The augmented reality (AR) market is newer than additive manufacturing (AM), and AR technology can only be realized in actual deployment. This is partly due to the rapid development of mobile computing technology, and depth perception has been integrated into smartphones, thereby providing AR platforms with greater space perception capabilities.
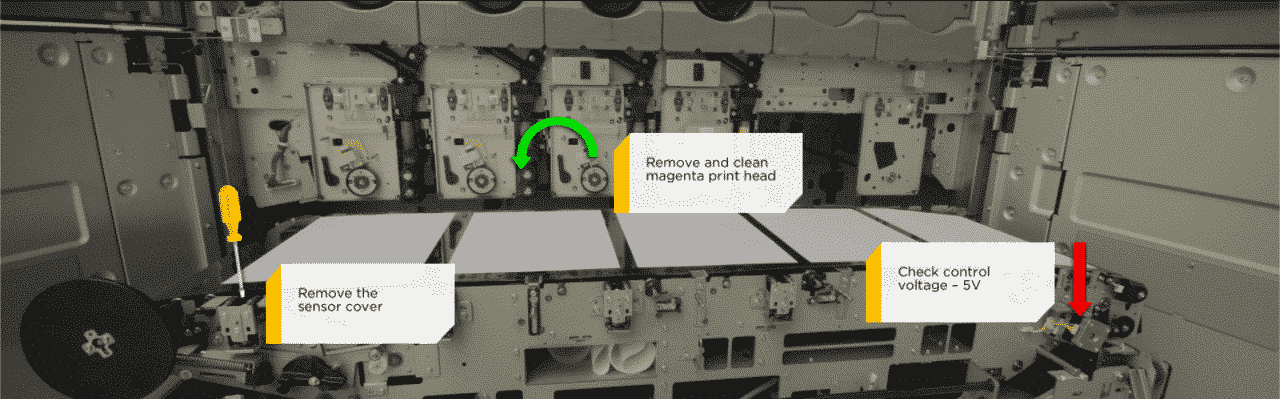
In an industrial environment, AR’s most promising applications include remote support for complex devices. Consulting startup 3D Alliances has sought to address this area by establishing a partnership with Israeli counterpart Fieldbit. 3D Alliances is working with AR to develop its existing platform to provide field service technicians with real-time information and guidance on AM technology.
Gil Lavi, CEO of 3D Alliance, told us that the platform will allow 3D printing companies to perform remote field services, including installation, technical training, and continuous technical support for machine operators. Although such operations are obviously time-consuming and complex, they become more challenging during the isolation of the quarantine associated with the COVID-19 pandemic, and social alienation and hygiene guidelines both restrict installation and maintenance and make implementation more difficult.
“In the past few weeks, I’ve heard that more than several [original equipment manufacturers (OEMs)] did remote installation of their printers over the phone. Imagine how complicated it is when an industrial 3D printer is involved, and not a desktop one, which is in many cases self-installed. Conducting this process over the phone is very challenging and has risks,” Lavi said. “Usually it’s done physically at the customer site and now it has to be remote in many cases. What I see these days: OEMs are recording videos with instructions of how to use the printer—again training over the phone. This is a limited source of knowledge. The user can’t ask questions and it takes valuable time.”
In addition to the above-mentioned challenges related to remote installation and training, continuous technical support is also an important issue. Certain technical problems can only be solved by OEM expert engineers, which is not always possible and is currently particularly challenging.
In this way, using AR can help equipment operators perform these tasks with remote assistance. Fieldbit’s AR technology is currently available on a variety of platforms, including Android and iOS mobile devices and smart glasses, such as RealWear and Vuzix glasses. Using the Industrial Internet of Things, this technology can be used to obtain real-time feedback from components in the system, guide installation, indicate what needs to be repaired, or introduce the user to the way the system works.
So far, Fieldbit has listed examples that are more widely used in industrial 2D printing and manufacturing. With the help of the 3D alliance, the company will see that the technology is suitable for AM system manufacturers, and they will be able to deploy remote assistance. Reducing the downtime experienced by the AM system, in turn, means that the machine can be restarted and running, which means that less money is wasted by idle printers.
For the 3D alliance, this can expand its influence in the field of additive manufacturing, because it can consult the hardware and software 3D printing business and help recruit new talent. So far, the company claims that its network includes “tens of 3D startups from 73 countries and more than 1500 active 3D printing/additive manufacturing distributors.” Considering the natural combination of AR and 3D printing in other areas, it is not surprising to see these two technologies merge here. In fact, this partnership represents a broader digital thread that is currently being sewn to stitch Industry 4.0 together.