Compare the features of industrial 3D printing technologies – filament, resin, powder bed – and one stands out as ideal for mass production of complex parts: binder jetting. Not only are the materials relatively affordable, but the machines typically have a larger print volume, print with high speed and accuracy, and can produce more complex shapes than other methods.
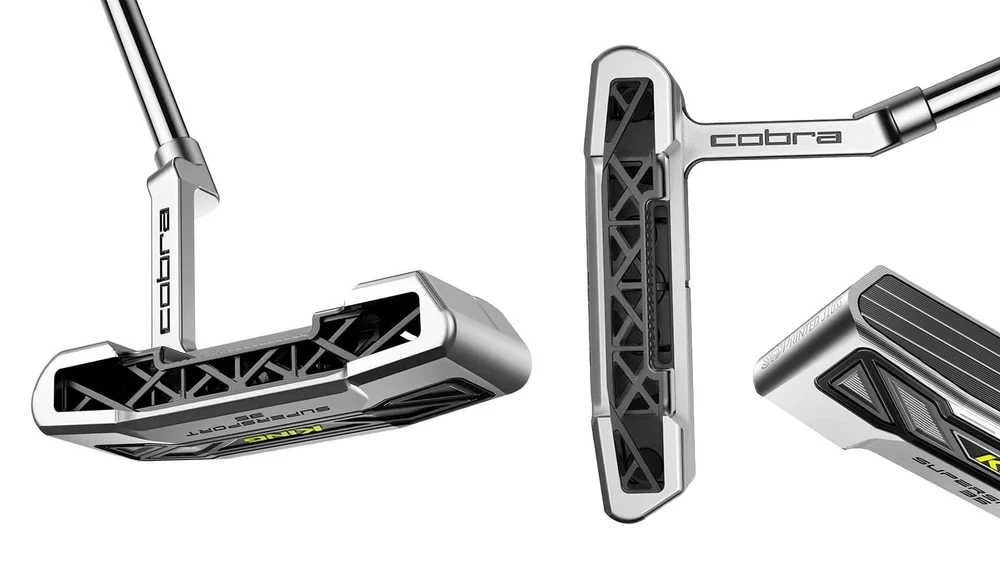
From Volkswagen automobiles to Cobra golf clubs, manufacturers are turning to binder jetting over traditional metal and plastic fabrication methods and over other 3D printing methods for a host of reasons we’ll get into below. But first, if you’re not familiar with binder jetting, let’s summarize:
Binder jetting is a method of 3D printing that uses a liquid binding agent to bond powdered materials in layers to create solid, complex shapes. As the build progresses, the layers of the print are bonded together, resulting in a box of powder with the desired part geometry inside. For plastic parts, the process often stops here, but for metal parts, there are essential post-processing steps.
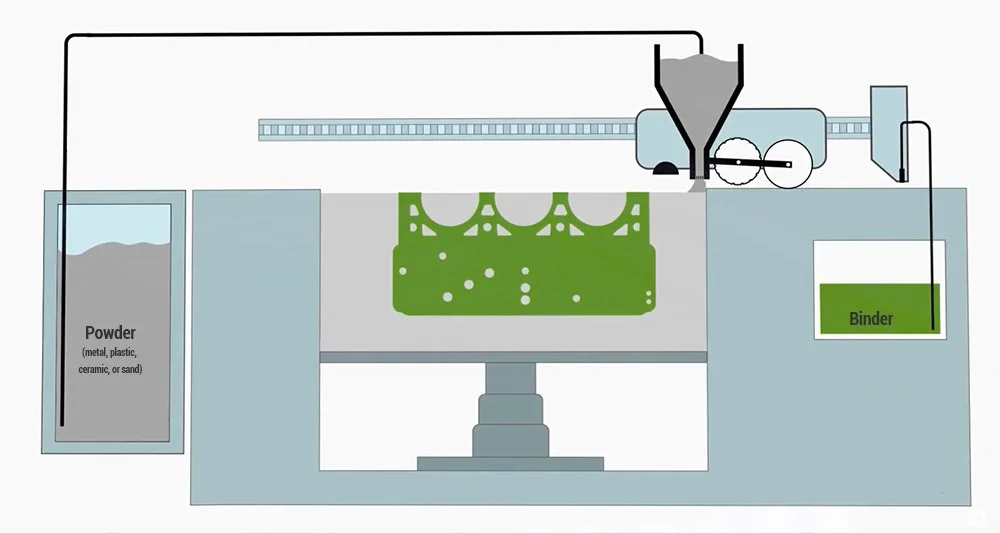
Mixing liquid and powder may sound messy, but today’s advanced 3D printer technology can precisely place millions of nanogram-sized drops of binder per second onto a fine powder bed to define a cross-section layer of a part about 0.01 mm thick. For a deep dive into the technology, skip to the Basics of Binder Jetting – How it Works section below.
Why Binder Jetting?
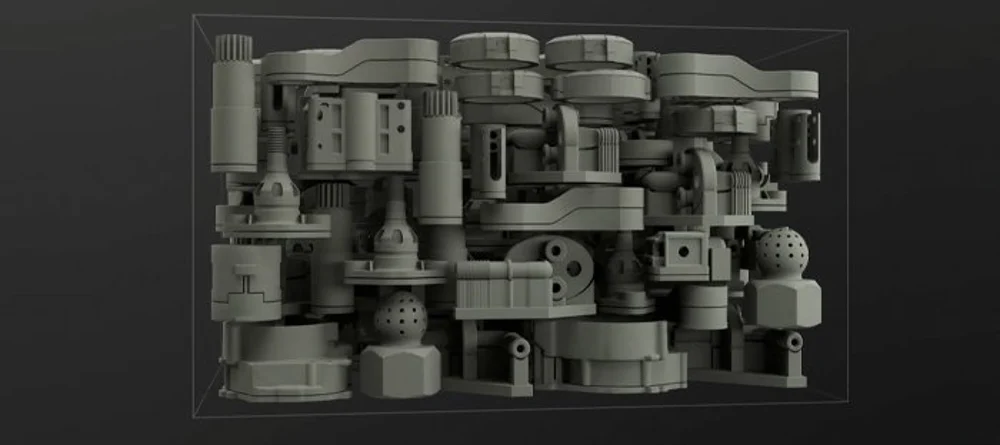
Binder jetting has several advantages over traditional metal injection molding and over other forms of 3D printing, depending on your requirements. The technology especially shines when it comes to speed and resolution since printheads typically work faster than lasers or electron beams.
According to new research by Amir Mostafaei, assistant professor in the Department of Materials, Mechanical and Aerospace Engineering at the Illinois Institute of Technology, binder jetting is poised to dominate other areas of manufacturing, specifically metal injection molding, because they share the same materials and processes, and size and geometry details, such as wall thickness.
Binder Jetting Pros:
- Materials. Binder jetting is compatible with a wide range of powdered materials currently available, and because powdered metals and ceramics are sintered to full density in many other traditional manufacturing processes, proponents of binder jetting say it has the potential to surpass powder-bed fusion in applications and have the widest selection of materials of all AM processes. In theory, binder jetting can be used with any powdered material and complementary binding liquid. Currently, some of the most unusual materials include wood powder and sugar.
- Process. Most binder jet printing processes operate at room temperature and atmosphere, avoiding issues related to oxidation, residual stress, elemental segregation, and phase changes, making the powder around the parts in the build box highly recyclable, saving on material costs, researchers say. [1]
- Size. By avoiding the use of expensive sealed chambers for vacuum or inerting, the build volume of binder jetting 3D printers is among the largest of all 3D printing technologies while still maintaining the high resolution afforded by inkjet. [1]
- Volume. Batches of different parts are printed at once. This high-volume production capacity makes it ideal for companies that want to print a lot of complex parts.
- No supports. The need for support structures is eliminated or significantly reduced for any part geometry produced by binder jetting because the powder bed provides enough support, which means greater design freedom (especially to create internal channels), less material waste, and less time and labor to remove supports, and more space to nest many parts in one build volume. However, some shapes may benefit from supports in the sintering process.
- Speed. Binder jetting is fast and has high production rates so it can produce large volumes of parts more cost-effectively than other AM methods.
- Versatile. Binder jetting can produce various densities with controlled porosity based on the sintering temperature and time, which leads to a wide range of uses. [1]
Binder Jetting Cons:
- Multi-steps. Binder jetting is a multistep process requiring post-processing steps (curing and densification), which, in some cases, involve additional equipment.
- Distortion risks. The process of making the binder jetted parts more dense – sintering for example – can result in distortion of the geometry. However, this should be avoidable with proper software calculations in advance.
- Manual depowdering (removing parts from the bed of metal powder) is necessary for most metal parts because they are delicate in their green state. Some depowdering automation is possible depending on the part geometry.
METAL BINDER JETTING
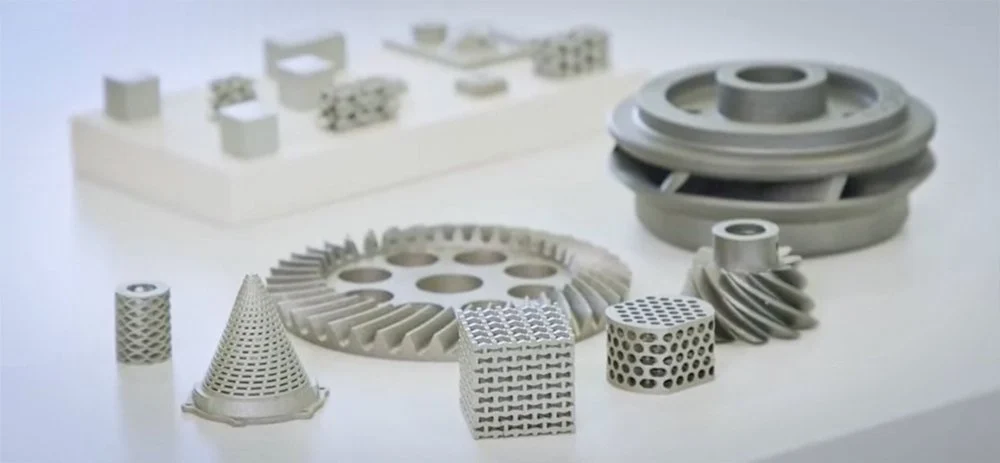
Metal binder jetting is a very appealing technology for metal part production for all the reasons mentioned above, plus one very important point related specifically to metal: lightweighting.
Because binder jetting can print parts with complex pattern infills instead of being solid, the resulting parts are dramatically lighter while being as strong. Binder jetting’s porosity feature can also be used to achieve lighter end parts for medical applications, such as implants, for example.
As with other additive manufacturing processes, binder jetting can produce complex components with internal channels and structures, eliminating the need for welding and reducing the number of parts and weight of components. Redesigning your metal parts for binder jetting can lead to a dramatic reduction in material used and wasted.
Overall, the material properties of metal binder jet parts are equivalent to metal parts produced with metal injection molding, which is one of the most widely used manufacturing methods for the mass production of metal parts. Plus, binder jet parts exhibit higher surface smoothness, especially in internal channels.
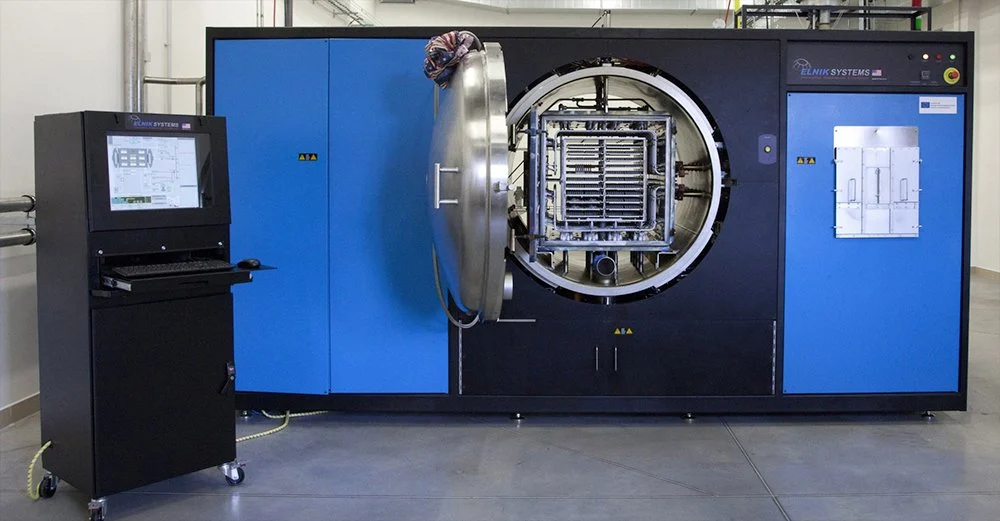
It’s a two to three-step process
Metal binder jetting parts require secondary processes after printing to achieve their good mechanical properties. Right off the printer, parts basically consist of metal particles bound together with a polymer adhesive.
After printing, curing, and removing the parts from the bed of metal powder, one option is to place parts in a furnace where the binder is burnt out and the remaining metal particles are sintered (bonded) together. Depending on the temperature of the furnace and the time parts are sintered, they can be 99% dense or as much as 60% porous.
If your application requires density, bronze or another metal can be used to infiltrate the voids resulting in parts with low porosity and good strength. Highly porous parts may be desired for lightweight applications or medical implants, where porosity has been shown to enable bone growth.
Metals & metal alloys for binder jetting:
- Maraging steel
- Stainless steels
- Tool steels
- Low alloy steels (4140, 4340)
- Nickel
- Cobalt
- Titanium
- Aluminum
- Copper
- Bronze
Let’s take a look at the top metal binder jetting 3D printers.
ExOne
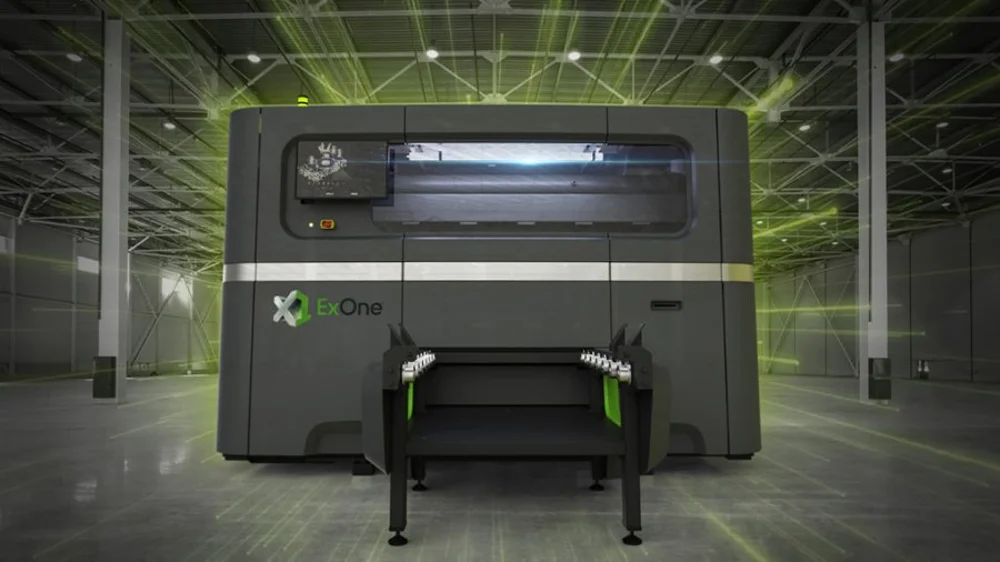
Although ExOne didn’t invent metal binder jetting it did launch the market’s first commercial metal binder jet 3D printer and now offers five models. ExOne’s family of metal 3D printers is designed as a scalable system to take you from R&D and prototyping to serial production on the same platform. The company was recently acquired by Desktop Metal.
ExOne’s smallest binder jetting 3D printer, the ExOne Innovent+ is compatible with a variety of powder injection molding feedstock – including, but not limited to, metals – to form one-offs and small batches of parts. The InnoventPro, however, is designed for production capabilities with three times the build area of the Innovent+. From here, ExOne’s printers get larger and faster culminating with the X1 160Pro with an 800 x 500 x 400 mm build volume and a speed of more than 10,000+ cc/hour.
ExOne machines can produce metal parts in a wide range of metals and metal composites, including aluminum, titanium, copper, stainless steel, and tungsten-bronze.
Desktop Metal
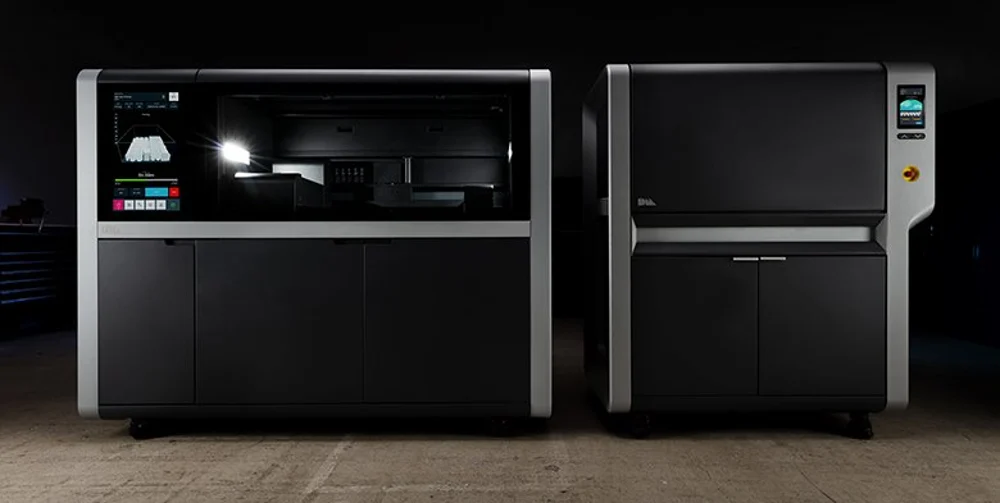
Desktop Metal (which recently acquired ExOne above) burst onto the additive manufacturing scene in 2015 and introduced its first binder jet 3D printer in 2019 hat was easier to use than the competition at the time and helped to expand the consumer base for the technology.
The company’s two binder-jetting platforms, the Production System and the Shop System (available in different configurations), both feature innovation on the established binder jetting technology.
Designed with smaller machine shops in mind, the Shop System produces metal parts with good surface finish and resolution all in a turnkey solution that doesn’t require a dedicated engineer.
Desktop Metal says its printers can produce customer-ready parts with densities up to or exceeding 99% without the need for infill or a solvent debinding step. With properties similar to castings, parts from the Production System are suitable for demanding applications where strength is critical.
The Production System can produce up to tens of thousands of parts per day and uses the same low-cost powders used in the metal injection molding industry so you can take advantage of an established powder supply chain. As much as 99% or more of the loose powder recovered during the process can be recycled, driving further cost efficiencies while reducing waste.
An overhead camera monitors each layer using multi-angle imaging to detect print defects and nozzle performance during printing, facilitating part inspection and build audits critical to deploying additive manufacturing in production environments.
The Production System produces parts with a wide variety of metals—including everything from stainless steels to reactive metals and high-performance alloys, while the Shop System prints with 17-4 PH stainless steel with other materials in development.
Digital Metal
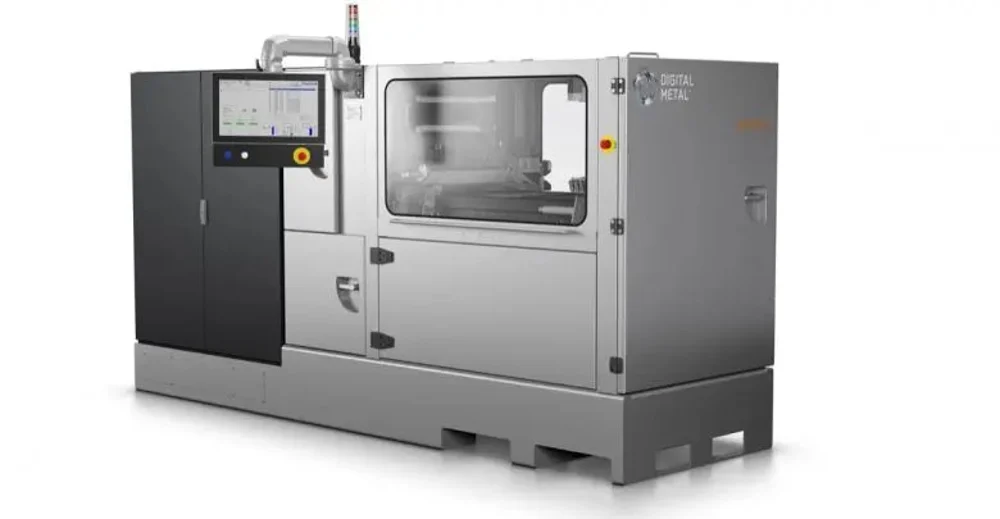
Digital Metal focuses exclusively on high-precision binder jetting technology developed by its parent company Höganäs AB, a pioneer in metal powder development. It’s making great strides into territories previously ruled by conventional manufacturing technologies.
The company’s DM P2500 is an impressive machine capable of large batches of small and exceptionally intricate metal parts, which can each be customized. Every single part in a batch of components can be custom-made, no matter the number. This opens up creative thinking and added marketing value as you are able to supply products customized for your market.
Featuring a build volume of 203 x 180 x 69 mm, the P2500 prints at some 300 cm3 per hour, making for a fast, flexible, and cost-effective solution for the production of metal part batches. Plus, it offers a high precision resolution of 35 microns, providing a crisp level of detail.
Digital Metal continues to improve its metal 3D printer. In the spring of 2020, the company rolled out an update which it claims tripled the print speed (presumably under specific conditions or print parameters). The firm is also expanding its material offering. In late 2020, Digital Metal rolled out the DM D2 tool metal alloy, and just in February 2021, it launched a pure copper material.
GE
GE Additive has had its H2 Binder Jet machine in beta testing for years now. The last word was that we should expect the H2 to be available later this year.
GE is already heavy into additive manufacturing with its accessions of Concept Laser and its direct metal laser melting (DMLM) technology, and electron beam melting (EBM) technology from Arcam.
“Our approach to binder jet is making additive mass production a reality in every industry,” says Jacob Brunsberg, GE’s binder jet product line leader. “And while it would be relatively easier to launch individual machines, we continue to hear from customers, especially in the automotive industry, that they need a complete solution that can scale.”
The only other detail available is that GE Additive is partnering with Sandvik Additive Manufacturing to develop a menu of metal powers and alloys for the machine. Stay tuned to All3DP for the latest when the H2 launches.
HP Metal Jet
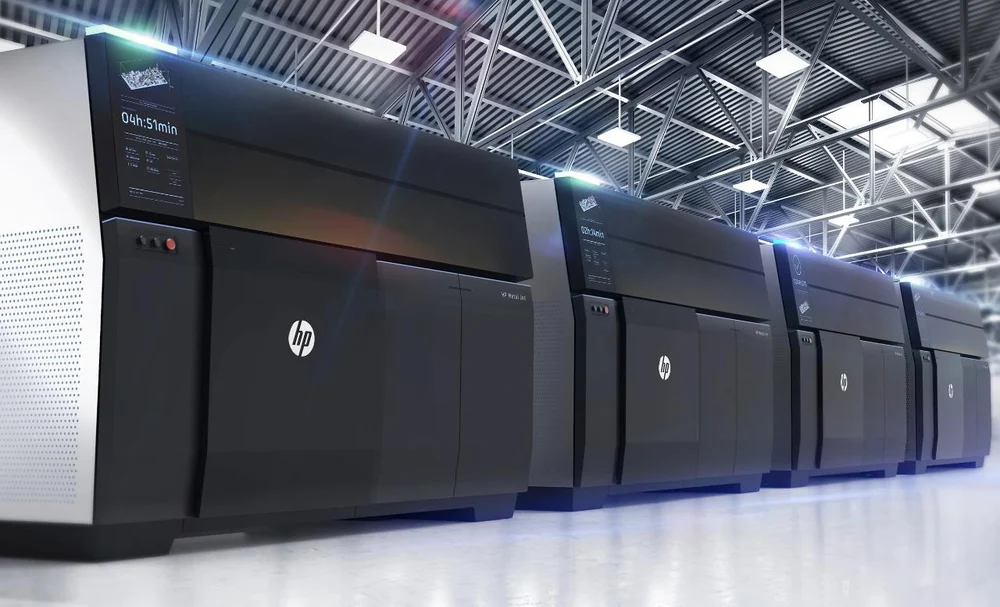
HP inkjet technologies have disrupted and led a broad range of printing markets for decades so it’s no wonder that when you talk about 3D printing with inkjets, HP is a major player.
HP started off in polymer 3D printing in 2014 and adopted its binder-and-powder technology called Multi Jet Fusion to metal, called Metal Jet, in 2018. HP Metal Jet is a binder jet technology that features density after sintering of more than 97%, similar to MIM.
HP uses a thermal inkjet to precisely deliver a binding agent to a powder metal bed. Throughout the Metal Jet printing process, the powder bed may be heated to evaporate volatile components of HP’s binding agent. (All metal binder jet processes require a heating step at some point.) The leftover metal powder has a high reusability rate so there’s less waste, the company says. The final parts can undergo machining and polishing to meet dimensional and surface finish requirements.
HP offers one model of metal 3D printer currently only printing with stainless steel (17-4 PH and 316L) and FSLA (Free Sintering Low Alloy).
POLYMER BINDER JETTING
The process and technology for plastic binder jetting are very similar to metal binder jetting. It involves plastic powder and a liquid binding agent. (No, you can’t use the same machine for both metal and plastic, but hopefully, someone will come out with that soon.)
Once printed, plastic parts are removed from their powder bed and can often be used without any further processing but can be infilled with another material, cured, polished, or painted. They do not require a furnace sintering step, like with metal.
Binder jetting with polymers, like with metals, has a range of unique advantages over injection molding and other polymer 3D printing technology.
Advantages of polymer binder jetting:
- Superb color reproduction
- Fast print speeds
- Support-free design flexibility
- High rate of material recycling
- High-quality surface finish
- Consistent mechanical properties
Disadvantages of polymer binder jetting:
- Limited materials
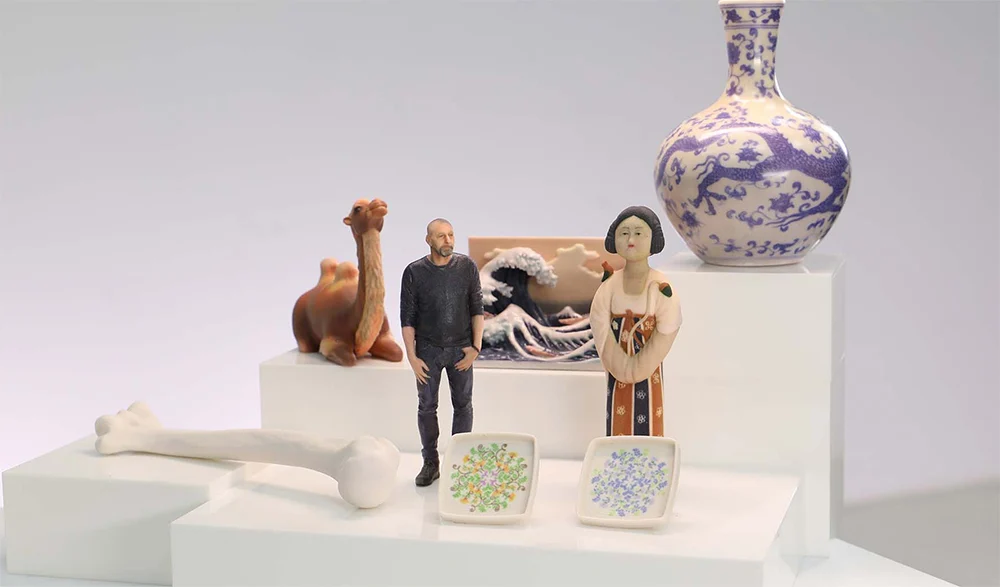
But now, let’s clear up some terminology and confusion around the use of the word “jet”.
All “Jet” Technologies Are Not the Same
For this article, our focus is on powder-and-binder technologies, but a lot of printers also incorporate the term jet, usually to refer to material jetting technology, and it can get confusing.
For example, MultiJet printing from 3D Systems is material jetting where a printhead prints out layers of UV curable liquid polymer onto a flat platform. The company offers a line of ProJet MJP printers for material jetting technology. However, the company’s ProJet line, including the ProJet 6000, is actually not binder jetting or material jetting machines, but rather resin printers. 3D Systems’ ProJet CJP (ColorJetPrinting) printers, however, are binder jetting machines.
PolyJet from Stratasys also uses liquid resin dispensed through inkjets following the material jetting model. The photopolymer material is added to the print bed layer by layer. In between, each layer is cured with UV light.
HP’s Multi Jet Fusion technology uses powder and a liquid fusing agent but includes an infrared power element to melt the core material. In the Multi Jet Fusion process, a radiation-absorbing ink is introduced into a powder bed by means of a print head. Areas that are not to be printed, on the other hand, are cooled with a second printing fluid, a detailing agent. After each layer has been printed, energy is introduced into it with an infrared lamp. This process sequence is repeated until the entire construction volume of the job box is filled and the required components within the powder bed have been printed. Unlike other binder jetting printing technologies, HP Multi Jet Fusion prints each layer of new material and agents on top of a previous layer that is still molten – so that both layers fuse completely – to deliver strong printed parts right from the powder bed.
HP is not the only 3D printer manufacturer to introduce heat to what would appears to be a binder jetting process. Voxeljet developed a technology called High Speed Sintering (HSS) where a thin layer of plastic powder, such as PA12 or TPU, is applied to a heated building platform. An inkjet print head then moves over the entire surface of the platform and moistens or infiltrates the areas of the building platform with infrared light-absorbing ink. The building platform is then irradiated with infrared light and inked areas absorb the heat, which sinters the powder layer underneath while the unprinted powder remains loose. The sintered parts are then cooled down in a controlled manner in the building area before they can be removed and unpacked. The HSS process, unlike the HP process, does not need a second printing fluid.
So are Multi Jet Fusion and High Speed Sintering types of binder jetting? Well, they do have a powder bed and a binder, but experts argue that the melting of the core material puts them more in the powder bed fusion category. They are not purely a cold technology. We’ll leave that distinction for you to decide, so we’ve included the machines here because they do offer most of the advantages of binder jetting.
3D Systems
3D Systems makes a wide range of 3D printers employing several types of technology. The one in the binder jetting category is called ColorJet Printing (CJP). The feature here is not the core material, but rather the color binder.
As with other methods, the material is spread in thin layers over the build platform with a roller. After each layer is spread, color binders (in cyan, magenta, and yellow) are selectively mixed and jetted from inkjet print heads, which causes the core material to solidify. The build platform lowers with every subsequent layer which is spread and printed, resulting in a full-color or white three-dimensional model. The unused powder can be reused. Parts can be sanded, drilled, tapped, painted, and electroplated, which further expands the options available for finished part characteristics.
Introduced in 2017, the 260Plus is 3D Systems’ most affordable and smallest CJP 3D printer, but they have three others (460Plus, 660Pro, 860Pro) offering the same layer thickness but more colors, larger build size, and integrated part cleaning.
HP
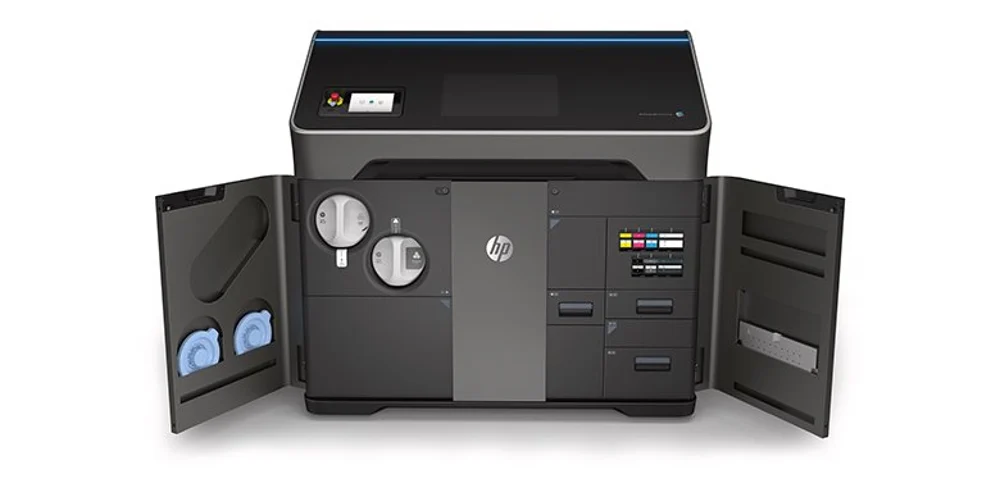
HP Multi Jet Fusion technology is at work in the company Jet Fusion series machines, 4200, 5200, 500, and 300.
The entry-level and cost-effective 500 and 300 3D printers are tailored for small or medium-sized product development teams, design firms, and universities. Depending on configuration and color preference, the cost of the Jet Fusion 300 / 500 series starts from $50,000. This price point should make Multi Jet Fusion technology more accessible to small to medium-sized businesses, universities, and research institutions.
The larger, industrial machines in the 4200 and 5200 series, are designed for fast, short-run production. Used for a wide variety of applications from healthcare to automotive, the Jet Fusion machines are designed to produce batches of functional, consistent parts with no support structures needed.
Voxeljet
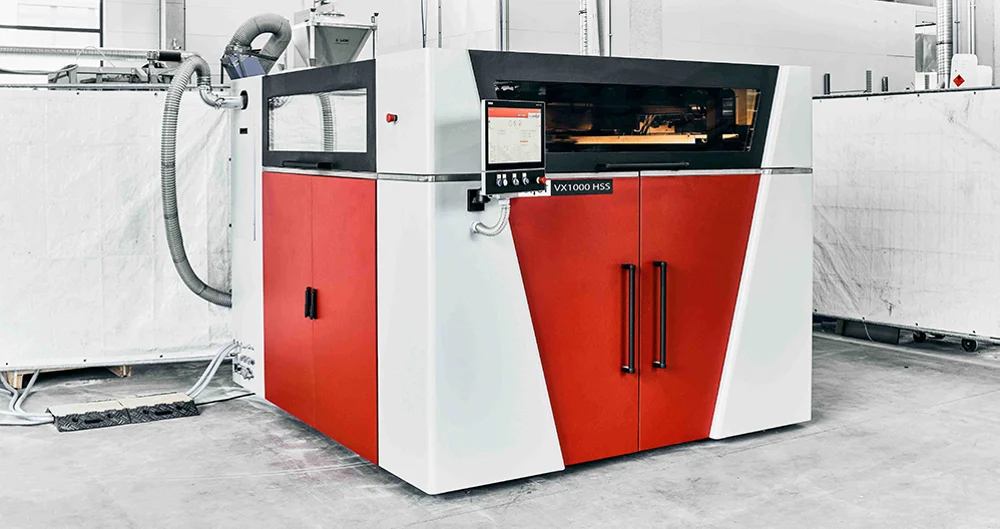
Whether sand, plastic, or ceramic, Voxeljet 3D printers use powder material and binder to deliver finely detailed parts. The Voxeljet line of industrial 3D printers is focused on industrial applications, such as the production of molds or models for small series metal casting applications. They are also popular choices for design samples, jewelry, art, and architecture parts.
Some Voxeljet printers feature binder jetting technology, while others feature what you could call a type of binder jetting called polymer High Speed Sintering (HSS). Don’t get confused by their use of the word sintering, there are no lasers or electron beams involved. Instead, Voxeljet’s technology uses infrared light to irradiate the binder (or ink, as they call it) that’s been selectively distributed on the polymer powder. The ink dyes the polymer black so it can better absorb the infrared light.
The smallest of their company’s printers is the binder jetting VX200, which can process sand, plastic, or ceramic. The VX200 HSS, on the other hand, is dedicated to polymers. The larger VX1000 also comes in both binder jetting and HSS versions and is designed for continuous use in industrial production. The VX1000 HSS positions itself as an economically viable alternative to conventional plastic injection molding. In fact, Voxeljet hopes its HSS tech will help establish additive manufacturing in the series production of the plastics industry.
XYZ Printing
Thankfully, XYZ Printing doesn’t have a proprietary name for its version of binder jetting, opting instead to just call it “full-color binder jetting”. In addition to plastic powder and binder, XYZ Printing adds another component, colored ink.
The company’s printer, the PartPro350 xBC offers full-color printing in one process by integrating all steps of curing, coloring, and 3D stacking at once with CMY three-color ink and transparent binder.
PartPro350 xBC delivers a vertical building speed up to 18mm per hour with full-capacity building. The focus is on volume and productivity with a removable build tray module so you can replace a new build tray directly into the machine and start a new print job immediately.
CERAMIC BINDER JETTING
Binder jetting is expected to become the universal process for preparing ceramic parts because it can overcome multiple problems that appear in the conventional ceramic preparation process, such as the difficulty to prepare complex-shaped ceramic parts and the shrinkage of the sintering process, according to reachers at China’s Northwestern Polytechnical University.
Binder jetting has inherent advantages for additive manufacturing of ceramics, including print speed, print size, and material choices, and flexibility.
Binder jetting is continuing to grow, and future machine enhancements for printing small particle size, and sinterable ceramic powders will continue to create broader adoption.
Voxeljet
Germany-based Voxeljet manufacturers a range of flexible additive manufacturing machines employing binder jetting process with classic sintering technologies. From prototyping to agile industrial series production, Voxeljet’s ceramic 3D printers can handle a spectrum of ceramic materials, such as aluminum oxide, zirconium oxide, mixed oxides and also non-oxide ceramics, such as silicon nitride in advance to ensure the optimum industrial applicability in our processes. Each printer is customized to the customer’s use case.
The VX200 offers the highest degree of flexibility in terms of material development in the voxeljet system series. Whether new binder and powder combinations or the rapid production of components for property testing.
The Voxeljet open-source software allows process parameters to be adapted to individual 3D printing materials.
ExOne offers multiple 3D production printing machines that are able to print with ceramic powders although all are still in beta testing.
SAND BINDER JETTING
The production of large sand casting molds and cores is one of the most common uses for binder jetting. The low cost and speed of the process make it an excellent solution for the foundry industry. Elaborate pattern designs that would be very difficult or impossible to produce using traditional techniques can be printed in a matter of hours.
The future of industrial development continues to place high demands on foundries and suppliers. Sand 3D printing is at the beginning of its potential.
ExOne
Sand 3D printers from ExOne support sand casting applications across industries, allowing you to innovate and provide enhanced design options. The company offers three models of sand binder jetting 3D printers featuring different build sizes.
The S-Print combines a compact structure and choice of four binders to accommodate a versatile range of applications. As with all ExOne 3D core and mold printers, cores and molds can be created from CAD data quickly and without the need for tools.
Voxeljet
As mentioned above, Voxeljet VX 200 and VX1000 machines can print with sand, polymers, and ceramic, but the company’s large industrial VX1300 X, VX2000, and the larges, VX4000, are dedicated to the additive mass production of highly complex sand cores for metal casting.
The printers user binder jetting technology to turn Cerabeads and classical quartz sand with different grain sizes into molds and cores.
EXOTIC & OTHER BINDER JETTING
At its core, using a liquid to bind a powder into a shape can theoretically be applied to countless liquid and powder combinations from sugar to silk to sawdust. Below are two stand-out examples of just how much potential binder jetting has as a manufacturing method.
Sugar Powder & Flavoring Binder
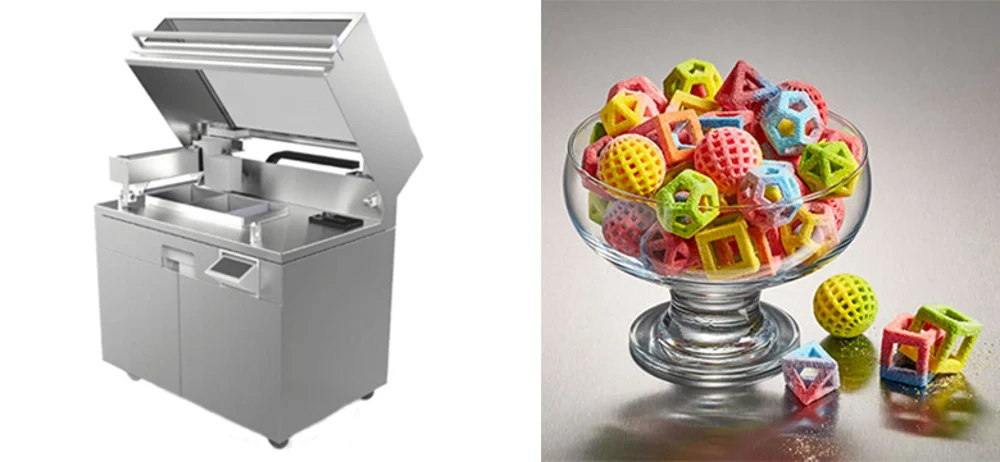
Perhaps the engineers at 3D Systems were craving sweets when they thought of applying the company’s binder jetting technology to sugar. In fact, they worked with partner CSM Bakery Solutions for years to perfect the professional-grade culinary 3D printing system known as the Brill 3D Culinary Studio. This 3D printer allows chefs to create edible culinary figurines and embellishments.
The integrated solution includes the Brill 3D Culinary Printer and software powered by 3D Systems technology, the Brill 3D Culinary Powder and Brill 3D Culinary Binder, all used in tandem to produce an array of full-color, life-like, and edible 3D figures and embellishments. Chefs can use their own design or select from a library of hundreds of 3D designs to mass-print smaller pieces such as cake decorations, confections, and garnishes or print larger, statement pieces.
Wood Powder & Sap Binder
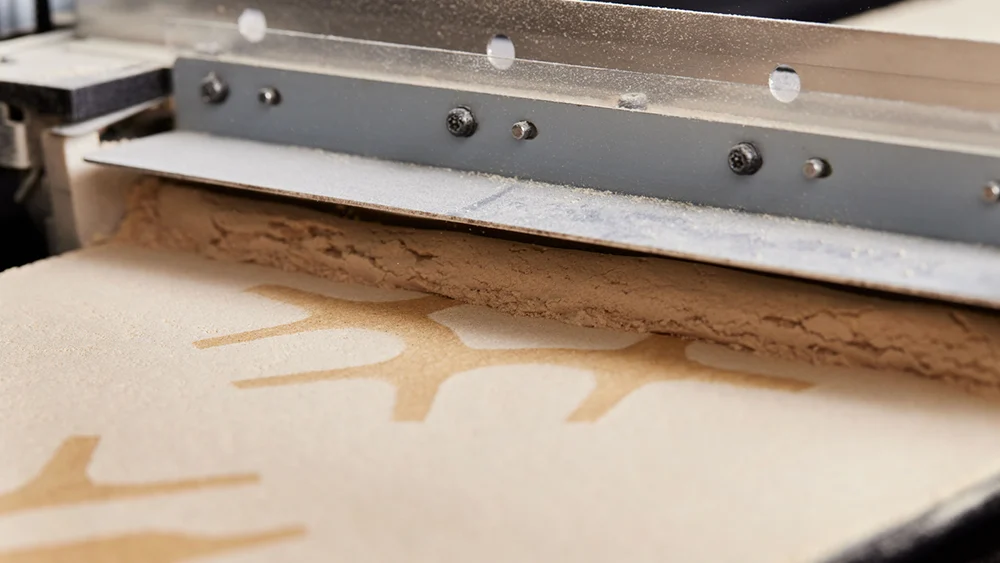
American 3D printer manufacturer Desktop Metal, known for making metal industrial parts from metal powders, launched a new subsidiary in 2021 called Forust (yes, like forest) to 3D print wood from lumber and paper manufacturing waste byproducts, namely cellulose dust and lignin (a class of complex organic polymers that form key structural materials in the support tissues of most plants).
The process uses Desktop Metal’s existing binder jetting additive manufacturing technology on a wood-configured Shop System printer. It can also be used with the robotic arm 3D printer adapted from printer manufacturer EnvisionTec, which Desktop Metal recently purchased. Both of these 3D printers are production platforms, so the idea is clearly intended for mass-manufacturing applications.
The goal behind Forust, the company says, is to sustainably manufacture custom wood products, such as furniture, household objects, and architectural pieces that feature a digital grain throughout. Final parts exhibit the functionality and stiffness in line with conventional wood and can be stained with a variety of finishes including natural, oak, ash, and walnut, the company says.
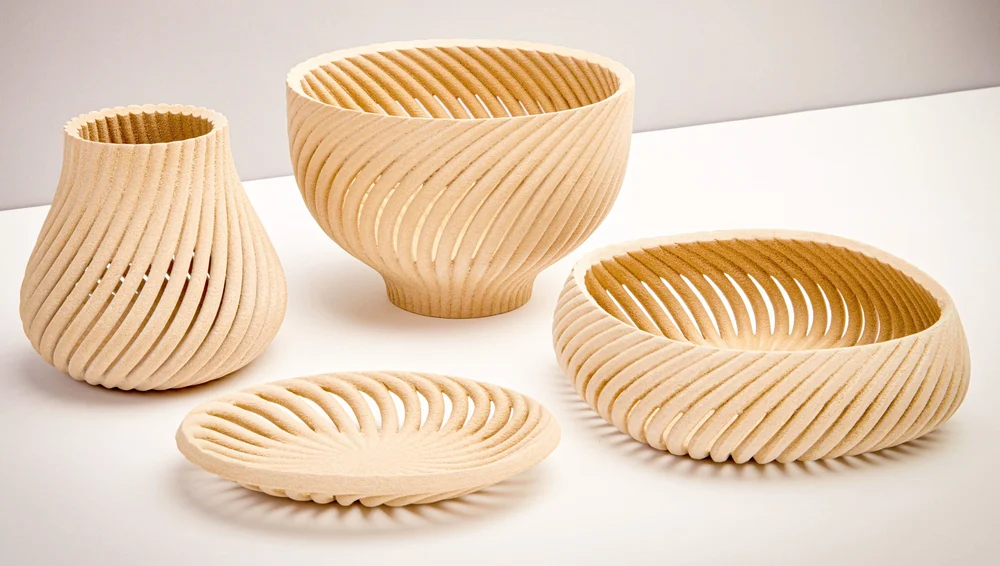
Basics of Binder Jetting – How it Works
Whether metal, plastic, sand, or another powdered material, the binder jetting process is the same. First, a recoating blade spreads a thin layer of powder over the build platform. Then, a printhead with inkjet nozzles passes over the bed, selectively depositing droplets of a binding agent that bonds the powder particles together. When the layer is complete, the build platform moves downwards and the blade recoats the surface. The process then repeats until the whole part is complete. Some versions of binder jetting technology incorporate heat to further fuse together the sections that received the binder liquid. There can also be colored inks introduced into the process.
After printing, the parts are encased in unused powder and often left to cure. Then the parts are removed from the powder bin and the excess powder collected and can be reused.
From here, depending on the material, post-processing is required, except for sand, which is usually ready to be used as a core or mold right from the printer.
Metal part post-processing first involves removing the binder from the metal part, and then heat treatment in a furnace to condense the part and remove the pours or holes left behind from removing the binder. Other post-processing can include filling the pours of the metal part with another material to create a desired matrix or composite material.
Plastic part post-processing often includes coating to improve the surface finish. You can also polish, paint, and sand polymer binder jetted parts.
Special thanks to Dr. Bastian Barthel, Project Manager Metal Additive Manufacturing / Metal Binder Jetting at the Fraunhofer IFAM research institute, and Dr. Alexander Azzawi, Head of Innovation Domain Binder Jetting Applications at Evonik specialty polymers for their technical review.
Source: https://all3dp.com/1/betting-on-binder-jetting-for-production-additive-manufacturing/