Radiophysicists at the National Research Tomsk State University (TSU) in Russia have successfully 3D printed with tecason, a high performance medical grade plastic with a melting point between 350-400°C.
Reportedly the first to process tecason with 3D printing in the country, the team at TSU has manufactured components for ultrasonic surgical instruments using the material. The medical devices are penned to enter the market in 2020, in Russia and its surrounding countries.
Tecason PPSU plastic
Tecason is a PPSU plastic known for its suitability for common sterilization techniques and cleaning products, agents and disinfectants. Combined with its biocompatibility, this makes tecason PPSU suitable for manufacturing medical devices, as it provides additional safety within hospital environments. Belgian chemical company Solvay also offers a PPSU plastic suitable for medical devices requiring repeated steam sterilization in its Radel line of materials.
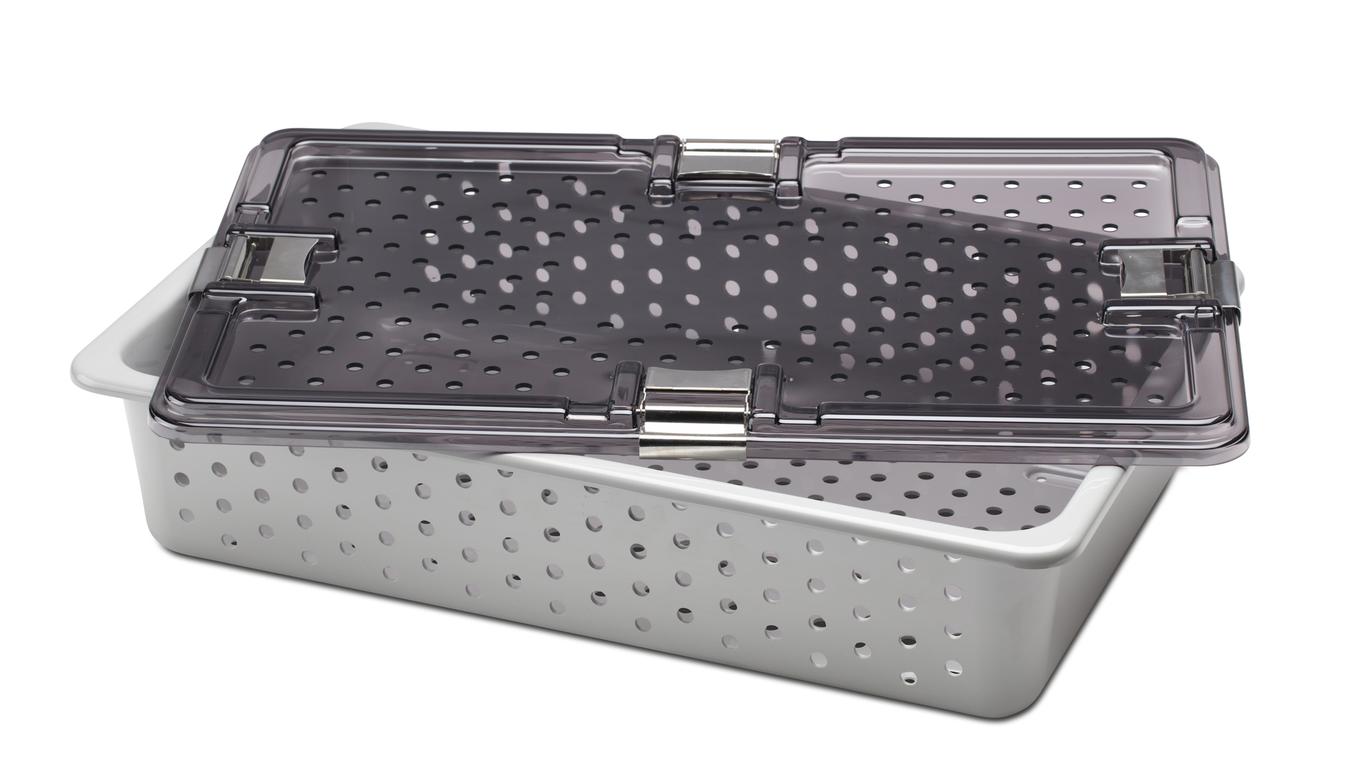
TSU’s project to 3D print parts for ultrasonic surgical instruments is being supervised by TSU Professor Dmitry Sukhanov. The TSU scientists have embarked on the project to produce tecason parts for medical devices using 3D printing as the technology provides increased efficiency, with less material wastage. 100 percent of the material is consumed when processed through 3D printing, whereas 90 percent goes to shavings when manufacturing using milling and turning techniques.
An additional advantage offered by 3D printing is the increased design freedom, allowing the team to manufacture complex shapes required for the surgical instruments. Milling machines, on the other hand, have been unable to realize the complexity of the instruments, according to the scientists.
Ultrasonic 3D printing
Manufacturing on Demand
Professor Sukhanov and his team were able to 3D print the surgical instruments at a temperature of 380°C. In order to carry out the high-temperature 3D printing process, the scientists reconfigured the software and equipped their 3D printer with a high-temperature extruder and a temperature sensor. Thus far, the team has 3D printed a plastic tecason handle for a prototype coagulation and tissue cutting tool.
“Now in Russia, the market for high-temperature printing is not very developed. As a rule, manufacturers work in the range of 200-250°C, and tecason wire is our new pilot project,” explains Marina Klishina, Project Manager at tecason supplier company Elmika.
“Tecason is used in the manufacture of medical devices–it is biocompatible, resistant to cleaning products and repeated sterilization, and it is an electrical insulator, so the technology of high-temperature printing with it should be in demand.”
In 2018, TSU scientists revealed they were developing an ultrasonic 3D printing method involving levitation. Foam plastic particles are suspended in an acoustic ultrasonic wave stream, where they can be controlled and deposited. Like the tecason medical devices, the researchers aim to make the 3D printing technology available by 2020.
* This article is reprinted from 3D Printing Industry. If you are involved in infringement, please contact us to delete it.
Author: Anas Essop
Leave A Comment