In 3D printing, stringing is a common problem, especially with flexible materials. Overcome this issue with these five simple solutions!
As an FDM printer nozzle travels across an open space to get to the next point, it may sometimes ooze melted plastic, which then solidifies and sticks to the printed parts. This is 3D printer stringing, and it leaves your 3D printed parts with thin strands of plastic that resemble cobwebs or strands of hair.
In theory, your nozzle should not deposit plastic as it travels through open air (otherwise known as a travel move). However, molten plastic will often leak onto parts where it shouldn’t, leaving your prints with what looks like “whiskers”.
The leading causes of stringing in FDM printers are using incorrect retraction settings and setting the hot end temperature too high. PETG, for example, requires relatively high temperatures for melting and is notorious for stringing. PLA and ABS, however, are also known to have this issue.
Luckily, there are some ways of preventing 3D printer stringing. Let’s take a look!
Enable Retraction
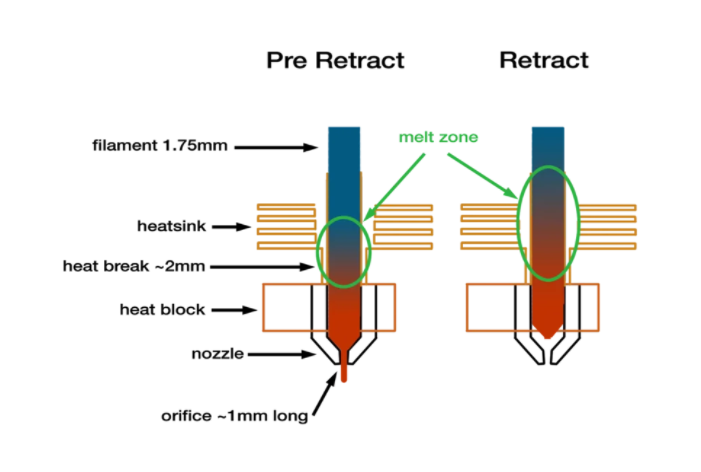
Enabling retraction is the most common method used to combat 3D printer stringing. Enabling retraction means that, where the extruder has to cross an empty space, the filament will be pulled back – just a little bit – by the feeder. This prevents the molten plastic from trailing behind as the printer head moves because the “pulling back” action serves as a countermeasure against oozing. Once the extruder has arrived at the next location, the filament is pushed back out, and printing resumes from the nozzle again.
In most slicing applications, like Cura, retraction is usually enabled by default. However, it’s always a good idea to confirm that this is true, especially when you start experiencing stringing. If the retraction setting is turned on and you’re still experiencing 3D printer stringing, you may then need to go into the nitty-gritty of the retraction settings:
Retraction Distance
Retraction distance is probably the most critical retraction setting, as it determines how far the filament travels. Generally, if your nozzle can retract further, it means you’re less likely to encounter 3D printer stringing. But again, if you retract too far, the filament may be unavailable in the hot end when you need to resume printing.
The retraction distance may vary depending on the type of extruder you’re using. However, an extruder on a Bowden setup will typically require a higher retraction distance, owing to the longer distance between the nozzle and the drive gear.
To determine the correct retraction distance, you may have to perform test prints. Try this retraction test print: It prints quickly and does not require too much filament.
Retraction Speed
The retraction speed determines how quickly the filament is retracted. A faster retraction speed suggests that 3D printer stringing is less likely to occur because the filament is pulled back fast enough before it starts oozing. However, when the retraction speed is too fast, it may cause the filament to disconnect with the other portion inside the nozzle. Worse, a quick movement of the drive gear may grind the molten plastic and jam the nozzle or create areas where the filament is not deposited.
Therefore, you should aim to find a sweet spot (between slow and fast), where retraction is optimal. This sweet spot may vary depending on the printing material. Perform a few test prints to determine the ideal retraction speed.
If you’re still unsure of what to do, check out Simplify3D. This program comes with pre-configured profiles that are a great place to start if you’re looking for a retraction speed that works best.
What Settings Should You Use?
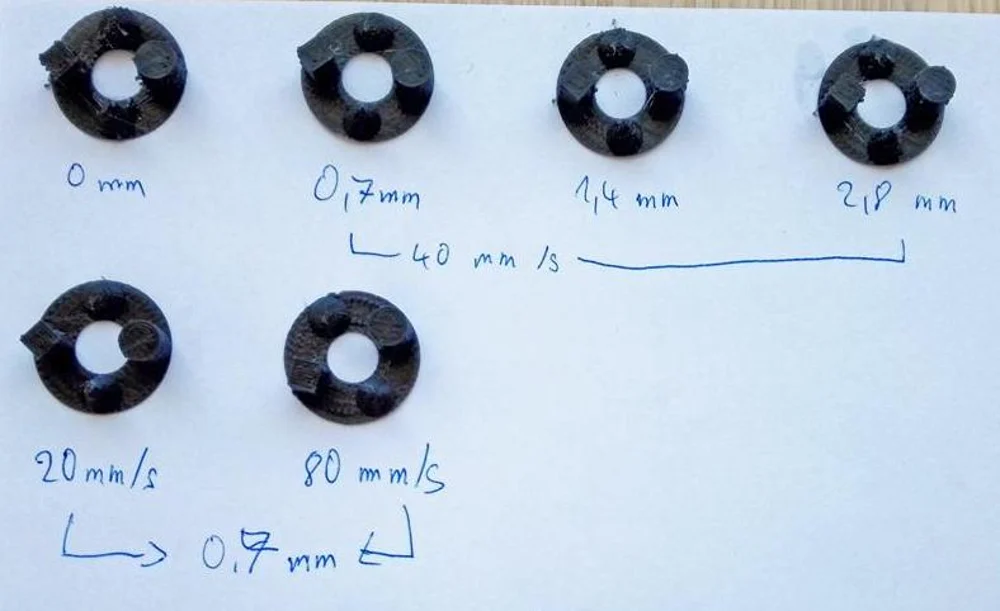
To determine the optimal retraction values, you must first know the extruder you will be using and the material you will be printing with.
Materials like ABS and PLA will do well with a speed of 40 to 60 mm/s and a retraction distance of 0.5 to 1.0 mm on direct-drive extruders. On the other hand, extruders on Bowden setups will generally require a speed of 30 to 50 mm/s, with a retraction distance of around 2.0 mm. These figures are not constant and can change based on many variables.
At the end of the day, when retraction is done correctly, it’s effective at ending stringing, and it’ll give you more control over your prints. Some slicer programs, like Simplify3D, come with “coast” and “wipe” parameters that are powerful tools for further dialing in your retraction values.
Set the Right Temperature
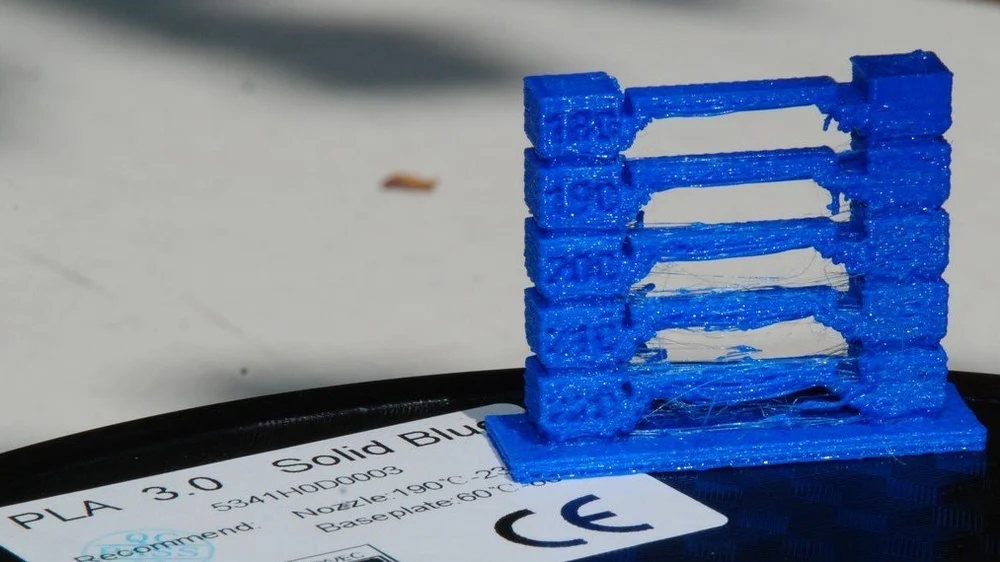
As the temperature increases, the printing material becomes more liquefied and is more likely to drip from the nozzle, even after adjusting the retraction settings. A lower temperature reduces this likelihood. However, you must be careful to not set the temperature too low. Very low temperatures could make the filament not melt enough, which could create issues with extrusion.
An ideal temperature depends on the printing material and other printing settings. However, it’s generally recommended to lower the temperature once you notice stringing. You can try reducing the nozzle temperature by 5 to 10 °C increments, but never reduce the temperature below the manufacturer’s minimum specifications. These are the commonly recommended temperatures for some of the most common filaments:
- PLA: 180-220 °C
- ABS: 200-250 °C (90-100 °C print bed)
- PET: 215-235 °C
- TPE: 210-240 °C (20-70 °C print bed)
- PVA: 160-190 °C (60 °C print bed)
- TPU: 230-250 °C (60 °C print bed)
Using a temperature calibration tower test print is a great way to identify the ideal temperature for each printing material.
For further guidance, our article on the best printing temperatures for different filaments has covered the most common filaments and is a great place to start if you’re looking for the ideal printing temperature for your filament.
Adjust the Print Speed
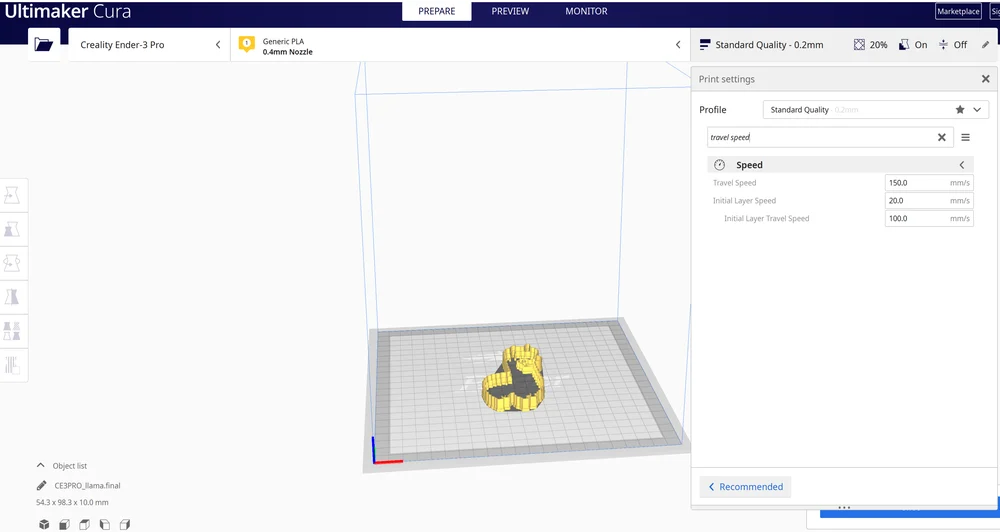
The print speed can also affect 3D printer stringing. If, for example, your nozzle takes too long to move between two points, stringing is likely to occur because molten plastic has more time to ooze out of the nozzle. But if the extruder can travel faster, the short moves may be quick enough that the filament will not have enough time to ooze.
Increasing the travel speed of the nozzle when it’s not trying to print can reduce 3D printer stringing, but if the temperature is low and the print speed is too high, you may end up with under extrusion because the plastic will lack enough time to drip.
Generally, a speed of 190 to 200 mm/s will work fine with most printing materials, but MatterHackers has found 150 mm/s to be the ideal travel speed for most printers.
As a creator, you’ll need to verify what speed your printer is using before you can decide to make any adjustments. X/Y axis movement speed, for example, represents the travel speed from side to side, and this speed is directly related to the length of time the nozzle will spend moving across an empty space.
A program like Simplify3D has a feature that ensures the travel path is short enough to reduce oozing, even if it means avoiding open spaces altogether. In fact, most slicer packages have a setting to speed up the nozzle for non-printing movements.
Thoroughly Clean the Nozzle Before Printing
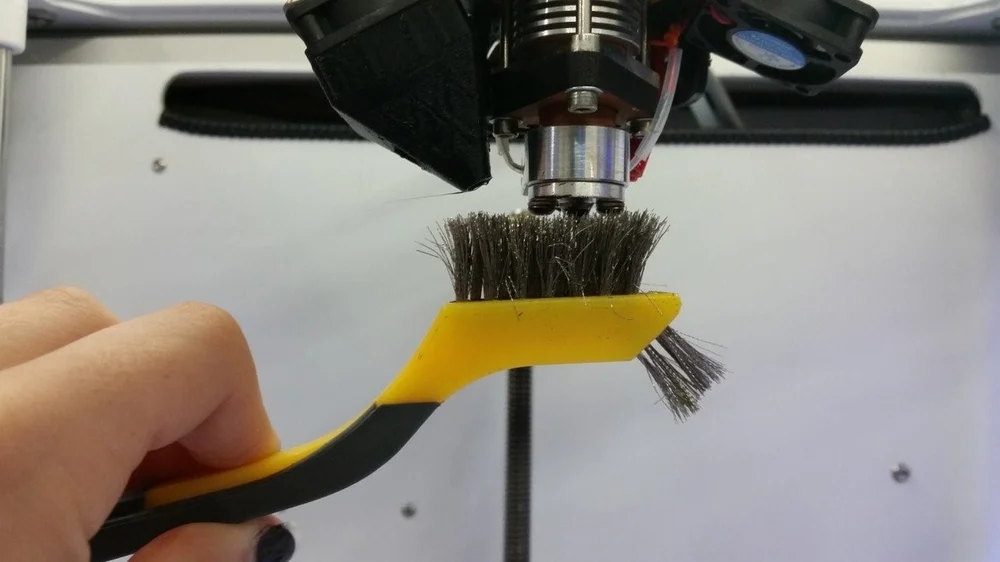
When you use a printer for a long time, especially with a single type of printing material like PETG, the filament can leave a thin layer of residue in the nozzle. This thin layer can cause 3D printer stringing as filament strands will try to stick to the surface of your printed part.
To avoid this type of problem, ensure your nozzle is thoroughly cleaned before any printing to remove any dirt from the previous filaments. For more guidance, check out our well-detailed nozzle cleaning guide.
Keep Your Filaments Moisture-Free
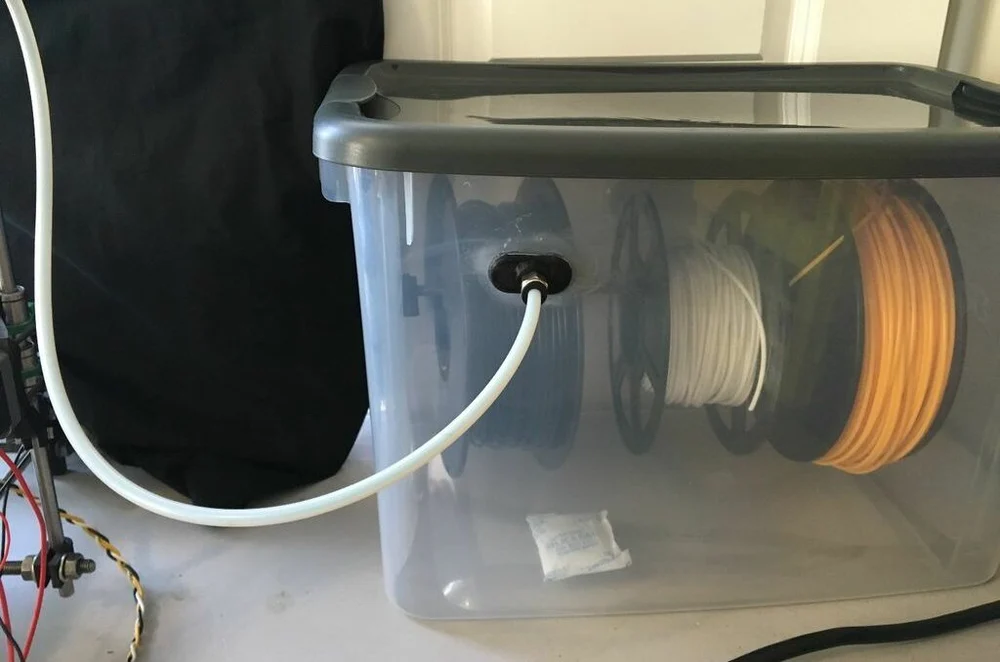
PLA is the main culprit here because it tends to absorb more moisture compared to ABS. Once moisture is present, it’ll tend to turn into steam as the plastic gets heated up. This steam can mix with the plastic and can increase the probability of oozing during non-print movements.
Therefore, you should store your filament in a moisture-free environment, like a plastic box, especially if you live in a humid environment.
Source: https://all3dp.com/2/3d-print-stringing-easy-ways-to-prevent-it/