Guyson International, a North Yorkshire-based industrial finishing equipment manufacturer, has launched its Powder Flush system to clean 3D printed medical implant trabecular structures.
Trabecular structures aid in the interlocking of human bone growth at the end of long bones or in the spinal column. Metal additive manufacturing processes such as SLM and EBM have enabled the customization of these implants. Due to its porous nature, particle residue is often present in the 3D printed implants, hence the need for powder flushing.
“Guyson has become the ‘go-to’ company for post-processing finishing equipment in the 3D Printing marketplace,” said Mark Viner, Managing Director of Guyson International. “This new Powder Flush unit adds to the already extensive portfolio of Guyson products provided for the Additive Manufacturing market.”
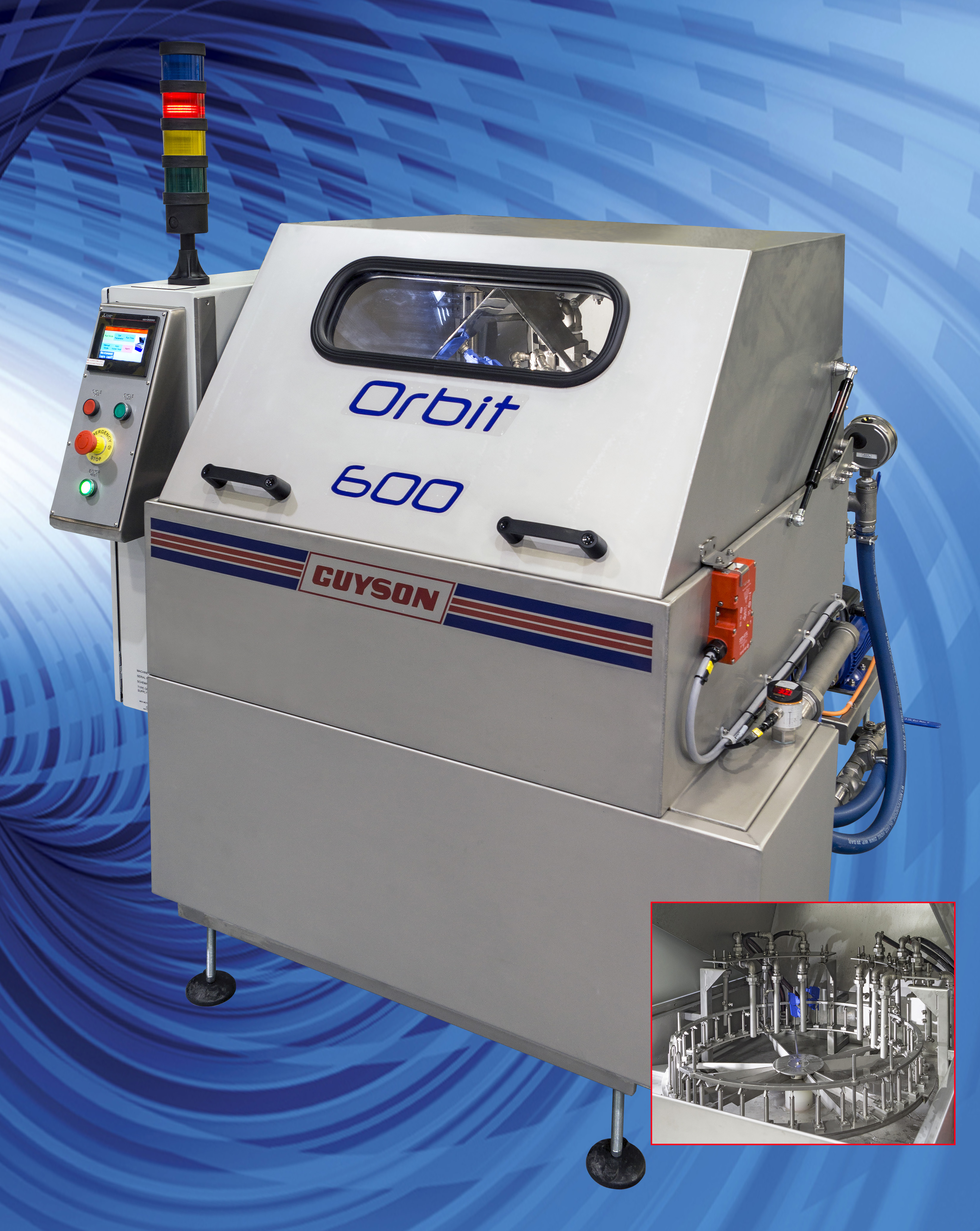
Post-processing 3D printed medical implants
The Powder Flush is based on Guyson International’s Orbit 600 rotary basket spray wash unit. This system is fitted with a 100-liter insulated tank and hot spray flushing for thorough cleaning purposes. It also offers directed jets for powerful component flushing followed by a compressed air-wash.
As the company’s latest additive manufacturing post-processing system, the Powder Flush integrates a PLC/HMI control panel which provides data monitoring and a timed pre-heat function ensuring accurate and repeatable process operation. Following its production, the 3D printed medical implants are individually or batch loaded on non-contaminating fixtures directed towards the flushing jets.
“[This system joins] our Euroblast Ex range of ATEX certified blast cabinets for surface finishing exotic metal AM parts, often used in the aerospace and medical markets,” added Viner.
Manufacturing on Demand
“[Furthermore,] the Guyson PRS (Powder Recovery System), which is an automated post-processing system, specifically for EBM additive builds, uses tried and trusted robotic blasting methodology to reveal components and manage the resultant powder in a highly contained blast system, and our ‘Kerry’ branded range of ultrasonic baths and tanks for 3D printed FDM support removal.”
Guyson and Materials Solutions
Earlier this year, Guyson International, installed four Euroblast blasting machines in the Digital Factory of Materials Solutions, a Siemens business specializing in 3D printing. As an SLS post-processing system, Euroblast is used to removes unsintered particles from 3D printed parts.
“Materials Solutions has been using Guyson blasters since our origin and when it came to upgrade and update it made perfect sense to us to go back to Guyson,” explained Phil Hatherley, General Manager at Materials Solutions. “We have increased size capability plus capacity and working with our team Guyson has provided us with a quality solution for blasting the larger components that our customers are now looking for us to supply.”
* This article is reprinted from 3D Printing Industry. If you are involved in infringement, please contact us to delete it.
Author: Tia Vialva
Leave A Comment