Online 3D model marketplace PROTIQ has worked with additive manufacturing software specialist trinckle to launch a 3D printing-based orthopaedic footwear customization tool.
Using the firm’s new web application, shoemakers can now upload client foot scans and create bespoke shoe templates that meet their exact specifications. Once ordered, PROTIQ SLS 3D prints the footwear from TPU, before shipping them out in a faster, more streamlined approach than wood-based ‘shoe last’ production currently allows.
“Tailor-made orthopaedic footwear typically takes several weeks to manufacture, particularly because traditional shoe lasts still need to be made from wood,” explained trinckle in a release. “PROTIQ demonstrates how this can be done faster. With the help of additive manufacturing, custom shoe lasts can now be virtually-printed overnight, and are available on the production bench within a few days.”
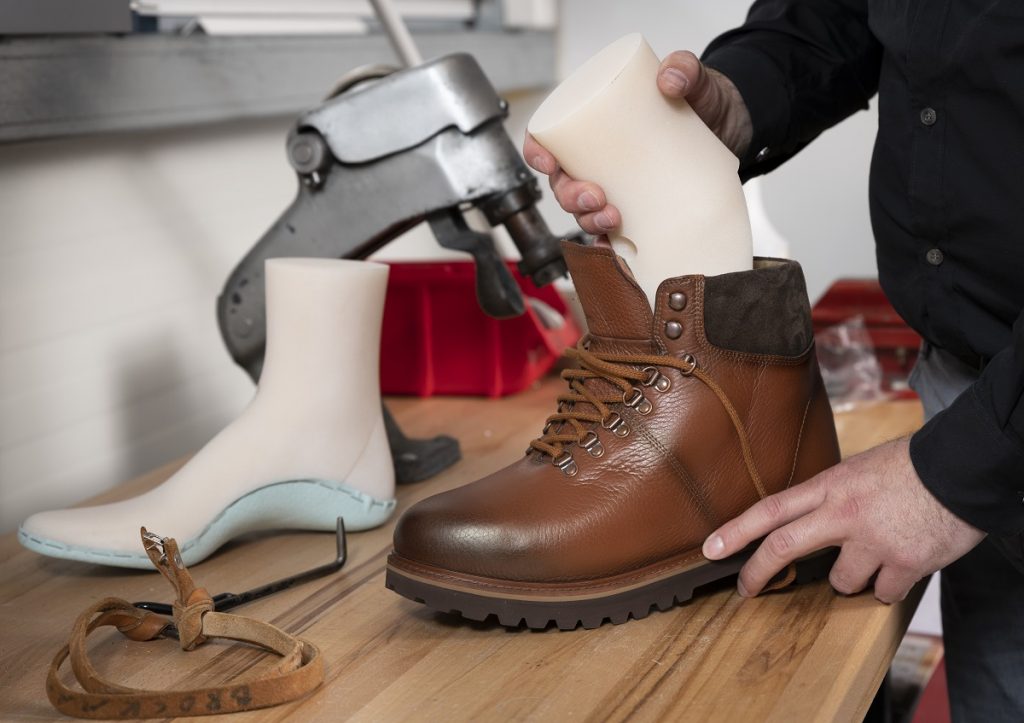
The art of shoe last-making
Essentially, shoe lasts are foot forms used to shape custom footwear, and with orthopaedic models, in particular, precision is key to accommodating the exact needs of each wearer. To produce a perfectly-fitted shoe, aspects such as a client’s heel and instep sizes, as well as their rolling motion when walking need to be factored-in, thus lasts represent a vital element of medical insole production.
At present, shoemakers tend to mill lasts from wood or mold them from foam based on a client’s sole, ball, instep and heel specifications, before sanding them down in a lengthy and costly process. Although ‘blank’ casts are also available, they often need reworking, making the approach similarly long-winded and inefficient.
What’s more, whichever manufacturing method orthopaedic shoemakers choose to adopt, they currently have to wait a few weeks for shoe lasts to arrive before they can even start customizing them. As a result, PROTIQ has now spotted an opportunity to ramp-up the footwear production process, by harnessing the flexibility of 3D printing to deliver custom orthopaedics rapidly and at scale.
Expediting orthopaedic production
To overcome shoemaking’s current limitations, PROTIQ has worked closely with BASF subsidiary Forward AM to qualify the optimal TPU for 3D printing shoe lasts, as compared to conventional beachwood, TPUs have greater flexibility and stress resistance, making them ideal for SLS additive manufacturing foot forms.
Manufacturing on Demand
Additionally, within its new production workflow, PROTIQ leverages its own vacuum thermoformer to pre-qualify 3D printed lasts, in a process that it says is much faster than deploying a test shoe, yields parts with “excellent mechanical properties,” and is ultimately “the most innovative” manufacturing method in orthopaedic footwear.
Once printed, the resulting molds can be tacked or grinded by shoemakers without showing signs of abrasion, and they’re able to keep their shape when being milled, drilled or placed under pressure too. As an added bonus, the firm’s models also feature an ‘easy-grip’ surface, making them lightweight and generally much easier to work with.
Finally, to complement its new 3D printing set-up, PROTIQ has turned to long-term partner trinckle to develop an easy and intuitive means of allowing shoemakers to upload client models. Trinckle, in turn, has built an online portal that enables customers to seamlessly design, customize and order shoe lasts, even allowing them to create a single pair before placing repeated orders if required.
“Our free shoe last configurator allows you to easily upload your foot scans and based on them, shape individual last soles,” reads FORTIQ’s website. “You can then adjust the leg axis, twists, deformations and more. Once you have your 3D model configured exactly to your customer’s needs, all you have to do is order and your lasts are ready to print.”
AM and insole customization
PROTIQ’s web-based approach might well be unique, but high-profile sports brands like Adidas and Under Armour are known to have been 3D printing custom insoles for several years now. In the past, Nike has also experimented with digital personalization in the form of its ‘Nike Fit’ app, which allowed users to measure their feet via 3D scanning.
Similarly, sticking with sport, New Balance has previously worked with Formlabs to launch a new 3D printing platform that’s capable of producing personalized, lightweight shoe components. Referred to as ‘TripleCell,’ the system has since been used to revamp the design of New Balance’s classic 990 Sport and FuelCell Echo sports shoes.
Elsewhere, in more clinical applications, Bayer foot care brand Dr. Scholl’s revealed at CES 2019 that it was working with Wiivv to develop a line of customized 3D printed footwear. Now renamed FitMyFoot, the firm’s technology revolves around a scanning app, which lets users image their feet and create customized medical-grade footwear accordingly.
* This article is reprinted from 3D Printing Industry. If you are involved in infringement, please contact us to delete it.
Author: Paul Hanaphy
Leave A Comment