An Introduction
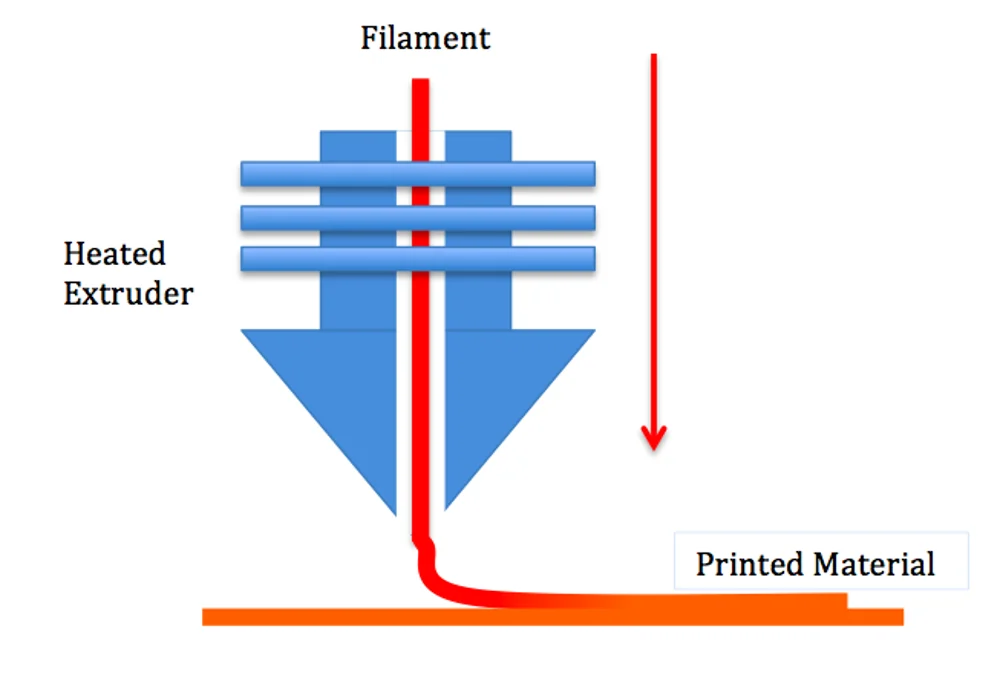
Fused deposition modeling, or FDM 3D Printing, is a method of additive manufacturing where layers of materials are fused together in a pattern to create an object. The material is usually melted just past its glass transition temperature, and then extruded in a pattern next to or on top of previous extrusions, creating an object layer by layer.
In layman’s terms, a typical FDM 3D printer takes a plastic filament and squeezes it through a hot end, melting it and then depositing it in layers on the print bed. These layers are fused together, building up throughout the print, and eventually they will form the finished part.
FDM is the same as fused filament fabrication (FFF), but the term “fused deposition modeling” and the abbreviated “FDM” were trademarked by Stratasys in 1991, creating the need for a second name.
Many types of materials can be used with FDM techniques, including the most common thermoplastics, chocolate, pastes, and even “exotic” materials like metal- or wood-infused thermoplastic.
Widely accepted as the simplest way to achieve 3D printing, FDM is cheap and fairly efficient. FDM 3D printers dominate the 3D printing market, almost drowning out more expensive methods. For a list of all 10 methods of 3D printing, take a look at this article, and to find the best 3D printers available today, have a look at this curated list.
Variations in Design and Capability
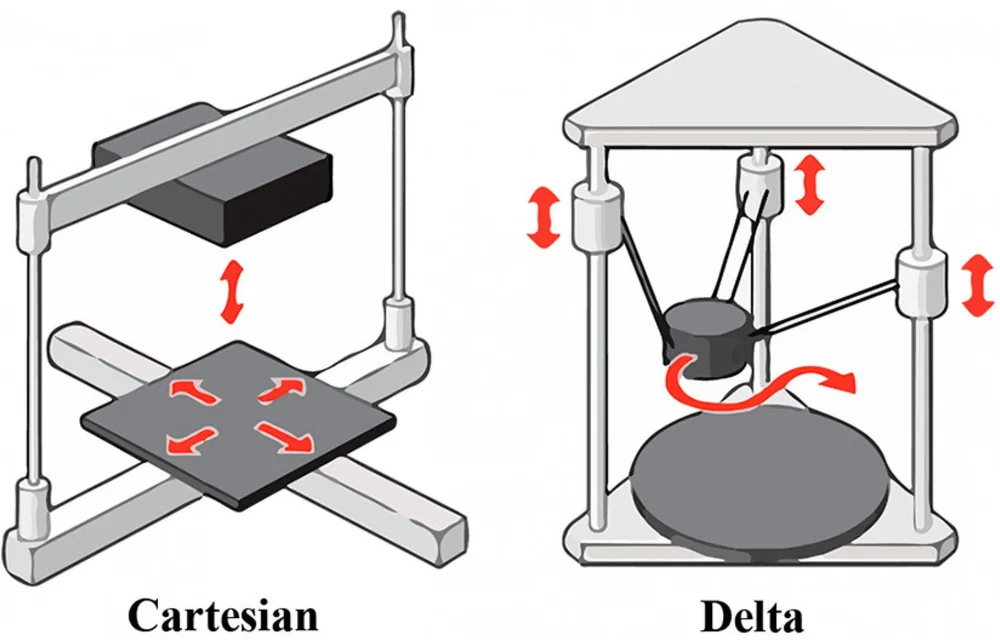
Variations in the extrusion system of fused deposition modeling 3D printers include, but are not limited to:
- Filament extruders, the most common and versatile variation which utilizes reels of thermoplastic filament
- Pellet extruders, exchanging the filament for granules of plastic
- Chocolate extruders (whoopee!)
- Paste extruders, where any paste can be extruded. Common uses are with ceramics and food. Paste extrusion is sometimes left in its own category, as the paste is not necessarily a thermoplastic material.
The common theme with all of these variations is that a substance is being extruded through a nozzle onto a build plate and/or fusing through heat or material adhesion to a previous layer in specific patterns to create a shape, which is the basis of an FDM 3D printer.
Other variations in FDM 3D printing include the systems of movement for all 3 axes on a printer. The two main variations are Cartesian 3D printers — like the RepRap/Prusa i3 or the CoreXY designs — and delta 3D printers. Each has advantages over the others, but they all use the same general method of printing.
Advantages and Disadvantages
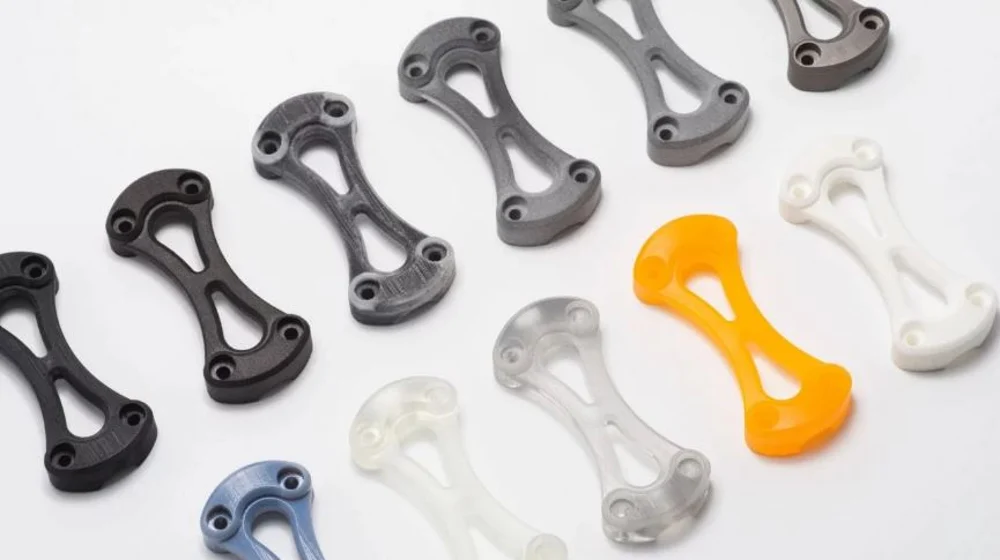
FDM offers a number of advantages over other 3D printing methods, but it also has some downsides.
Pros
One of the biggest advantages of FDM 3D printing is scalability: It can be easily scaled to any size. This is because the only constraint in the size of a build area is the movement of each gantry – make the gantry rails longer and the build area can be made larger. Of course, there are a few minor issues, and at a certain point the cost is no longer offset by the benefits, but no other printer design is capable of being scaled as easily with as few issues as FDM.
One of the more obvious benefits of having an easily-scalable design is the cost-to-size ratio. FDM printers are continually being made bigger and less expensive, due to low part costs and the simple designs involved. Other styles of printer cost many times more per unit area of build volume, simply because they are difficult to scale up and the key components are still quite expensive.
Another advantage is material flexibility. On any FDM printer, a wide variety of thermoplastic materials and exotic filaments can be printed with relatively few upgrades and modifications, something that cannot be said of other styles where a material must be a resin or fine powder.
Cons
One of the most often referenced downsides of FDM 3D printing is part quality or detail. Because the material must be extruded in layers, and has a certain thickness predefined by the nozzle, high detail prints are hard to achieve and often require lots of post-processing to acquire a professional, finished look. Another downside of the layers in FDM printing is that they create and inherent weak point in the print where each layer is joined, making prints less sturdy and unsuitable for certain applications.
Source: https://all3dp.com/2/fused-deposition-modeling-fdm-3d-printing-simply-explained/