What is PLA material? Learn all you need to know about PLA plastic: basics, advantages, properties, uses, types, sustainability, and more.
What Is PLA?
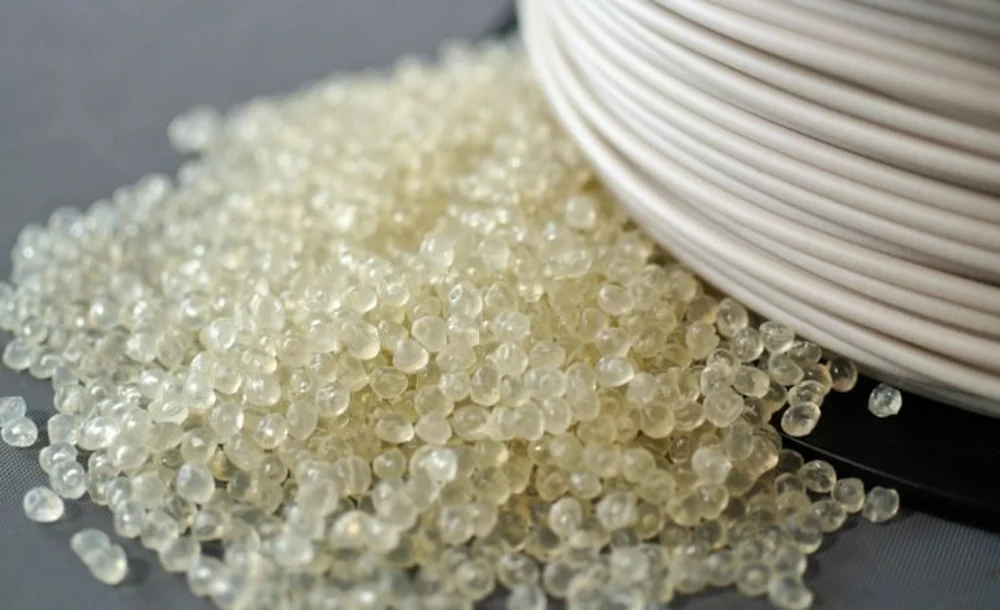
Even if you’re new to the world of 3D printing, you’ve probably heard of PLA filament, the most popular 3D printing material out there. Polylactic acid, commonly referred to as PLA, is a bioplastic and thermoplastic made from natural materials like corn starch. It’s most known for its use in the 3D printing industry, sold in spools of a stranded material known as filament, but PLA plastic is also used in other manufacturing contexts due to its unique properties.
PLA is comparatively easy to work with, usually requiring minimal effort to produce quality parts, especially on an FDM 3D printer. As it’s created from natural or recycled materials, PLA is also embraced for its eco-friendliness, biodegradability, and many other characteristics.
In this article, we’ll go over everything about PLA plastic, especially with reference to its use in 3D printing. We’ll look at how this plastic is made, its pros and cons, uses, manufacturing methods, properties, sustainability issues, and more.
How Is PLA Made?
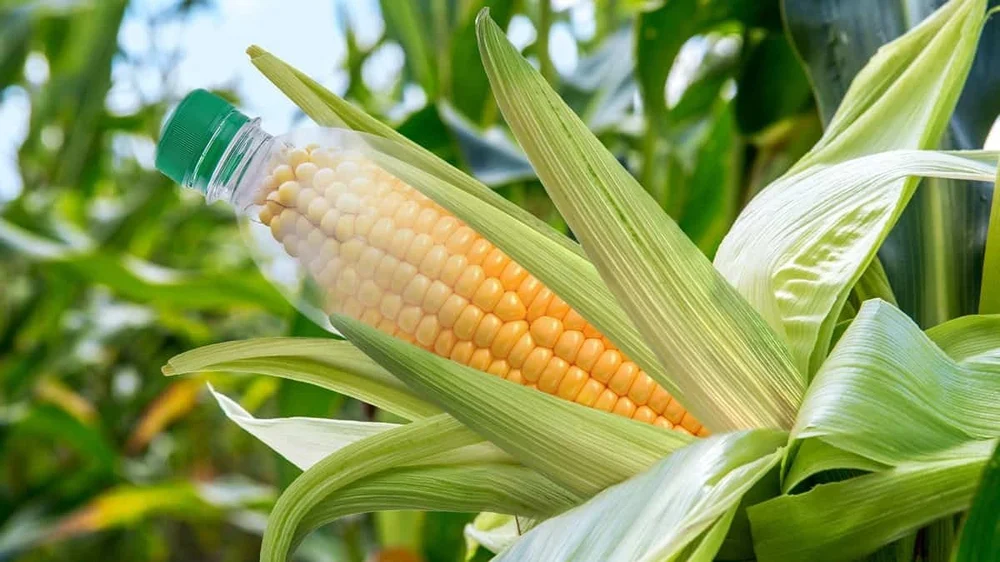
While this process may not happen right in front of you, it’s still good to know how a filament or material is made. Unlike many plastics made through refining crude oil, PLA is made from plant-derived substances like corn starch and sugarcane.
Raw Material
First, the raw natural material, such as corn, undergoes wet milling, where the plant’s starch is isolated and separated. Following this extraction, the starch is mixed and heated with enzymes and other chemicals to release dextrose (D-glucose), a type of sugar. Then, the dextrose is fermented, producing lactic acid monomers, which polylactic acid is primarily made of (as you might be able to guess from the name).
The lactic acid can then be processed into PLA material in two ways: by condensing the lactic acid into a lactide and then using a polymerization process or by using a condensation process with the lactic acid directly. The former method is more common and involves binding the molecules together by adding different catalysts and heat.
Filament
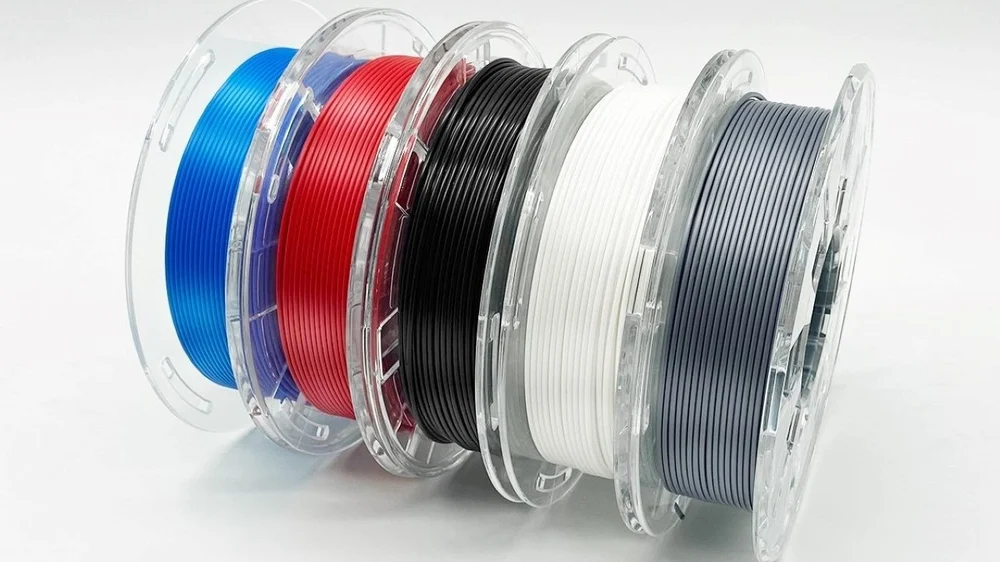
Once the PLA is processed, the plastic is granulated and sold as a raw material. In the production of PLA filament, filament manufacturers first mix these PLA pellets with other substances. These additives typically give the final product enhanced properties such as a different color, heat resistance, or strength.
The new mixture is then loaded into a special filament extruder that melts the grains and then cools them in a stringed form at a precise diameter (usually 1.75 or 2.85 mm). Finally, the stringed plastic is wrapped around a spool, packaged, and shipped around the world.
When PLA is used in contexts other than filament manufacturing, the process is very similar, except that the precise form varies depending on the intended end product.
Pros & Cons
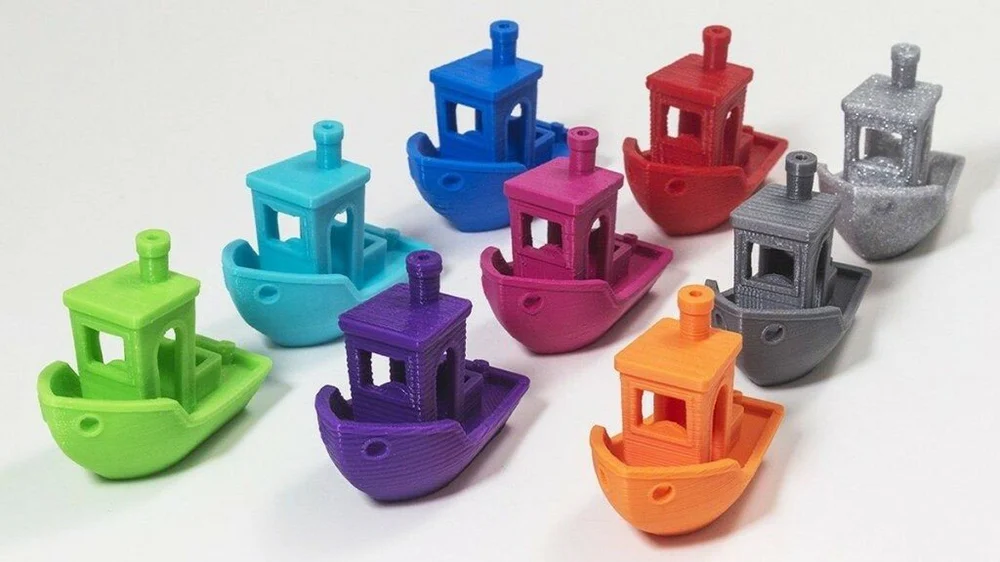
PLA as a 3D printing material has some obvious advantages, but it’s important to recognize that this material isn’t perfect and has some drawbacks. Below, we’ve listed some of the benefits and disadvantages of this material.
Pros
- Easy to print: PLA is super easy to print with; almost all 3D printers can print this material, and it doesn’t need a heated bed. PLA requires relatively low temperatures compared to other printing materials, can be printed somewhat fast (around 60 mm/s), and doesn’t require an enclosure.
- Inexpensive: PLA is pretty cheap to buy compared to other, more specialized printing materials such as nylon or polycarbonate (PC), making it a great option for makers on a budget.
- Wide range of color and options: PLA comes in many different forms, and manufacturers have made this filament in almost any color you can think of. Additionally, there are composite and special-purpose PLA filaments like carbon-fiber-infused PLA, glittery PLA, and even scented PLA.
- Biodegradeable and eco-friendly: As PLA is sourced from plants, it makes sense that it’s biodegradable, unlike other plastics (e.g. ABS) that are made from refining crude oil, which harms the environment.
- Non-toxic: PLA is non-toxic when it can be kept uncontaminated, expanding its applications to areas like the medical and food industries.
- No fumes: Fumes are unavoidably released when thermoplastics are melted, and these fumes, especially from toxic materials like ABS, can contain harmful inhalants and even carcinogens. While PLA can release some fumes, there is almost no odor and far less risk.
Cons
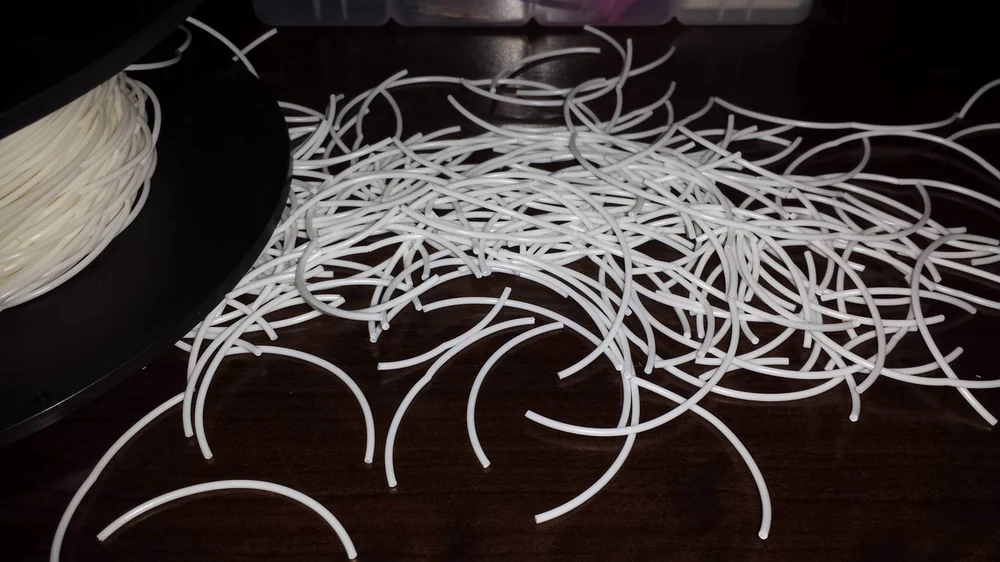
- Brittle and relatively weak: The most obvious disadvantage of PLA is its low flexural strength. 3D printed PLA parts are significantly weaker than injection-molded parts and even parts 3D printed in other materials like PETG and ABS. PLA parts also don’t usually bend; they snap very quickly after enough force is applied, meaning the material is very brittle.
- Low temperature and chemical resistances: On top of not being the strongest material out there, PLA isn’t very heat resistant, either. PLA has a low glass transition temperature, so parts printed in this material tend to deform under hot conditions, making PLA a less-ideal material for outdoor use. Additionally, certain chemicals cause PLA to release its raw chemicals, namely lactic acid, which can be harmful in high quantities.
- Slow decomposition: Even though PLA is biodegradable, as you might expect from plastic, it still takes a long time to decompose. Under ideal composition conditions, PLA plastic takes three months to decompose, which is a long time compared to other decomposable materials.
Where It’s Used
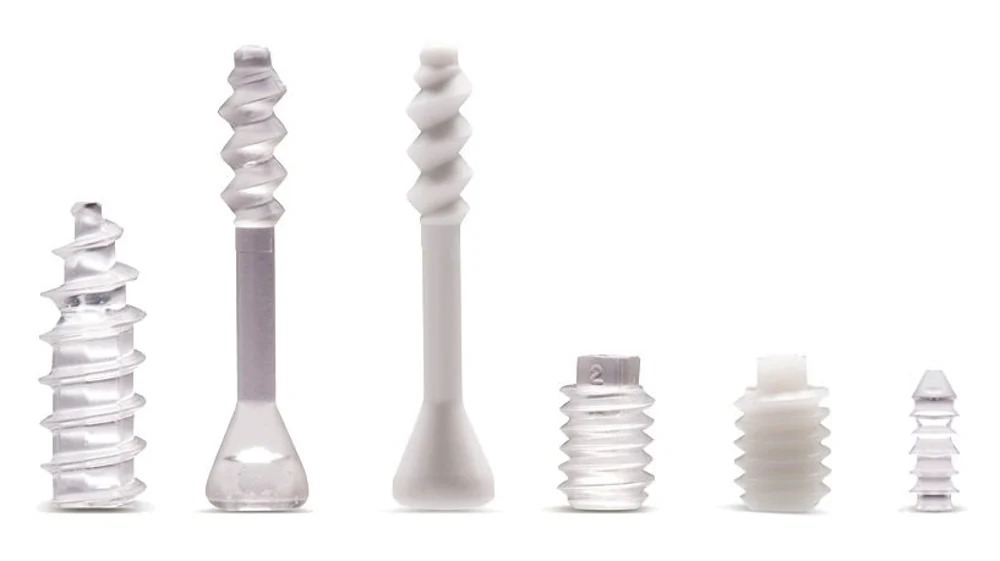
PLA is the most popular 3D printing material, but it has plenty of uses besides 3D printing:
- Food-packing: PLA is an all-natural, non-toxic, and theoretically food-safe material, making it a great plastic for food packing because it won’t contaminate food. Even though PLA can react with certain chemicals and liquids, results have shown that it releases an insignificant amount of lactic acid. For example, NatureWorks, a bioplastic company, has successfully used PLA to make a food-safe food-packing component.
- Medical: Again, PLA’s non-toxic composition makes it useful in the medical and healthcare industry. PLA components have been used in bone fixation devices, like binding screws and plates.
- Prototyping: Prototyping in PLA is typically done with 3D printing, and it’s a great way for businesses and individuals to bring an idea to life. That’s because PLA is super easy to print, inexpensive, and can be used with any FDM 3D printer.
- Structural applications: Despite its brittleness and low durability, PLA is commonly used in buildings, from carpet fibers to insulation foam. PLA can also be used for furnishing items that won’t be under physical stress.
- Textiles: PLA is also used in the production of cloth and other textiles due to its breathability, low weight, and other properties. PLA certainly isn’t the most popular plastic in the textile industry, but it has potential, and it’s an eco-friendly alternative. An example of this use can be found in the Fibfab project, which has successfully tested PLA for use in casual and protective clothing.
- Cosmetics: The cosmetics industry is a huge contributor to plastic waste, and PLA is gaining popularity as a packaging alternative for its eco-friendliness and all-natural sources.
Now that you know the industries where PLA is most used, below are a few ways that PLA components are produced:
- 3D printing: FDM 3D printing is a very common way to produce parts in PLA: The material is very easy to print, and it doesn’t need high temperatures, a heated bed, or a direct drive extruder.
- Injection molding: Injection molding is the most popular method of manufacturing plastic parts, and it’s how most day-to-day plastic parts are made. While injection molding is typically used with ABS plastic to make parts like Lego bricks or internal car parts (like dashboards), this method can also work with PLA. However, PLA isn’t as commonly used for injection molding due to its low crystallization rate.
- Casting and more: Casting is very similar to injection molding but uses gravity instead of applied pressure to form a part. There are also other similar manufacturing methods for PLA, like thermoforming. Like injection molding, these methods aren’t super popular for producing PLA parts, but are used in some industries.
Material Properties
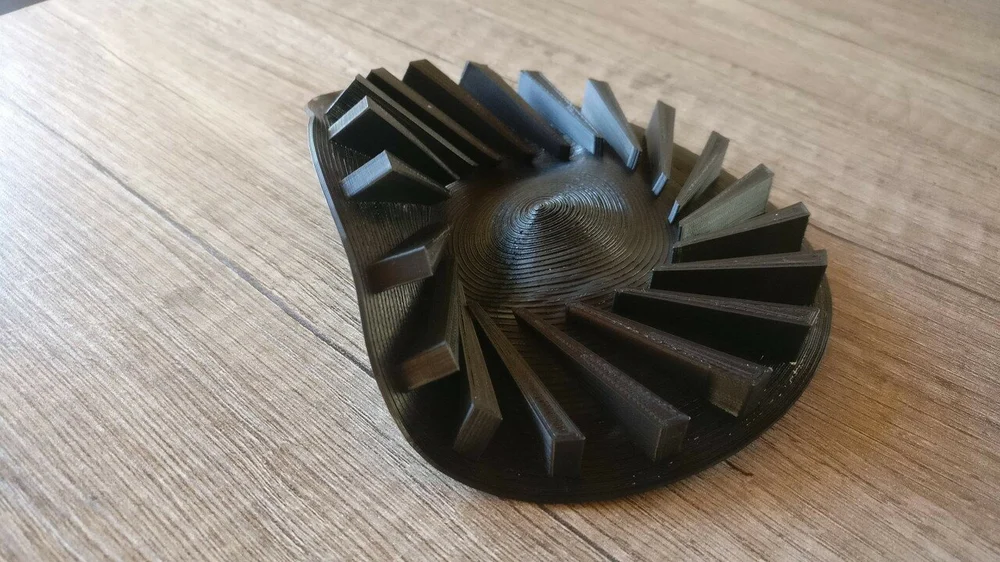
Although we’ve already mentioned a few, such as brittleness, PLA plastic has many properties worth discussing:
- Strength: PLA isn’t a plastic known for its strength (that would be nylon or PC), but a PLA part’s strength is more dependant on how it was made than the material itself. For example, using a higher infill density and layer height would yield a stronger 3D printed part.
- Flexibility: PLA is a stiff plastic, meaning it has a low flexural strength compared to other plastics, especially flexible ones like TPU. Additionally, as we’ve mentioned, PLA is brittle. Instead of bending, it usually snaps and breaks.
- Temperature resistance: PLA doesn’t require a heated bed to be printed, which means it can be used on budget machines. This is due to PLA’s low glass transition temperature, meaning that it deforms quickly under heat. This means you probably shouldn’t be using PLA parts outdoors or keeping them in direct sunlight, as they will easily become disfigured.
- UV resistance: Unlike ABS, which has great UV resistance, PLA doesn’t handle the sun’s rays very well. Similar to when confronted with heat, PLA parts can deform when exposed to UV light for extended amounts of time.
- Chemical resistance: PLA isn’t soluble in solvents like acetone or isopropyl alcohol and, overall, PLA plastic is a very chemically resistant and chemically stable material. However, you can still use more powerful solvents such as dichloromethane and mixtures like XTC3D to dissolve or layer-smooth PLA parts.
Printing Performance
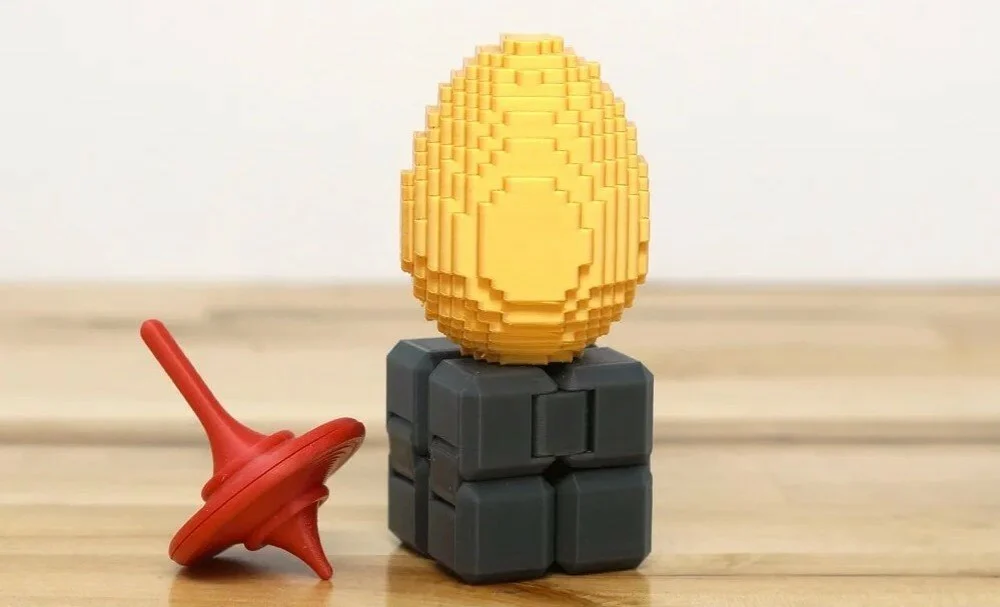
PLA is a material primarily meant for 3D printing, unlike other plastics such as ABS or polycarbonate that are predominantly used in other ways. Overall, PLA has a great printing performance, due to a few factors.
First, PLA doesn’t require a heated bed, enclosure, or direct drive extruder, so the equipment needed to print this material isn’t expensive, sometimes costing under $100. Materials like ABS, PETG, and TPU all require at least one of these things to create quality prints.
Second, PLA is widely accessible, and the consumer 3D printing industry has grown enough that PLA filament is readily available online. It’s also pretty cheap, starting from around $20 per kilogram. Other filaments, like PETG, costs a few extra dollars per kilogram, and there are fewer options.
Third, PLA is quite tolerant of varying print settings (within reason), so achieving a good print is pretty easy without a lengthy testing process to perfect slicer settings. Most default slicer profiles will leave you with a satisfactory model right off the bat, and just a little bit of adjustment can improve your prints even more. In contrast, ABS, PETG, and TPU are all sensitive to slicer settings, so your slicer profiles for these materials need to be delicately tuned to produce good prints.
Last, PLA can be printed more quickly than most other materials, and due to the desire for rapid prototyping, PLA is popular for quickly developing prototypes. No one wants to wait around for days until their first prototype is produced because, by then, they may have moved on to the next prototype!
Types of PLA
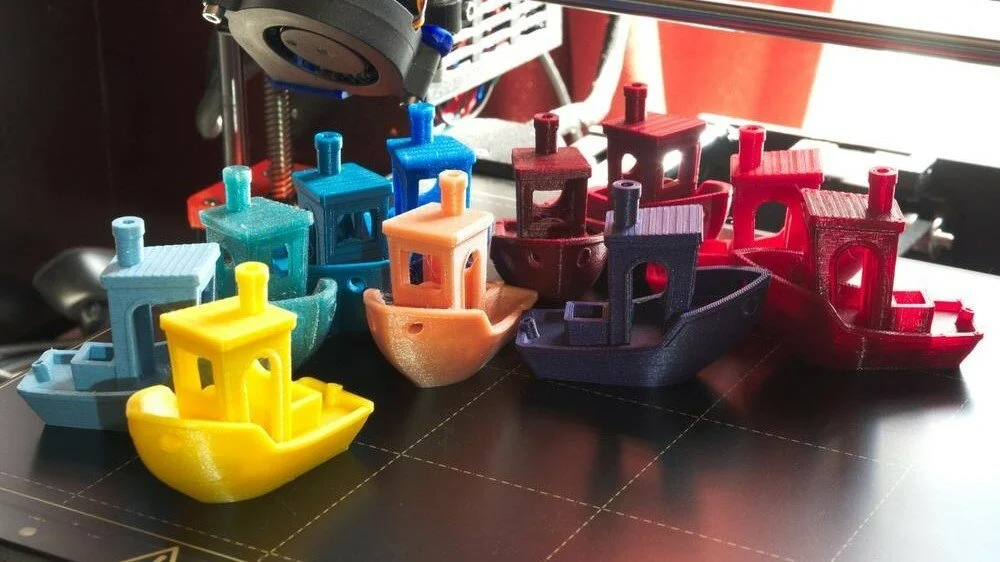
Over the years, many unique types of PLA filament have emerged, giving the consumer many choices:
- Standard: First and foremost, standard PLA is the regular type of PLA prevalent in the 3D printing industry, with no unique or special features besides the basic properties of the PLA material.
- Plus: Plus and Pro are common terms in the filament business to describe a material that has been mixed with special additives to enhance its performance, usually concerning its strength. Pro PLA and PLA+ are great options if you want to print functional, real-world-use parts that will be subject to physical stresses but in a material that’s still easy to print.
- Wood: Wood PLA is a composite type of PLA that contains additives that provide wood-like visual properties, and this filament is useful for making want-to-be wood parts, like plaques.
- Silk: Silk PLA yields a super shiny, smooth, and silky finish to parts, making it a popular option for printing aesthetic pieces like vases.
- Marble: Marble filament is another popular option, and real marble filaments contain small particles of marble to yield a marble-like, speckled finish. Other speckled filaments are also sometimes classified as marble PLA, even if they don’t contain real bits of marble.
- Glittery: Glittery or sparkly PLA is a fun one! This type of PLA has large glitter particles that are very visible, so you can watch a printed part shine under light.
- Carbon-fiber-infused: This type of PLA is another composite and, as the name suggests, is a PLA filament infused with carbon-fiber particles to increase the PLA’s strength and durability while maintaining most of its ease-of-use properties.
- Glow-in-the-dark: Glow-in-the-dark PLA is very popular and will shine in the dark due to special additives in the filament.
- Conductive: Conductive PLA is a type of filament that yields electrically conductive parts that you can use for low-magnitude electrical projects, like powering an LED using a 3D printed circuit.
Popular Products
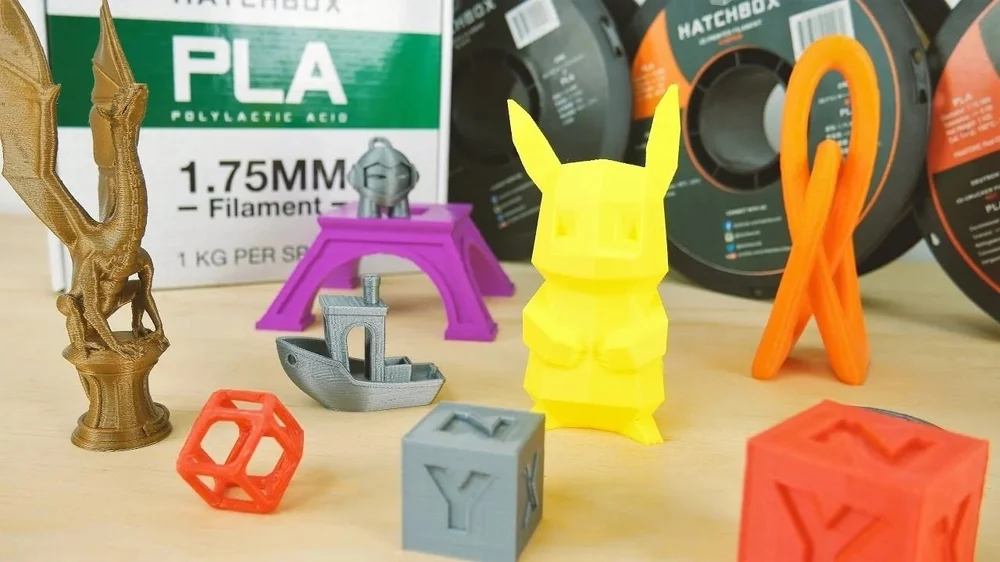
Now that you know the pros, cons, and types of PLA, you may want a spool or two of PLA filament. While many companies make claims about the quality of the filament, a few are known for their reputation and consistent quality from spool to spool. Below is a list of some quality brands of PLA filament:
- Hatchbox: Hatchbox is a small 3D printing filament manufacturer that sells quality filaments in basic colors at an affordable price (around $20 per kg), including a well-reviewed PLA.
- Prusament: Prusament is Prusa Research‘s filament sector, and they make an assortment of materials, including PLA, which they offer in basic and shiny colors.
- Protopasta: While their filament might cost a good deal more than most brands, Protopasta offers some of the most unique PLA filaments out there. From glittery and sparkly to coffee-scented and carbon-fiber-infused, Protopasta has got you covered.
- Polymaker: Polymaker sells a few different types of PLA in basic colors. These include PolyLite, their standard option, PolyMax, an impact-resistant filament, PolyTerra, their eco-friendly choice, and composites like PolyWood.
- MatterHackers: MatterHackers is a popular online retailer of 3D printing supplies for a variety of brands, and they also make their own set of filaments, including their Build Series PLA and their Pro Series PLA. MatterHackers also offers other types of PLA like silky options and glow-in-the-dark PLA.
- Fillamentum: Fillamentum is another higher-end filament manufacturer, and their PLA filaments are some of the best out there, known for their unique colors (e.g. crystal clear) and great printing performance.
Sustainability
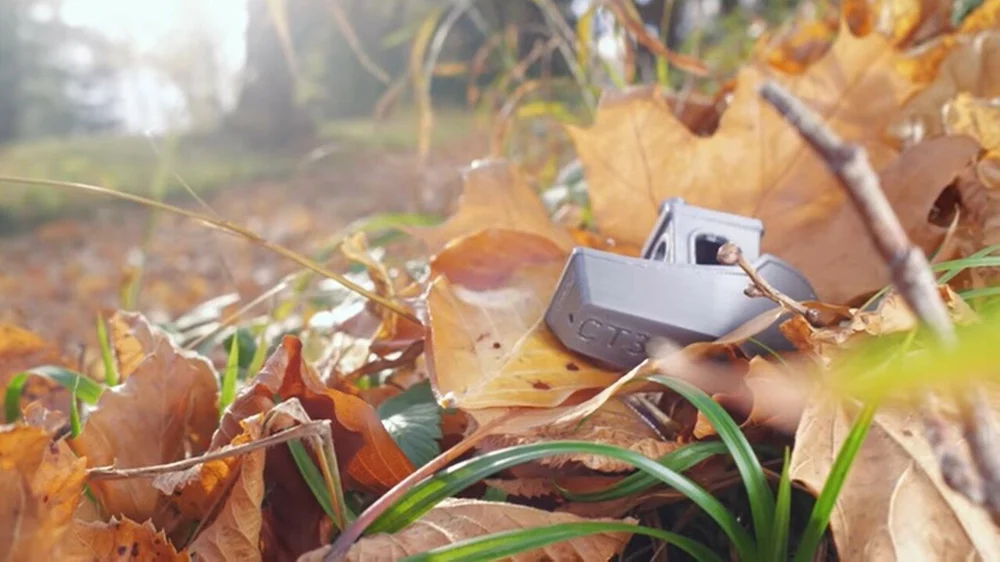
As we’ve mentioned, PLA plastic is sourced from plants like corn instead of harmful materials like crude oil, which most other plastics are made from. This means PLA is a sustainable material for the most part, as plants are relatively renewable.
PLA is also technically biodegradable, but it takes a long time, even in an ideal environment, for PLA plastic parts to degrade. One study found that in a controlled composting environment, with heat and decomposing organisms to expedite the process, PLA plastic took three months to break down.
It would take even longer than three months for PLA to decompose in natural, uncontrolled conditions. So, it’s not like you can just toss all your old 3DBenchys in the composter or on the ground. Instead, it’s best to send PLA parts to a special facility meant for composting bioplastics.
The plants required to produce PLA are important as a food source, and some could argue that it’s not in the planet’s best interest to use these limited crops to make plastic over food. Perhaps in the future, PLA might be seen as an unsustainable material, if crop yields aren’t high enough to satisfy the need for both plastic and food.
Overall, while PLA is technically a sustainable material, it has some limitations. Still, PLA is a bioplastic and is more sustainable than other plastics, like ABS, which rely totally on non-renewable resources and don’t decompose (or not nearly as quickly).
Toxicity & Food Safety
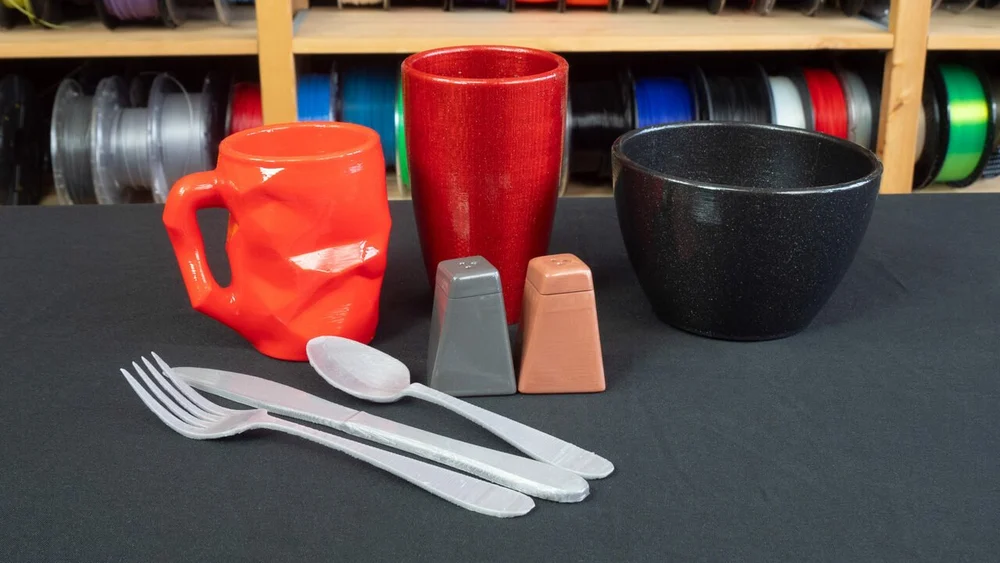
Lastly, it’s important to discuss the toxicity and food safety of PLA plastic, as this a key consideration of using any material. PLA is a non-toxic material and can theoretically be used for producing food-safe items, unlike other 3D printing plastics such as ABS. However, many other factors contribute to the food safety of PLA, especially if it’s a 3D printed part.
Just because a material is non-toxic, doesn’t mean it’s safe to come in contact with food. For example, FDM 3D printing creates parts layer-by-layer, and there are pretty obvious gaps between these layers. These gaps can trap foreign particles, potentially contaminating the part and making it no longer food safe. Before this can even happen, though, PLA filament is fed through an extruder, tube, hot end, and nozzle, all locations where other, potentially unsafe materials come into contact with the PLA.
With this in mind, it’s important to remember that while pure PLA plastic is non-toxic and food-safe, other materials and particles can affect the safety of the finished part. We recommend consulting our guide to printing food-safe parts before attempting to print anything that will come into contact with food.