All types of 3D printing technology that 3D printers use today. Learn about FDM, SLA, MSLA, DLP, SLS, DMLS, SLM, EBM, material jetting, DOD, binder jetting, and more.
If you’re new to the wonderful world of 3D printing, then may we be the first to offer you a warm welcome. You’re going to have lots of fun.
The challenge that many newcomers to 3D printing face is distinguishing between the different processes and materials available. What’s the difference between types of 3D printing like FDM and SLS, for example? Or SLS and binder jetting? Or EBM and DMLS? It can be pretty confusing, and with so many different acronyms flying around, you’d be forgiven for mistaking a type of 3D printing for a genre of dance music.
Truth is, 3D printing, also commonly referred to as additive manufacturing, is an umbrella term that encompasses a group of different 3D printing processes. In 2015, the ISO/ASTM 52900 standard was created with the aim to standardize all terminology and classify each of the different types of 3D printers.
In total, seven categories of additive manufacturing processes have been identified and established so far. These seven 3D printing processes have brought forth many different types of 3D printing technologies that 3D printers use today. In this article, we’ve done our best to outline what they are and simply explain how they work.
3D PRINTING PROCESS: MATERIAL EXTRUSION
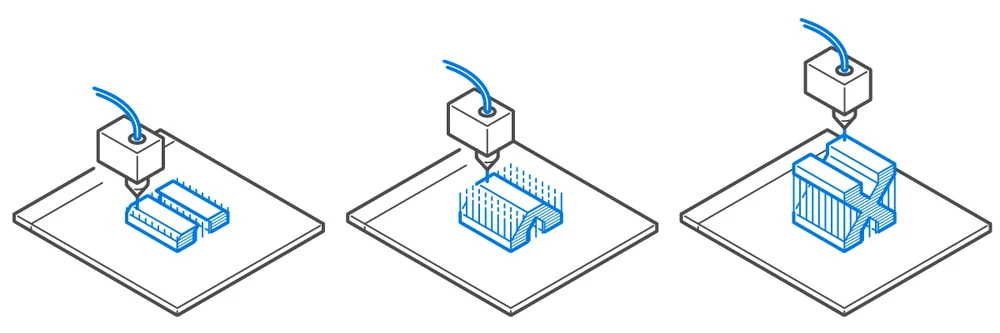
Material extrusion is exactly what it sounds like: material being extruded through a nozzle. Most of the time that material is a plastic filament pushed through a heated nozzle, melting it in the process. The printer deposits the material on a build platform along a predetermined path, where the filament then cools and solidifies to form a solid object. You can also extrude metal paste, biogels, concrete, chocolate, and a wide range of other materials, but plastics are the most common.
- Types of 3D Printing Technology: Fused deposition modeling (FDM), sometimes called fused filament fabrication (FFF)
- Materials: Plastic filament (PLA, ABS, PET, PETG, TPU, Nylon, ASA, PC, HIPS, Carbon Fiber, and many more.) and other material
- Dimensional Accuracy: ±0.5% (lower limit ±0.5 mm)
- Common Applications: Electrical housings, form and fit testings, figs and fixtures, investment casting patterns, etc.
- Strengths: Lowest cost 3D printing method, wide range of materials
Fused Deposition Modeling (FDM)
Material Extrusion devices are the most commonly available – and affordable – types of 3D printing technology globally. You might be familiar with them as fused deposition modeling or FDM. They are also sometimes referred to as fused filament fabrication or FFF.
The way it usually works is that a spool of filament is loaded into the 3D printer and fed through to a printer nozzle in the extrusion head. The printer nozzle is heated to the desired temperature, whereupon a motor pushes the filament through the heated nozzle, causing it to melt.
The printer then moves the extrusion head along with specified coordinates, laying down the molten material onto the build plate, where it cools down and solidifies. Once a layer is complete, the printer proceeds to lay down another layer. This process of printing cross-sections is repeated, building layer-upon-layer until the object is fully formed.
Depending on the object’s geometry, it is sometimes necessary to add support structures, for example, if a model has steep overhanging parts.
FDM is used is in 3D printed buildings by extruding clay or concrete, 3D printed deserts by extruding chocolate, 3D printed organs by extruding live cells in a bio gel, you get the idea. If it can be extruded, it can be 3D printed, well almost.
3D PRINTING PROCESS: VAT POLYMERIZATION
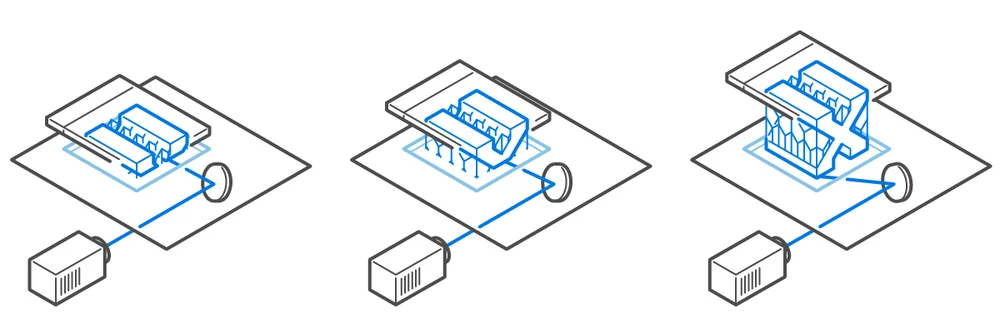
Vat polymerization is a 3D printing process where a light source selectively cures a photopolymer resin in a vat. In other words, light is precisely directed to a specific point on a thin layer of liquid plastic to harden it. This process is repeated layer by layer until the 3D part is formed.
Three common forms of vat polymerization are stereolithography (SLA), digital light processing (DLP), and masked stereolithography (MSLA). The fundamental difference between these types of 3D printing technology is the light source they use to cure the resin and we detail each method below.
Some 3D printer manufacturers, especially those that make professional-grade 3D printers, use slightly unique and patented variations of vat polymerization, so you may see different types of SLA on the market. One manufacturer, Carbon, uses a vat polymerization technology it calls Digital Light Synthesis (DLS), Origin by Stratasys calls its technology Programmable Photopolymerization (P³), Formlabs offers what it called Low Force Stereolithography (LFS), and Azul 3D is the first to commercialize the high area rapid printing (HARP) form of vat polymerization. There’s also lithography‐based metal manufacturing (LMM), projection micro-stereolithography (PµSL), and Digital Composite Manufacturing (DCM), which is a filled-photopolymer technology that introduces functional additives, such as metal and ceramic fibers, to liquid resin.
- Types of 3D Printing Technology: Stereolithography (SLA), masked stereolithography (MSLA), microstereolithography (µSLA), and more.
- Materials: Photopolymer resins (castable, transparent, industrial, biocompatable, etc.)
- Dimensional Accuracy: ±0.5% (lower limit ±0.15 mm or 5 nanometers with µSLA)
- Common Applications: Injection mold-like polymer prototypes; jewelry casting; dental applications
- Strengths: Smooth surface finish, fine feature details
Stereolithography (SLA)
An SLA printer uses mirrors, known as galvanometers or galvos, with one positioned on the X-axis and another on the Y-axis. These galvos rapidly aim a laser beam across a vat of resin, selectively curing and solidifying a cross-section of the object inside this building area, building it up layer by layer.
Most SLA printers use a solid-state laser to cure parts. The disadvantage of these types of 3D printing technology using a point laser is that it can take longer to trace the cross-section of an object when compared to our next method (DLP), which hardens an entire layer at once.
Digital Light Processing (DLP)
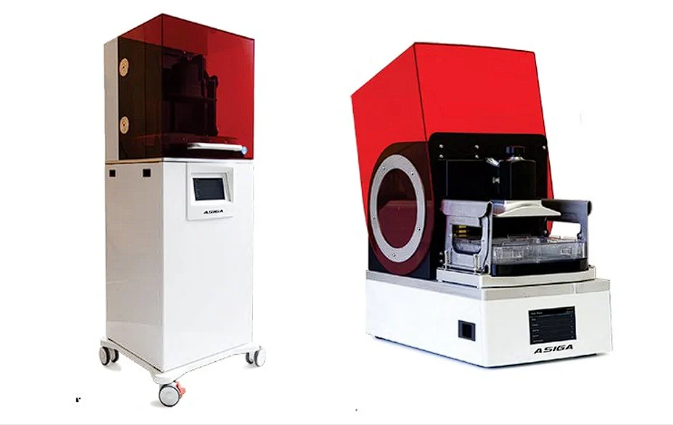
Looking at digital light processing machines, these types of 3D printers are almost the same as SLA. The key difference is that DLP uses a digital light projector to flash a single image of each layer all at once (or multiple flashes for larger parts).
Because the projector is a digital screen, the image of each layer is composed of square pixels, resulting in a layer formed from small rectangular blocks called voxels.
Light is projected onto the resin using light-emitting diode (LED) screens or a UV light source (lamp) that is directed to the build surface by a digital micromirror device (DMD).
A DMD is an array of micro-mirrors that control where light is projected and generate the light-pattern on the build surface.
Masked Stereolithography (MSLA)
Masked Stereolithography uses an LED array as its light source, shining UV light through an LCD screen displaying a single layer slice as a mask — hence the name.
Like DLP, the LCD photomask is digitally displayed and composed of square pixels. The pixel size of the LCD photomask defines the granularity of a print. Thus, the XY accuracy is fixed and does not depend on how well you can zoom/scale the lens, as is the case with DLP. Another difference between DLP-based printers and MSLA technology is that the latter utilizes an array of hundreds of individual emitters rather than a single-point emitter light source like a laser diode or DLP bulb.
Similar to DLP, MSLA can, under certain conditions, achieve faster print times compared to SLA. That’s because an entire layer is exposed at once rather than tracing the cross-sectional area with the point of a laser.
Due to the low cost of LCD units, MSLA has become the go-to technology for the budget desktop resin printer segment.
Other Vat Polymerization Technologies
As we mentioned above there’s a growing list of proprietary takes on vat polymerization, particularly in professional circles. Instead of talking about each one individually and risk repeating ourselves, here we’ve compiled them in list form with links to relevant manufacturer sites where you can read more.
3D PRINTING PROCESS: POWDER BED FUSION
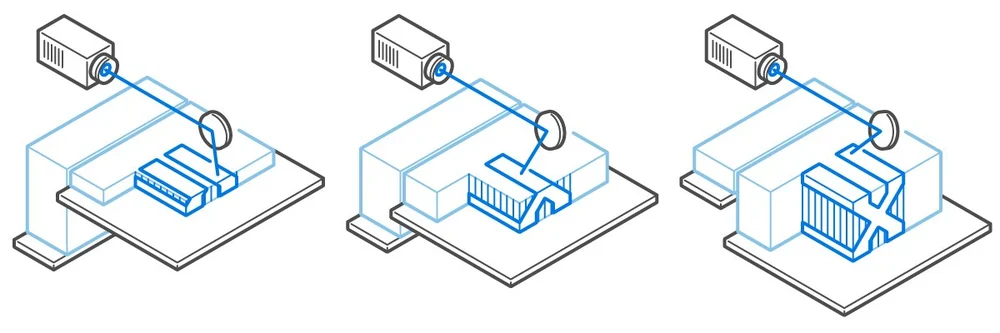
Powder bed fusion is a 3D printing process where a thermal energy source selectively induces fusion between powder particles (plastic, metal, or ceramic) inside a build area to create a solid object layer by layer.
Powder bed fusion devices spread a thin layer of powdered material over the print bed, typically with a type of blade or wiper. Energy fused specific points on the powder layer, then another powder layer is deposited and the process repeats until the entire object is fabricated. The final item is encased and supported in the unfused powder.
- Types of 3D Printing Technology: Selective laser sintering (SLS), selective laser melting (SLM), electron beam melting (EBM), direct metal laser sintering (DMLS), Multi Jet Fusion (MJF)
- Materials: Thermoplastic powders (Nylon 6, Nylon 11, Nylon 12, etc.), metal powders (steel, titanium, aluminum, cobalt, etc.), ceramic powders
- Dimensional Accuracy: ±0.3% (lower limit ±0.3 mm)
- Common Applications: Functional parts, complex ducting (hollow designs), low-run part production
- Strengths: Functional parts, excellent mechanical properties, complex geometries
Selective Laser Sintering (SLS)
Creating an object with powder bed fusion technology and polymer powder is generally known as selective laser sintering (SLS). As industrial patents expire, these types of 3D printing technologies are becoming increasingly common and lower cost.
First, a bin of polymer powder is heated to a temperature just below the polymer’s melting point. Next, a recoating blade or wiper deposits a very thin layer of the powdered material – typically 0.1 mm thick – onto a build platform. A CO2 or fiber laser then begins to scan the surface. The laser selectively sinters the powder and solidifies a cross-section of the object. Just like SLA, the laser is focused on the correct location by a pair of galvos.
When the entire cross-section is scanned, the build platform will move down one layer thickness in height. The recoating blade deposits a fresh layer of powder on top of the recently scanned layer, and the laser will sinter the next cross-section of the object onto the previously solidified cross-sections.
These steps are repeated until all objects are entirely manufactured. The powder that hasn’t been sintered remains in place to support the object, which reduces or eliminates the need for support structures.
Micro selective laser sintering (μSLS) is essentially selective laser sintering (SLS) on a tiny scale and often called micro laser sintering. Although SLS usually refers to a process with plastics, here μSLS more commonly refers to a laser sintering process with metals. μSLS can produce true 3D metal parts with sub-5 μm resolution and a throughput of greater than 60 mm3/hour.
In μSLS, a layer of metal nanoparticle ink is coated onto a substrate then dried to produce a uniform nanoparticle layer. Next, laser light that has been patterned using a digital micromirror array is used to heat and sinter the nanoparticles into the desired patterns. This set of steps is then repeated to build up each layer of the 3D part in the μSLS system.
Direct Metal Laser Sintering (DMLS) / Selective Laser Melting (SLM)
Both direct metal laser sintering (DMLS) and selective laser melting (SLM) produce objects in a similar fashion to SLS. The main difference is that these types of 3D printing technology are applied to the production of metal parts.
DMLS does not melt the powder but instead heats it to a point so that it can fuse on a molecular level. SLM uses the laser to achieve a full melt of the metal powder forming a homogeneous part. This results in a part that has a single melting temperature (something not produced with an alloy).
This is the main difference between DMLS and SLM; the former produces parts from metal alloys, while the latter forms single element materials, such as titanium. Unlike SLS, the DMLS and SLM processes require structural support to limit the possibility of any distortion that may occur (despite the fact that the surrounding powder provides physical support).
DMLS/SLM parts are at risk of warping due to the residual stresses produced during printing because of the high temperatures, yet because DMLS doesn’t melt the powder, parts can have less stress. After printing, parts are also typically heat-treated to relieve any stresses in the parts.
Electron Beam Melting (EBM)
Distinct from other powder bed fusion techniques, electron beam melting (EBM) uses a high energy beam, or electrons, to induce fusion between the particles of metal powder.
A focused electron beam scans across a thin layer of powder, causing localized melting and solidification over a specific cross-sectional area. These areas are built up to create a solid object.
Compared to SLM and DMLS types of 3D printing technology, EBM generally has a superior build speed because of its higher energy density. However, things like minimum feature size, powder particle size, layer thickness, and surface finish are typically larger.
Also important to note is that EBM parts are fabricated in a vacuum, and the process can only be used with conductive materials.
Multi Jet Fusion (MJF)
Multi Jet Fusion is technically a powder bed fusion 3D printing technology although it has similarities to binder jetting. MJF was introduced to the market by HP in 2016. The company explains its technology is built on decades of HP’s investment in inkjet printing, jettable materials, precision low-cost mechanics, material science, and imaging.
The technology gets its name from the multiple inkjet heads that carry out the printing process. The processes of material recoating and agent distribution and heating are carried out by separate head arrays that move across the print bed in different directions, thus allowing the user to optimize both processes independently.
In the Multi Jet Fusion printing process, the printer lays down a layer of material powder on the printing bed. Following this, an inkjet head runs across the powder and deposits both a fusing and a detailing agent onto it.
An infrared heating unit then moves across the print. Wherever a fusing agent was added, the underlying layer melts together, while the areas with detailing agent remain as a powder. The powdery parts shed off, which produces the desired geometry. This also eliminates the need for modeling supports, as the lower layers support those printed above them.
HP says that a Multi Jet Fusion printer differs from most other 3D printing technologies in that each new material and agent layer is placed while the previous layer is still molten. This lets both layers fuse completely, delivering improved print durability and finer detail.
To finish the printing process, the entire powder bed – and the printed parts in it – are moved to a separate processing station. Here, the majority of the loose unfused powder is vacuumed up, allowing it to be reused instead of producing excess waste.
3D PRINTING PROCESS: MATERIAL JETTING
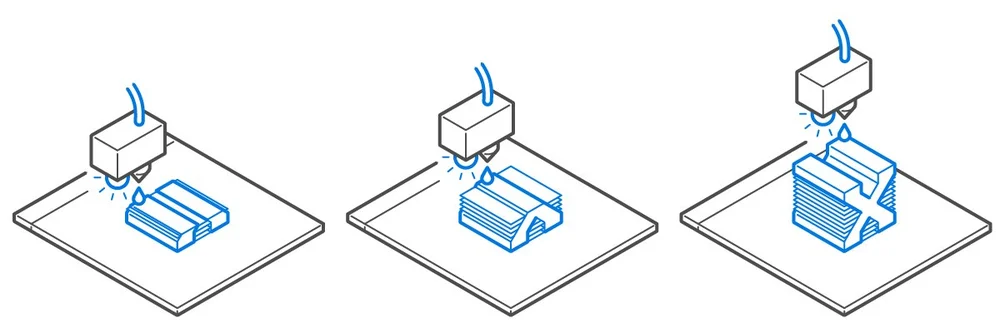
Material jetting is a 3D printing process where droplets of material are selectively deposited and cured on a build plate. Using photopolymers or wax droplets that cure when exposed to light, objects are built up, one layer at a time.
The nature of the material jetting process allows for different materials to be printed in the same object. One application for this technique is to fabricate parts in multiple colors and textures.
- Types of 3D Printing Technology: Material Jetting (MJ), Drop on Demand (DOD)
- Materials: Photopolymer resin (Standard, Castable, Transparent, High Temperature)
- Dimensional Accuracy: ±0.1 mm
- Common Applications: Full-color product prototypes; Injection mold-like prototypes; Low run injection molds; Medical models
- Strengths: Best surface finish; Full color and multi-material available
- Weaknesses: Brittle, not suitable for mechanical parts; Higher cost than SLA/DLP for visual purposes
Material Jetting (MJ)
Material jetting (MJ) works in a similar way to a standard inkjet printer. The key difference is that, instead of printing a single layer of ink, multiple layers are built upon each other to create a solid part.
The print head jets hundreds of tiny droplets of photopolymer and then cures/solidifies them using ultraviolet (UV) light. After one layer has been deposited and cured, the build platform is lowered down one layer thickness, and the process is repeated to build up a 3D object.
MJ is different from other types of 3D printing technology that deposit, sinter, or cure build material using a point-wise deposition. Instead of using a single point to follow a path that outlines the cross-sectional area of a layer, MJ machines deposit build material in a rapid, line-wise fashion.
The advantage of line-wise deposition is that MJ printers can fabricate multiple objects in a single line with no impact on build speed. So long as models are correctly arranged, and the space within each build line is optimized, MJ can produce parts faster than other types of 3D printers.
Objects made with MJ require support, which is printed simultaneously during the build from a dissolvable material that is removed during the post-processing stage. MJ is one of the only types of 3D printing technology to offer objects made from multi-material printing and full-color.
Drop on Demand (DOD)
Drop on Demand (DOD) is a type of 3D printing technology that uses a pair of inkjets. One deposits the build materials, which is typically a wax-like material. The second is used for dissolvable support material. As with typical types of 3D printing technology, DOD printers follow a predetermined path to jet material in a point-wise deposition, creating the cross-sectional area of an object layer-by-layer.
DOD printers also use a fly-cutter that skims the build area after each layer is created, ensuring a perfectly flat surface before commencing the next layer. DOD printers are usually used to create patterns suitable for lost-wax casting or investment casting and other mold-making applications.
Other Material Jetting Technologies
There isn’t too much variation in Material Jetting technology, but you may see the technology referred to as one of the following. We’ve listed and linked them for clarity and further reading.
3D PRINTING PROCESS: BINDER JETTING
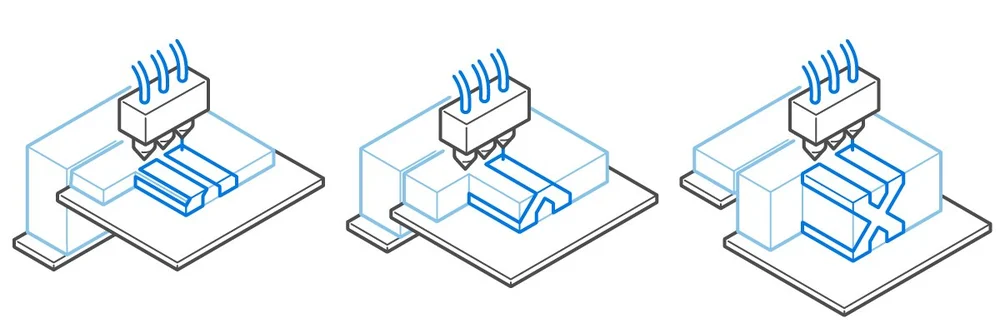
Binder jetting is a 3D printing process where a liquid bonding agent selectively binds regions of a powder bed.
Binder jetting is a similar 3D printing technology to SLS, with the requirement for an initial layer of powder on the build platform. But unlike SLS, which uses a laser or energy to sinter powder, binder jetting does not use heat and moves a print head over the powder surface depositing binder droplets, which are typically 80 microns in diameter. These droplets bind the powder particles together to produce each layer of the object.
Once a layer has been printed, the powder bed is lowered, and a new layer of powder is spread over the recently printed layer. This process is repeated until a complete object is formed.
The object is then left in the powder to cure and gain strength. Afterward, the object is removed from the powder bed, and any unbound powder is removed using compressed air.
- Types of 3D Printing Technology: Binder jetting
- Materials: Sand, polymer, or metal powder: Stainless / Bronze, Full-color sand, Silicia (sand casting); Ceramic-Metal composites
- Dimensional Accuracy: ±0.2 mm (metal) or ±0.3 mm (sand)
- Common Applications: Functional metal parts; Full-color models; Sand casting
- Strengths: Low-cost; Large build volumes; Functional metal parts, Superb color reproduction, Fast print speeds, Support-free design flexibility
- Weaknesses: Mechanical properties not as good as metal powder bed fusion
Sand Binder Jetting
With sand binder jetting devices, these are low-cost types of 3D printing technology for producing parts from sand, e.g., sandstone or gypsum.
After printing, the cores and molds are removed from the build area and cleaned to remove any loose sand. The molds are typically immediately ready for casting. After casting, the mold is broken apart, and the final metal component is removed.
The significant advantage of producing sand casting cores and molds with Binder Jetting is the large, complex geometries the process can produce at relatively low cost. Plus, the process is quite easy to integrate into existing manufacturing or foundry processes without disruption.
Metal Binder Jetting
https://youtu.be/L6Rd9diIkrsBinder Jetting can also be used for the fabrication of metal objects. Metal powder is bound using a polymer binding agent. Producing metal objects using Binder Jetting allows for the production of complex geometries well beyond the capabilities of conventional manufacturing techniques.
Functional metal objects can only be produced via a secondary process like infiltration or sintering, however. The cost and quality of the result generally define which secondary method is the most appropriate for an individual application. Without these additional steps, a part made with metal Binder Jetting will have poor mechanical properties.
The secondary infiltration process works as follows: initially, metal powder particles are bound together using a binding agent to form a “green state” object. Once the objects have fully cured, they are removed from the loose powder and placed in a furnace, where the binder is burnt out. This leaves the object at around 60% density with voids throughout.
Next, bronze is used to infiltrate the voids via capillary action, resulting in an object with around 90% density and greater strength. However, objects made with metal Binder Jetting generally have lower mechanical properties than metal parts made with Powder Bed Fusion.
The sintering secondary process can be applied where metal parts are made without infiltration. After printing is complete, green state objects are cured in an oven. Next, they’re sintered in a furnace to a high density of around 97%. However, non-uniform shrinkage can be an issue during sintering and should be accounted for at the design stage.
Plastic Binder Jetting
The process and technology for plastic binder jetting are very similar to metal binder jetting. It involves plastic powder and a liquid binding agent. (No, you can’t use the same machine for both metal and plastic, but hopefully, someone will come out with that soon.)
Once printed, plastic parts are removed from their powder bed and can often be used without any further processing but can be infilled with another material, cured, polished, or painted. They do not require a furnace sintering step, like with metal.
Binder jetting with polymers, like with metals, has a range of unique advantages over injection molding and other polymer 3D printing technology.
3D PRINTING PROCESS: DIRECT ENERGY DEPOSITION
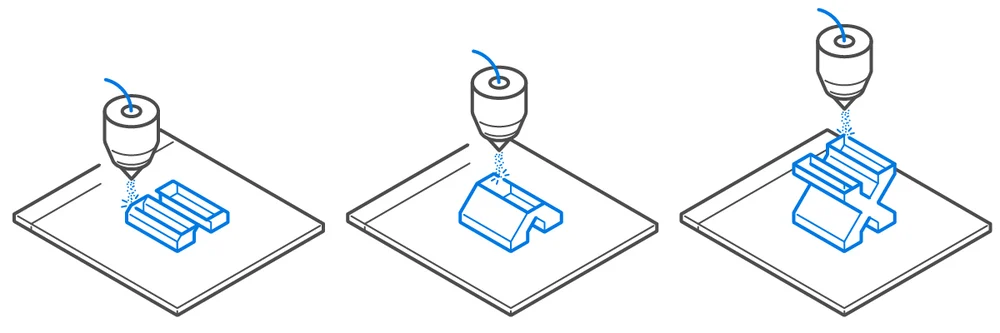
DED is a 3D printing process where material is fed and fused by powerful thermal energy simultaneously to when it is deposited.
The energy source in question is usually one of three – an electron beam, laser, or plasma. Material is fed in either wire or powder forms for the heat source to melt as it leaves its nozzle, forming complex shapes.
This technology can be used to build up a print layer by layer, but it can also be used to repair objects. For this reason, DED is often used more for repair than perhaps it is being used to create entirely new printed items.
When the material being used in this printing method is in powder form, it is common for the powder to be sprayed alongside an inert gas (historically, often referred to as noble gases) in order to reduce or eliminate the possibility of oxidation. With powder feedstock, there’s also the possibility of using multiple powders in order to mix materials and achieve different results.
While the need for a good supply of inert gas could be seen as a negative aspect of DED, perhaps the biggest issue with this method is that not all of the material is used during the process. Inevitably, there will be some powder that goes off-target and is not melted. Another downside to DED is that parts produced in this manner often require a fair amount of post-processing.
- Types of 3D Printing Technology: Laser Engineered Net Shaping (LENS); Electron Beam Additive Manufacturing (EBAM); Cold Spray
- Materials: Metals, in wire and powder form
- Dimensional Accuracy: ±0.1 mm
- Common Applications: Repair of high-end automotive/aerospace components, functional prototypes, and final parts
- Strengths: Support structures rarely required; mixing metals; ability to work in 3 dimensions
- Weaknesses: Poor surface finish requires post-processing; expensive
Electron Beam Additive Manufacturing (EBAM)
With EBAM, we use an electron beam as the energy source and both powder and wire feedstock can be used.
EBAM is often carried out in a vacuum, reducing the possibility of contaminants tainting the final product and disregarding the need for an inert gas atmosphere. Layers are built up one by one, with the electron beam creating a melt pool and simply adding the material where its commands tell it to.
Commonly used metals with this procedure include alloys of copper, titanium, cobalt, and nickel, but pure titanium and tantalum are also used. For the most part, an alloy of titanium is the most frequently used material with this printing method, producing parts such as medical implants – such as you’ll find in hip replacements.
Laser Engineered Net Shaping (LENS)
LENS 3D printing happens inside a hermetically sealed chamber, as a metal powder is fed through one or more nozzles and fused specifically via a powerful laser. An object is then built up layer by layer as the nozzle and laser move around, sometimes in a 3-dimensional manner.
The chamber itself has to be as close to the void of oxygen and moisture as possible to ensure the production of a clean part. For this reason, an inert gas floods the chamber (usually argon) and reduces the amount of oxygen and moisture within it dramatically. Metals commonly used in this process include titanium, stainless steel, aluminum, and copper.
This printing method is often used to repair high-end aerospace and automotive components, such as jet engine blades, but it can also be used to produce entire components. Often, the surface finish of completed parts is not particularly impressive, so a degree of post-production finishing is required in order to deliver a completed component.
Cold Spray
It could fairly be argued that cold spray 3D printing doesn’t under the DED banner. Instead of using an external energy source, such as an electron beam or laser, cold spray works by the velocity of the molecules of metal alone.
Cold spray is a manufacturing technology that sprays metal powders at supersonic speeds to bond them without melting them, which produces almost no thermal stress. Since the early 2000s it’s been used as a coating process, but more recently, several companies have adapted cold spray for additive manufacturing because it can layer metal in exact geometries up to several centimeters at about 50 to 100 times higher speed than typical metal 3D printers.
It might not be surprising to learn that this 3D printing method doesn’t produce prints of great surface quality or detail, but the technology doesn’t need such high-quality powdered metal to function as other methods do, and there’s no need for inert gases or vacuum chambers either.
To finish the prints to a worthwhile standard, often CNC machining is involved, sometimes in connection with the printer, producing a sort of hybrid 3D printer/CNC router.
Other Direct Energy Deposition Technologies
A few other terms have been used to describe DED, with some to differentiate due to marketing purposes and some technically different in execution. However, the below-listed items could all be considered DED.
- Direct Metal Deposition (DMD)
- Wire Arc Additive Manufacturing (WAAM)
- Rapid Plasma Deposition (RPD)
It is also worth mentioning that some hybrid 3D printers exist that combine DED technology with CNC milling, one example being DMG Mori’s Lasertec 65 hybrid.
MICRO 3D PRINTING
Additive manufacturing on the microscale generally refers to the production of parts measured in single-digit microns down to a layer thickness of 5 microns and a resolution of 2 microns. Some technologies are even capable of printing parts measurable in nanometers (nm), which is 1,000 times smaller than a micron. For reference, the average width of a human hair is 75 microns and a strand of human DNA is 2.5 nanometers in diameter.
Most micro 3D printing is accomplished through resin printers, or more specifically, photopolymerization reactions with light. Some companies, however, have begun moving beyond polymers and into the realm of metals, including steel, copper, and gold. Let’s take a look at the five major categories of micro-additive manufacturing technology.
- Types of 3D Printing Technology: Microstereolithography (µSLA), Projection Microstereolithography (PµSL), Two-Photon Polymerization (2PP or TPP), Lithography-based Metal Manufacturing (LMM)
- Materials: Polymer, metal, ceramic
- Dimensional Accuracy: ± 30 µm
- Common Applications: Microneedle patches, medical implants, circuits
- Strengths: strong yet tiny parts, more cost effective than traditional micro-manufacturing
- Weaknesses: High cost printers and materials
Microstereolithography (µSLA)
This process is in the vat polymerization family. It involves exposing photosensitive material (liquid resin) to an ultraviolet laser. The general process is the same as for most commercial resin printers: pour resin into a tank, lower a build platform into the resin, a laser draws a cross-section of the 3D part, layer by layer, while the platform is lowered into the chamber. The difference is the sophistication of the lasers and the addition of lenses, which are capable of generating almost unbelievably small points of light, and specialized resins.
Projection Microstereolithography (PµSL)
This additive manufacturing technique is growing due to its low cost, accuracy, speed, and also the range of materials that it can use, which include polymers, biomaterials, and ceramics. It has shown potential in applications ranging from microfluidics and tissue engineering to micro-optics and biomedical microdevices.
The PµSL process is similar to µSLA, except that instead of a laser, PµSL uses ultraviolet light from a projector. The technique allows for rapid photopolymerization of an entire layer of liquid polymer using a flash of UV light at micro-scale resolution, so it’s significantly faster. It’s quite similar to digital light processing (DLP) resin 3D printing technology you’ll see in 3D printers from companies, such as Carbon.
Two-Photon Polymerization (2PP or TPP)
This technology has shown to provide the highest accuracy among micro 3D printers. It is being used for promising medical innovations including tissue engineering and medical implants, as well as industrial applications, including micromechanics. But the technology and materials are still very expensive and the printers can be slower than other technologies.
In this method, a pulsed femtosecond laser is used to trace 3D patterns in the depth of the vat of special photosensitive resin. We won’t go into the weeds of the science here, which involves absorbed and generated photons, but know that the technology enables resolutions of less than 1µm, which is considered a nanofabrication technology.
Lithography-based Metal Manufacturing (LMM)
This metal 3D printing method creates tiny metal parts for applications including surgical tools and micromechanical parts, using some of the same principles of photopolymerization. In LMM metal powder is homogeneously dispersed in a light-sensitive resin and then selectively polymerized by exposure with blue light. After printing, the “green” parts have their polymer component removed leaving fully metal “brown” parts that are finished in a sintering process in a furnace. Feed stocks include stainless steel, titanium, tungsten, brass, copper, silver, and gold.
At the cutting edge of micro metal 3D printing technology is the Swiss company Exaddon, which developed a metal micro 3D printing process that does not require any post-processing. In this process, a printing nozzle delivers a liquid containing metal ions through a microchannel onto a print surface. These ions dissolve into solid metal atoms which grow into larger building blocks (voxels) until the object is complete.
3D PRINTING PROCESS: SHEET LAMINATION
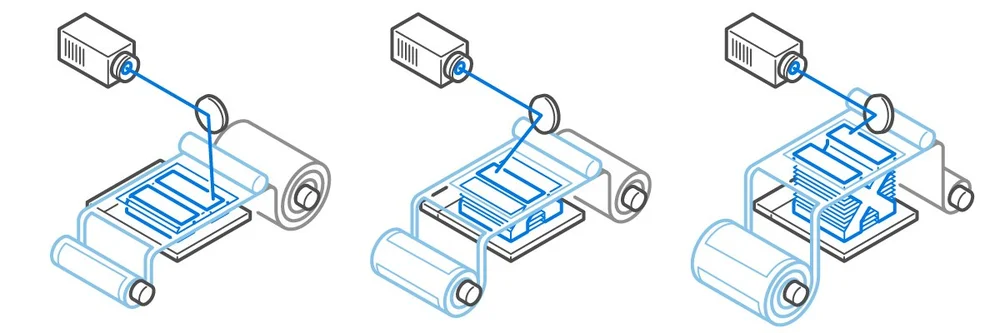
Sheet lamination is a form of 3D printing that functions by stacking and laminating sheets of very thin material together in order to produce a 3D object. The material layers can be fused together using a variety of methods, with heat and sound commonly used to do so. Which method is most appropriate depends on the material in question, with paper, polymers, and metals all used in sheet lamination.
The technology is one of the less accurate 3D printing technologies, with parts produced using this method requiring a lot of post-production finishing. Laser cutters and CNC routers are used as the print progresses to form the print into the desired shape, which can lead to more wastage than in other 3D printing technologies.
Manufacturers use sheet lamination to produce cost-effective, non-functional prototypes at a relatively high speed. The technology is also used to produce composite items, as the materials used can be swapped around during the printing process. It should be noted that many objects produced this way are not strong enough to serve as functional components and serve better as aesthetic pieces.
- Types of 3D Printing Technology: Laminated Object Manufacturing (LOM), Ultrasonic Consolidation (UC)
- Materials: Paper, polymer, and metal in sheet forms
- Dimensional Accuracy: ±0.1 mm
- Common Applications: Non-functional prototypes, multi-color prints, casting molds.
- Strengths: Low-cost; quick production possible; composite prints
- Weaknesses: Low accuracy; more waste; plenty of post-production work required for parts
Laminated Object Manufacturing (LOM)
LOM is the most common form of Sheet Lamination 3D printing. Sheets of material are layered on top of each other and bonded together using glue. Like many other forms of 3D printing, layers are built up one at a time, but a sheet cannot form a complex shape alone, and in LOM, a knife (or laser, or CNC router) is used to cut the layered object into the correct shape.
The amount of glue applied during this printing process can be varied, with more sticky stuff being applied to areas that will eventually form part of the final print and less being applied to areas that will be removed by the cutter. The cutter works as the print proceeds, cutting a 2D cross-section of the eventual final print.
This printing method has some notable advantages, with prints being quick and affordable to produce and larger objects capable of being produced using this method. There are some downsides too, of course.
More often than not, prints produced using this technology are pretty strong and retain good properties over time, but they require more post-production finishing (and can be altered with drilling or machining) and produce more excess waste than other 3D printing methods.
Ultrasonic Consolidation (UC)
Ultrasonic Consolidation (UC) is a way to 3D print metal objects that falls under the Sheet Lamination umbrella. You’ll sometimes see it referred to as Ultrasonic Additive Manufacturing (UAM).
This 3D printing method uses ultrasonic vibrations and pressure via a sonotrode to fuse thin sheets of metal together at a low temperature. Because of that low temperature, the metal sheets are not melted together but rather bonded together due to the breakdown of oxides on the surface of the metals.
This method does produce heat, but it is far lower than what you would need to join metals together only via temperature, and an advantage of this method is that different types of metal can be bonded together, producing multi-metal parts without the metals intermixing.
Like with other Sheet Lamination printing methods, a cutter is required to cut the 2D cross-section of the 3D printed shape, and with metal parts like this, a CNC router is the most commonly used method. Due to the cutting process, you do get more waste with this method than other metal 3D printing, and the cutter can also be used to produce details and designs as the print is being formed. Post-production finishing is often required, but the high speed of the process and the low temperatures at which metal sheets are bonded give Ultrasonic Consolidation more advantages than disadvantages.
Other Sheet Lamination Technologies
As with the vast majority of the other print processes on this list, there are a few other types of Sheet Lamination technology out there on the market that generally fall under the same umbrella. Here we’ve listed them for the curious among you to explore as further reading.
Source: https://all3dp.com/1/types-of-3d-printers-3d-printing-technology/