Manufacturing on a Grand Scale?
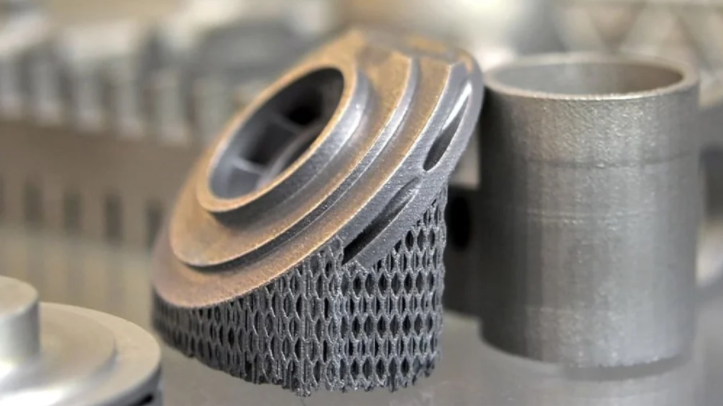
Additive manufacturing is the general term for all manufacturing techniques that create physical objects by successively adding material, usually in a layer-by-layer manner. These technologies differ from traditional methods, which either remove material (machining) or somehow shape it (casting and forging). Of course, the term “additive manufacturing” with another that you’re probably familiar with: 3D printing.
Although the terms additive manufacturing and 3D printing are frequently used interchangeably, the latter is actually just one type of the former. In other words, “additive manufacturing” is a broader term that’s more commonly associated with industrial applications, including the serial production of components.
“3D printing”, on the other hand, has more of a consumer focus. The very nature of the parts made by these two technologies is different: While 3D printing is often used for figurines, decorations, and even small functional parts, additive manufacturing produces molds, components, and end-use products.
Getting Official
In this article, we’ll cover all seven additive manufacturing technologies as categorized by the International Organization for Standardization (ISO/ASTM 52900):
- Vat photopolymerization
- Material extrusion
- Sheet lamination
- Powder bed fusion
- Binder jetting
- Material jetting
- Directed energy deposition
After briefly discussing each processes’ background, we’ll then go over some of its important aspects, like the materials it uses, example industrial applications, and common machines and manufacturers.
Don’t Get Lost
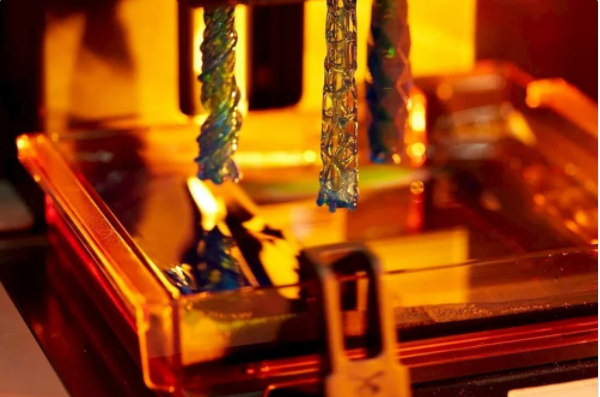
At this point, you may be wondering, where are all the familiar terms like FDM, SLA, and DLP? Don’t worry – they’re still relevant. They’re just going to fall under some of the broader processes we’ll discuss here.
Though many of the following are often only used in professional and industrial contexts, they’re still accessible. If you’re looking to benefit from the advantages of metal printing or material jetting, for example, try a 3D printing service. For the widest variety of materials, check out our 3D printing service marketplace.
Now, let’s get back to these awesome manufacturing techniques.
Vat Photopolymerization
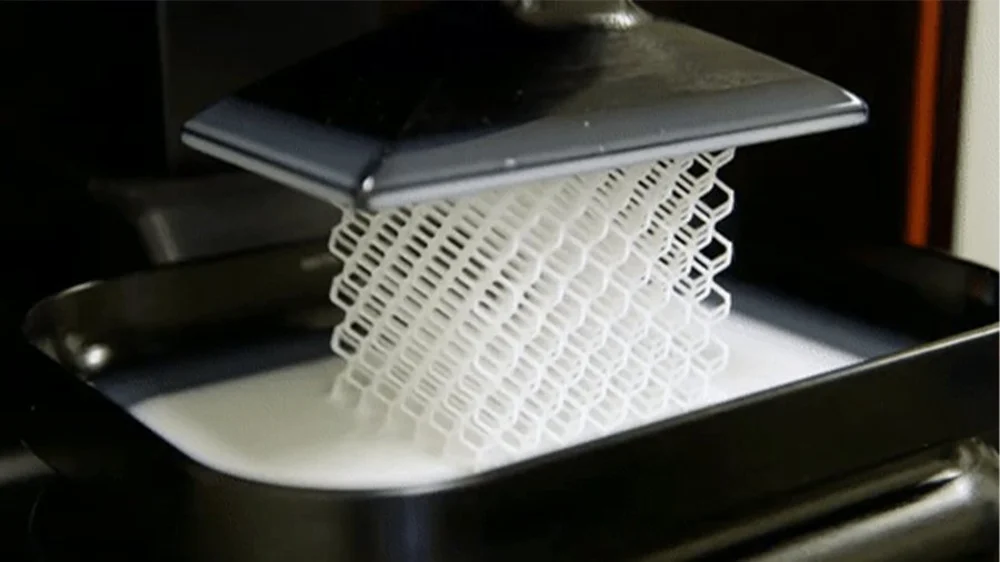
Vat photopolymerization, also known as stereolithography (SLA), is the process by which a liquid is cured by a light source, turning it into a solid. This phenomenon became known as polymerization and was the very first industrial additive manufacturing technology.
SLA was developed in the early 1980s by Chuck Hull, founder of 3D Systems, who then patented the process and took it to market in 1987 with the SLA‐1 machine.
Materials
The photopolymer resins used in vat photopolymerization processes are usually either epoxy- or acrylate-based. While epoxy-based resins require more energy to solidify, they are currently the most used in industrial applications due to their better mechanical and thermal properties. Epoxy resins are also less prone to shrink during processing than acrylate-based resins.
On the other hand, acrylate-based resins are very versatile, ranging from extremely tough to flexible, rubber-like materials. These resins are also more color-stable, so they’re more often used when a specific color is needed.
Common Applications
SLA processes produce very detailed and dimensionally-accurate parts. There’s even a subprocess called “micro-stereolithography”, which handles parts on the nanometric scale and is unmatched in its precision to any other type of additive manufacturing technology.
Vat photopolymerization is used in a wide range of markets because materials are readily available and the method is useful for making various consumer products. For example, hearing aid manufacturer Sonova uses SLA to create products customized to individual clients. The shoe industry, including Adidas and Nike, is also using this technology for serial production.
- Advantage: High level of accuracy
- Limitations: Support structures often required, lengthy post-processing
- Raw material: Photo-curable resins
- Manufacturers/machines: 3D Systems, ProX 800; Formlabs, Form3
Material Extrusion
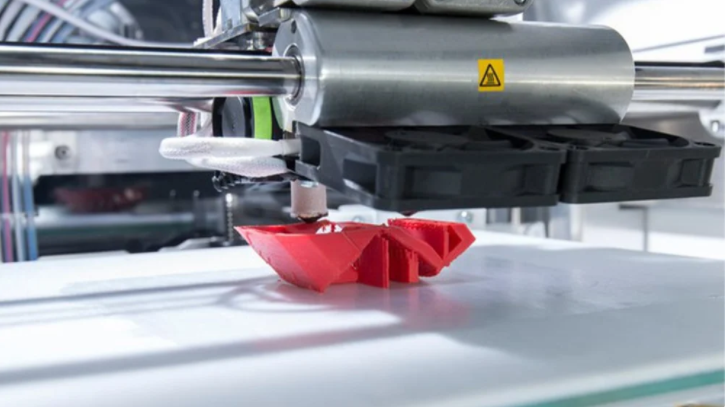
Material extrusion is the umbrella term for all additive manufacturing processes in which material is dispensed through a nozzle to form shapes. The first industrial material extrusion process was invented and patented by Scott Crump in 1989.
Crump is the co-founder of Stratasys, the company that introduced fused deposition modeling (FDM) in 1991, making it the second additive manufacturing technology to reach the market.
How Does It Work?
The build material is any composite capable of being pushed through a nozzle and retaining its shape. In this way, a print head – where the nozzle is located – can move around while depositing the material, thereby drawing a 2D layer. Once the paste-like material is deposited, it hardens, whether through cooling down or drying.
The print head then moves upwards to deposit the next layer of extruded material on top of the previous one. This process is repeated until, layer by layer, the desired 3D object is obtained. This is no doubt the process that is most commonly associated with desktop FDM 3D printing.
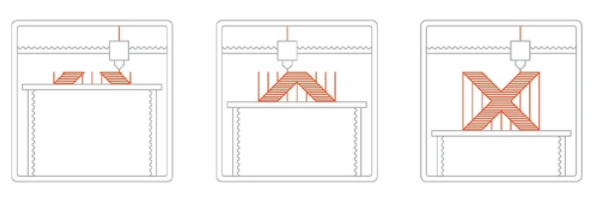
Materials
Technically, any material that can be pushed through a nozzle and retains its shape can be used for material extrusion processes, regardless of whether it’s heated or not. This includes materials like plastic, concrete, clay, bioink, and edibles like chocolate.
Undoubtedly, the most frequently used material for extrusion is pure or composite thermoplastics in filament form. In fact, most thermoplastics are suitable for this technology, from industrial standard plastics, like ABS and nylon, to more high-end engineering materials like PEEK. Composite materials, like metal- or carbon-fiber-filled plastics, are also an alternative for more technical projects.
Common Applications
Material extrusion is a very straightforward process. The raw material is typically easy to handle and the finished part usually doesn’t require much post-processing, other than support structure(s) removal and superficial finishing. This provides the perfect environment for rapid prototyping, which is the most common application for FDM-like processes.
There are literally hundreds of industrial applications for material extrusion processes. Buildings can be made with concrete extrusion machines, and human tissues and organs have already been created using novel bioprinting techniques.
Material extrusion also thrives on jigs and fixtures fabrication. Due to the relatively low cost of the materials, lead automotive companies like Volkswagen and BMW constantly produce manufacturing aid devices for their car assembly lines.
- Advantages: Cheap and straightforward process
- Limitations: Relatively low accuracy and speed
- Raw materials: Polymers and composites
- Manufacturers/machines: Stratasys, F900
Sheet Lamination
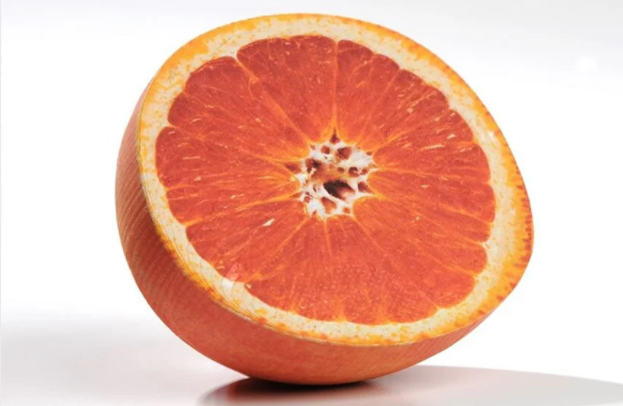
Sheet lamination is the process by which sheets of material are bonded together, layer by layer, to form a 3D object. While the principle behind this additive manufacturing process isn’t entirely new, the first sheet lamination machine was produced in 1991 by a company called Helisys. There are two main types of sheet lamination, which we’ll look at below.
How Does It Work?
ULTRASONIC ADDITION MANUFACTURING
Perhaps the most common sheet lamination technology is ultrasonic additive manufacturing (UAM). In this technique, room temperature metal sheets are bonded together by the application of ultrasonic waves and mechanical pressure.
The sheets are cut using a laser or by milling prior to or after the bonding. This will produce a cross-sectional shape of each layer that, when stacked together, will eventually form a 3D model. The parts are polished during or after the process to achieve a better finish.
The other technique is laminated object manufacturing (LOM), which uses an adhesive coating to bond sheets of material. These sheets are often heated by a roller that also presses them against the build plate to improve the adhesion. When the process is complete, the final parts are extracted from the surrounding material. The part or surrounding boundaries are usually created with cross-hatching to provide easier extraction.
Materials
Metals like aluminum, copper, stainless steel, and titanium alloys are most suitable for UAM. Interestingly, this process allows for the combination of different metals to make the much-valued “functionally-graded materials” (FGM) and their structures.
For LOM, the most popular material is regular A4 paper. Selective deposition lamination (SDL), a subprocess, uses colored printed sheets of paper to create full-color 3D objects. It’s also possible to use plastic.
Common Applications
Sheet lamination technologies are relatively affordable in comparison to other additive manufacturing processes. UAM requires low levels of energy since the metal sheets aren’t melted, and LOM uses cheap materials that are very easy to handle. Both techniques are also relatively fast.
UAM provides a reliable way to join dissimilar metals, ideal for creating new material combinations. LOM is generally used for rapid prototyping since it can’t produce parts with complex geometries, which lack dimensional accuracy. SDL might be a cost-effective option for full-color prototyping.
- Advantages: Fast, cheap, easy to handle
- Limitations: Low part strength (LOM), lengthy post-processing (UAM)
- Raw materials: Paper, plastic, metal
- Manufacturers/machines: CleanGreen 3D, CG-1 Full-Colour (LOM); Fabrisonic, SonicLayer 1200 (UAM)
Powder Bed Fusion
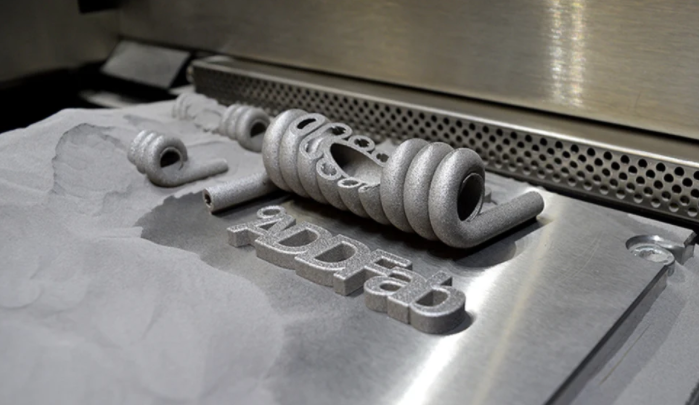
By definition, powder bed fusion processes use a thermal energy source to fuse specific areas of powdered material. This encompasses several commercial processes frequently used for industrial applications.
The first powder bed fusion process invented is known as selective laser sintering (SLS), developed and patented by Dr. Carl Deckard at the University of Texas. In 1992, the first SLS machine was introduced to the market by DTM, Dr. Deckard’s company, which now belongs to 3D Systems.
How Does It Work?
Regardless of the technique, all powder bed fusion processes happen in a near-vacuum chamber with an inert gas. The chamber is pre-heated and the process starts by spreading a thin layer of powder material onto a build platform.
Then, a thermal energy source selectively scans regions of the bed to bond the powder together, forming a thin layer of combined material. Once finished with one layer, the build platform moves down and another layer of powder is spread on top.
The next layer is fused together with the previous, and the process is repeated until a 3D object is formed. The unbonded powder is removed from the part and what’s left in the chamber can be reused to a certain degree.
The most common heat source is a laser. This appears in both SLS and selective laser melting (SLM). Electron beam technology (EBM) is also an effective alternative to using a laser, reaching higher temperatures and being capable of better processing materials like titanium alloys.
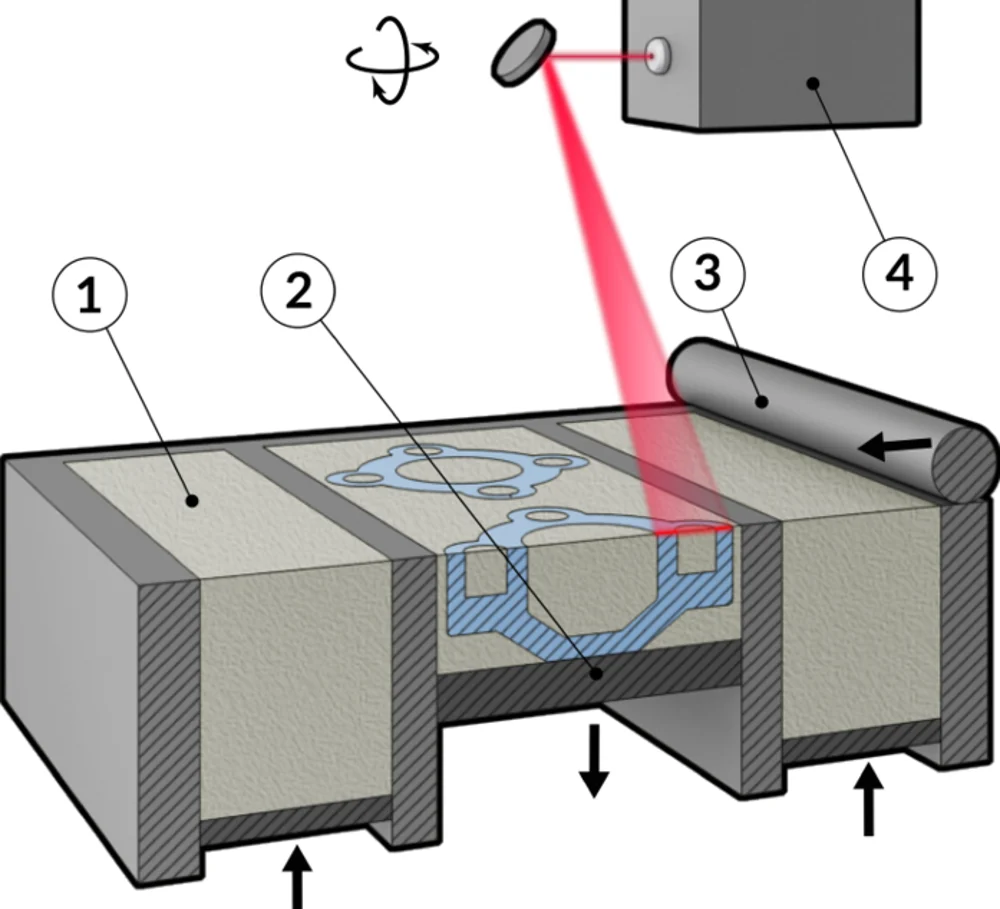
Materials
A very wide range of materials can be powder-fused, ranging from plastics like nylon to various metals like stainless steel, aluminum, and titanium alloys. Ceramic materials can also be processed by adding a few extra steps to the main process.
Depending on the material, the powder can be fused by sintering, a metallurgical process where the material is only partially melted. This is the case with SLS and another process called selective heat sintering (SHS). As for the remaining techniques, the powder is fully melted to a point where it fuses to itself and to the previous layers.
Common Applications
Powder bed fusion is one of the few additive manufacturing techniques that’s heavily used for production parts. The mechanical properties of metal parts produced by SLM and EBM processes are comparable to those obtained by traditional manufacturing methods like machining and casting. While post-processing is very often required, industries like medical and aerospace are already making use of these technologies on a regular basis.
It’s been reported that the new Boeing 777X engines contain around 300 additively-manufactured components each, and all of them are made by powder bed fusion methods. This includes parts that can’t be produced by any other fabrication technique, like the jet engine’s so-called inducer.
- Advantages: Wide range of materials and good mechanical properties
- Limitations: Costly material and post-processing steps
- Raw materials: Plastic, metal, ceramic
- Manufacturers/machines: SLM Solutions, SLM 280; GE Additive, Arcam Spectra L; EOS, Formiga P110
Binder Jetting
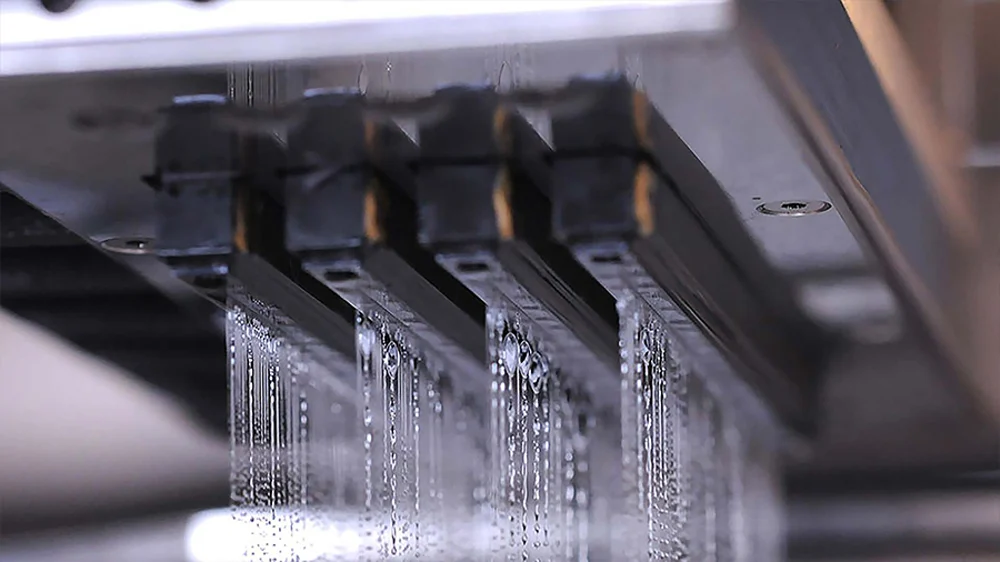
Binder jetting processes use a bonding agent to join powder materials together. It was developed and patented by MIT in 1989, licensed to Z Corporation in 1994, and later to ExOne in 1996.
How Does It Work?
The binder jetting process uses two types of material: a powder-base for its build material and a liquid binder agent. Manufacturing starts similarly to that of powder bed fusion, with a leveling roller spreading a thin layer of the powder material over a build platform. A print head, very similar to a traditional inkjet one, moves horizontally and sprays the binder agent material on certain areas of the powder layer.
The liquid binder causes a chemical reaction and the powder material bonds to form the first layer. The build platform is then lowered so that a new thin layer of powder can be spread. The process repeats with subsequent layers bonding together until the entire object is formed.
After the build process, the product needs to undergo post-processing steps to increase its resistance. We’ll look deeper into that in the following.

Materials
Binder jetting is widely applied for ceramic, metallic, and even sand parts. Regardless of the material, all objects require post-processing:
- Curing and sintering: This involves the application of heat, usually in a controlled environment like a furnace, to effectively fuse the particles together.
- Sintering: The binder agent is burned away in this process, leaving the part quite porous.
- Infiltration: To reduce porosity and increase density, the parts are infiltrated with different materials that fill these voids.
- Finishing: By the end of post-processing, the parts display much higher resistance and better mechanical properties.
Common Applications
The binder jetting process produces metal parts at a lower cost than other technologies like powder bed fusion. Also, since the metal powder isn’t melted during the process, issues related to residual stress are eliminated. Furthermore, binder jetting is a faster process relative to other metal additive manufacturing processes.
Since binder agent can be colored, non-metallic parts can be produced in a wide range of colors, making this process especially suitable for high-fidelity prototyping. This is the case with 3D Systems’ trademarked process ColorJet Printing (CJP). These materials are also widely used for producing sand molds and cast patterns.
- Advantages: Colored parts, cheaper metal fabrication
- Limitations: High process time and costs
- Raw materials: Plastic, metal, ceramic
- Manufacturers/machines: ExOne, X1 160Pro and S-Print
Material Jetting
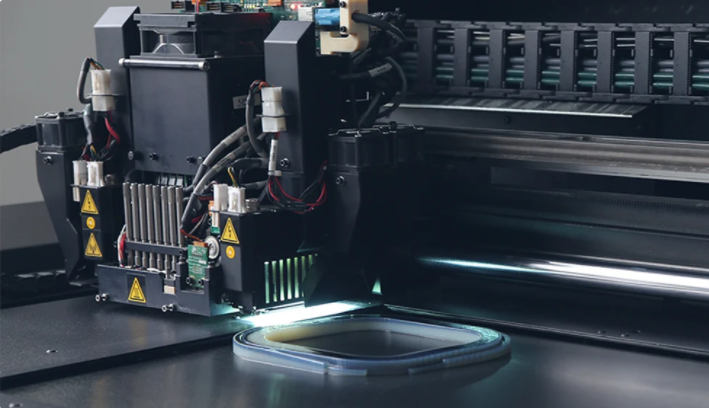
Material jetting is the process by which droplets of build material are selectively deposited and cured to form a part.
The first commercialized systems were produced by Solidscape in 1994. These machines produced wax parts via a technology known today as “drop on demand” (DOD). In 1998, a new material jetting process was patented called PolyJet. It was developed by Objet, an Israeli company that’s now part of Stratasys.
How Does It Work?
Material jetting can be described as a mix of 2D inkjet printing and SLA. The process starts by heating up the build material, a photoreactive resin, in order to achieve the right viscosity. Then, one or more print heads move horizontally and shoot hundreds of micro-droplets of material onto the build platform, either continuously or drop by drop.
These droplets form a layer that is solidified either through cooling, UV-light curing, or by evaporating the liquid part of the material via an infrared laser. The build platform then moves down so that another layer of material can be deposited. The process is then repeated until the final product is complete.
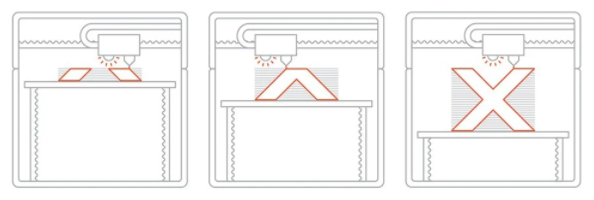
Materials
Perhaps one of the main advantages of jetting technologies is related to the materials it uses. Each printhead can store a different one, allowing multi-material and multi-color parts to be used simultaneously. This means that different regions of a single part can be made from different materials or colors.
The most common build materials for material jetting are polymers in the form of liquid resins. UV photo-curable resins in material jetting have the advantage of outputting already fully cured parts, thus avoiding extra post-processing steps. Although it’s less common, metals can also be directly jetted.
Common Applications
Apart from the ability to print multi-material parts, material jetting is perhaps the fastest and most accurate additive manufacturing technique. It can also provide very smooth surface finishes and produce very large parts without compromising dimensional accuracy.
While its multicolor capabilities enable the production of incredibly realistic objects and prototypes, the different materials and high accuracy also make this process suitable for tooling and injection mold manufacturing.
- Advantages: Very high accuracy, fast process, smooth finishes
- Limitation: High equipment cost
- Raw materials: Polymers, waxes
- Manufacturers/machines: Stratasys Object500 Connex3; HP, Jet Fusion 4200
Directed Energy Deposition
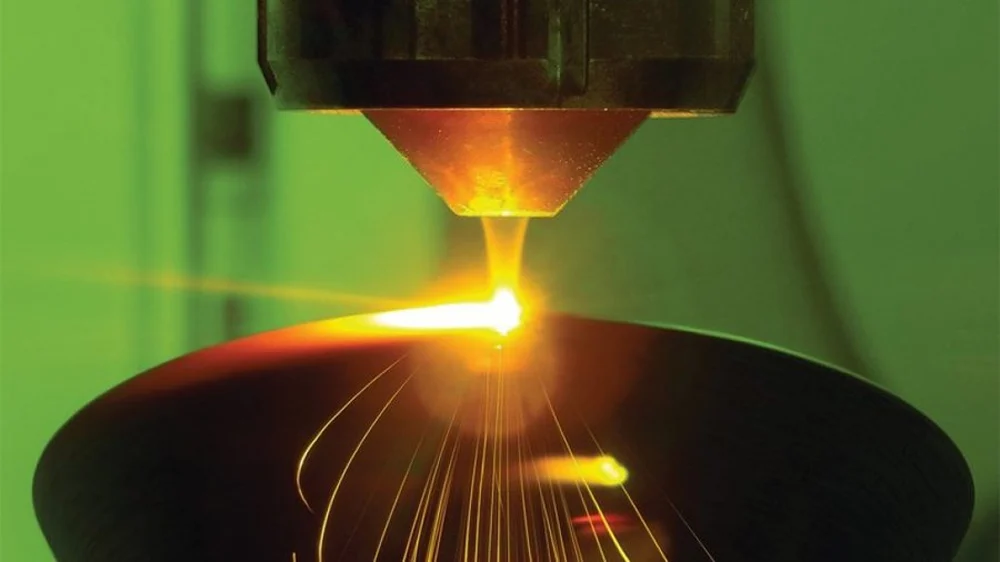
Directed energy deposition (DED) technologies fuse materials by melting them as they’re being deposited. It’s a complex manufacturing process that’s often used for repair and maintenance.
There’s a great variety of processes that fall under this category, like directed light fabrication (DLF), direct metal deposition (DMD), and the most popular, laser engineered net shaping (LENS).
The latter was the first DED technology, developed by Sandia National Laboratories between 1994 and 1997. At that time, it was considered both commercially and militarily significant.
How Does It Work?
In order to melt materials together, an intensely focused energy source is required, usually a laser. The laser is mounted with a nozzle on a multi-axis arm, allowing a freedom of movement not seen in other additive manufacturing technologies.
The material is pushed through the nozzle, then incorporated into the focused energy flow, melting and depositing at the same time. Once solidified on the underlying surface, a new layer is complete. The process is somewhat similar to material extrusion, but it required much more energy and can be deposited in multiple directions.
Materials
The build materials for DED processes are either in the form of wire or powder. Wire can be less accurate but more efficient in terms of material waste. Powders, however, can be changed during the process to combine different materials in one part, allowing for the creation of functionally-graded materials (FGM).
Depending on the process, DED can be used with plastics and ceramics, but metals are by far the most popular material. Due to the high-energy sources applied, ceramic materials melt during the deposition, often turning to a glassy state.
For metals, DED supports a wide range, including titanium, Inconel (a trademarked austenitic nickel-chromium-based superalloy), copper, aluminum, and stainless steel. It’s worth noting that the build material for these processes is significantly cheaper than with the metal powders used in powder bed fusion.
Common Applications
This technology is known to provide high material deposition rates, making for a fast manufacturing process, overall. The parts produced by DED require limited post-processing and display mechanical properties comparable to (or better than) those of cast or wrought metals. Due to the nature of these processes, DED doesn’t require gravity, making it potentially useful for applications in space.
The LENS process can repair damaged parts that traditional methods can’t otherwise fix. This is because DED processes can add material to damaged areas in different directions, and post-processing achieves the required tolerance. In fact, these processes are frequently used in hybrid manufacturing machines, where both additive and subtractive methods are applied.
- Advantages: Flexible and fast process, material efficient
- Limitation: High equipment cost
- Raw materials: Plastic, metal, ceramic
- Manufacturers/machines: DMG Mori, LASERTEC 65; Mazak, INTEGREX i-400 AM