When it comes to 3D printing, challenges abound in matching the capability of the most advanced magnets produced by traditional methods. Learn all about the possibilities in 3D printed magnets!
Your Question, Answered
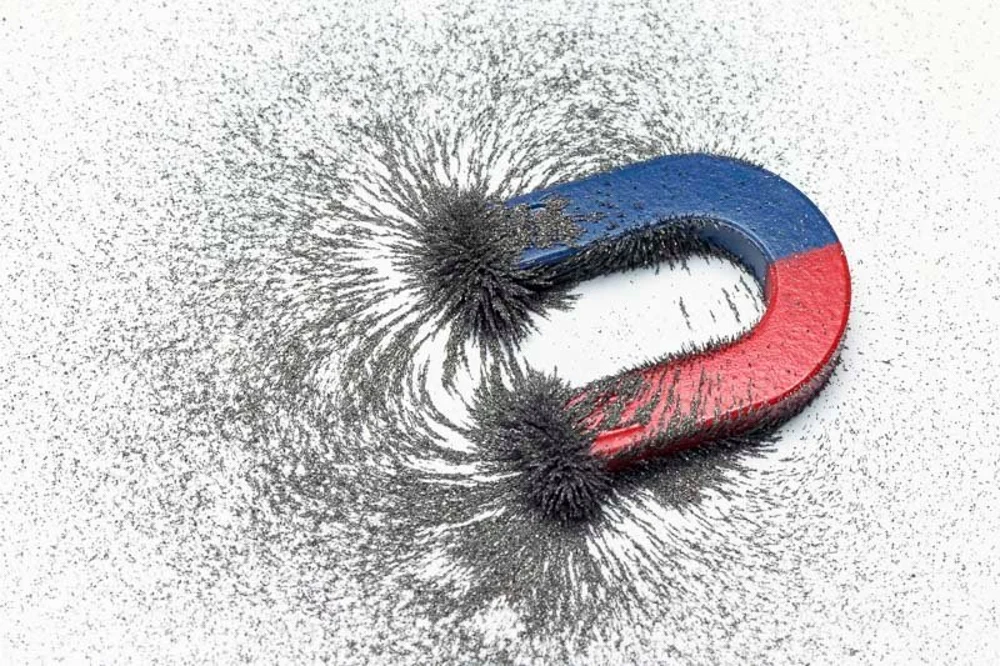
So, is 3D printing magnets possible? Sort of, but not yet at home.
Bringing the power of 3D printing to magnet manufacturing is attracting a lot of interest. Magnets are made of critical rare earth metals, such as neodymium, which are in short supply and high demand in the current push for electric cars and alternative energy. 3D printing can help reduce overuse of this material with its ability to create efficiently-shaped and -sized magnets without the time or expense of tooling. This also helps to quickly bring new designs to market.
So what’s the hold-up? A magnet seems simple. There’s a north end and a south end. We even use magnets on our refrigerators. How complicated can they be?
Beneath the surface, the most powerful permanent magnets have an organized granular structure that’s a challenge to recreate with a 3D print head.
In order to understand the potential of 3D printing magnets, let’s first take an in-depth look at what actually makes materials magnetic.
What Makes Material Magnetic?
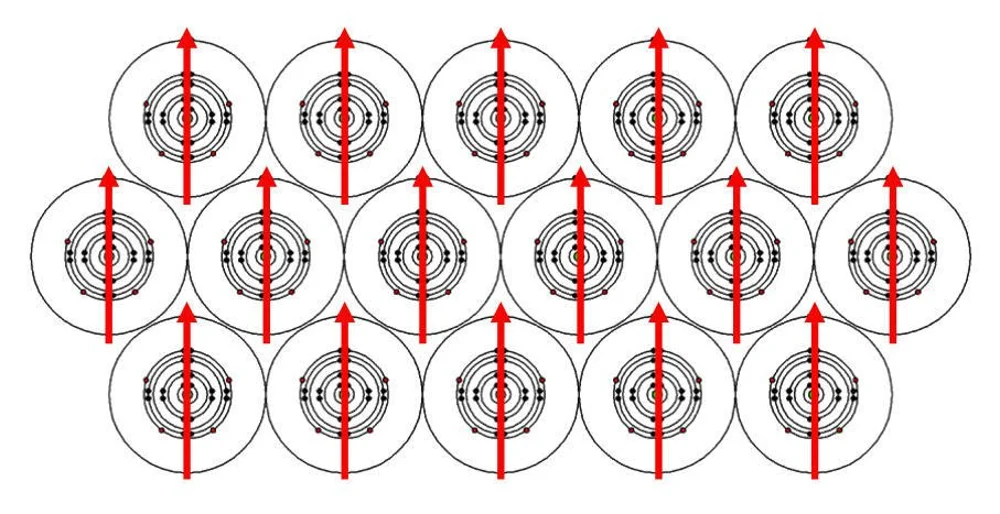
All materials have electrons. As small as they are, electrons have what is called “spin”. This spin creates a tiny magnetic field so that each electron is like a tiny magnet. In non-magnetic substances (like wood, water, or aluminum), these electrons and their tiny magnetic fields are arranged in opposing pairs, essentially canceling each other out.
In ferromagnetic materials, like iron, some unpaired electron spins favor being aligned so that their magnetic fields add together rather than cancel out. Interestingly, in a plain piece of unmagnetized iron, this alignment of spins and their microscopic magnetic fields spread through the entire piece of material. The result is that the material is divided into sub-millimeter magnetized regions, called magnetic domains.
Within each magnetic domain, all of the unpaired spins are aligned. When a piece of iron is in the unmagnetized state, these domains exist but are randomly oriented and create a net zero magnetic field. However, if exposed to a sufficiently strong magnetic field, the domains will align, and the iron is magnetized with a north and a south pole.
Hard vs Soft Ferromagnetic Materials
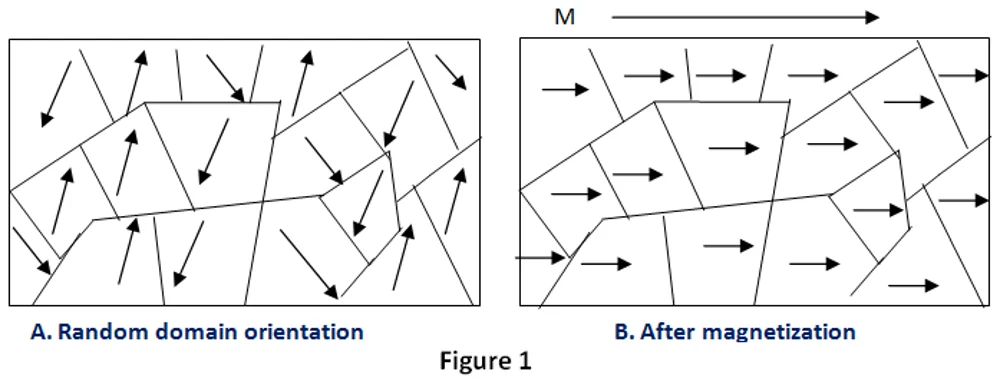
Only three of the elements in the periodic table are ferromagnetic at room temperature: iron, cobalt, and nickel. Practical magnets are based on these elements but are often combined with other elements, such as neodymium and samarium, to modify their properties.
“Hard” ferromagnetic materials, or permanent magnets, maintain their magnetized state, attracting materials like iron and steel regardless of surroundings and electrical current. These materials are not easy to magnetize, requiring a strong field and energy to change the direction of their magnetic domains. On the other hand, they also hold their magnetization permanently.
In “soft” ferromagnetic materials, like pure iron, the magnetic domains align (and disalign) easily to an external field. This means they can be easily magnetized and demagnetized. Soft magnetic 3D filament is currently available, but because much of the material is PLA (and therefore non-magnetic), there are limitations if you are considering serious soft magnetic applications, like inductors or transformer cores.
Isotropic vs Anisotropic Magnets
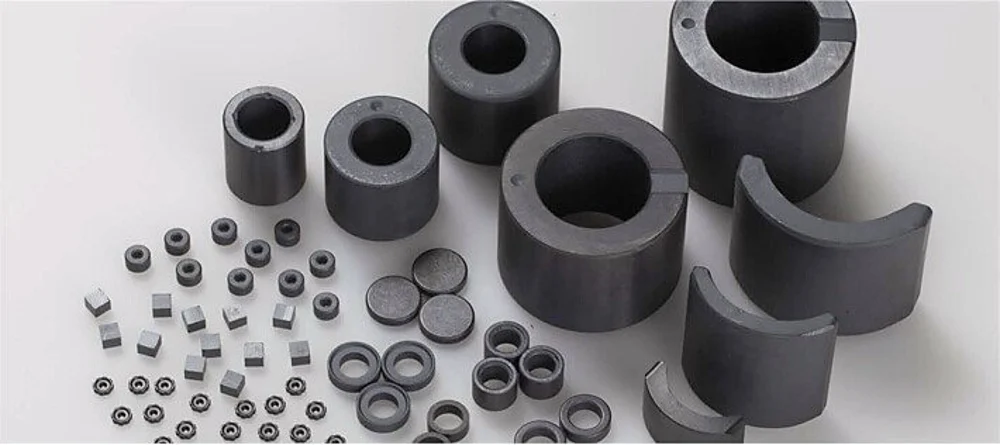
Permanent magnets are all about direction: north and south. But before magnetization, the raw materials of magnets exhibit this same directionality, or magnetic anisotropy. This means they have a preferred direction for magnetization.
During the manufacturing of anisotropic materials, powders of ferromagnetic material can be pre-aligned so that the fine grains line up with the desired direction of magnetization. This alignment can be done with a strong magnetic field or when the powder is squeezed with high pressure. Once the grains are aligned, they are locked in place before the actual magnetization step. This pre-alignment results in a stronger magnet because all of the crystals point in the preferred direction and contribute to the resulting magnetic field.
Manufacturing isotropic magnets create unmagnetized bodies with grains pointed in every direction. When it comes time to magnetize them, only a fraction of the grains can contribute. This means that the resulting magnet is weaker. However, it simplifies manufacturing, which also means that any direction of magnetization is possible.
Sintered vs Bonded Magnets
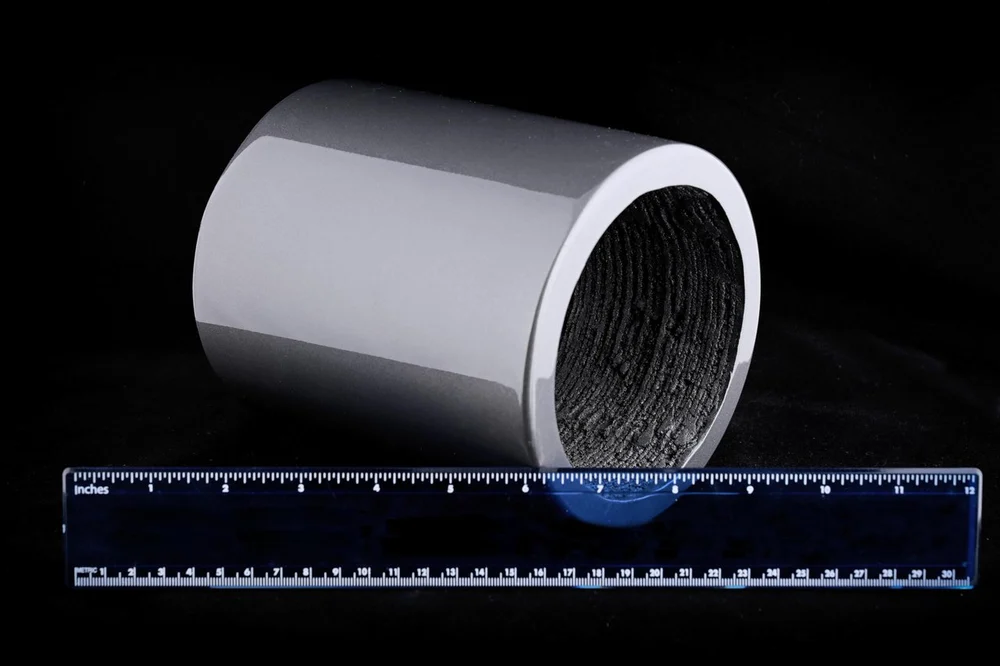
Sintered magnets are the gold standard for magnets of today: solid magnetic material, formed with pressure and temperature without a filler or bonding agent. Today’s most powerful neodymium magnets are sintered anisotropic magnets.
Bonded magnets use nylon or epoxy to adhere the magnetic grains. The bonding process allows for more intricate designs and mass production techniques like injection molding. However, the bonding substance dilutes the density of the magnetic material and therefore the strength of the magnet.
While it doesn’t create the strongest magnets, bonding technology forms the basis for most of the current research in 3D printed magnets.
3D Printing Magnets at Home
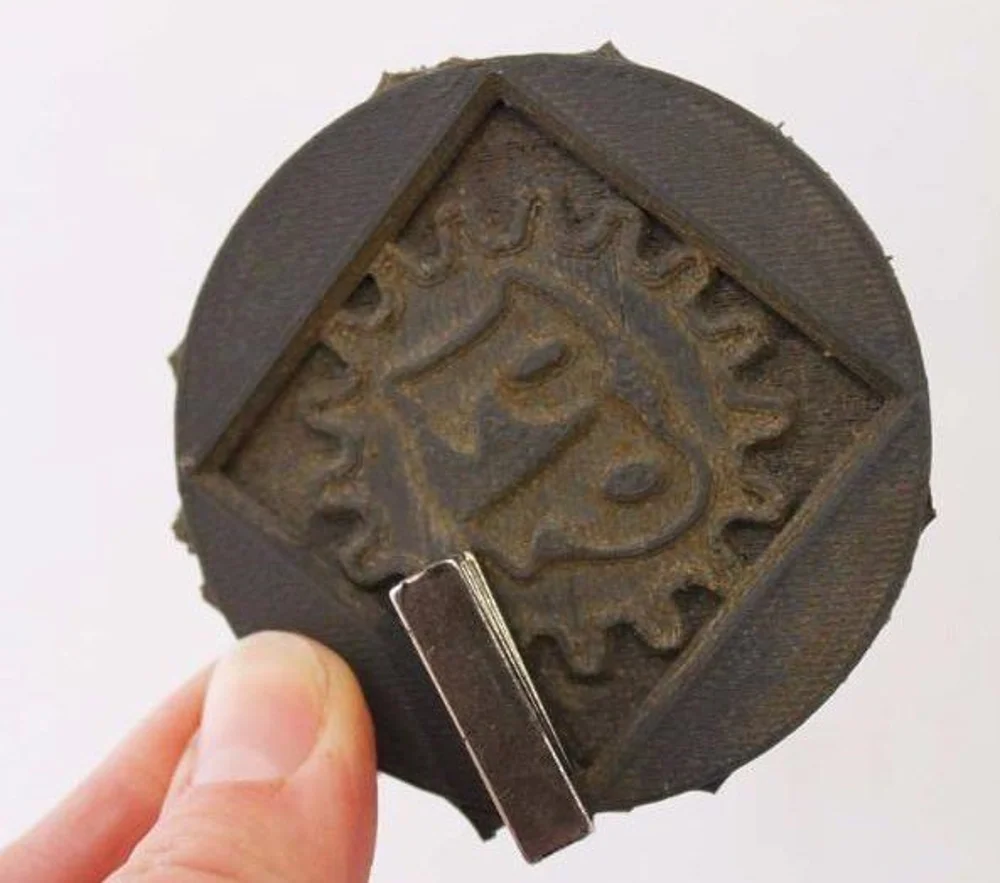
As you can probably guess, desktop magnet 3D printing is limited to filaments composed of soft magnetic material. In other words, prints will react to magnetic fields but won’t be able to produce them.
While other “magnetic” filaments exist, perhaps the best-known is Proto-Pasta’s Magnetic Iron PLA.
3D Printing Magnet Research
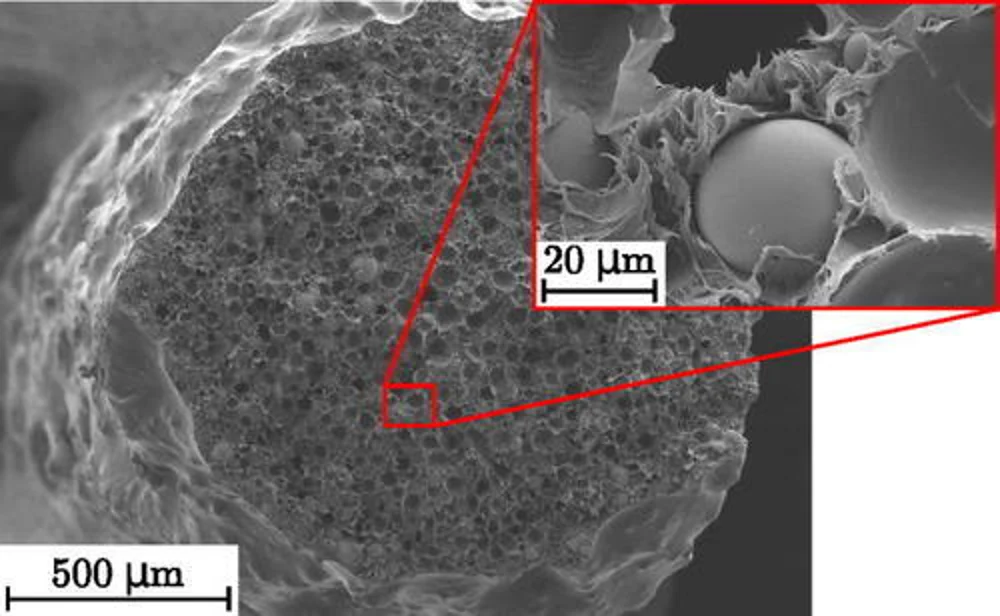
With magnets being so critical and 3D printing being such a revolution, it’s no surprise that researchers are looking into how to bring the two together.
One of the first publications detailing 3D printed magnets comes from the Vienna University of Technology. They proved the concept that 3D printed magnets are possible, using custom magnetic filament and a standard printer.
At MIT, researchers have combined a magnetic 3D printing ink and magnetic field applied during extrusion to control the magnetic directions of 3D printed regions of soft magnetic materials. The process doesn’t create a magnet, but their innovative use of a field in the actual printing may point toward future advances in 3D printed magnets.
Oak Ridge National Labs (ORNL) is using additive manufacturing to work on the problem of the efficient use of the critical rare earth elements used in the manufacture of permanent magnets. Their Big Area Additive Manufacturing (BAAM) system is showcased in a wide range of BAAM projects. It has been applied in the creation of large magnets over 5 inches in diameter. What may come as a surprise is that BAAM doesn’t use filament. Filament melting is simply too slow to keep up with the deposition rates they need. Instead, BAAM directly extrudes pellets to create parts at high speed.
Originally limited to isotropic magnets, ORNL has extended their work to include a post-printing alignment step for anisotropic powders. This is pushing them closer to directly competing with existing injection-molded magnets while offering the scale of BAAM and tool-less advantages of additive manufacturing.
What’s Ahead?
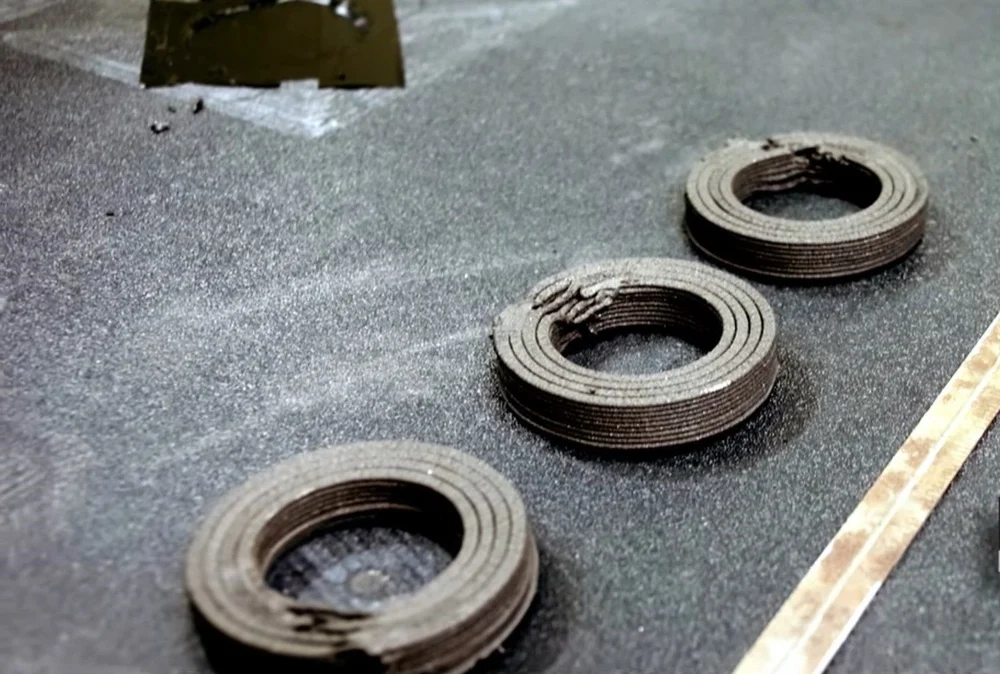
Higher concentrations of magnetic material and lower concentrations of plastic binder strongly affect magnetic strength. This, along with the move to anisotropic materials, are under development at ORNL and elsewhere.
What does this mean for your desktop 3D printer at home? Will these advancements make their way into an affordable filament? Maybe… Deposition is just one step of making a magnet, and magnets may not be a big DIY application. But, looking into the crystal ball, these magnetic powders are nylon-coated, so maybe they’ll end up in a Multi Jet Fusion system, which uses just such powders.
Whether created at home or in industry, powerful magnets are central to applications like electric cars and wind generators. Bringing the power of additive manufacturing and 3D printing to these 21st century needs only makes sense.
Source: https://all3dp.com/2/3d-printed-magnets-is-it-possible-to-3d-print-them/