The Basics
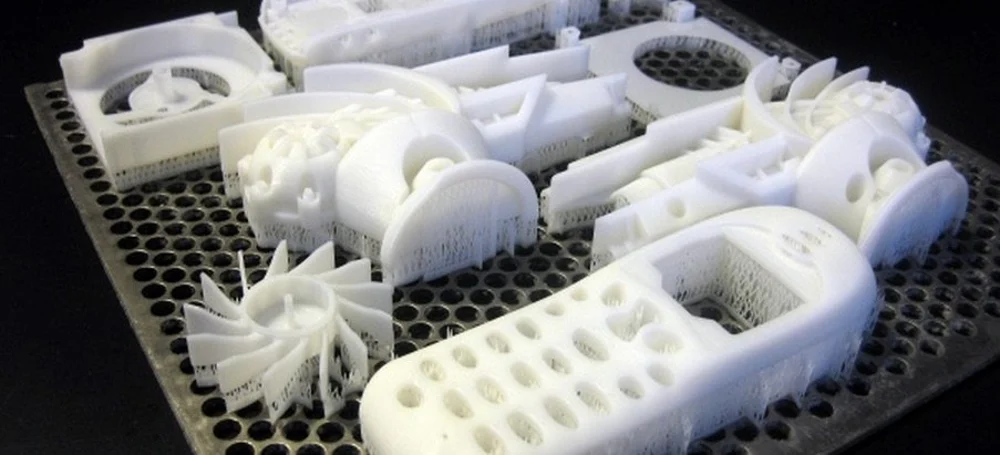
Stereolithography – more commonly referred to as SLA 3D printing – is one of the most popular and widespread techniques in the world of additive manufacturing. It works by using a high-powered laser to harden liquid resin that is contained in a reservoir to create the desired 3D shape. In a nutshell, this process converts photosensitive liquid into 3D solid plastics in a layer-by-layer fashion using a low-power laser and photopolymerization.
SLA is one of three primary technologies adopted in 3D printing, together with fused deposition modeling (FDM) and selective laser sintering (SLS). It belongs to the resin 3D printing category. A similar technique that is usually grouped with SLA is called digital light processing (DLP). It represents a sort of evolution of the SLA process, using a projector screen instead of a laser.
History
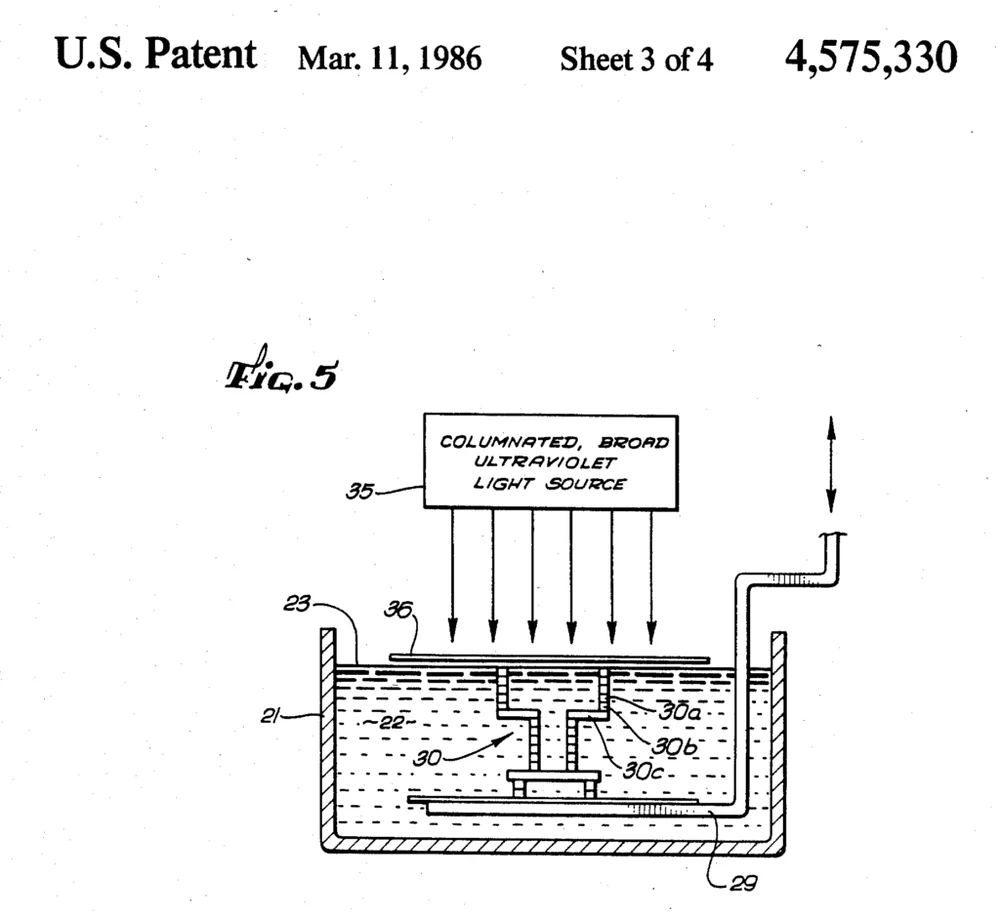
Despite being less popular than FDM technology, SLA is actually the oldest additive manufacturing technique.
The technology and the term were created in 1986 by Chuck Hull, founder of 3D printing company 3D Systems. According to him, SLA is a method of creating 3D objects by successively “printing” layers, by which he meant a photosensitive material.
In 1992, 3D Systems created the world’s first SLA apparatus, which made it possible to fabricate complex parts, layer by layer, in a fraction of the time it would normally take. SLA was the first entry into the rapid prototyping field during the 1980s and has continued to advance itself into a widely used technology.
Components
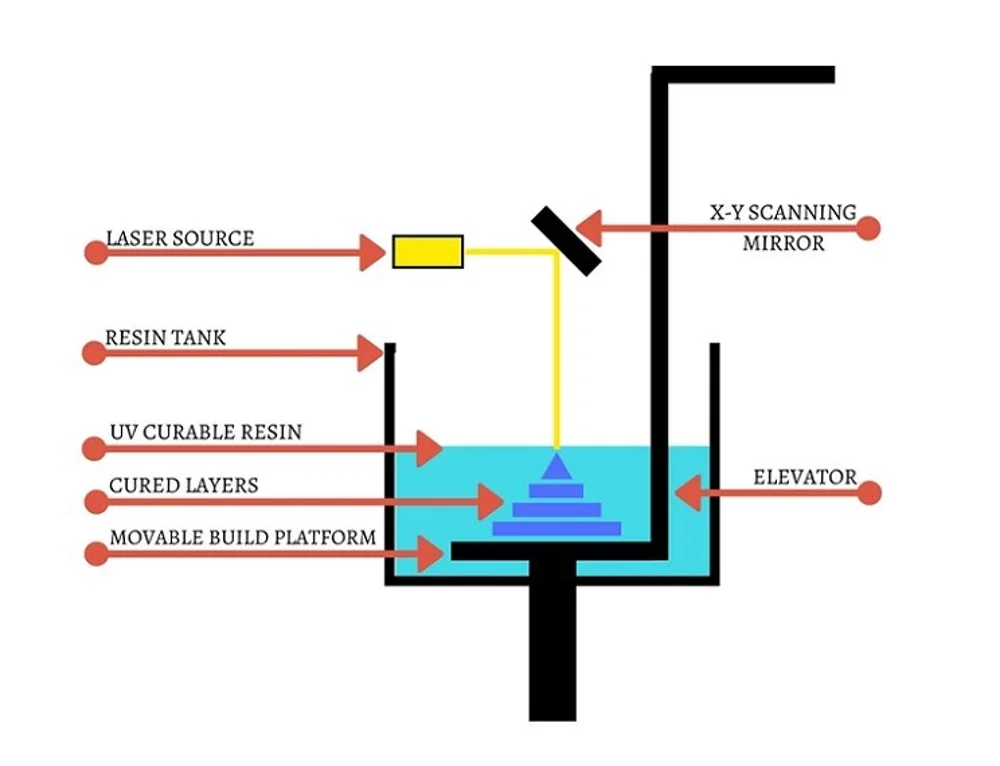
Every standard SLA 3D printer is generally composed of four primary sections:
- A tank filled with the liquid photopolymer: The liquid resin is usually a clear and liquid plastic.
- A perforated platform immersed in a tank: The platform is lowered into the tank and can move up and down according to the printing process.
- A high-powered, ultraviolet laser
- A computer interface, which manages both the platform and the laser movements
How Does It Work?
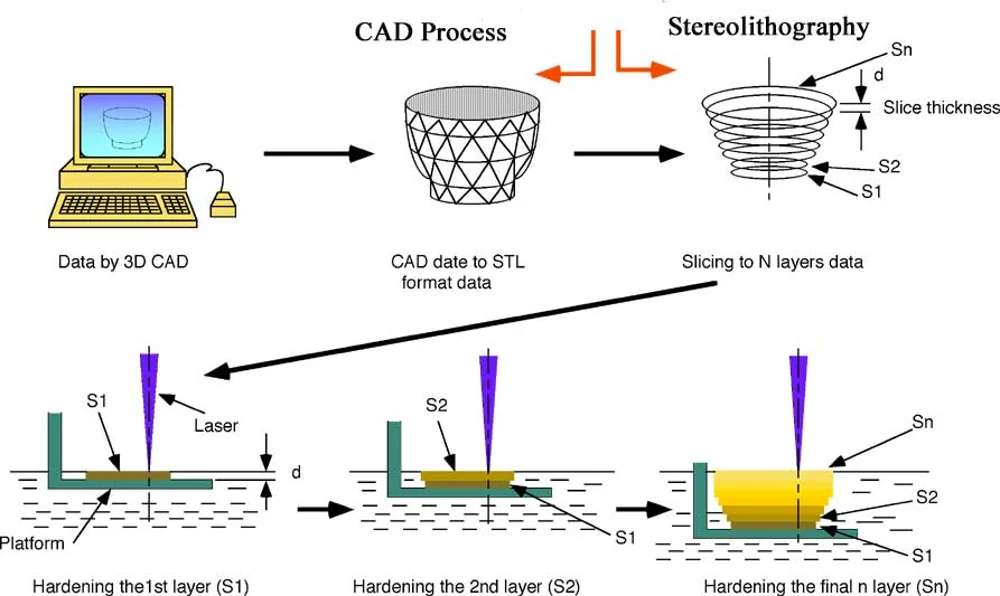
Software
As is the case for many additive manufacturing processes, the first step consists of designing a 3D model through CAD software. The resulting CAD files are digitalized representations of the desired object.
If they are not automatically generated as such, the CAD files must be converted into STL files. Standard tessellation language (STL), or “standard triangle language”, is a file format native to the stereolithographic software created by the Abert Consulting Group specifically for 3D Systems back in 1987. STL files describe the surface geometry of the 3D object, neglecting other common CAD model attributes, such as color and texture.
The pre-printer step is to feed an STL file into a 3D slicer software, such as Cura. Such platforms are responsible for generating G-code, the native language of 3D printers.
SLA 3D Printing
When the process starts, the laser “draws” the first layer of the print into the photosensitive resin. Wherever the laser hits, the liquid solidifies. The laser is directed to the appropriate coordinates by a computer-controlled mirror.
At this point, it’s worth mentioning that most desktop SLA printers work upside-down. That is, the laser is pointed up to the build platform, which starts low and is incrementally raised.
After the first layer, the platform is raised according to the layer thickness (typically about 0.1 mm) and the additional resin is allowed to flow below the already-printed portion. The laser then solidifies the next cross-section, and the process is repeated until the whole part is complete. The resin that is not touched by the laser remains in the vat and can be reused.
Post-Processing
After finishing the material polymerization, the platform rises out of the tank and the excess resin is drained. At the end of the process, the model is removed from the platform, washed of excess resin, and then placed in a UV oven for final curing. Post-print curing enables objects to reach the highest possible strength and become more stable.
Alternative Process: Digital Light Processing
As we mentioned before, one descendant of SLA is digital light processing (DLP). Unlike SLA, DLP uses a digital projector screen to flash a single image of each layer across the entire platform. As the projector is a digital screen, each layer will be composed of square pixels. Thus, the resolution of a DLP printer corresponds to pixel size, whereas with SLA, it’s the laser spot size.
Pros & Cons
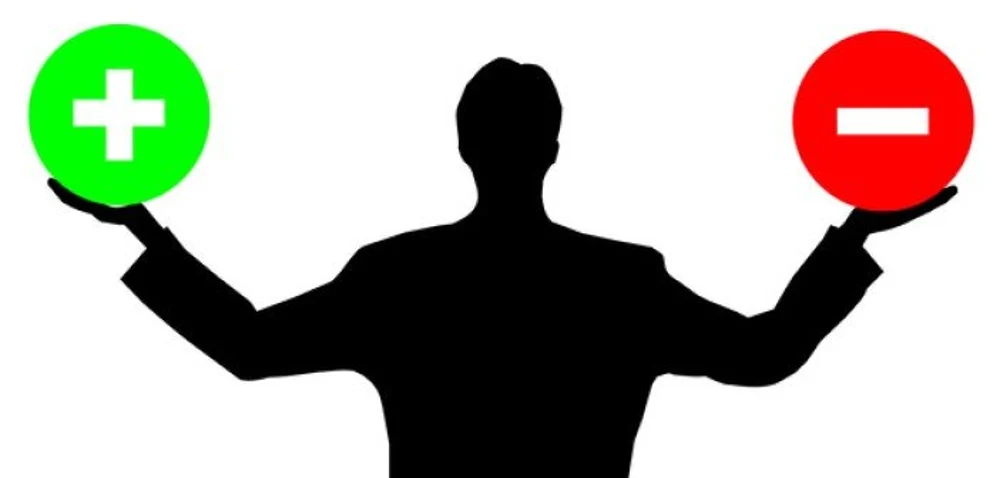
Pros
- SLA is one of the most precise 3D printing techniques on the market.
- Prototypes can be created with extremely high quality, with finely detailed features (thin walls, sharp corners, etc…) and complex geometrical shapes. Layer thicknesses can be made as low as 25 μm, with minimum feature sizes between 50 and 250 μm.
- SLA provides the tightest dimensional tolerances of any rapid prototyping or additive manufacturing technology: +/- 0.005″ (0.127 mm) for the first inch, and an additional 0.002″ for each additional inch.
- Print surfaces are smooth.
- Build volumes can be as high as 50 x 50 x 60 cm³ without sacrificing precision.
Cons
- Printing tends to take a long time.
- Steep slopes and overhangs require support structures during the building process. Such parts may potentially collapse during printing or curing phases.
- Resins are comparatively fragile and therefore not suitable for functional prototypes or mechanical testing.
- SLA offers limited material and color choice, usually offering black, white, grey and clear material. Resins are oftentimes proprietary and therefore cannot be easily exchanged between printers from different brands.
- SLA printing costs are comparatively high (e.g. machine, materials, lab environment).
SLA vs. FDM
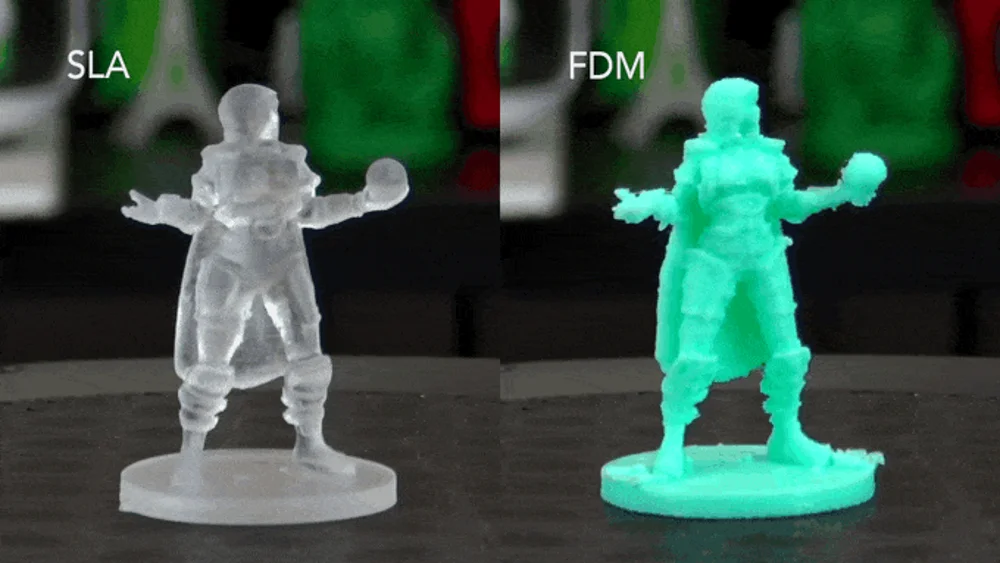
In FDM, filament is fed through a hot extruder and deposited layer-by-layer. The materials used are typically thermoplastics, but they can be mixed with other elements, including wood, metal, and carbon fiber. This is one advantage over SLA, which has only a limited choice of materials.
Whereas in FDM resolution refers to the precision of the motors, in SLA it depends on the tightness of the laser beam. This is why SLA is capable of producing objects of higher detail and accuracy.
An object printed using an FDM 3D printer is post-processed by removing supports (if present) and smoothening surfaces. In SLA, prints are submerged in isopropyl alcohol to remove excess resin before being subjected to passive UV light for extra strengthening. Nevertheless, the final result is in general not as strong as a product of FDM.
The cost of materials is decisively lower for FDM, since the printers are more affordable, and plastic reels are cheaper than resin.
In a nutshell, if high precision and a smooth finish are priorities, SLA will be your best bet. If cost and (to a lesser extent) durability play a role, use an FDM printer. For a more in-depth comparison, take a look at our article.
SLA vs. SLS
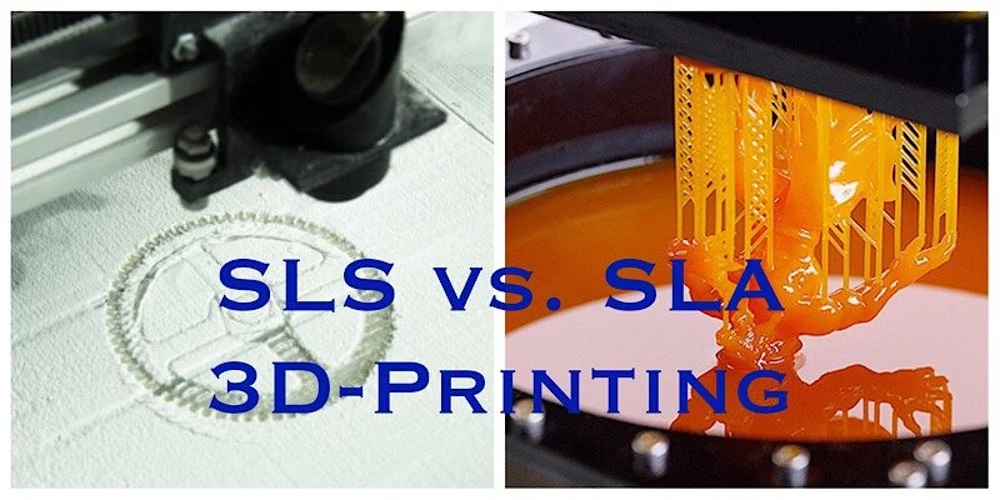
Selective laser sintering (SLS) involves an entirely different approach, although it also involves the use of a laser
Although it also uses a laser, it’s much more powerful. That’s because, instead of curing a substance, the beam heats a powder to the point of fusing its particles together. Often grouped with SLS are direct metal laser sintering (DMLS) and selective laser melting (SLM), which are specifically adapted to metals. Normal SLS works with polymers like nylon.
Compared to objects made with other technologies, SLS prints are especially strong and durable. Also, because supports aren’t necessary in SLS, prints can be of complex geometries. Detailing can be fairly high with SLS, it generally can’t compare to the precision of SLA.
Because of their highly powered lasers, SLS machines incorporate more advanced technology, including special shielding against harmful UV radiation. This results in printers that are more expensive, with few desktop or benchtop options available.
Furthermore, SLS powders are more expensive than liquid photopolymers.
In a nutshell, if high mechanical strength and complex shapes are your priority, and the cost is of minor importance, use an SLS printer. Otherwise, SLA is probably your best bet. For a more in-depth comparison, check out our article SLA vs SLS: The Differences – Simply Explained.
Final Remarks
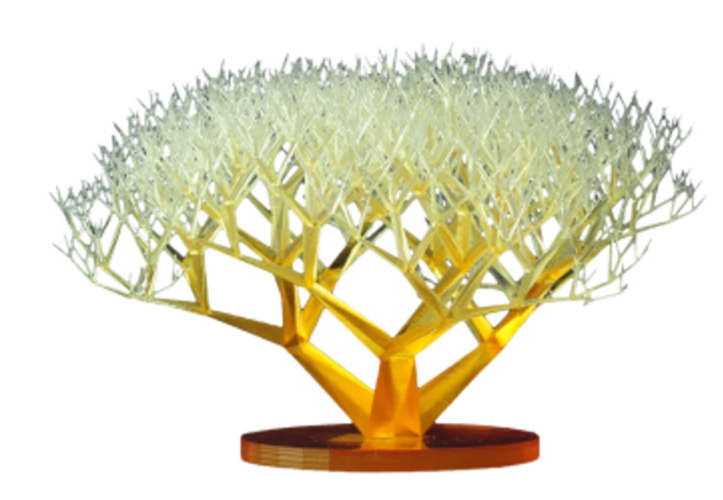
Although stereolithography is the first process developed for rapid prototyping, and the oldest among the main 3D printing methods, it still remains an attractive solution for creating prototypes with high accuracy and durability. Many industries and hobbyists use this process to build prototypes as well as final products, and the technology continues to become more affordable and accessible.
Source: https://all3dp.com/2/stereolithography-3d-printing-simply-explained/