Researchers from the German Kiel University have developed novel 3D printed ‘spiky-joints’ that provide wrist injury patients with a more flexible form of arm support.
Inspired by the natural wing micro-joints of the dragonfly, the spiky-joint features a novel interlocking mechanism that’s designed to cushion the wrist without impairing free movement. When set to its maximum rigidity, the scientists believe their device could be ideal for treating everyday strains and sprains, and preventing common hyperextension injuries in athletes.
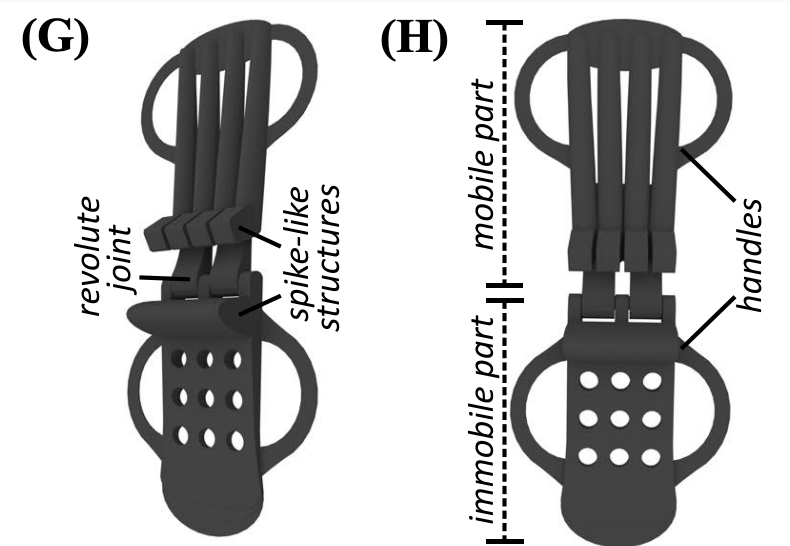
Revolutionizing the wrist splint
Damage sustained to the muscle, bone or joint (also known as musculoskeletal injuries), are as plentiful as they are painful. According to the Kiel researchers, as many as 15% of all U.K and U.S. visits to GPs relate to such strains, sprains and fractures, with the majority resulting from strenuous sporting activity like bodybuilding or weightlifting.
At present, musculoskeletal injuries are often treated with orthodox casts, but these can be heavy, restrictive and extremely bad for the environment. In one study dating back to 2012, researchers found that 670,000 kg of refuse is generated each year from wasted bandaging alone, necessitating the creation of a more eco-friendly solution.
While the increased accessibility of 3D printing has recently yielded more lightweight and recyclable wrist splint designs, they’re often built for rigidity over mobility, limiting the wearer’s movements. To overcome this, the Kiel team have taken inspiration from the joints that control deformation in dragonfly wings, to develop more flexible supports capable of better adapting to applied loads.
The strong yet adaptable spiky-joint
Utilizing a Prusa i3 MK3 3D printer and PLA filament, the scientists have been able to turn their patented design into reality, creating a working wrist splint prototype. The device itself features a mobile part with four interconnected tubular elements, each including spike-like stoppers that allow users to set the desired angle at which it locks into place.
Elsewhere, the 14 × 3 × 2 cm3 wrist support is perforated to improve breathability, and fitted with four handles and velcro straps on its lateral side, making it easy to attach or remove. In order to evaluate their device’s load-bearing capacity, the team subjected it to a series of static bending tests, in which it proved capable of resisting weights up to 30kg.
If constructed out of more resilient alloys, the researchers claim their support could sustain pressures of over 450kg, which is no mean feat given the world weightlifting record currently stands at 477kg. Further testing showed that the device’s ‘spikes’ could also be activated at wrist angles up to 70–80°, demonstrating its efficacy in preventing hyperextension injuries.
Manufacturing on Demand
Although the scientists haven’t yet conducted clinical trials of their novel wrist splints, they’ve already designed a knee and elbow variation, and consider their approach to represent a “marketable technology.” The team also believe their ‘variable mobility’ concept could be well-suited to robotics or engineering applications, potentially yielding morphing load-bearing structures in future.
3D printing optimized arm braces
Using 3D printing, it’s possible to precisely adjust the dimensions and rigidity level of many clinical devices, and the technology is often deployed to fabricate customized supports.
Researchers based at the University of Georgia, for instance, have used a 3D printer to create a personalized arm brace for American football player Sony Michel. The carbon fiber support enabled the running back to return to action, while retaining the ability to feel the ball under his arm during play.
Similarly, clinicians from Zhongda Hospital at Southeast University have 3D printed novel arm support that enabled a patient to regain the use of his left hand. Using 3D scanning and modelling, the medics were ultimately able to fabricate a more customizable brace than would be possible using conventional technologies.
Taking a more scalable approach, the Italian biomedical start-up Exos has begun marketing its new ‘Armor’ range of customizable 3D printed back braces. Debuted at CES 2021, the modular supports are designed to be strong and breathable, while being tailorable to the needs of each individual patient.
The researchers’ findings are detailed in their paper titled “,” which was co-authored by Ali Khaheshi, Stanislav N. Gorb and Hamed Rajabi.
* This article is reprinted from 3D Printing Industry. If you are involved in infringement, please contact us to delete it.
Author: Paul Hanaphy
Leave A Comment