Researchers from France and the UK are looking for ways to improve the 3D printing of buildings, and revealed their analysis in the recently published ‘Nailing of Layers: A Promising Way to Reinforce Concrete 3D Printing Structures.’
Concrete extrusion is a source of continuous innovation in the construction industry, providing hope for the concept of 3D printed offices, houses, and entire villages, and adding potential to more affordable housing. Greater affordability, faster production speeds, fewer manpower requirements, and the ability to create composite materials to improve performance are just some of the benefits.
“Recent research on 3D printing has almost all been focused on mix-design, rheological and process-related issues. It has allowed the production of a physically-based background in order to formulate concrete with the required fresh properties, and allowed us to evaluate a time window during which it is possible to deposit a new layer of cement-based material,” stated the researchers.
“Nowadays, some technical solutions have emerged in the development of successful concrete printing, and researchers have started to work on the structural performances of reinforced and unreinforced concrete printed structures.”
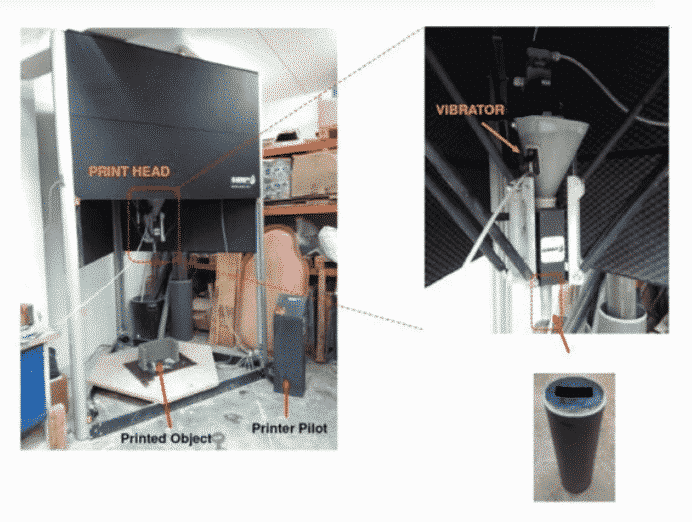
For some structures (including infrastructure such as bridges), additional reinforcement is the only way to comply with design standards. Contemporary solutions may include steel bars or fibers made with cables or the following materials:
- Steel
- Basalt
- Glass
- Bio-based materials
- Polymeric fibers
In this study, scientists conducted experiments on 3D printed nails, and the nails passed through several layers. The overall goal is to provide ductility, tensile strength, and shear strength, while also providing greater strength between the layers.
“This strategy can be easily automated using a robotic placement of the nail which can be a real advantage and beneficial in the context of digital construction,” stated the researchers.
The gradient of the mechanical properties of the nail placement was studied, and the reinforcement effect was evaluated by a three-point bending test (evaluation direction, surface roughness and steel density).
Three-layer samples and ten-layer samples were fabricated with 10 × 25 mm² rectangular cross-section layers of mortar with a screw extrusion system mounted on a WASP 3MT Industrial 4.0 printer.
The bending resistance, post-peak behavior, and durability issues and the possibility of steel corrosion were tested. Starting with permeability, many issues must be considered to avoid corrosion because it must be “the lowest possible” to reduce carbonization and any resulting corrosion. A cover must be used to protect the steel and other materials (such as fly ash or slag) to prevent corrosion of the steel nails. Other solutions include using stainless steel, glass, basalt, or carbon to avoid corrosion.
“It was also demonstrated that reinforcement, by using nails, was able to efficiently strengthen printed samples if the orientation of the nails was correctly chosen and the nails surface was sufficiently rough to ensure a good interface with the mortar,” said the researchers.
“In conclusion, this investigation paved a new path towards fully automated selective steel nail placements as reinforcements during the digital fabrication of concrete in order to strengthen the concrete structure.”