New York-based automated post-printing developer PostProcess Technologies has announced a collaboration with Great Lakes Dental Technologies, one of North America’s largest orthodontic laboratories, to automate the company’s powder removal and surface finishing process for 3D printed dental products.
With most custom dental solutions specifically fitted to an individual’s mouth, traditional mass production manufacturing techniques are inapplicable in the product development process. However, without an automated post-printing solution, Great Lakes struggled to surface finish and remove excess powder with the accuracy necessary to achieve the desired comfort and function for its custom 3D printed dental products.
Using PostProcess’ RADOR Surface Finishing solution, Great Lakes has been able to streamline its workflow by automating its powder removal and surface finishing SLS post-printing processes. Commenting on the advantages of the system, James R. Kunkemoeller, President and CEO of Great Lakes Dental Technologies said, “The RADOR has not only improved our efficiencies but has allowed us to produce a superior product while maintaining our valued workforce.”
“Great Lakes’ forward-thinking mentality has always driven us to look for ways to improve business sustainability, competitiveness, and workforce retention.”
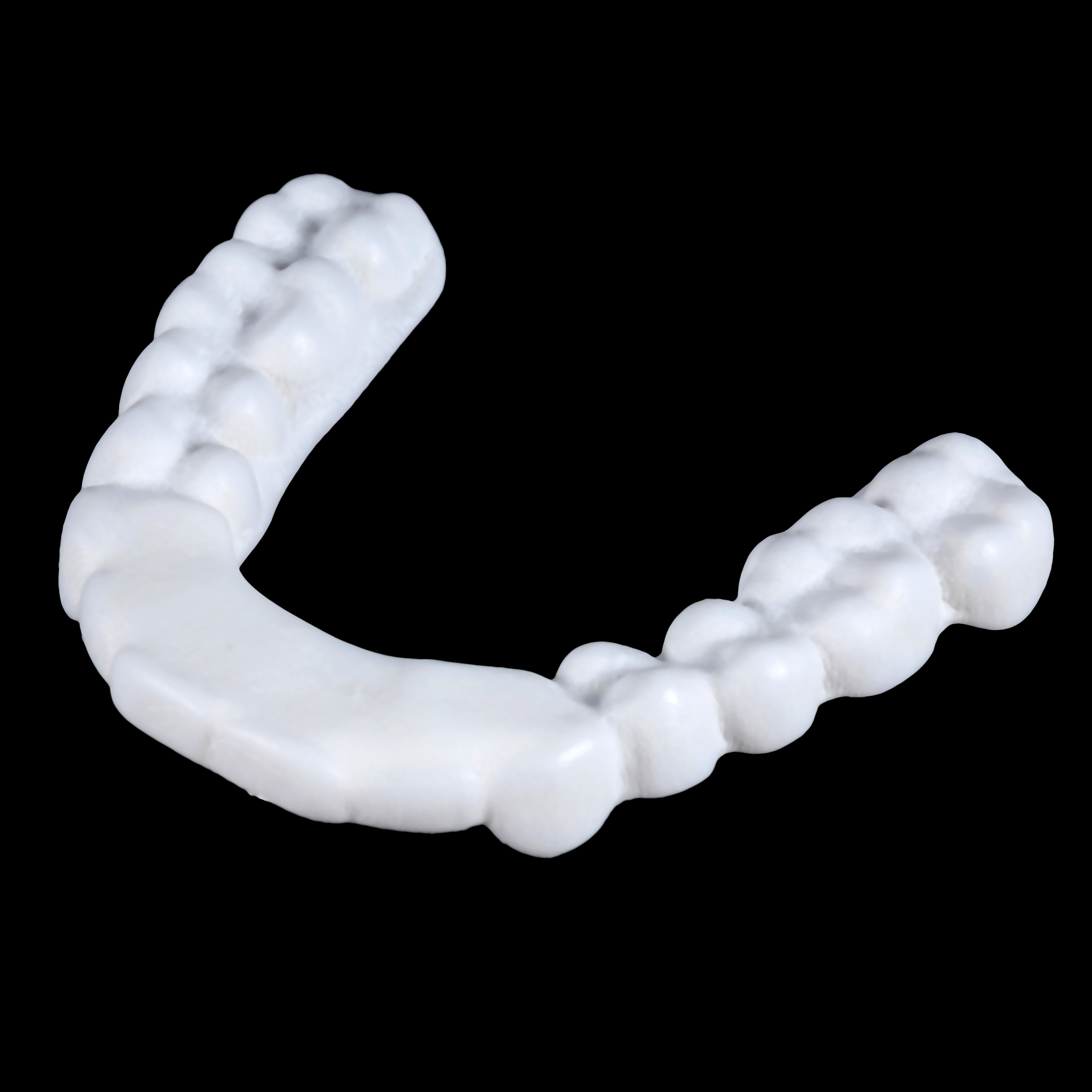
Automating the dental 3D printing workflow
Starting as a small orthodontic laboratory in 1964, Great Lakes now designs, develops, manufactures, and markets more than 4000 products and services for use in the orthodontic, dental, and sleep/airway market.
The company has been a long-time adopter of additive manufacturing, initially using the technology over ten years ago. Great Lakes has invested in PolyJet, DLP, and SLS 3D print technologies in their own facilities, and is also a reseller for Stratasys and 3D Systems dental solutions. Although the firm has successfully integrated additive manufacturing into its workflow, completing the process chain with post-printing solutions has proven difficult.
Since dental appliances are custom-manufactured on a case-by-case basis, no two designs are the same. A dental aligner is personalized for each patient and features numerous intricate crevices that can be difficult to post-print and to remove excess powder from. The accuracy of these appliances is critical to both comfort and function for the patient.
As well as powder removal, it is also imperative that dental aligners have a smooth exterior, achievable using the surface finishing postprocess technique. Having to implement both these methods would require a significant amount of labor without an automated solution.
Manufacturing on Demand
As such, Great Lakes opted to use the PostProcess RADOR Surface Finishing system which automates both the powder removal and surface finishing SLS post-printing processes. Equipped with PostProcess’ patent-pending technology, RADOR utilizes software, hardware, and vibratory technology to dually remove powder from and burnish printed parts via suspended rotational force (SRF) technology. SRF establishes an effective friction force and suspends parts in a circulating motion. This movement is designed to ensure that every area of each part receives equal exposure to the finishing hardware.
“As a fellow early technology adopter hailing from Western New York, our business relationship with Great Lakes Dental has been a natural fit,” commented Nate Harris, Vice President of Sales, North America, PostProcess Technologies. “While dental in additive manufacturing scales into a projected $9 billion industry over the next decade, we look forward to helping more companies enable scalable post-printing for their business with our full-stack solutions.”
3D printing in dental aligner production
Dentistry is a field in which additive manufacturing has proven to be an ideal manufacturing solution. Because a key advantage of 3D printing is its ability to manufacture one-of-a-kind, intricate solutions quickly, it is suited towards the development of retainers, dentures, custom implants, crowns, and more. Without the option of additive manufacturing, most dentistry operations are forced to rely on more labor-intensive subtractive manufacturing methods, like milling machines, for example.
Firms like SmileDirectClub, a Nashville-based teledentistry company, have recognized the potential of 3D printing in the dental sector. The company uses HP MJF technology to produce up to 50,000 unique mouth molds per day. Before SmileDirectClub was Align Technology, which uses 3D printing to produce the Invisalign range of clear aligners.
Voodoo Clear Aligners, a dental manufacturing offshoot of New York-based 3D printing bureau Voodoo Manufacturing, is also planning to manufacture and ship over 20,000 unique orthodontic clear aligners each month in the future.
* This article is reprinted from 3D Printing Industry. If you are involved in infringement, please contact us to delete it.
Author: Anas Essop
Leave A Comment