In 2017, Siemens achieved an industry breakthrough through the first successful commercial installation and the continued safe operation of 3D printed components in nuclear power plants. This is a remarkable achievement due to the strict safety and reliability requirements of the nuclear department, because the components used in nuclear power plants must be strong, reliable, high temperature resistant, and subject to more supervision and quality assurance than any other industry jobs.
3D printing, also known as additive manufacturing, is an innovative technology that simplifies the manufacturing process by converting directly from 3D models to actual parts. Additive manufacturing can reduce costs, improve quality and design flexibility, and eliminate traditional manufacturing constraints.
3D design and printing provide quality and money-saving options, especially for manufacturing spare parts and creating prototypes, which often require huge costs to build new production lines. Changes in 3D printing are only minor changes in programming.
GE Hitachi Nuclear Energy (GEH) is an important pioneer in this field. GEH can irradiate 3D printed parts to test and compare traditional parts over the entire range of conditions. They will use 3D printing to minimize waste and reduce production time by 90%.
3D printing is known for creating scale models and other novelties, as well as more sinister pistols. You may even have a 3D printer at home. The technology was first pioneered in the 1980s and revolutionized the manufacture of almost everything in the last 10 years. Today, we can not only print with plastic and rubber. We can use metal and other materials (such as various high-tech composite materials) for printing.
It is therefore not surprising that it will enter the nuclear industry. The most promising application is in the development of microreactors, which are very small nuclear reactors, usually less than 10 MW, and can be installed on the back of a tractor-trailer.
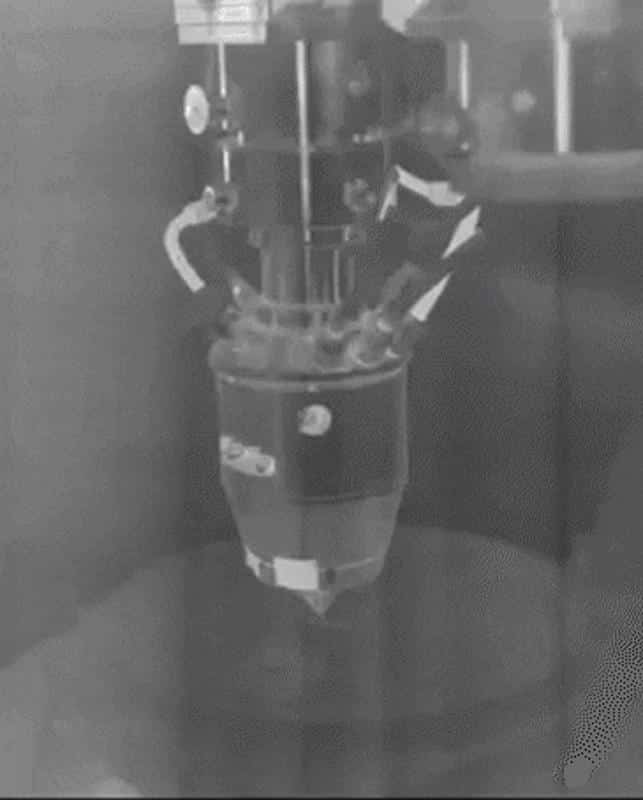
Oak Ridge National Laboratory has collaborated with the US Navy ’s Disruptive Technology Lab to manufacture the first 3D printed submarine hull for the Navy using carbon fiber composite materials (see video above). Its size is the same as the microreactor.
The cost of a traditional submarine is between $ 600,000 and $ 800,000, and the manufacturing time is several months. The price of this 3D printed hull is less than $ 100,000 and it took a few weeks-saving ten times the cost and time. And it is easy to change between printing, so it can save traditional costs on a scale without mass manufacturing.
Although the internal components of the microreactor may be complex, the aerospace industry has less time and lower cost than traditional methods for 3D printing of complex jet engine components. The replacement of discontinued parts is a challenge for nuclear power plants, and 3D printers can be used to manufacture parts.
But by far the coolest thing is to 3D print the core of a nuclear reactor. This is what ORNL researchers are doing. Printed cores will become a leader in the US nuclear industry, thereby reducing the cost and time to build next-generation facilities.
ORNL Director Thomas Zacharia said: “The nuclear industry is still thinking about how we design, build and deploy nuclear energy technology.”
This is not science fiction. 3D printed components have entered nuclear power plants, and advanced test reactors use 3D printing to manufacture test capsules.
Westinghouse Electric Company successfully installed a 3D printed thimble plugging device. The equipment is using nuclear reactors to help lower fuel assemblies to nuclear reactor cores, and the plant’s refueling overhaul was installed at Exelon’s Byron Nuclear Power Station Unit 1 in Illinois this spring.
Ken Petersen, vice president of nuclear fuel for Exelon Generation, said: “Additive manufacturing is an exciting new solution for the nuclear industry. The simplified approach helps meet the industry’s demand for a variety of small-batch, high-critical plant components. We are very happy Westinghouse became a partner in this industry milestone and helped further prove the feasibility of the technology. ”
Westinghouse plans to become the first company to install 3D printed components for nuclear fuel elements in commercial nuclear reactors, thereby reducing prices and accelerating the quantification of materials and 3D printed components.
The company has used 3D printing to make molds, brackets and bearing boxes for electric engines.
Larger components (such as pressure vessels used in small modular reactors) can use advanced methods including 3D printing, powder metallurgy hot isostatic pressing (pressing metal powder into a solid shape), and Electron Beam Welding (at the molecular level welding). These all reduce manufacturing costs and time.
In fact, NEI’s recent report on advanced manufacturing found that the nuclear industry is most interested in 16 methods.
Swedish 3D printing companies Additive Composite and Add North 3D have developed and released a new boron carbide composite filament suitable for radiation shielding applications together with the University of Uppsala. The name of the material is Addbor N25, which consists of boron carbide and copolyamide matrix.
Boron carbide is one of the hardest materials known, so it has been used in many extreme applications, such as tank armor and bulletproof vests. The material also has a high neutron absorption capacity, making it ideal for applications such as nuclear radiation shielding.
Like all other industries, nuclear energy is entering the future through 3D printing, two new processes of new materials and new applications. Seeing a large number of printed microreactors supporting the Martian colony in just a few decades is just the beginning.