With a well-rounded 3D printing product portfolio comprising production-grade printers, multi-material systems, and medical ceramic 3D printing machines, Lithoz has progressed immensely in recent years, delivering products that have contributed to the advancement of ceramic 3D printing. With its newest product launch—the CeraFab Lab L30—the company is going back to its roots with the aim of filling an important gap in the market. The CeraFab Lab L30 is an entry-level ceramic AM machine intended for researchers and academia, as well as material and applications developers. We say back to its roots because the cost-friendly machine is based on Lithoz’s first industrial system developed over a decade ago, the CeraFab 7500.
The origin story
We spoke to Dr. Johannes Benedikt, Lithoz’s Chief Technology Officer, about the newest addition to the company’s 3D printing offering and how it came to be. “More or less three years ago, we started a new product line: the CeraFab System. This whole series was developed for serial production and we put all the technologies we had into it: including security features and top-quality parts. In the last two years, however, we found that we needed another type of machine, one that would be suited to academia, researchers, material and application developers. In other words, the people who want to 3D print ceramics but do not need to start with production machines. This is where the idea for the CeraFab Lab came from.”
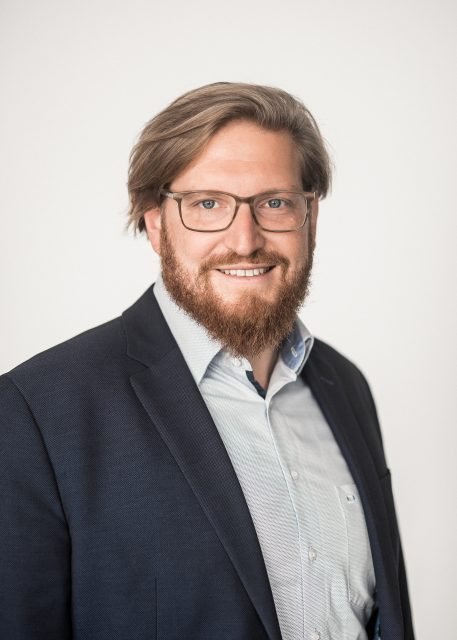
In conceiving the CeraFab Lab, the Lithoz development team went back to its CeraFab 7500. “Created more than a decade ago, the CeraFab 7500 is a compact, easy-to-use printer. It offers a lot of possibilities for manual adjustments. It’s also the system we started our own material development on,” he says. “To mark the company’s 10th anniversary, we decided to go back to the basics and bring this really successful product line back.”
The result is a compact, affordable system that is designed for researchers and developers. “We think it is important to give all the researchers and developers access to ceramic 3D printing,” Dr. Benedikt specifies. “We will launch the new machine this spring.”
Same quality at a lower cost
A crucial thing to note is that despite being at a lower price point, the CeraFab Lab L30 does not compromise on quality. The machine integrates the same optical systems as the production-grade CeraFab System and is compatible with all the same materials. Dr. Benedikt says: “At the end of the day, every customer can achieve the quality they would expect from a Lithoz machine. The idea is to have a machine with which researchers can work not only on materials but also on applications. When the application is developed, it can be easily scaled using the production system because the optical system, parameters and materials are the same.”
So where does the price reduction come from? In large part size. The CeraFab Lab has a small build envelope measuring 76 x 43 x 170 mm. The CeraFab System machines by contrast have larger envelopes of up to 192 × 120 × 320 mm. The CeraFab Lab also cuts back on some automation features present in the production systems.
Manufacturing on Demand
“In the CeraFab System, everything is automatic, including the calibration and an automatic central database for process data,” Dr. Benedikt explains. “It also includes other features necessary for production, such as remote control, a computer vision module, etc. With the CeraFab Lab, we have done our best to reduce this to a minimum. Users have manual control over parameters, which enables them to develop new materials and applications or push the limits of the process.”
A material developer’s dream
One of the key uses of the CeraFab Lab will be material development. The machine is an open platform, meaning that users can print with any of Lithoz’s existing materials as well as any ceramic slurry of their choice. “You can develop your own materials with the CeraFab Lab,” the Lithoz executive tells us. “There are a lot of experts out there and we think they should have the opportunity to work on an open system, using a well-known, high-quality technology to realize their ideas.”
Presently, Lithoz works with many competence centers and companies around the world to develop new ceramic 3D printing materials. The company brings to the table an in-depth knowledge of additive manufacturing technologies and ceramic and photopolymer material bases. Its partners bring to the table an array of specialities, including knowledge of post-processing treatments and applications. “We offer 3D printing technology and related/corresponding softwares and materials,” Dr. Benedikt says. “Our customers bring the product and application know-how. If we get to a point where we can combine these, we can develop an application much more quickly and with a great chance of success.”
Adapting to a remote future
Though Dr. Benedikt and his team had pictured a big worldwide launch for Lithoz’s upcoming system, the pandemic has somewhat curtailed these plans. It has also played a part in the company’s distribution and installation strategy. That is, while the CeraFab Lab will be sold through the company’s established global distribution channels, installation has been adapted to our mostly remote existence.
“The whole installation process should be much easier than on the usual 3D printers,” he says. “We plan to ship the box and provide remote training and installation for our customers. That being said, if a customer asks for an in-person training, we will do our best to make it happen. But the basic operations on the machine should not require our typical on-site training and installation.”
Interestingly, though COVID-19 has caused a slowdown in many sectors, Lithoz has experienced growth over this past year. “At the beginning of last year, a lot of our customers turned to us after supply chains from China were disrupted. Since then, we have had to grow our team, hiring new customer support personnel as well as expanding our production facility”
The imminent launch of the CeraFab Lab is further proof that the company has had a highly productive year. “The first tests and feedback from customers has been really good,” Dr. Benedikt concludes. “So we have really achieved our goal to provide the same quality as our production systems in a more cost-friendly machine. Because at the end of the day in ceramics, it’s all about quality. The development team also had a lot of fun bringing this system to life: we used all our experience from the last decade to develop this new generation.”
* This article is reprinted from 3D Printing Media Network. If you are involved in infringement, please contact us to delete it.
Author: Tess Boissonneault
Leave A Comment