Additive manufacturing of metal parts is set to revolutionize how many things are made. Selective laser melting (SLM) is one of the premier technologies, but how does it work? That’s what this article is all about.
What Is SLM?
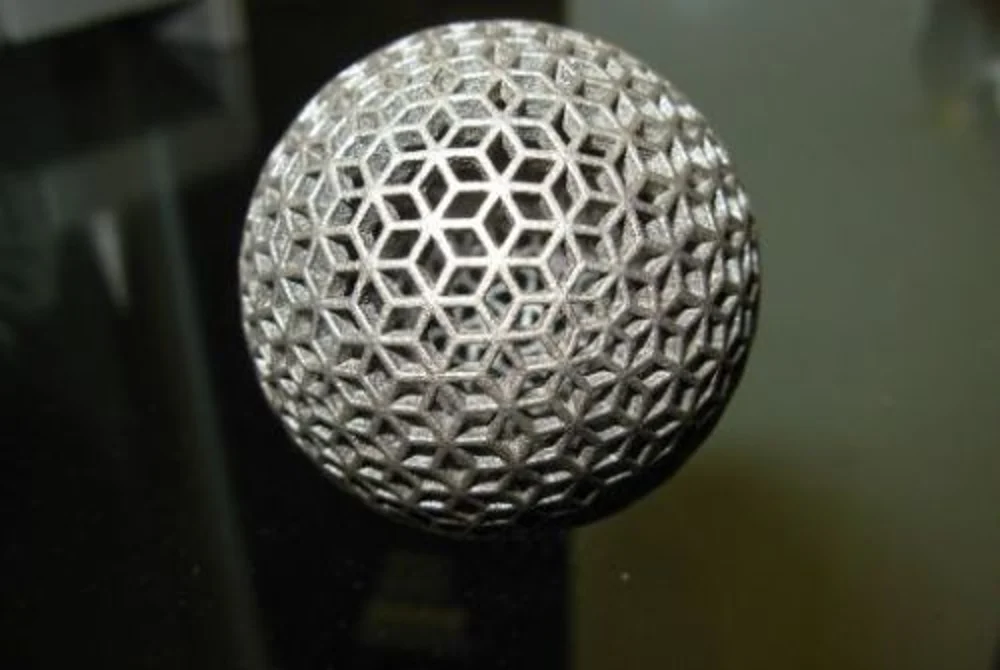
Selective laser melting (SLM), also called direct metal laser melting (DMLM), is a type of metal additive manufacturing or 3D printing. Often, the terms SLM and direct metal laser sintering (DMLS) are used interchangeably. However, the two technologies differ slightly, in that SLM melts metals while DMLS fuses or sinters metals.
SLM is one of the most exciting 3D printing technologies available today and is utilized both for rapid prototyping and mass production. The range of metal alloys available is fairly extensive. The end result has properties equivalent to those manufactured via traditional manufacturing processes.
How Does It Work?
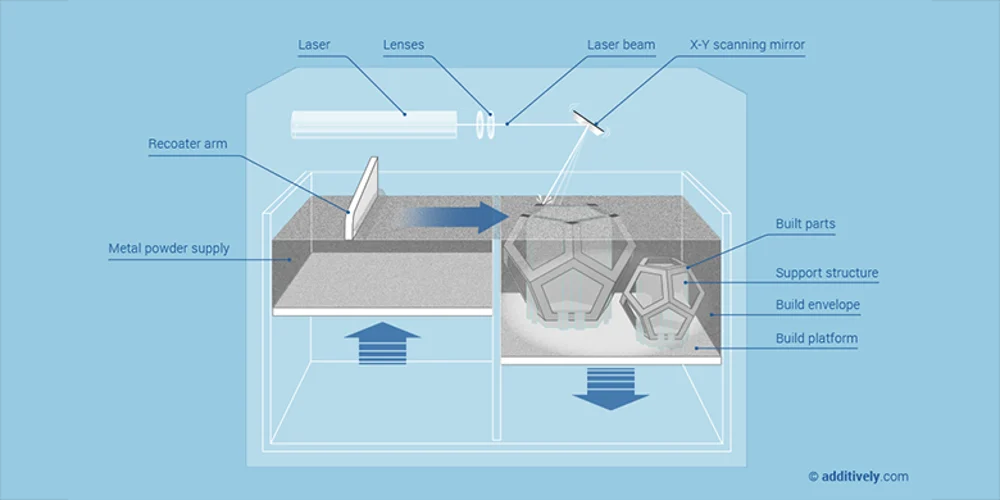
SLM is very similar to DMLS, and both processes are covered under the metal powder bed fusion umbrella. As demonstrated in the image above, the laser melts the powder together, layer-by-layer, until the model is complete.
On a molecular level, the powder is melted together, resulting in a homogeneous part. Most commonly the printing materials are “pure” materials, for example, titanium. However, alloys are also used.
Although the powder bed lends support to the print while printing, often, because of the weight of the material, SLM requires support structures to be added to any overhanging features.
The Process in Depth
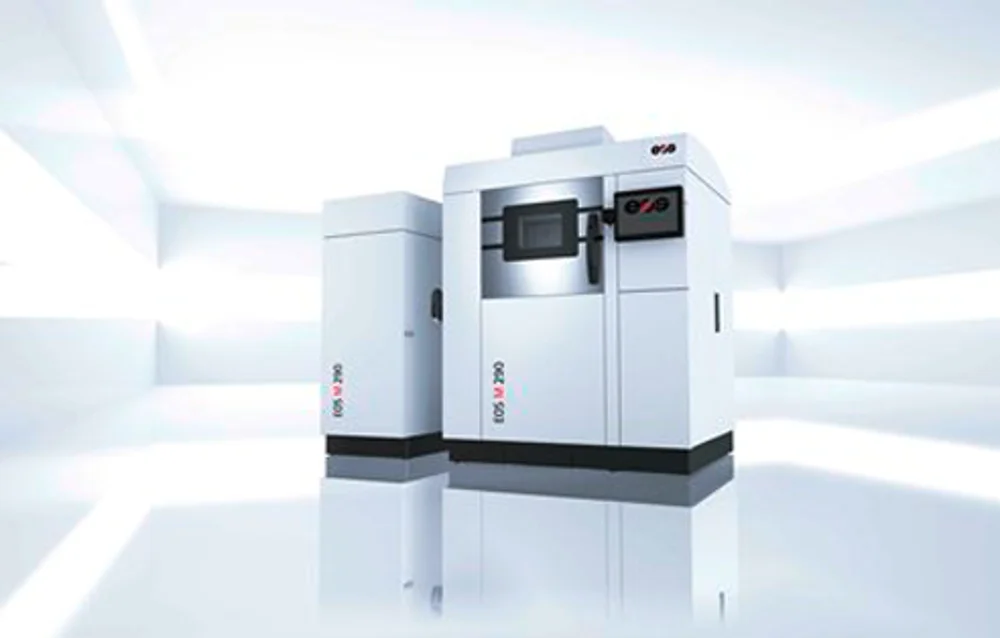
An SLM machine has a chamber filled with metal powder. This metal powder is then spread across the substrate or build plate in very thin layers by a coater blade.
A high power laser then fuses a 2D slice of the part by selectively melting the powdered material. The build plate then drops down by the height of one layer, and the coater spreads another layer of fresh powder finely across the surface. The process is repeated until you have the finished part.
This whole process is performed in a controlled atmosphere inside the machine. Once the part is built, it can be removed from the machine. SLM parts need to be removed from the build plate, which is often done with a bandsaw. Then you need to remove the supports. As the support material is the same as the part material, this can be difficult and a time-consuming process.
The surface finish of the sintered parts is rough and, depending on your requirements, may need some post-processing. It is also common to machine parts to achieve fine tolerances and finish fine features, surfaces, and holes.
Pros and Cons
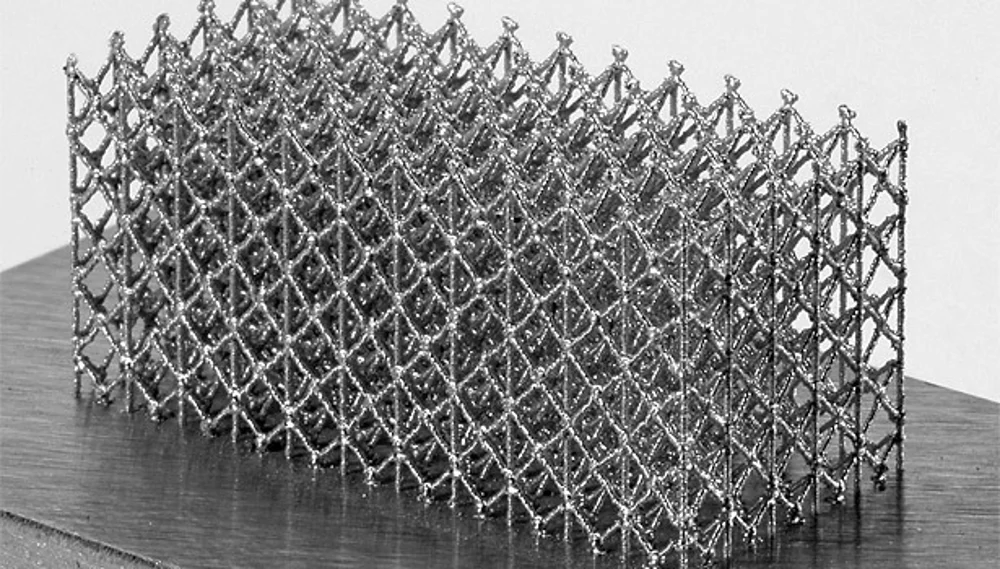
SLM is a great alternative for traditional manufacturing methods. Here are the pros and cons of producing a model via SLM as opposed to traditional methods.
Advantages
- Large range of metals available
- Ability to realize complex shapes or internal features (which would be incredibly difficult or expensive to achieve via traditional manufacturing)
- Reduced lead times, due to no need for tooling
- Part consolidation, allowing the production of multiple parts at the same time
Drawbacks
- Expensive, especially if parts aren’t optimized or designed for the process
- Specialized design and manufacturing skills and knowledge needed
- Limited currently to relatively small parts
- Rough surface finish
- Lots of post-processing required
A Shiny Future
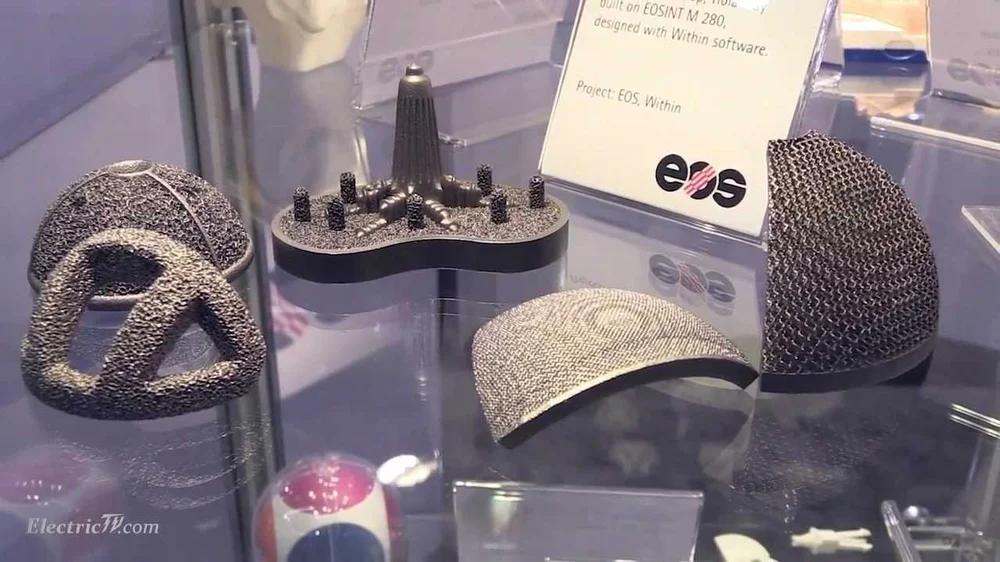
Despite its potential, SLM is only being utilized in a few industries. This is mostly due to the high cost of the equipment and the parts, as well as the post-processing requirements. The industries where it is most useful, as of now, include the following:
- Medicine: patient-specific implants and other high-value medical device components
- Automotive: high-speed prototyping and bespoke parts or low volume high-value applications
- Aerospace: ducts and other parts
- Tooling: conformal cooling channels in production tool inserts
SLM is an exciting technology with a lot of potential applications. As the use cases grow, the technology matures and the process and materials become cheaper, we should see it become more and more prevalent.