Swiss motorsport company Sauber is a historic team in the Formula 1 circuit, where it has been competing since 1993. The intensive implementation of AM at Sauber since the early 2000s is not the only reason why the company is now playing such a relevant role in the AM industry: Sauber Engineering was established to leverage the team’s unique engineering know-how and provide design and production services using Additive Industries’ MetalFAB1 metal 3D printers. Last year this led to the production of over 22,000 metal laser PBF printed parts; and these are just the start.
Over the years, the ongoing challenge of making racing cars faster, lighter and more reliable has forced Sauber to produce parts that simply did not exist. This expertise, and the new AM production methods that go with it, are now available to clients in industries beyond motorsports, for mass automotive and wider industrial applications.
On the occasion of the new C41 Formula 1 car’s official presentation, Sauber Engineering Technology & Innovation Director Christoph Hansen took 3dpbm for a spin around the firm’s state-of-the-art facility.
“We started using AM in the mid-nineties,” Hansen tells us. “Initially we found polymer AM to be a very quick solution to print prototypes for wind tunnel tests. In 2007 we started setting up our plastic additive manufacturing department and 10 years later, in 2017, we invested in metal 3D printing through a partnership with Additive Industries.”
AM represents a way to tackle two competitions at once: the racetrack on one side and the race for car development on the other. The two are closely intertwined because the performance of the car on the racetrack comes from the ongoing aerodynamic development: the more iterations you can do in the wind tunnel, the quicker you develop the car. “In the past, even the most complex shapes were done manually,” Hansen says, adding that the first 3D printed parts were created for the wind tunnel model, which is a 60% model, designed for measurement purposes, it is a measurement tool for the aerodynamicists. However, that first trial led to printing the entire skin of the wind tunnel model and investing in an internal polymer machine park.
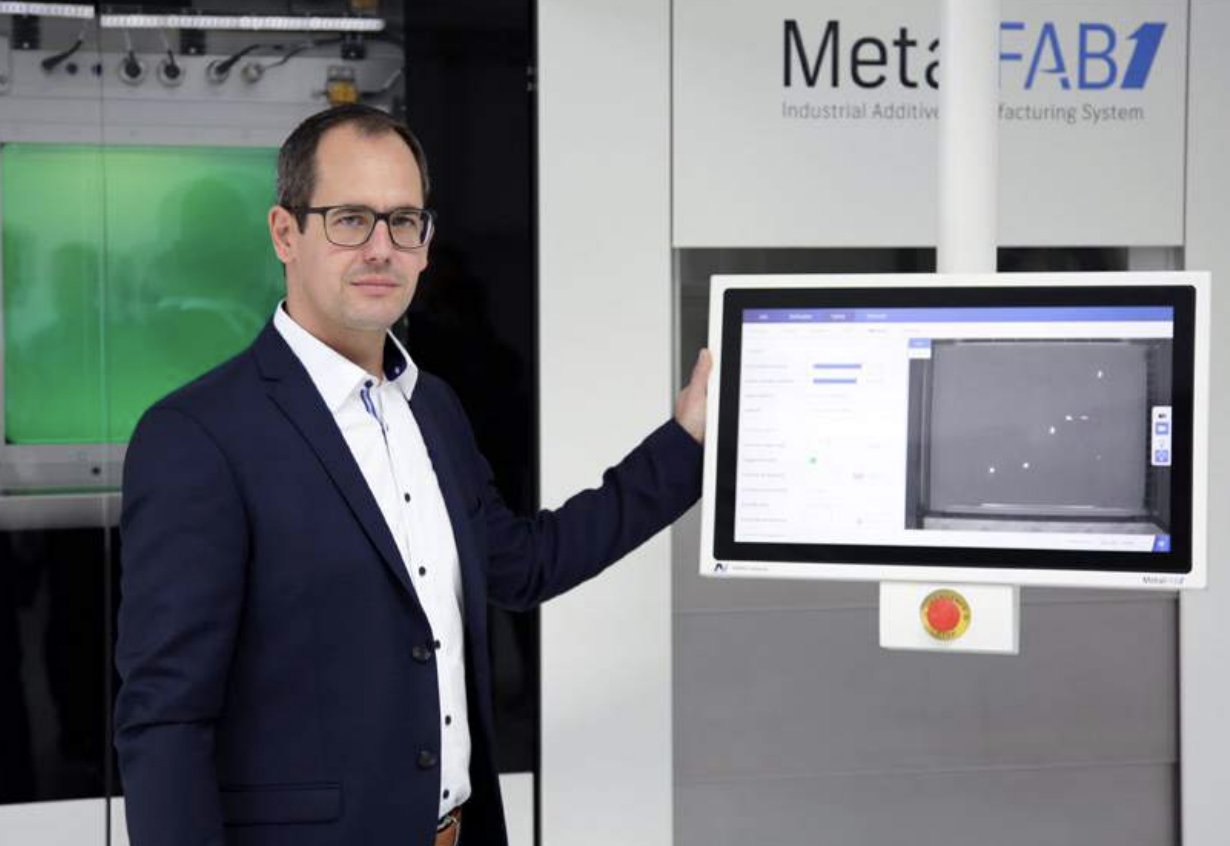
Pedal to the metal
“In 2015 I took over the 3D printing department and it became clear that we needed to implement metal production,” Hansen tells 3dpbm. He first saw Additive Industry’s technology at Formnext and understood its potential specifically for end-use part production. “We were already performing some serial production for customers and produced parts for our racecar using polymer 3D printing technologies. But metals opened an entirely new area of possibilities in terms of mechanical properties,” he explains.
Sauber entered into the collaboration with Additive Industries with the objective of setting up a metal 3D printing competence center within three years. “The initial plan was to get two of these large machines installed within three years,” Hansen says. “We are now entering year four and we already have four machines operating.”
Developing advanced additive manufacturing capabilities has proven to be very beneficial for Sauber. The Sauber Group is a company with three business entities. One, of course, is Sauber Motorsport which operates Alfa Romeo Racing ORLEN. This is the company that is developing the race car and operates the racing team. The second unit is Sauber Aerodynamics Ltd., which is an important player in the field of aerodynamic development, including safety services and wind tunnel tests for the automotive industry.
The third is Sauber Engineering Ltd. This is where the 3D printing is based. In addition to AM production, the company provides engineering services to the broad industry. “We see ourselves as an access point to the technologies that we developed in the last 50 years here at our premises,” Hansen explains, adding that “3D printing was an important element in the kick-off of this spinoff, as it was already a successful business field.”
From start to finish
Sauber Engineering today houses 13 large-format polymer systems, as well as the four MetalFAB1s and a HIP system. “We invest a lot in the quality insurance of the parts, both from a geometrical point of view and of course for in-process quality. Monitoring and tracking of the mechanical properties as well as in the composition of our materials is the key to success. We focus on achieving repeatable part quality,” Hansen says.
The company now provides a holistic service that goes from idea to final product and it does this at the highest levels. “If a company comes to us with an idea,”Hansen continues,”we support them in designing the products and optimizing them for 3D printing. We have the possibilities to produce the first functional prototypes and take care of qualification and industrialization up to the point where the project is scaled up to serial production of several thousand parts per year.”
“We’re active in a broad field of industries. Obviously, automotive is our heritage, but we’re also very deep in the business of prototyping for pre-series and design studies, especially in plastic 3D printing. In metal printing, there are huge opportunities for end-use applications in various industries, such as packaging or even space and aviation,” Hansen explains.
Manufacturing on Demand
In order to be able to provide these services and truly move into mass production of advanced—end even less advanced products—Hansen’s team came to the realization that they needed to achieve true repeatability and quality assurance on metal AM. For this reason, the facility has been ISO 9001 certified and has also been audited and certified by TÜV SÜD for the DIN SPEC 17071. This shows to customers that production is real.
Fast pit stop
Sauber is producing parts for all types of industries, in both metal and plastic, including parts for Alfa Romeo and for companies around the globe. Still, Formula 1 can be the most challenging of tests of AM’s true capabilities: “It’s very critical. When we bring a metal printed part to a race car, it is often a crucial part that needs to endure severe fatigue,” Hansen explains.
“In order to compete, you need first to finish the race so you have to build a reliable car. In the monocoque, for example, you must make sure that a part can last through the whole season. So, one aspect is reliability. The other thing is that there is always a human inside the car, and you do not want to risk the life of the driver just because you use a technology that you do not understand. On our cars, the roll hoop, as well as some crash parts, are 3D printed, using high-strength aluminum. Also, chassis inserts, such as the engine mounts, are printed in titanium.”
These titanium inserts are bonded into the back face of the monocoque and they’re acting as fixing points for the entire powertrain. The powertrain is composed of the engine and gearbox and acts as the structural part which holds the rear axle and the rear wing. These are parts that need to be extremely stiff and precise and undergo the demanding NDT and QA tests.
At the same time, Hansen confirms that additive has brought incredible advantages to the F1 team in terms of development. These include the ability to produce extremely complex parts that can fit into the intricately optimized structure of the F1 car, as well as the ability to build hollow, ultra-light-weight parts with the shortest lead times.
High-speed partners
Sauber is not the only F1 team to use metal AM for car part production. However, as a Switzerland-based firm, it was key to bring these production capabilities in-house, in order to avoid importation-related slowdowns. And this proved beneficial in terms of establishing the Sauber Engineering arm, which is now experiencing high-speed growth.
The Additive Industries machines are equipped with AlSi10Mg alloy, along with Ti64GD23 titanium and Scalmalloy. In general, the material price is not an issue, because so much less material is used compared to subtractive and traditional manufacturing methods. Titanium is often the material of choice. Hansen agrees that material prices may become more of an issue when production batches increase in size. “I expect that material prices will decrease when the metal AM production method is fully industrialized,”he says,”however, the market for metal materials is more open than plastics and more alloys are being constantly developed to improve performance while reducing costs. The fact that the metal powder can be completely recycled and reused makes it more cost-efficient than solid material blocks of titanium.”
This level of expertise in metal AM has few comparisons around the world and Hansen credits Additive Industries for being the ideal partner. “We needed a partner which could help to address our specific issues and needs,” Hansen explains. “Working with too large a company can become very complex. With AI we found a great management team, from the owners to the CEO, who listened to our requirements and implemented a business model that worked well for both of us. In addition,their closed-powder-loop technology is uniquely tailored to our needs and it was one of the first machines on the market with four independent full field lasers. You also have to consider that the cost of labor in Switzerland is extremely high, so the high degree of automation of the MetalFAB1 systems was very important for us.”
Today there are 35 people working at Sauber Engineering. About one-third are working within engineering services or in operations. The other two-thirds are working in production. Now the goal is to significantly expand serial production capabilities as well as the level of automation. “We now have to go even further into the technology,” Hansen confirms. “To this end, we have installed the HIP system and a five-axis CNC machine to finish parts and we are investigating specific laser parameters for each customer’s application: our focus in terms of business, outside of F1, is serial production. We do still have a lot of work to do, especially in terms of educating and convincing the customer to fully embrace the benefits of laser PBF.”
AM always starts off as an apparently more expensive solution. Then, Sauber engineers start to convert the part or assemblies into a specific design for AM (Design for Production). They look at how to make the part more durable and reliable. They design the integrated system to be lighter and more efficient, which means it can be more productive. “It has to start with the part’s design, as the first prototypes are already showing all the way into serial production,”Hansen says. “t this point, the clients start to see the true benefits of 3D printing.”
As the pandemic takes its course, and F1 prepares for a new season with many unknowns, Sauber Engineering can count on AM to widen its horizons and realize the vision of a new type of F1-powered AM factory of the future.
* This article is reprinted from 3D Printing Media Network. If you are involved in infringement, please contact us to delete it.
Author: Davide Sher
Leave A Comment