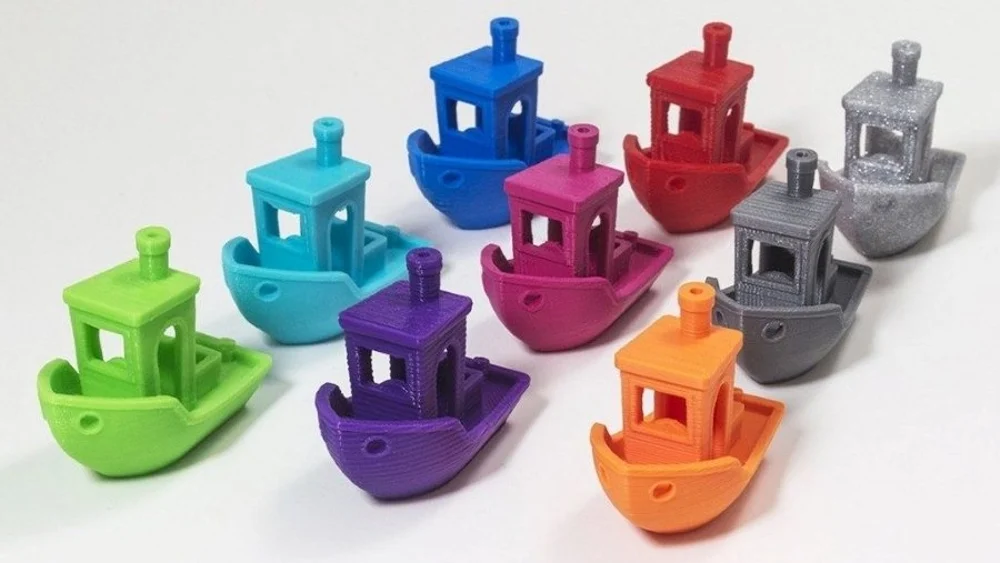
PLA stands for polylactic acid, a biodegradable polymer made from corn starch or sugar cane. PLA is no doubt the most popular filament material for FDM 3D printers, being relatively easy to use and displaying appealing aesthetics once printed.
This material is easily pigmented, being available in a huge variety of colors and tones. In terms of mechanical properties, it has decent strength and hardness, perhaps a bit too tough to post-process parts with sanding when compared to other materials.
Its biggest disadvantage, however, is the lower melting point. PLA printed parts are known to deform when left inside vehicles parked under the sun on a hot day. It’s also a fairly brittle material and is better employed for aesthetic or prototyping applications rather than functional parts that will be submitted to stress.
PLA also comes in different blends and grades, but the standard filaments cost between $15 and $20 per kg on average. You can find special filaments like the cool-looking silk PLA for around $30, whereas color-changing PLA could set you back at something like $40 per kg.
- Average price range: $15-$20 per kg
ABS
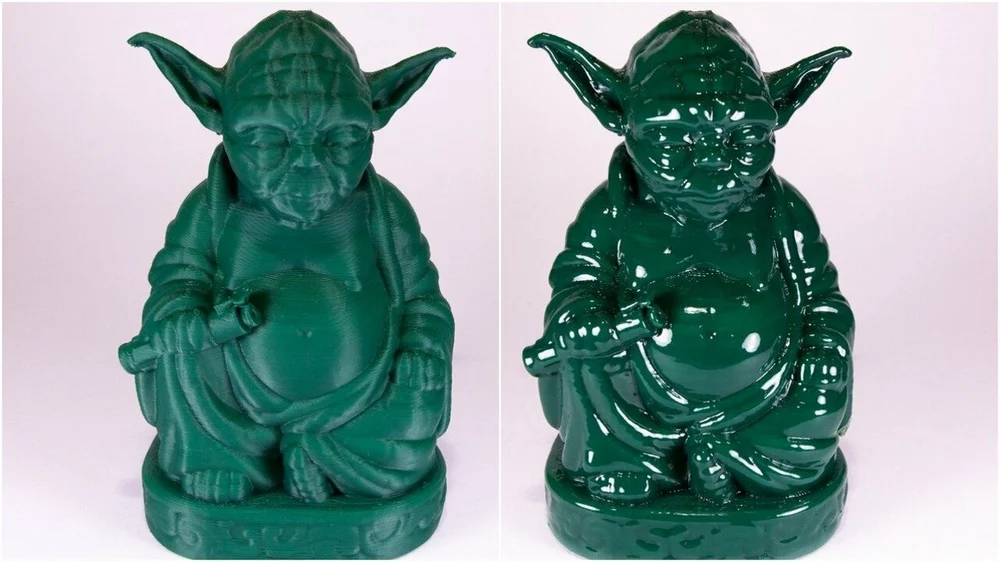
ABS is one of the most used plastics worldwide, as its frequently used in injection molding processes. The acrylonitrile butadiene styrene plastic is obtained from petroleum, and it’s known to release foul-smelling and toxic fumes when used for 3D printing.
The ABS used in 3D printing experiences significant thermal shrinking during cooling, making it very difficult to print without a heated build plate. This thermal cooling can cause warping and, alongside its fume toxicity, it’s highly recommended to print in enclosed machines.
However, 3D printed ABS parts have great mechanical properties. They’re durable, heat resistant, and strong enough for plenty of functional applications. ABS is also easier to sand and can be smoothed by chemicals that create a shiny flawless surface appearance.
Finally, ABS is considered to be a relatively cheap material for FDM 3D printing. A 1-kg spool of good ABS can be found for between $20 and $35, including low-odor versions like Polymaker’s PolyLite ABS.
- Average price range: $20-$35 per kg
PETG
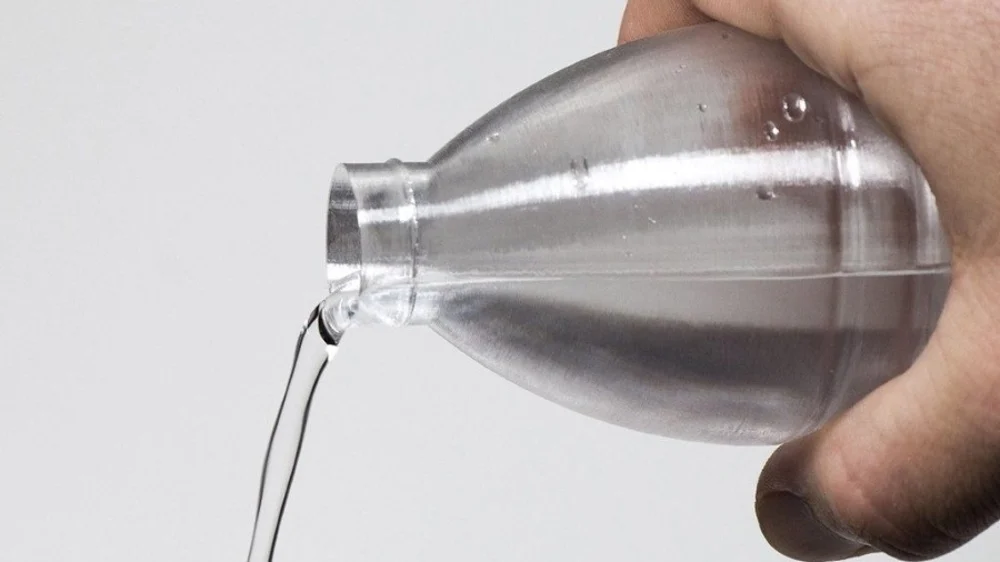
PETG is a close relative to the PET plastic used in soda and water bottles. The ‘G’ refers to glycol, which is partially replaced with cyclohexanedimethanol (CHDM) to create a material more suitable for 3D printing.
This material is known as a good alternative to ABS in terms of strength, temperature resistance, and relative ease of use. It can be printed without a heated bed and is a little more flexible than ABS, providing better impact resistance overall.
PETG is also more chemically resistant and often called a food-safe material by manufacturers, although 3D printing with it makes things a little more complicated in this regard. This material is prone to more stringing and blobs, though, so a bit of calibration is often recommended.
One might think that PETG would be more expensive given the improved characteristics, but that’s no longer the case. A decent quality PETG filament costs around $20 to $25 per kg, with higher-end materials costing up to $55, like MatterHackers Pro PETG.
- Average price range: $20-$25 per kg
HIPS & PVA
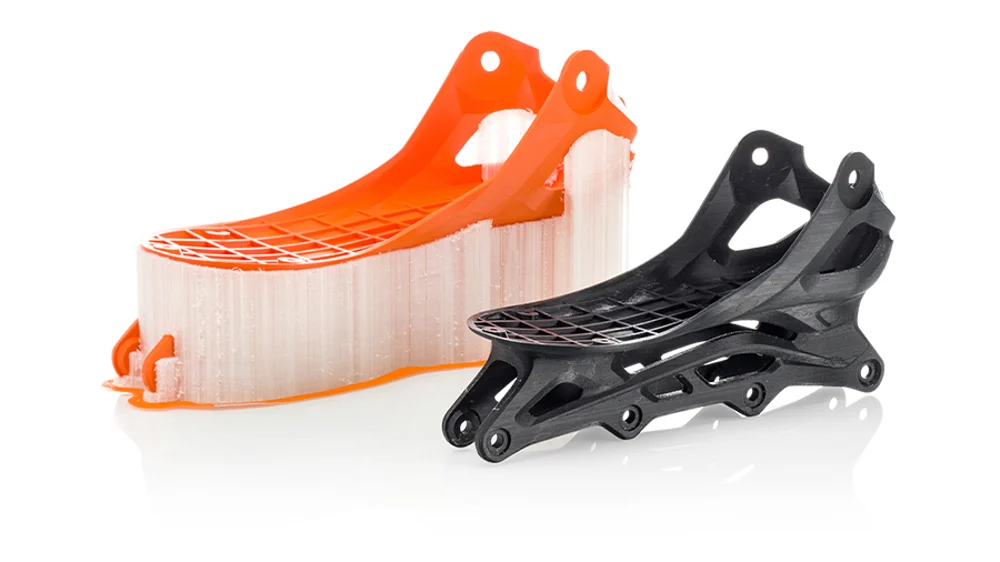
3D printing works in a way that some overhang regions require a material to adhere to during the layer deposition that will be subtracted later on. These support structures are often made of the same material that’s being used for the object being printed.
However, with the use of a dual extrusion machine, another kind of support can be used. Known as dissolvable supports, the material used for structuring the prints can be dissolved in a liquid after the part has been printed. This has many benefits, including the smooth finish that these supports leave on the interface with the object, as opposed to the rough ones that can be left by regular support structures.
Here enters HIPS and PVA. While these materials can be used as a primary 3D printing material (HIPS, mostly) they’re both more commonly used as soluble supports in dual extrusion machines.
HIPS has similar properties to ABS, including the printing temperature, which makes them a perfect match: ABS as primary material and HIPS as support. A spool of HIPS can be found between $20 to $60 per kg, whereas the liquid used for dissolving (Lemonesol) is priced at around $20 for a 500-ml bottle.
PVA, on the other hand, is best paired with PLA due to the similar temperature melting point. This material, however, is water-soluble, not requiring special chemicals for dissolving. This is great because PVA is a quite expensive filament, costing between $60 to $130 per 1-kg spools.
- Average price range: $20-$60 per kg (HIPS), $60-$130 per kg (PVA)
Flexible Materials
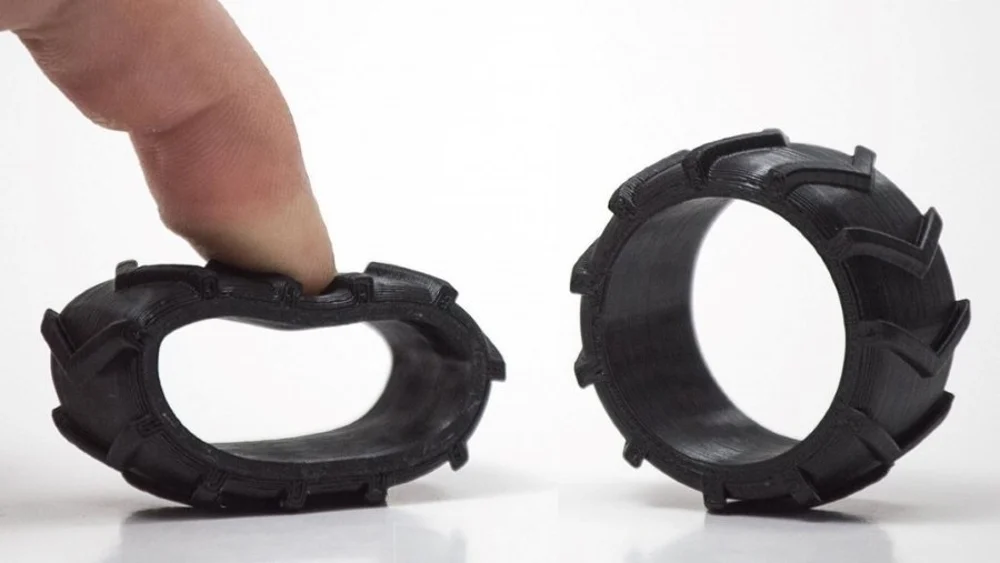
Choosing the right material is crucial for getting a part that fulfills its function, and sometimes it’s not strength that’s required but flexibility. The so-called flexible materials in 3D printing refer to a class of elastic polymers that can be properly 3D printed since rubber can’t.
In more technical terms, this category of materials is known as thermoplastic elastomers (TPEs). It includes polymers such as TPU, TPC, TPA, soft PLA, and it’s even common to find flexible filaments marketed as TPE.
In the end, all of these filaments have their own characteristics but share the rubber-like property of flexible materials. Usually, they’re differentiated by their Shore hardness, a standardized property used to classify rubbers and semi-rigid plastics.
With all that said, these flexible filaments can be used for multiple purposes, from RC car tires to small dampeners, and even shoes. Flexible filament comes at a high price tag, though: from $65 up to $180 per kg. The 85A Shore hardness NinjaFlex filament is one of the most popular, listing at around $85 per kg.
- Average price range: $65-$180 per kg
Composite Materials
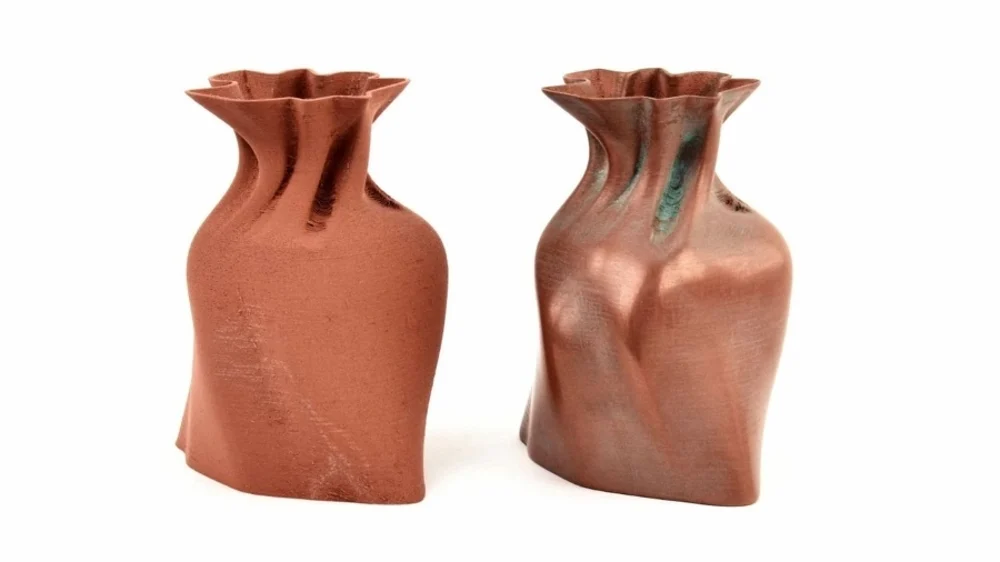
Composite materials are a blend of two materials with different physical and chemical properties. For FDM 3D printing, this is usually done by adding small particles of a non-polymer material to common regular filaments, such as PLA and ABS.
The non-polymer material must be very small particles to avoid clogging nozzles. This is why these materials usually show the mechanical properties of the base polymer. For instance, a metal-filled PLA will usually display strength and heat resistance very similar to regular PLA.
However, composite filaments are entirely different in terms of aesthetics, and this is perhaps what’s most appealing about them. Given the highly diverse number of additives such as wood fibers, metal, carbon fiber, magnetic materials, and even marble, the average cost for these types of filaments ranges from about $20 per kg to well over $600 per kg!
Here, the difference in price comes down to the uniqueness of the additive and the overall quality of the filament. Perhaps the most sought-after additives for filaments are wood and carbon fiber, ranging from around $30 for a 1-kg spool of Hatchbox Wood filament to Protoplant’s carbon fiber PLA at $60 per kg.
- Average price range: $20-$600 per kg
VAT POLYMERIZATION
Vat Polymerization is popularly known within the 3D printing world as resin 3D printing. This was the first 3D printing technology ever, and it works by curing layers of material with a light source. While there are many different technologies, all of them use the same kind of material, known as thermosets.
Thermosets are also polymers, but what sets them apart from thermoplastics is that they don’t melt but instead become solid through light-curing. These somewhat toxic resins’ prices are highly dependent on the composition of the material, the overall quality, and whether they’re water-washable or not.
Standard Resin
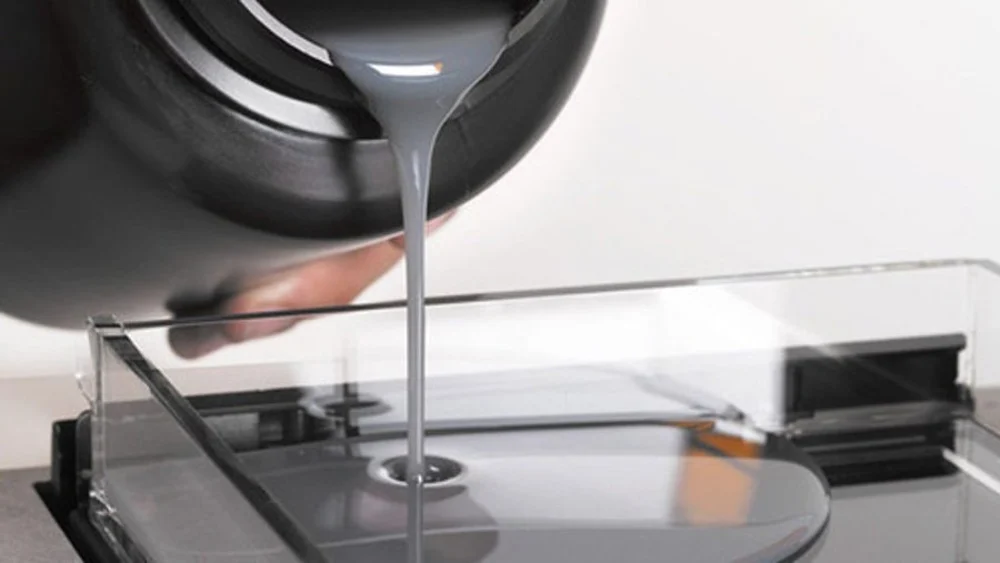
While vat polymerization can produce very high-resolution prints, one big drawback is the cost of the resin. Standard 3D printing resin for these machines can vary quite widely, but on average, it costs approximately $50 per kg.
With that said, one should also consider the cost of the cleaning agent needed. Resin 3D prints require extra post-processing steps that include the removal of residual liquid material prior to a final curing step, and that’s usually done with isopropyl alcohol (IPA).
However, there are also water-soluble resins on the market, which can cost up to $70 per kg like eSun’s water-washable resins. Besides reducing the risks associated with storing flammable liquids like IPA, water is free to use and not harmful to our skin like high-purity alcohol.
- Average price range: $50-$70 per kg
Tough Resin
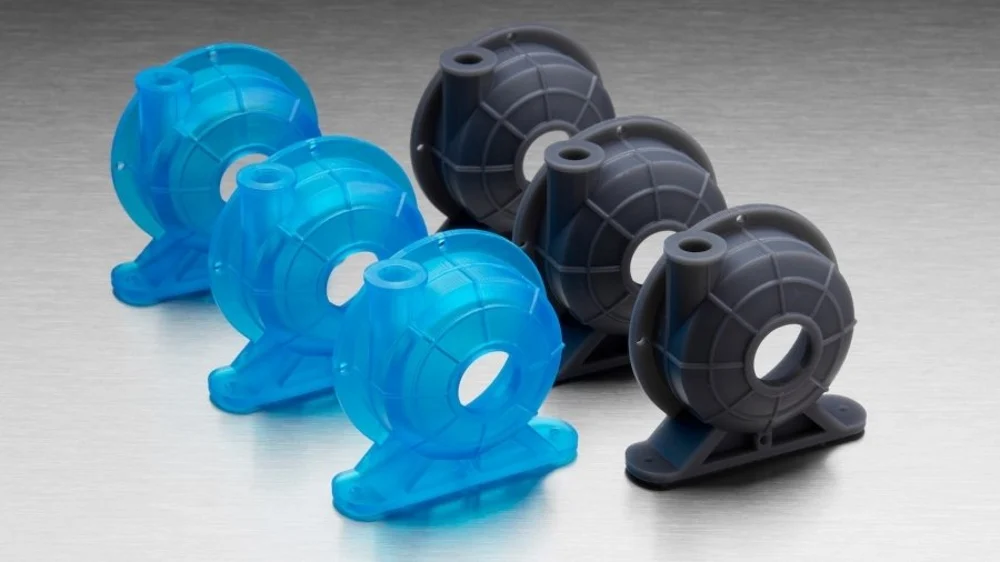
Standard resin for vat polymerization is relatively crumbly and fragile when compared to FDM 3D printing materials. This is the main reason why we associate resin 3D printing with more aesthetic and artistic purposes rather than functional ones.
However, there are resins specifically designed for creating robust and durable parts, which are popularly known as tough resins. These materials generally have mechanical properties comparable to ABS while being only slightly more brittle overall.
3D printing with tough resin can be a little more challenging than printing with standard resin because the parts adhere more strongly to the build platform and usually require longer post-curing processes. Yet, they usually perform as intended and sometimes even outperform FDM parts.
A 1-kg bottle of tough resin can cost as little as $60 per kg for eSun’s Hard-Tough resin or up to $175 per kg like Liqcreate Strong-X.
- Average price range: $60-$175 per kg
Flexible
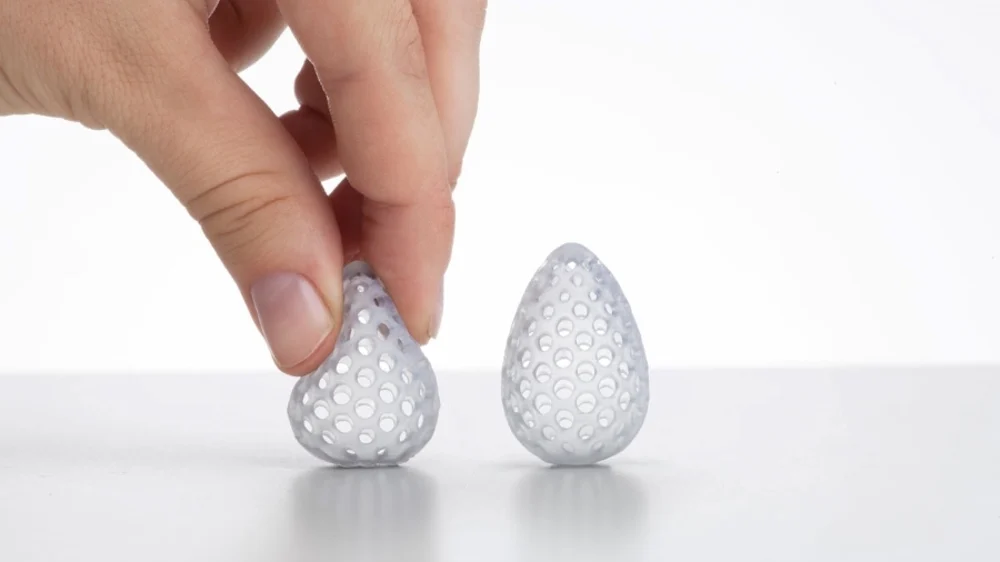
Vat polymerization can also create 3D print parts with rubber-like properties. Flexible resins can be used to create parts with Shore hardness from 50 to 90A without too much hassle, although make sure the resin is adequate for your 3D printer’s specific technology (SLA, DLP, LCD).
Flexible resins are also known to be mixed with standard resin to improve mechanical properties by reducing brittleness. In terms of pricing, you can find a 1-kg bottle starting around $65 per kg for Siraya Tech Tenacious, but prices up to $150 or even $200 per kg are not unheard of.
- Average price range: $65-$200 per kg
Specialty Resins
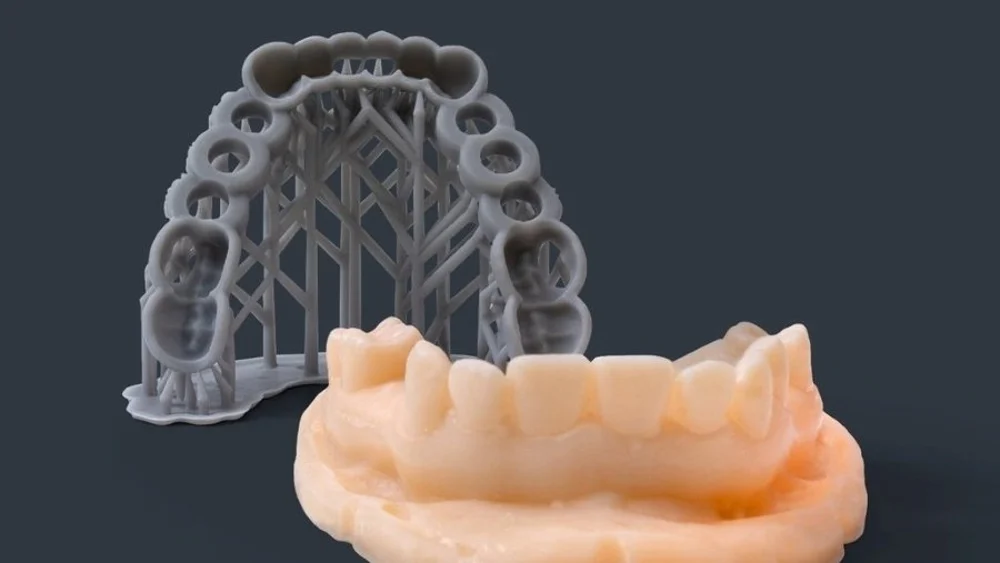
The market for specialty materials in 3D printing is expanding. For resins though, it’s rather focused on two major applications of this technology: jewelry and dental.
Investment casting is the most popular method for creating precious small jewelry parts with 3D printing. The mold for pouring the liquid metal is made with an identical copy of the final part that melts when the metal is cast.
This copy is 3D printed in a castable wax-like resin that provides a smooth finish to the mold and leaves no ash inside. A bottle of castable resin can cost from $75 per kg up to $250 for Formlabs’ Castable Wax 40 Resin.
As for dental, there is a wide array of possible applications of resin 3D printed parts: surgical guides, aligners, temporary teeth, dentures, among others. However, any part that comes in contact with a patient’s mouth requires special biocompatible resins certified by local authorities.
As you can imagine, these resins come at very high costs (for a reason) and also require certified 3D printers to make proper use of them. Prices depend on the final application of parts but 1-liter bottles can reach as high as $500.
- Average price range: $75-$250 per kg
POWDER BED FUSION
The 3D printing technology known as powder bed fusion is one of the most used by different industry sectors to create end-use parts. It works by selectively fusing or melting powder material into several layers with a laser or other heat sources like electron beams.
Today, these processes are mostly referred to by their commercial names. The process known as selective laser sintering (SLS) is often used when processing polymers, whereas selective laser melting (SLM), direct metal laser sintering (DMLS), and electron beam melting (EBM) for metallic parts.
Polymers
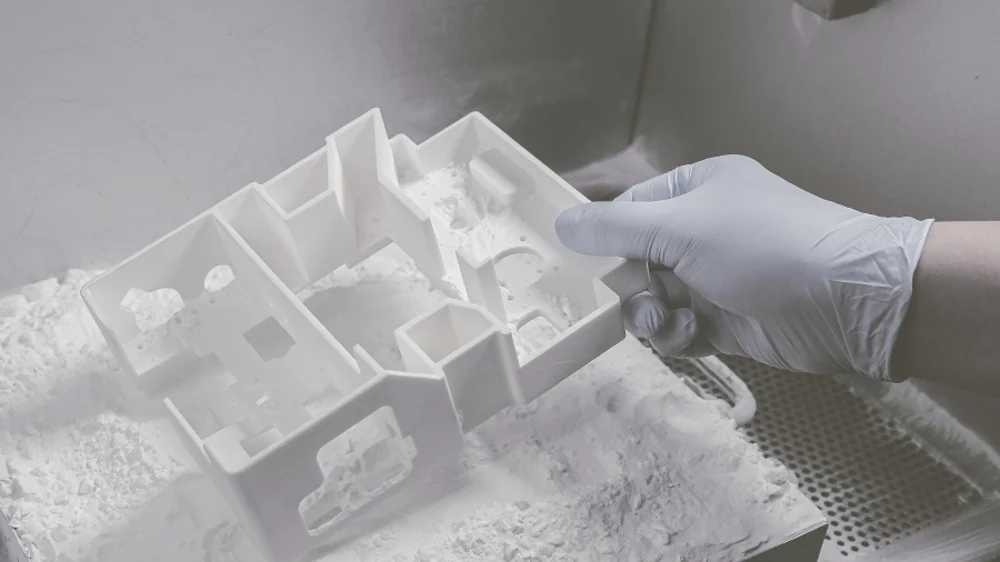
The most used type of polymer powders for SLS is called polyamide, also known as PA, with nylon being the most common representative of this kind of material.
The standard PA powder for SLS is PA 12 nylon, which costs around $150 per kg for industrial-grade powders. Just as with other 3D printing materials, this is an approximation for “standard” powders, which are often used for rapid prototyping purposes.
Naturally, there are more expensive powders that require superb material appearance and properties like PEEK and even flexible TPEs. Given the more industrial nature of these processes, these materials are often proprietary technology and are paired with printing equipment.
- Average price range: $150-$225 per kg
Metals
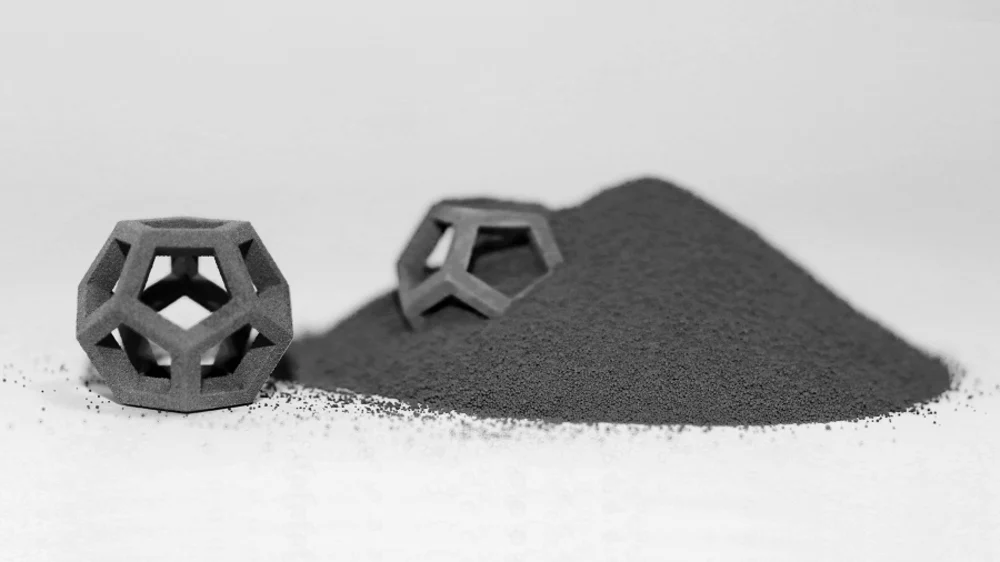
The final 3D printing material that we’ll take a look at is metal powder. While today, metallic parts can be made using different 3D printing technologies, powder bed fusion methods remain the best option for reliable and cost-effective manufacturing.
However, one of the biggest disadvantages of these processes is material cost. Metal powders are created by a process known as atomization, and ensuring the proper size of particles of the powder alone is very costly. Moreover, the metals used for powder bed fusion are high-end, which includes titanium and nickel-based superalloys.
You can expect to pay between $350 and $600 per kg of these special metallic powders, whereas regular stainless steel can be found at around $150 per kg.
- Average price range: $150-$600 per kg