3D printing and injection molding may be vastly different processes, but both hold valuable places in manufacturing. Learn more in this handy guide!
The Basics
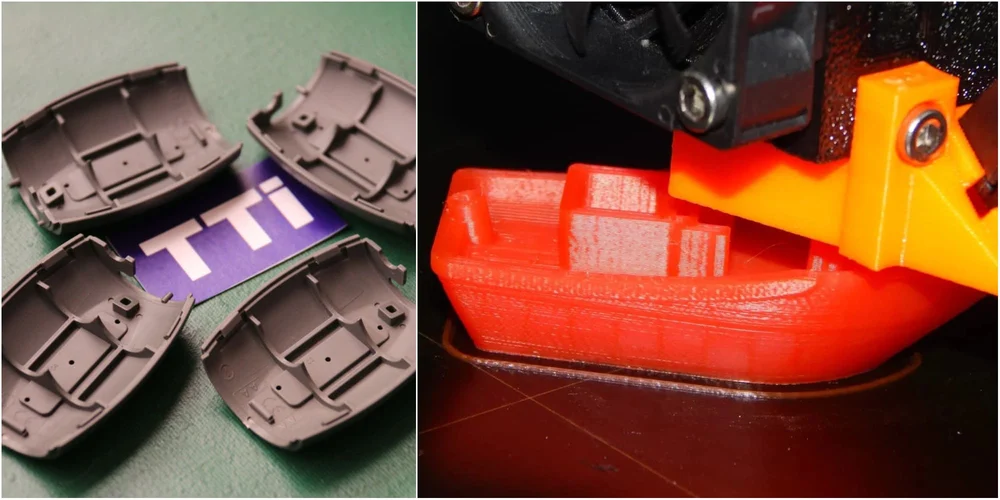
3D printing and injection molding have a lot in common. Both are manufacturing processes meant to make a designer’s vision a reality as painlessly as possible, and both are great at producing prototypes or replacement parts, among many things. But although they get you the same result, they are vastly different processes.
First of all, 3D printing is an additive process. It manufactures objects by building them up layer by layer. You can watch this build process as it happens, which is useful when you’re testing a new design.
Injection molding makes use of molds (as you may have guessed from the name). First, an object’s inverse is carved out of a material that is safe to handle the molten build material (the material the finished object is made of). Then, the molten build material is poured into the mold. Once the material has cooled in the mold, the finished object is ready.
It’s important to realize the differences between these two processes in order to determine which works best for your application. That’s what we’re here for – so let’s dive in!
What You Need
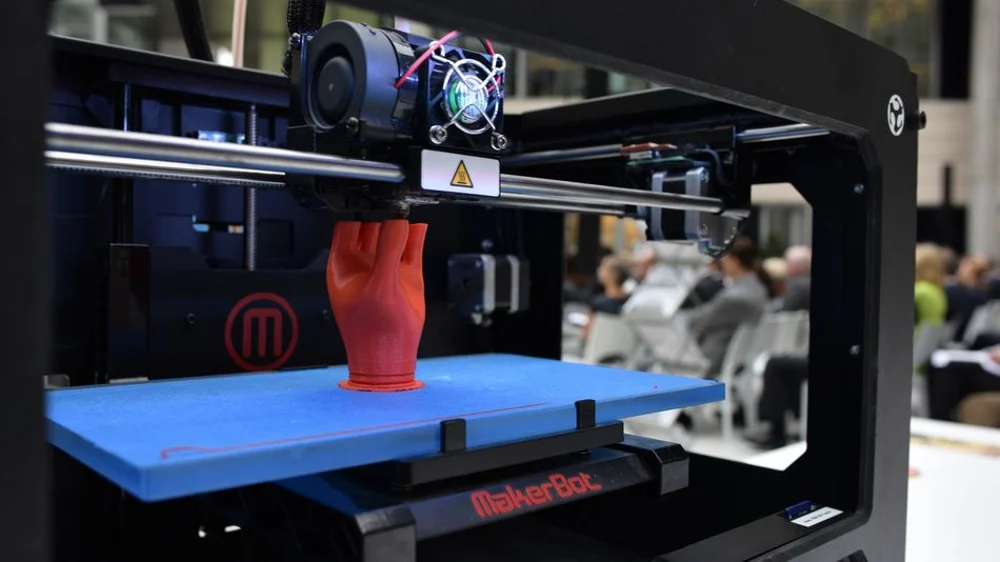
Both 3D printing and injection molding start with a digital 3D design. And while we’re in the design stage, below are a few different things that are needed for these two different processes.
3D Printing
- 3D printer. The obvious answer. You can find whatever you need in a huge range of prices. It’s also worth noting that if you’re not ready to invest in your own machine, you can use various 3D printing services, such as FacFox online 3D printing services, that print your designs with a wide range of materials and machines. These services can be great for testing your initial idea if you’re on the fence about whether you want to be manufacturing in-house or for the long haul.
- Filament/material. 3D printers use spools of filament which are fed into the printer, melted, and extruded onto the printer’s bed to form the object – it’s sort of like using an icing bag. There are many different filaments that exhibit an array of properties, everything from thermoplastics designed for beginners to blends with stone, metal, and wood, which are trickier to manipulate. And as you may have guessed, we have a handy filament guide.
Injection Molding
- Injection molding machine. Duh again, right? But once more, there’s more to this than meets the eyes. Injection molding requires a specific machine that contains a material hopper, an injection ram (or some kind of plunger), and a heating unit. These machines are designed to keep the molds in place while they’re being filled, so nothing jostles them to mess up the final products.
- Molds designed for your object. This is the most valuable tool for injection molding. It will literally make or break your manufacturing, and unfortunately, it’s much easier to make a mistake here than to fix one. Molds are expensive to create from original designs, so a lot of manufacturers make the molds on a large scale to stretch their money further. They’re usually made from hardened steel, aluminum, or a copper alloy to stand up to the heat of the injection process.
- Material for your final object. Like 3D printing filaments, a large range of injection molding materials are available. Metal alloys and plastic polymers are both popular for machine parts and other replacement objects. Again, the specific material you need depends on what you’re making.
Pros and Cons of 3D Printing
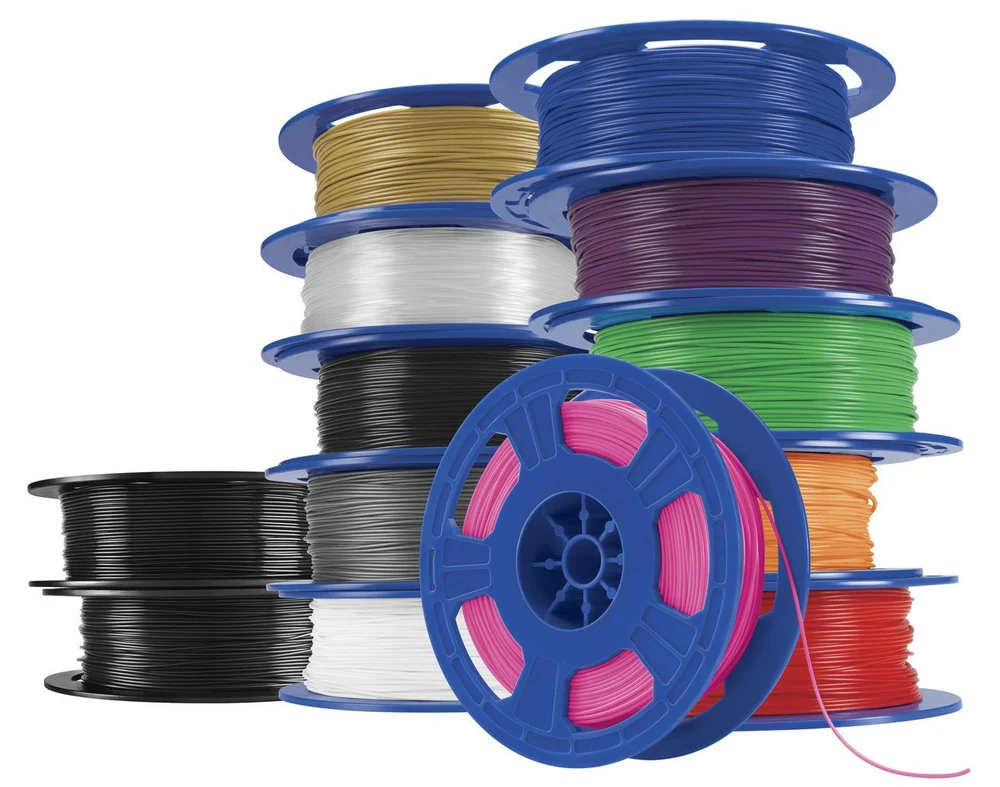
3D printing is a great entry point into manufacturing, especially if you’re looking to print small amounts of intricate designs. Here’s what you need to know about 3D printing to help you decide if it works for your ideas.
Pros
- Low entry cost. You can spend as much money as you want to get into 3D printing – and if that’s not a lot, you’ve still got plenty of options. A desktop 3D printer and a filament supply will set you back exponentially less than an injection molding setup, and the ongoing proliferation of open-source software and hardware in the community gives you a great support network of others who can help you along the way at little to no cost.
- Easy to make changes. Because of its additive nature, you can spot and fix issues with your design while your model is being made. This makes it possible to avoid wasting an entire run of material on objects that all have the same flaw. 3D printers let you pause mid-process and continue in the same spot, which is perfect for spot adjustments that otherwise would make you start all over.
- Easy to support complicated designs. 3D printing’s process of adding layers on top of each other makes it perfect for creating intricate infrastructure. The extruder lends a delicate hand to printing details, and the previous layers act as support.
Cons
- Slow object output. One drawback to 3D printing’s detail-oriented process is that it severely limits how many objects can be printed at one time. The vast majority of 3D printers will only produce one or two models at a time – even machines with more than one extruder.
- Limited build volume. Manufacturing with 3D printers is also limited by the size of their printing area because the extruder arm will always have a maximum reach. Plus, the larger the sections that hang off the edges of the printing area, the more unstable the entire design becomes. Large-scale 3D printing is possible, but even that is relatively small compared to what can be achieved through injection molding.
- Rough object surface. 3D printing’s layers are small and close together – but still noticeable. This creates a ridged surface on finished objects no matter how fine the layer detail is set. This presents a problem if you want to manufacture objects that will move against other objects, like machine parts which should be flush. At the very least, you will have to add an extra smoothing step to your process if you want to use 3D printing without its distinctively bumpy finish.
Pros and Cons of Injection Molding
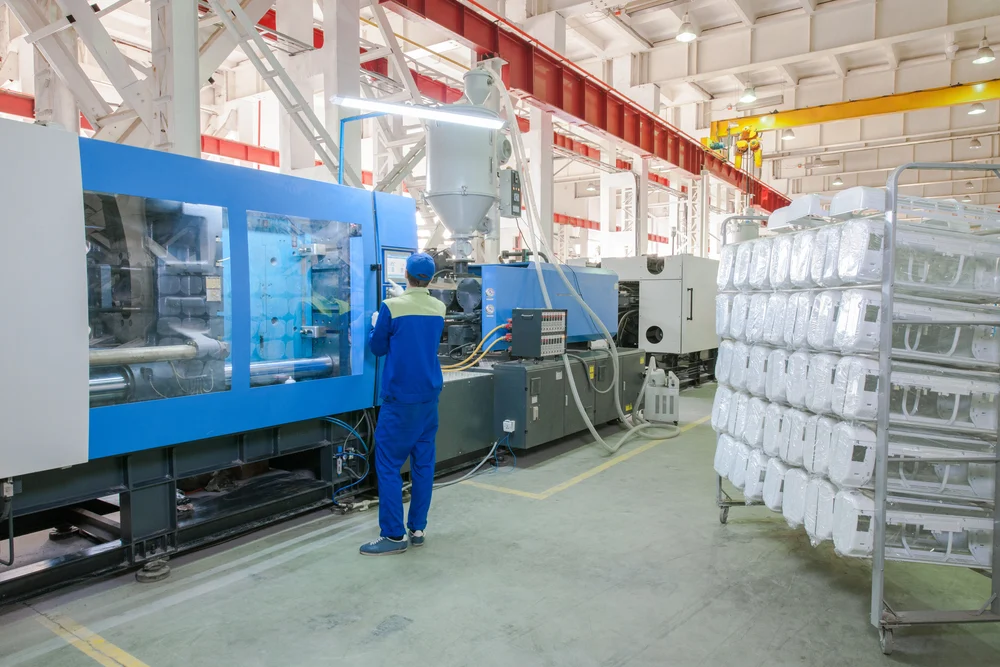
Injection molding is a tried and tested manufacturing process. It’s got a lot going for it, but it’s not without its own issues to consider.
Pros
- Large simultaneous output. Injection molding is designed to utilize a large number of molds at once. The machines are built on a scale that lessens the cost of each mold with every one that’s added, so producing batches of dozens, hundreds, or even thousands of molded objects is the norm. This is perfect if you’re ready to mass produce your design.
- Enhanced object strength. Objects made through injection molding consist of a single poured layer, which adds strength to the shape because there are no fissures or points of weakness. Furthermore, injection molding can handle pure varieties of dense materials like concrete that have to be diluted or otherwise modified for 3D printing filaments.
- Minimal scrap produced. Because injection molding pours material as fits into the molds, it uses exactly as much as is needed for each design. That makes it a very efficient way to mass produce objects without worrying about waste.
Cons
- Limitations of design. Constructing a mold constricts the geometry of your designs in several crucial ways. First, right angles are inadvisable because they make it difficult to pull out the hardened object without risking breakage. Slanted angles ease edges out with less competing pressures. Second, injection molding just doesn’t lend itself to delicate areas of design that stand on their own. Creating a mold – an inversion of your design – is not as precise as additive technology.
- Difficult to correct mistakes. In the same vein, discovering and rectifying any mistakes you find in your injection molding process will cost you time, money, and sanity. If an object turns out wrong, that means the mold needs to be completely remade, and chances are you’ll need to redo an entire batch of objects as well.
- High entry cost. Injection molding machines alone cost upwards of six figures – they’re designed for industrial use, rather than hobby use. That doesn’t include the cost of making your molds, getting your materials, and prototyping all the designs before putting them into production.
Ideal Applications
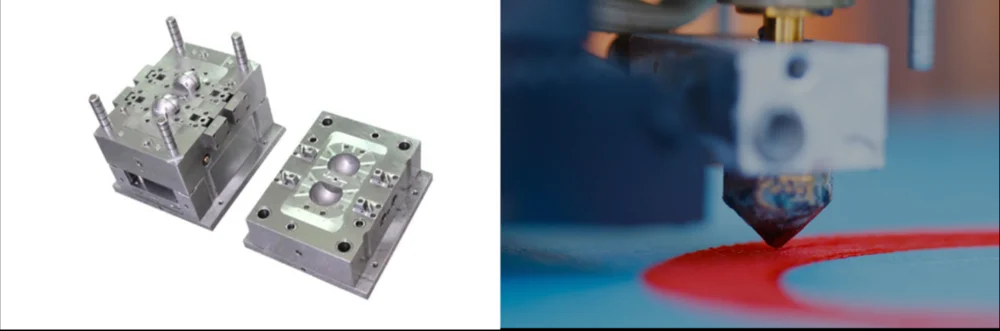
So, what have we learned about the distinctions between 3D printing vs injection molding? Basically, they’re two different ways to approach the same basic task – creating 3D objects. But because of their different strengths and weaknesses, their use cases are different.
3D printing is best for…
- Limited run objects. This includes objects like prototypes or small-batch production, among others.
- Designs with a lot of gaps or holes in the middle. 3D printing is great for adding design support as it’s needed, like when a piece branches off or causes a gap.
- Tweaks in design. 3D printing lets you adjust your design as it comes to life, so it’s great if you’re not sure where your design might fail during the creation process.
Injection molding is best for…
- Large batches of finished objects. If you’re looking to create a large number of identical objects at the same time, injection molding has you covered.
- Solid designs. Injection molding’s one-step forming process makes your model one continuous form, which adds strength to your finished object.
- Objects that will move against something else. There’s no need to add an extra finishing step to make sure injection-molded objects are smooth enough to reduce friction against moving parts – this makes it especially suitable for applications where parts mesh together.
3D printing and injection molding are both excellent ways to make your creations come to life. Now go forth and create!
Source: 3D Hubs
https://all3dp.com/2/3d-printing-vs-injection-molding-know-the-differences/