3D Printing Industry is in Detroit this week to bring our readers all the news from RAPID + TCT. So far we’ve published over 30 articles dedicated to all the latest in the additive manufacturing ecosystem – with much more to come.
Across the first two days of RAPID + TCT 2019, we picked out some key themes developed through keynotes and news originating from the show. Now, from the penultimate day of this year’s event, we hone in on one of the conference’s dedicated tracks – medical.
How is the 3D medical market shaping up?
The RAPID + TCT Medical Manufacturing Innovations (MMI) keynote this year was delivered by Dr. Naomi Murray, Director of Advance Operations, Additive Technology Solution, at leading American medical device manufacturer Stryker.
Stryker is best known in additive manufacturing for its Tritanium technology, applied to create porous, cell-stimulating, spinal implants/cages. In the keynote, Dr. Murray explained that rapid prototyping was never a viable, or valuable option for 3D printing at the company. Instead, the Stryker team has always targeted end-use with additive manufacturing, as this is the point at which they can have a legitimate impact on patient’s quality of life.
In August 2018, Stryker acquired a competitor and fellow medical device manufacturer K2M, a specialist in the 3D printed production of spinal implants. Following the combination of the companies’ assets, Dr. Murray shared, Stryker has “the largest portfolio of 3D printed cages on the market.”
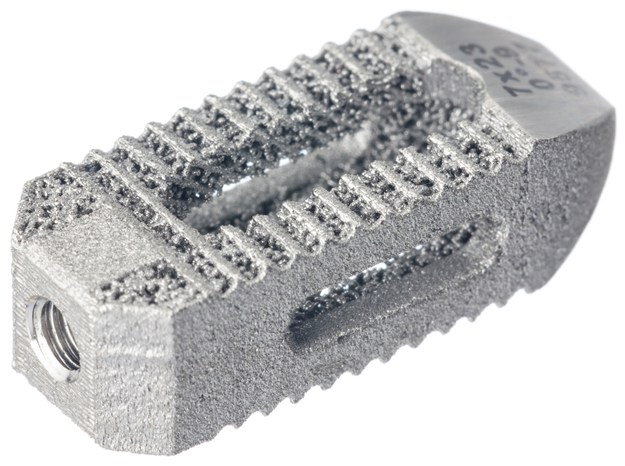
Other notable acquisitions within the 3D printed implant area have included Johnson & Johnson Medical GmbH‘s purchase of German device manufacturer Emerging Implant Technologies (EIT), the developer of Cellular Titanium technology.
The next step for Stryker is to develop a portfolio of patient-specific, 3D printed medical implants, starting with craniomaxillofacial devices. Similarly Johnson & Johnson relative DePuy Synthes‘ has purchased technology for patient-specific implants from Michigan-based Tissue Regeneration Systems.
Certification for 3D medical
Though it may be full-steam ahead for 3D printed medical device development, no conversation in this area is complete without a consideration of certification and regulation.
The FDA of course is the leading authority on the certification of medical devices. At present, the rule is that any 3D printed medical device must acquire 510(k) clearance, therefore proving its similarity to other already tried and tested products on the market.
Manufacturing on Demand
In Wednesday’s 3DTalk however Amy Alexander, Biomedical Engineer at the Anatomic Modeling Lab of the Mayo Clinic in Minnesota clarified that the same classification is not required for those devices made within a hospital. First of all there is no commercial aspect of the device. Objects such as surgical guides and anatomical models also don’t undergo the same intensity of stress as implanted devices.
Each one of the devices made by Alexander and the rest of the lab team is made in close collaboration with the surgeons that require them. At the Mayo Clinic especially they are seeing much more crossover between these roles, “As [surgeons] get more familiar with the lab,” Alexander explains, “they become pseudo-engineers.”
“We don’t see 3D printing as the answer to all of the questions,” she adds, but it has in some cases enabled the team to achieve the Mayo Clinic’s “one-week treatment” goal.
“So the patient arrives on a Monday, they’re seen by their surgical team […] surgery [then] could be as soon as Wednesday. So in our lab, we’re taking imaging that’s required on a Monday, we segment the anatomy, preparing it for 3D print. Printing, post-processing, archiving and delivering the model to the OR [can be completed] by Wednesday morning. That’s an extremely short turnaround.”
What’s next for additive manufacturing?
On the final day of RAPID + TCT the keynote presentation will be on the topic “Shaping New Ways for Smart Automotive Production by Using AM.” It will be delivered by Dominik Rietzel, Dr.-Ing., Head of Additive Manufacturing (Non-Metals) at BMW Group. Emphasizing the local expertise within this area, and highlighting automotive’s growing adoption of 3D printing, many exhibitors have brought demo cars to Detroit.
Lifting the hood on a Ford Mustang racer, Stratasys is presenting a number of 3D printed end use parts that are a product of what it is calling “performance partnerships.” In a special presentation earlier in the week, Mike Lewis, Senior VP of Don Schumacher, also detailed how this company is using Stratasys 3D printers to gain a competitive edge in drag racing.
Formed in January 2019 by NASCAR champion Brad Keselowski, Keselowski Advanced Manufacturing Solutions (KAM) is making it’s RAPID + TCT debut, GE Additive is showcasing the next generation HRE Wheels HRE3D+ set and, Oak Ridge National Laboratory’s BAAM capabilities are nicely highlighted on the Shelby Cobra.
* This article is reprinted from 3D Printing Industry. If you are involved in infringement, please contact us to delete it.
Author: Beau Jackson
Leave A Comment