From bowls to bone implants, the ceramic material is 3D printed for art and for the industry. Take a look at the latest in ceramic 3D printer technology.
3D Printing Brings Out the Best of Ceramic
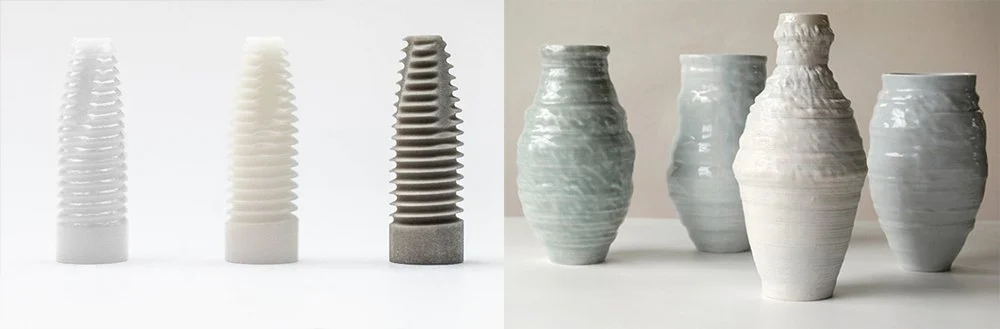
Even though there are hundreds of metals and plastics to 3D print with, ceramic materials have unique properties that are extremely valuable in both high-tech manufacturing and art. 3D printing heightens the appeal of this material because it not only enables you to create parts with shapes not currently possible with any other process, but it is far more cost-effective and faster than producing ceramic parts in the traditional way particularly for industrial applications.
First, we’ll take a look at how new printers and materials are igniting an explosion of 3D-printed ceramics in art, sculpture, and architecture. Then, we’ll dive deep into the growing use of 3D printed technical ceramics in industry and healthcare, and how this once-niche application is set to rival metal 3D printing in its wide range of applications.
Ceramic 3D printers are in a category of their own and within it are distinctly different machines for industry and art. We’ll guide you through the best on the market in both segments.
3D Ceramic Printing for Design
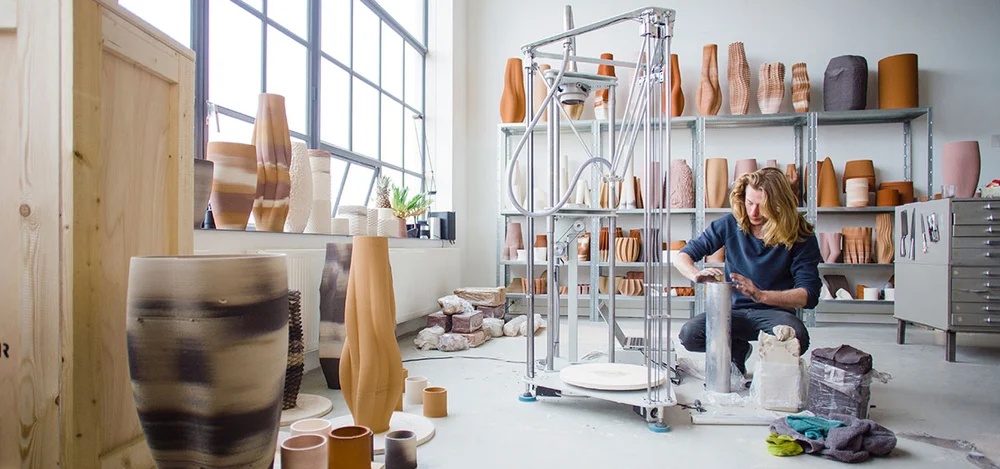
3D printing ceramics has inspired a new generation of artists, sculptors, and architects attracted to the ornate and exceptionally detailed shapes that would be impossible or too labor intensive using traditional ceramic processes. From pottery to architectural design applications, designers are finding new ways of crafting ceramics.
Ceramic artists, such as Jonathon Keep, Kate Blacklock, and Emre Can have been using 3D printing processes to create ceramic pieces for museum and private collections with stunning and unique results.
Keep creates his work with computer design software then 3D prints them in clay on a custom-made delta-arm 3D printer. After printing, the ceramic art is fired and glaze in the traditional way. The author offers the free “A Guide to Clay 3D Printing” online with 78-pages of printing and material tips. Blacklock uses binder jetting technology to 3D print her work in her Providence, R.I., studio.
3D printers have been used in recent years to extrude terracotta to create unique roof tiles, artificial reefs, and even entire buildings. They’ve been used to print building facades, including the blue ceramic archway in the historic Dutch city of Delft, which is world famous for its white and blue porcelain, and a 3D printed ceramic pavilion by Ceramic Morphologies that explores the design opportunities and expressive potential of ceramic 3D printing.
Ceramic Art Materials & Methods
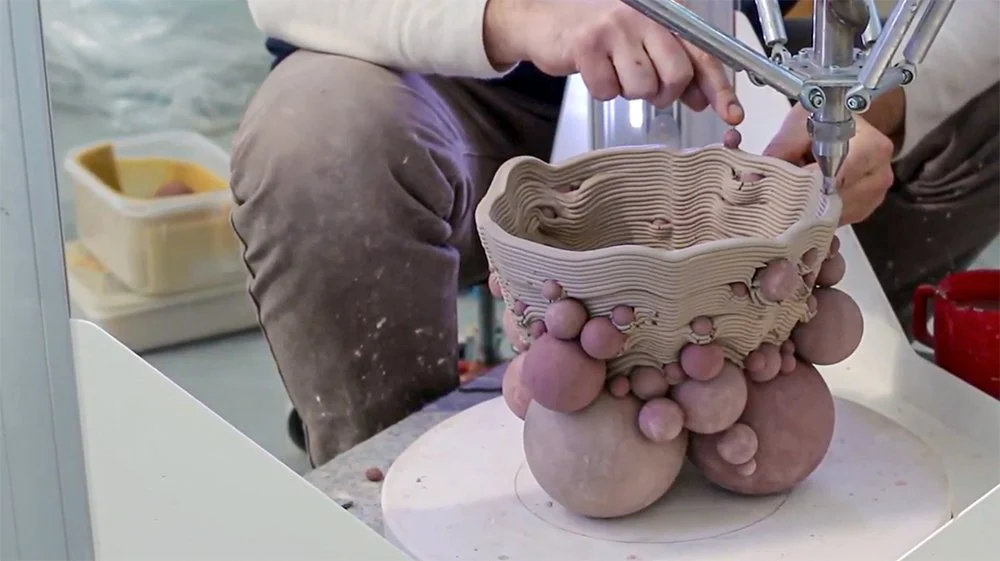
The terms ceramic and clay are often used interchangeably in art circles to describe different materials for making pottery. Of course, clay is a type of ceramic, but certainly not all ceramics are made of clay. Clay is a natural material that comes from the ground, and ceramics are various materials that harden when heated, including clay. When it comes to 3D printing, a wide range of clay material, including ceramic and terracotta, can be extruded through a nozzle to produce final shapes.
3D printers can extrude everything from Kaolin and porcelain clay to stoneware and terracotta, even concrete (but that’s a different story you can see here).
Extrusion, or fused deposition modeling (FDM), is by no means the only method for 3D printing ceramic art. Designers use binder jetting and to a lesser extent stereolithography and digital light processing (DLP) to produce complex ceramic parts from a liquid ceramic slurry.
There are 3D printers that work with a variety of materials. Usually, all that is required is a toolhead change or a material pre-setting, and off you go. Although these machines are not dedicated to ceramic 3D printing, they can “officially” produce ceramic parts out-of-the-box, and they are interesting alternatives that might be suitable for a number of different applications.
Below are five of our favorite 3D printers for ceramic and clay art.
DeltaBots 3D PotterBot Series
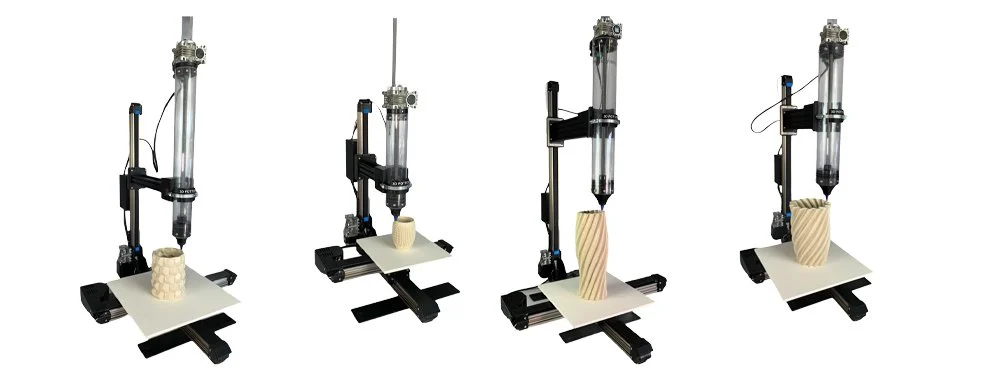
The 3D PotterBot series is one of the first truly dedicated ceramic 3D printers, being specifically designed for the pottery industry. It outputs large volumes of undiluted ceramic materials via its sizable capacity ram extruder, allowing for a continuous flow and precise prints.
This is done by eliminating the usual hose feedstock system, getting rid of lag and hysteresis caused by hoses. The constant extrusion ensures precise layer deposition throughout the entire print, and the extruder itself doesn’t use any external power sources or air compressors to propel the paste.
The company behind this printer, DeltaBots, has specially designed them for larger ceramic vessels. The Scara V4, for example, can print all the way up to one meter in height! Currently, there are strictly 6 different ceramic 3D PotterBot printers with a price range of $3,250 to $27,950.
Delta WASP 2040 & 40100 Clay
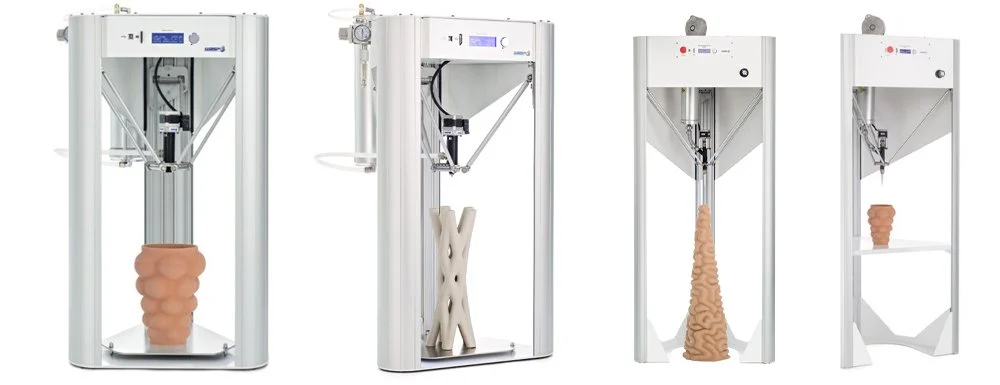
Italian 3D printer manufacturer WASP is known for its large delta 3D printers. They made headlines by using their big delta systems to build houses and shelters in developing countries.
Originally, WASP entered the ceramic printing world with the LDM clay extruder system, an add-on that can be used with their printers and also a handful of third-party 3D printers. When properly set up, this technology offers some of the most precise paste extrusion ceramic 3D printing on the market. The WASP clay kit will set you back about $760.
The company eventually recognized that some users would rather have an original ceramic 3D printer working out of the box. And that’s what they did. The WASP 2040 Clay and its big brother WASP 40100 Clay are both extrusion-based delta machines designed specifically for clay 3D printing.
The machines’ extrusion system has an output pressure multiplier of up to 40 bar and features an optional, yet unusual, retraction system. Costs are relatively low: the 2040 Clay costs around $3,300, with a build volume of Ø400 x 200 mm and a minimum layer height of 0.5 mm.
StoneFlower 3.0
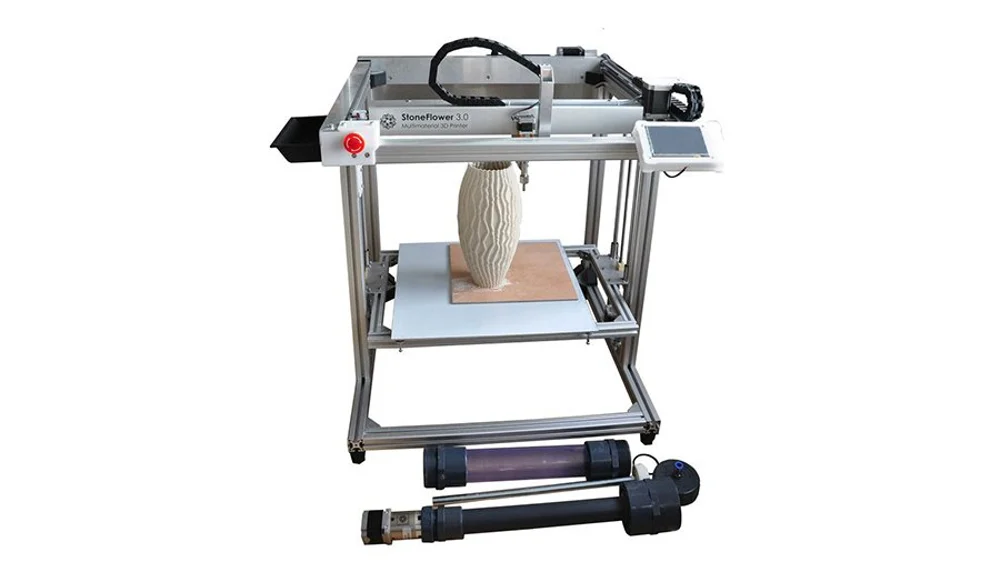
German StoneFlower offers a ceramic 3D printing suitable for prototyping and small production for arts, design, and architecture. The StoneFlower 3.0 Multimaterial printer produces parts as big as 480 x 480 x 500 mm in not only ceramics and porcelain but also other paste-like or viscous liquids like plaster, pulp, wax, and even soldering paste. Equipped with a 5-inch touchscreen control panel, this printer can also be fully controlled in real-time via WiFi.
The company also offers a clay extruder add-on system for adaptation to third-party 3D printers. Every kit includes a ram extruder, a print head, and a control unit. While the standard kit costs around $680, the StoneFlower 3.0 out-of-the-box 3D printer will set you back $3,850.
Cerambot Eazao & Delta
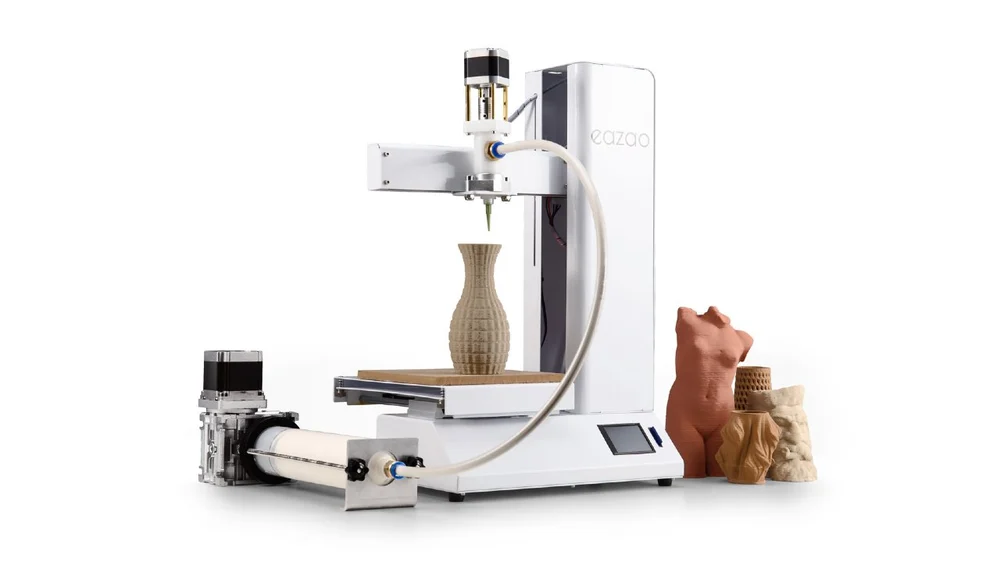
Although still in the kickstarter phase (meaning that it is taking orders to fund further development of its machines), the Cerambot Eazao is pretty promising.
This is Cerambot’s second kickstarted ceramic 3D printer. (The Eazao has already blasted past its $10,000 target.) The original Cerambot is a delta printer, but the company has now switched to a cartesian design for the Eazao, claiming it more stable and faster than the previous machine.
The Cerambot delta is $499, while the Eazao’s base price is $799. Cerambot also offers a larger pro model of the delta.
VormVrij 3D Lutum
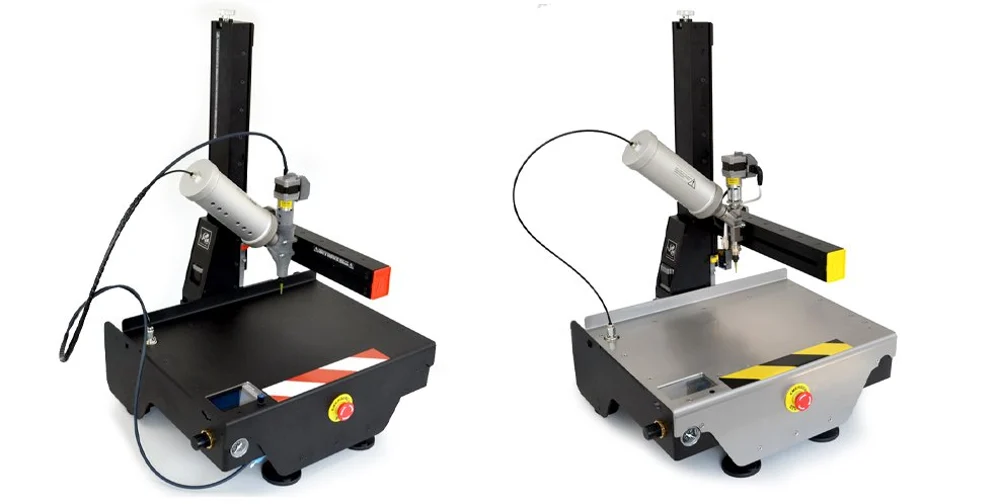
Dutch clay 3D printer maker VormVrij 3D offers five machines in their Lutum line, and introduced two new ones in 2021: a starter version, the 4M ($3,700), and the new smaller version of its popular 5 called the 5M ($7,400). M is for mini, since these machines have a smaller footprint and lower initial investment than the larger versions.
The new Lutum 5M is the smaller and more economic version of the Lutum 5 and capable of most of its functions, except it can only control one clay extruder. The company also recently introduced a new budget clay extruder that can be installed on any Lutum clay printer and is ideal for smaller DIY projects or the experimental clay print setup.
The Lutum line is capable of continuous clay flow, fast precision interrupted clay flow, and accelerated or decelerated clay flow. The stationary print bed enables you to work on the object while the print is ongoing, which is especially useful for potters who have a more hands-on approach. The 200º of freedom around the machine gives you full access to interact with the printed clay.
Depending on the chosen clay, nozzle sizes vary from 0.8 mm to 7 mm with layer height ranging from 0.5 mm to 3 mm. The optimal print range for the average clay is 1mm layer thickness with a 3-mm nozzle.
Except for the Lutum 4M, all printers are equipped with a touchscreen and can be fully controlled via Wi-Fi capable devices or networks. All printers need Gcode instructions to work, which can be generated by most slicing software packages, but the (free) Prusa Slicer app is the recommended software to prepare prints for Lutum.
Formlabs Form 3
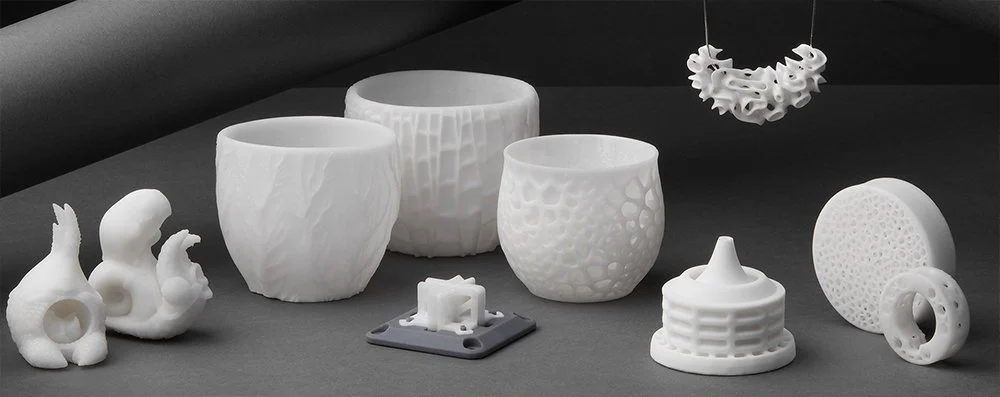
Unique on our list is the Formlabs Form 2 3D printer since it prints with the company’s ceramic resin instead of an extruded material. This machine is definitely a valuable addition to any engineer’s office, dental lab, or jewelry designer’s shop, as it really does turn ideas into reality. It can even be used to manufacture small batches.
With the release of its ceramic resin, you can now leverage the power of SLA technology (known to deliver more details than extruder technology) to produce precise ceramic parts at a fraction of the cost of industrial equipment. There are, however, a few “buts”.
For one, Formlabs markets this resin as “experimental”, stating that it’s a more complex material which “requires extra steps and additional experimentation for successful printing,” being more suitable for designers and enthusiasts rather than a production machine. Ceramic Resin is a silica-filled photopolymer. After firing, the photopolymer network burns out to form a true ceramic part.
In addition, the build volume of 125 × 125 × 165 mm is rather small when compared to its FDM competitors. Still, for finely detailed parts, this is a nice piece of kit.
3D Printing Ceramics for Industry
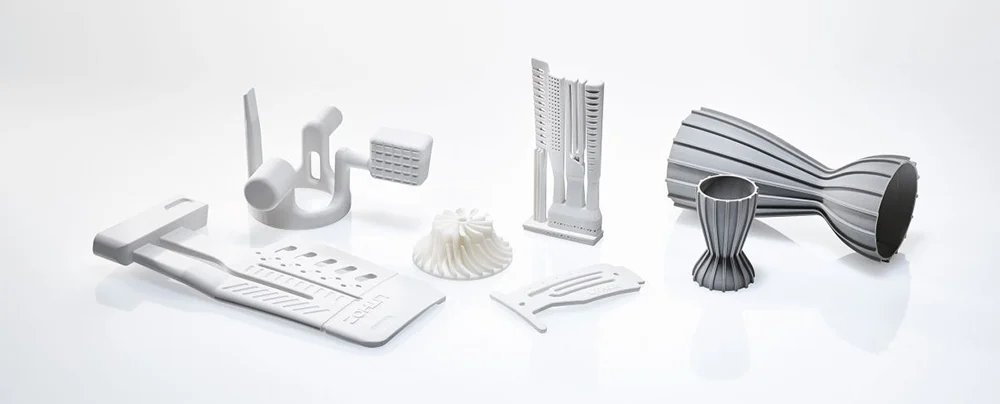
Aerospace, defense, and healthcare are driving the rapid adoption in industrial uses of 3D printed ceramics. In fact, the 3D printing ceramic market is growing at a remarkable pace. By 2025, it’s projected to be a $384 million market – more than double the market size from 2020.
Industrial ceramics are available in a range of properties and can be tough as the hardest metal, heat resistant enough for space applications, porous to enable cellular growth in the human body, wear resistant for the most demanding oil and gas industry applications, and ideal for electrical insulation. Today, manufacturers are using 3D printed technical ceramics in everything from automotive parts and hydraulics to satellites and investment casting.
3D printed ceramic bioresorbable patient-specific implants — able to be reabsorbed for regeneration in the body — have uniquely defined pore structures and geometries that require exceptionally precise manufacturing. These medical-grade implants, custom 3D printed to match each patient’s unique needs, are helping regenerate bones and repair defects from tumors and trauma.
Materials for Technical Ceramics
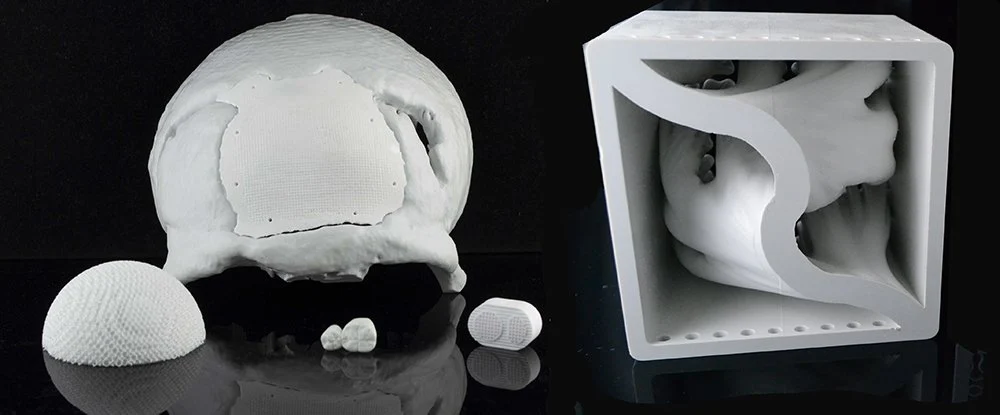
Unlike the design ceramics detailed above, technical ceramics (also called industrial or engineering ceramics) have nearly nothing to do with clay. They come in a wide variety of formulas ranging from aluminum oxide (Al2O3), which is the most common, to zirconium oxide (ZrO2) commonly called “ceramic steel”. There’s also tricalcium phosphate (TCP) used as a functional material for implants and bone replacement and silicon carbide (SiC) and boron carbide (B4C) used in oil and gas and automotive applications.
Unlike design ceramics, you’ll rarely find technical ceramics used with extrusion technology. More common is binder jetting, stereolithography (SLA), and digital light processing (DLP), and ceramic powder-based selective laser sintering and selective laser melting.
Below are seven of the top industrial 3D printers for technical ceramic parts.
3DCeram Series
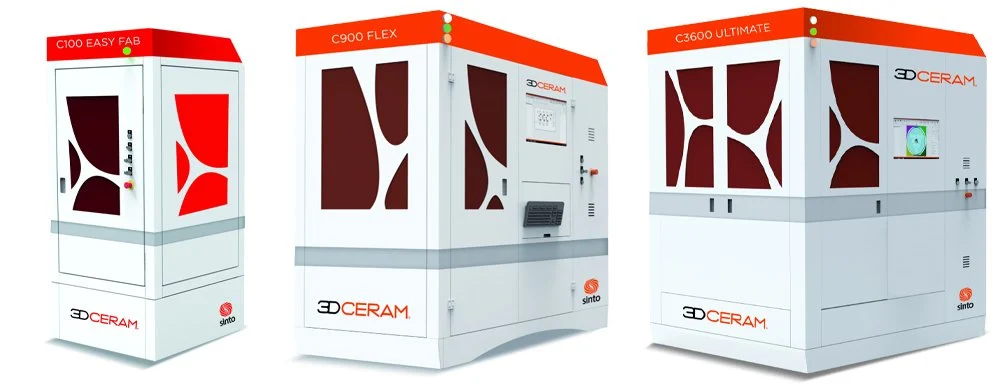
With over 15 years of expertise in ceramic 3D printing, French company 3DCeram might be your ideal partner for professional services. The company offers on-demand and serial production services, including materials consulting and R&D for new parts and components.
3DCeram developed its own ceramic 3D printers, which are also used for providing services. Their proprietary “support-link-free” technology is said to leave no support marks on any surface, and their services are said to be particularly suited to “mold-less production of small quantities of functional parts.”
Lithoz CeraFab S Series
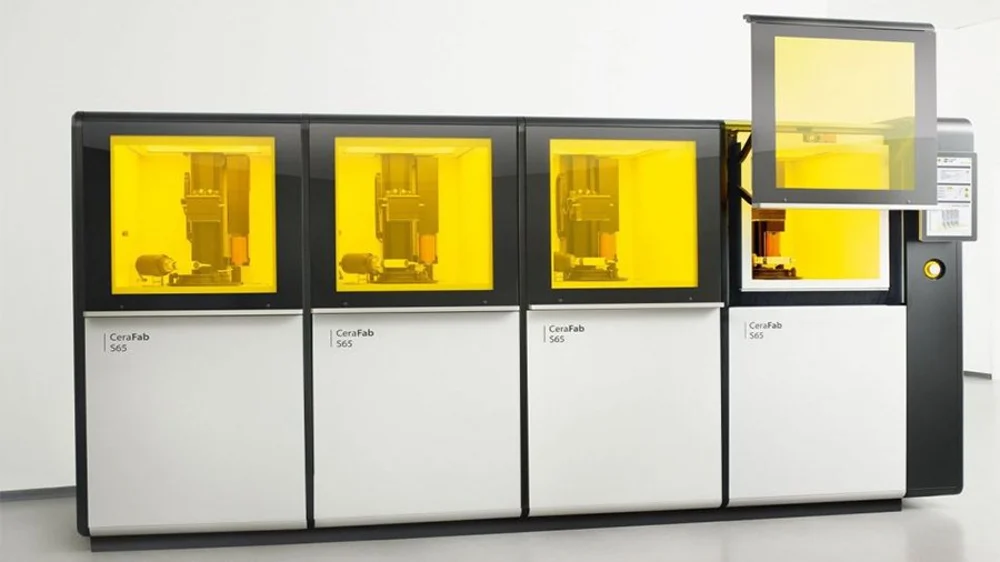
Austrian additive manufacturing company Lithoz focuses on 3D printers for high-performance and bioresorbable ceramics. The company recently announced its new ceramic 3D printer family, the CeraFab system. It comes in three models (S25, S65, and S230), which differ in resolution and build volume. The new CeraFab Lab L30 is a shop floor-friendly 3D printer with the full power of Lithoz’s original CeraFab 7500, expertly condensed and specifically developed as a starting point for ceramic 3D printing.
The CeraFab systems are DLP printers that pack high-definition projectors (2560 x 1600 pixels). But perhaps their most interesting feature is a modular design that allows for a combination of up to four production units, drastically increasing production output.
Lithoz CeraFab Control is the company’s database-driven software platform to promote complete traceability, intelligent data analysis of production related data and greater efficiency in manufacturing. For these and other reasons, the systems are especially suitable for the serial production of high-quality components required in the medical and aerospace industries.
Tethon 3D Bison 1000
US-based Tethon 3D straddles the line between design and industrial ceramic parts with its Bison 1000 DLP printer, but with it’s base price around $17,000 we’re going to put it here with the industrial machines.
Tethon 3D manufacturers ceramic powders for binder jetting and photo curable ceramic polymers for 3D printing and holds several patents related to ceramic 3D printing.
The Bison 1000 can print with the company’s ceramic resins in ceramic, glass-ceramic, and even flexible ceramic.
Admatic Admaflex 130 & 300
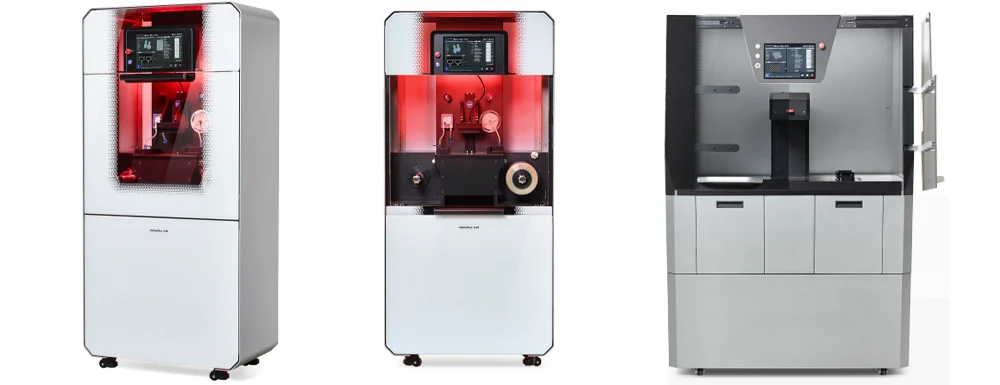
The Netherlands-based Admatec focuses on developing new 3D printing techniques for metal and ceramic materials.
Following the release of its first 3D printer, the Adamflex 130, in late 2019, the Dutch company unveiled its new ceramics printer: the Admaflex 300. It’s meant to produce large-scale parts, with a build volume of 200 x 200 x 300 mm, while featuring a patented feedstock system and a vision-based system for in-process monitoring. The AdmaPrint feedstock is specially formulated with a mixture of photosensitive resins and a solid load of powder (either ceramic or metal), called slurry. The use of light curing and slurries produces parts with high resolutions and very fine surface roughness in printed products.
ExOne X1 160Pro
German manufacturer ExOne is perhaps best known for its metal 3D printing systems and while the X1 160Pro binder jetting machine prints in nearly a dozen metals, it also prints in six ceramics including alumina, carbon, natural sands, and silicon carbide, materials often used in the medical (implants) and aerospace industries.
The 160Pro has a huge build volume of 800 x 500 x 400 mm, large enough for producing investment-cast parts. All binder jetting parts require post-processing steps, including sintering to increase the strength, just like any ceramics.
ExOne offers multiple 3D production printing machines that are able to print with ceramic powders, including the Rapidia, which uses a alumina-silica ceramic paste.
Scale and size of ExOne equipment makes binder jetting a commercially viable technology for additively manufacturing ceramic materials, the company says.
Voxeljet VX200 and VX1000
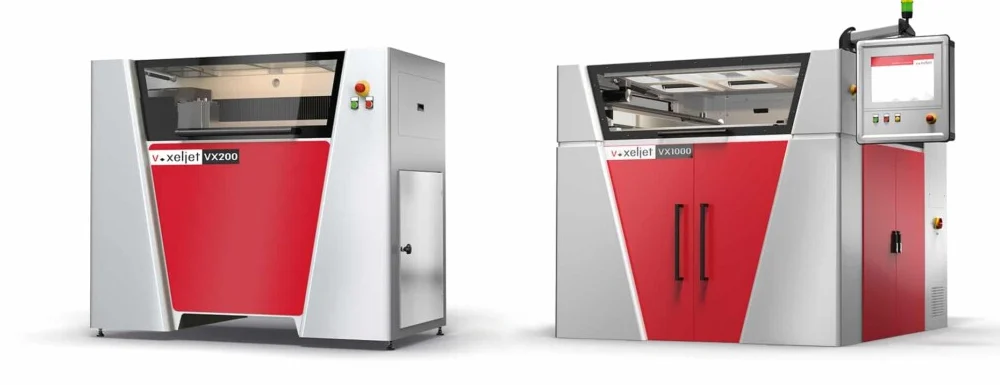
German company Voxeljet offers two industrial ceramic printers based on binder jetting technology.
The VX200 is capable of processing plastics and ceramics, while the VX1000 can process plastics, sand, and ceramics from medium-sized molds and cores for metal casting, to ceramic components.
XJet Carmel
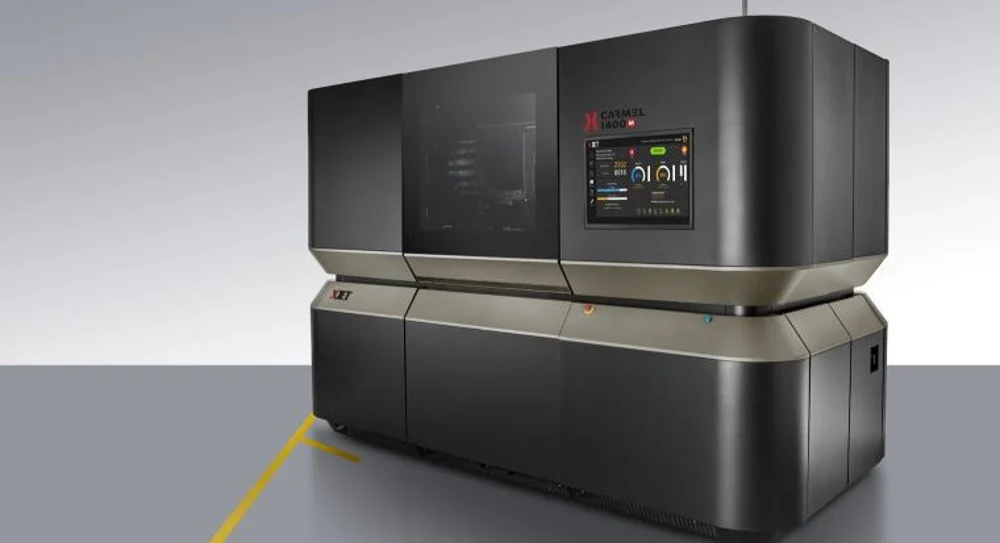
Isreal-based XJet takes a unique approach to industrial ceramic 3D printing with a material jetting technology the company calls NanoParticle Jetting. Unlike other ceramic printers, the Carmel 1400C does not use ceramic powder or a vat of ceramic slurry. Instead the materials, a ceramic liquid material and a separate soluble support liquid, are jetted onto the build plate through thousands of tiny ink jets.
Featuring a 1,400 cm² build tray, the Carmel 1400C enables the simultaneous production of multiple ceramic parts.
After printing, parts are moved into XJet’s SMART (Support Material Automatic Removal Technology) station that automates the post-printing removal of the soluble supports. Lastly parts undergo an overnight sintering process.
XJet ceramic materials include zirconia and alumina in convenient sealed cartridges.
Get Your Ceramic Parts 3D Printed
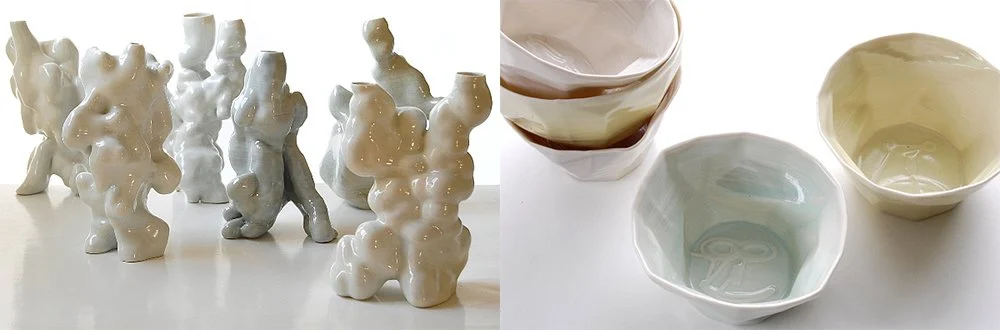
If you’ve read other guides to printing with metals and plastics you know that here is where we tell you about all the 3D printing services that will 3D print your parts for you. Not so with ceramics. The large global 3D print shops, including Craftcloud, Sculpteo, Xometry, and i.Materalise do not offer technical or design ceramics. Hopefully this will change as demand grows.
For now, though, you’re not totally out of luck. For technical ceramic parts, Admatec, the printer manufacturer mentioned above offers its customers in the EU ceramic print services through a partner, Formatec in the Netherlands. The German 3D printing company ProTIQ offers ceramic stereolithography 3D printing, and in the US you can reach out to Calix Ceramic Solutions.
For design ceramics, check out Kwambio, a New York-based 3D printing company focused on ceramic materials. The company has been extensively used by artists and designers, but also produces parts for industrial use.