Electron beam melting is a 3D printing technology that uses an electron beam to fuse metal powder together to build parts. We’ll explain how this technology works, point out its pros and cons, and showcase where it’s utilized.
What Is Electron Beam Melting?
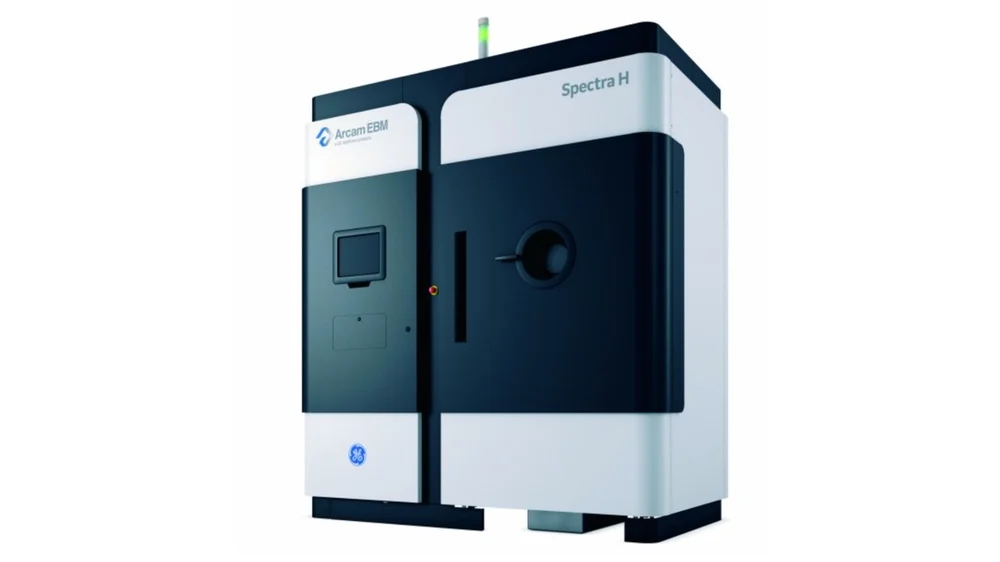
Electron beam melting (EBM) is a 3D printing technology that, at first glance, appears very similar to SLS 3D printing. However, closer inspection reveals that EBM differs in several ways. The most significant differences are that the energy source comes from an electron beam instead of a CO2 laser and that the material used is conductive metal instead of thermoplastic polymer.
In particular, EBM often uses titanium alloys and isn’t capable of printing plastic or ceramic parts. That’s due to the fact that the technology is based on electrical charges. They are what produce the reaction between powder and electron beam, causing the former to solidify.
In the following, we’ll take a closer look at EBM, including how it works, its pros and cons, as well as some ideal application areas.
The Printing Process
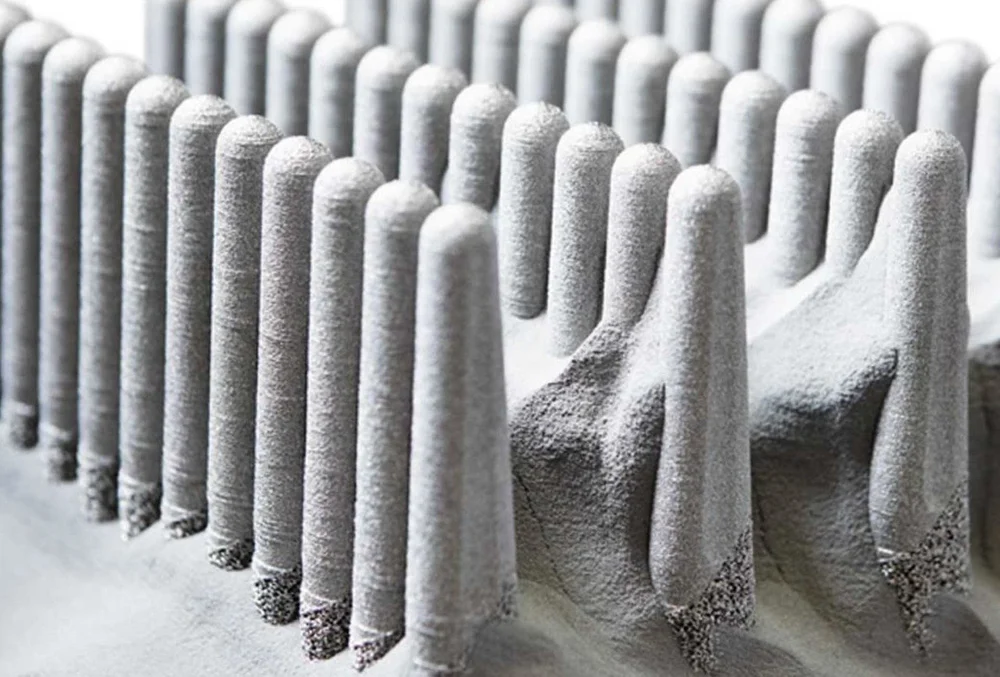
All EBM 3D printers consist of an energy source capable of emitting the electron beam, a powder container, a powder feeder, a powder re-coater, and a heated build platform. Important to note is that the printing process must take place in a vacuum. That’s because electrons of the electron beam would otherwise collide with gas molecules, which would “kill” the electron beam.
Pre-Printing
Before the printing process can begin, the powder bin is filled with the desired metal powder. Once that’s done, the powder bin is placed into the 3D printer, and the internal pressure is set to around 0.0001 mBar. Believe it or not, that’s around 10 million times less than atmospheric pressure!
When the desired pressure is achieved in the build chamber, the electron beam is “fired up”, heating the build platform to high temperatures. For example, titanium requires 600–700°C. After the build platform is heated, the printing process can finally start.
The Main Event
The 3D printing itself starts with the powder re-coater, which deposits a single layer of preheated powder onto the build platform. Once the powder is set, it’s time for the electron beam melting to begin. The electron beam is controlled by a set of electromagnetic coils, which accurately point the beam towards the desired points of the build platform. The electron beam moves selectively while melting the powder and causing the powder particles to fuse together.
After one layer is complete, the build platform is moved down one layer in height. The re-coater comes in again with a fresh layer of powder, and the electron beam starts to induce fusion of powder particles, causing the new layer to form. This process is repeated until the entire part is finished.
Post-Processing
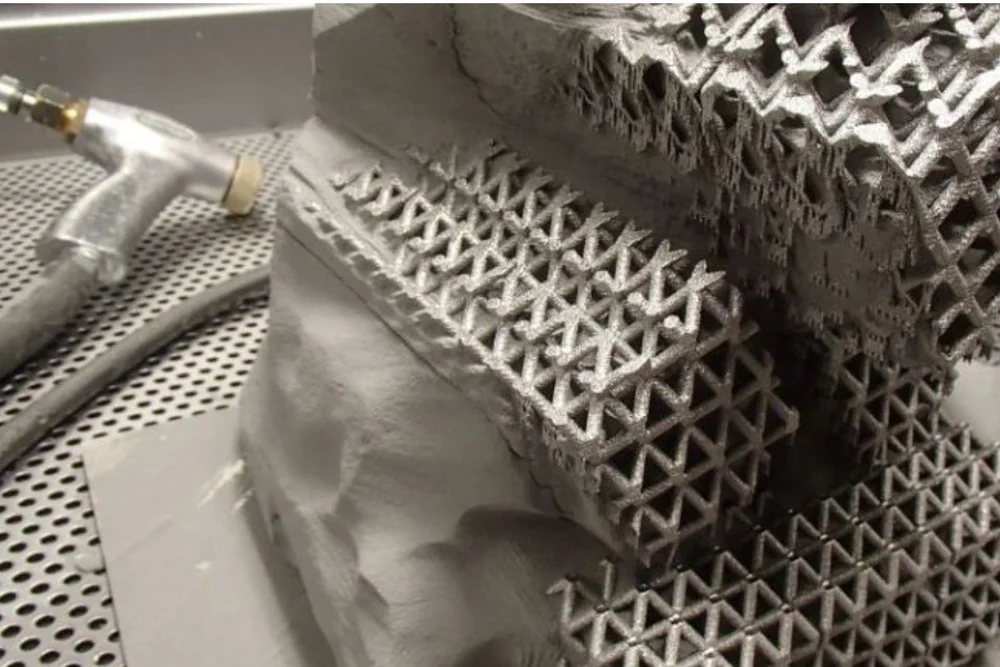
When finished, parts aren’t immediately visible since they’re inside the powder bin covered with semi-sintered powder, which must be removed.
Distortion
The EBM 3D printing process involves high temperatures, which can be a problem for parts. If they are too hot for too long a time, they can distort. This is the main reason EBM requires supports, whose main function is to provide paths for excess heat to “go away” and not to provide mechanical stability. Like SLS, the latter is provided by the semi-sintered powder that surrounds parts.
Interestingly, while high part temperatures are undesirable, high surrounding temperatures have a “stress relief” effect on the parts, helping to reduce the amount of distortion. This is a unique benefit only present with electron powder bed fusion systems.
Final Steps
When parts are finally finished, the powder bin is taken out of the 3D printer. Despite the parts already being manufactured, you still can’t use them yet. For starters, they have to be left to cool.
Despite the supports being made from the same metal material as the part itself, they’re actually rather easy to simply break away. Afterward, EBM parts can be polished, coated, or machined using traditional techniques.
Pros & Cons
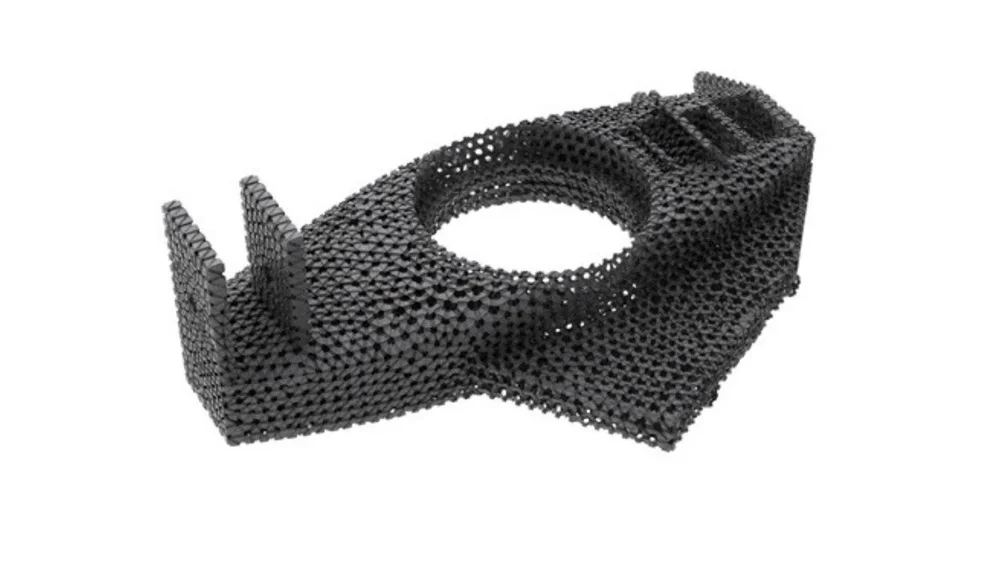
Just as with any other 3D printing technology, EBM also has its pros and cons.
Pros
- High density (and therefore strength) due to a full melt of the powder
- Faster printing process
- Non-sintered powder can be recycled
- Fewer supports required compared to laser powder bed fusion
Cons
- Small print volume (max. 350-mm diameter and 380-mm height)
- Limited material selection (only titanium or chromium-cobalt alloys)
- Expensive machines and materials
Industry & Applications
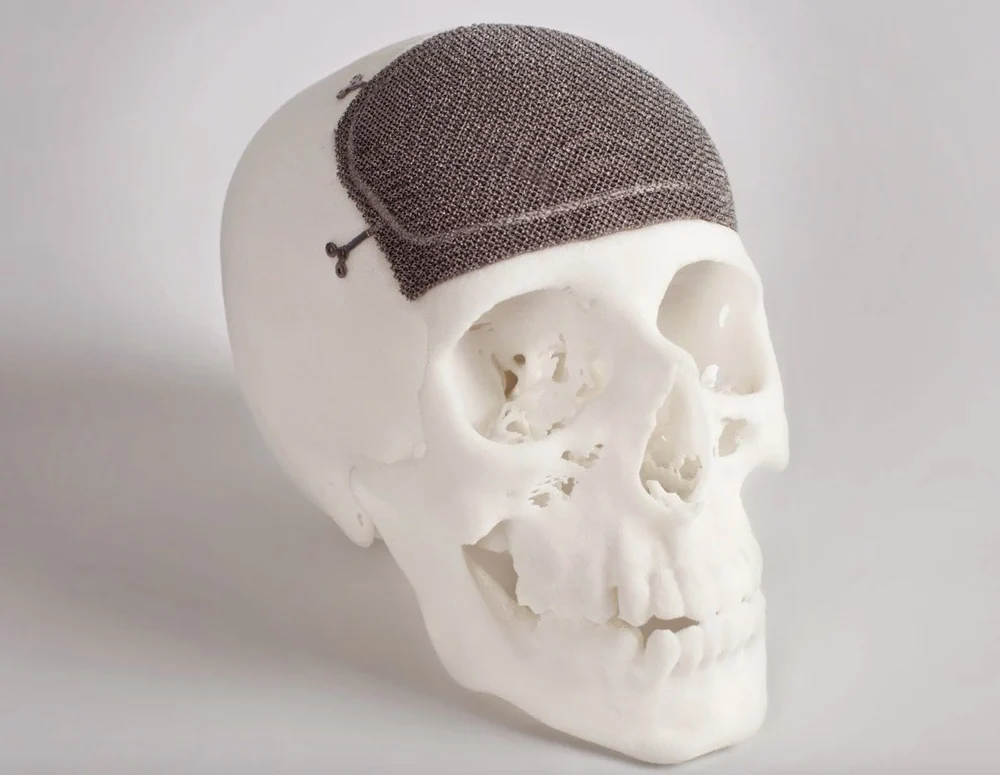
An interesting fact about EBM 3D printing is that there are only a few companies making the 3D printers. One of the best known is Arcam EBM, a GE Additive company which, naturally, is a leader when EBM is concerned. Apart from Arcam, there’s also Japan-based JEOL, Freemelt, as well as Chinese manufacturers, like Sailong Metal.
The prices for EBM 3D printers are high. We don’t know the exact pricing, as it’s not publicly available. Instead, we recommend contacting the respected manufacturers directly.
Since EBM 3D printers and powders are expensive, it’s no wonder this technology isn’t yet utilized for mass production. Instead, it’s used for manufacturing a small series of parts which usually feature a complex structure.
As you’d expect for a technology used for manufacturing high strength metal parts, it’s used in a number of fields. EBM has already seen its use in medicine, aeronautics, and motorsports, to name a few.
One of the EBM applications worth pointing out was born in the medical industry. With EBM, it was possible to produce a fully functional, custom-made skull implant. As EBM parts are strong by default, this piece is for sure just as strong as the skull, or even stronger.
Feature image source: Additive Manufacturing, LLC
Source: https://all3dp.com/2/electron-beam-melting-ebm-3d-printing-simply-explained/