3D printed prosthetic manufacturer Protosthetics has launched what it claims is the field’s first full-service, in-house 3D printing program for use in orthotics and prosthetics (O&P) practices.
Called Galileo, the plug-and-play system is designed to help O&P practices overcome many of the barriers that have so far deterred them from making the leap to 3D printing.
“Galileo was built from the ground up to solve these issues that O&P practices have with moving the 3D printing,” said Darren Jacoby, CEO of Protosthetics. “Our sole focus is on how to make the digital world easy to use for clinicians so that practices can realize the speed efficiency, and savings that 3D printing in clinic can provide, enabling clinicians to focus more deeply on patient care.”
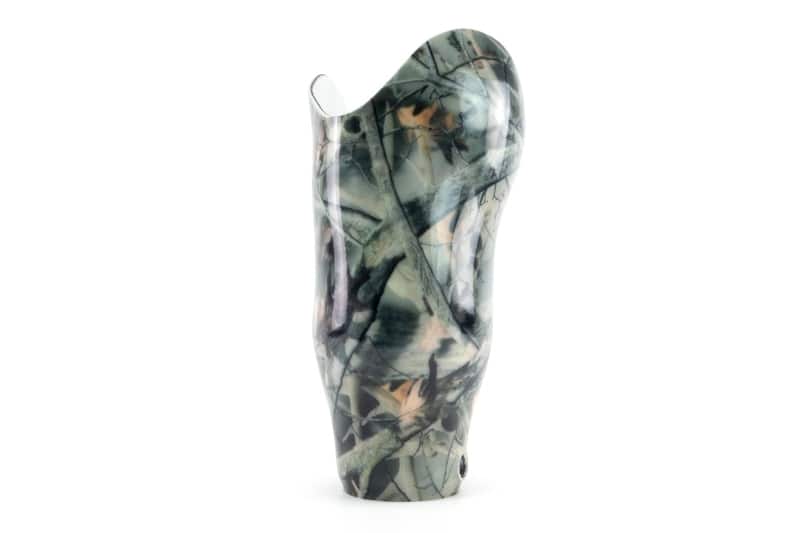
Galileo in-house 3D printing
Founded out of a university engineering project to design a 3D printed myoelectric arm, Protosthetics was the first central fabrication facility in the US to be based solely on 3D printing. Since its establishment in 2016, the firm’s central fabrication business has sought to bring 3D printed products to O&P practices to enable them to provide better patient care.
After years of customer requests for the benefits of 3D printing in-clinic to be realized, Protosthetics has launched its Galileo program, a first-of-its-kind fully managed 3D printing program designed exclusively for O&P.
In particular, the Galileo system aims to overcome the high up-front capital investments associated with 3D printing that have so far deterred practices from transitioning to the technology, while also addressing a lack of familiarity with 3D modeling software. The plug-and-play system also removes the complexity of managing multiple prints and printers for practices.
Rather than an initial upfront investment, practices can pay a flat monthly fee for partaking in the Galileo program and will receive an on-site remotely-managed 3D printer. Practices can upload 3D scans with modification requests to the system which the Galileo Product Engineering Team can prepare and then send to the printer in the clinic.
The Galileo program offers practices uncapped printing, customer support and on-site training, alongside a full warranty and repair program.
According to Protosthetics, the Galileo program can enable clinics to achieve more than 80 percent savings on each 3D printed product, and realize shorter turnaround times.
Manufacturing on Demand
“The mindset of creating 3D printing as a service for O&P practices is truly innovative,” said Aaron Sorenson, CPO and CEO of Restorative Health Services Group, one of Protosthetics’ customers. “We’re excited by how positively the Galileo program is impacting our patient care process.
“The interactive Galileo system connects our clinicians to experts in 3D printing who help us make successful sockets happen in real-time, improving turnaround, reducing costs, and allowing our fabrication team to deliver our higher-end products more efficiently.”
3D printing prosthetics
The flexibility offered by additive manufacturing has continued to drive the accessibility of prosthetic body parts in recent years. The technology has been leveraged to produce a wide array of prosthetics faster and at lower costs than traditionally manufactured alternatives, including pediatric finger and elbow implants, low-cost upper-limb sockets, and even prosthetic testicles.
In November, a London man became the first in the world to receive a 3D printed prosthetic eye in a trial which, if successful, has the potential to substantially reduce waiting lists.
More recently, non-profit 3D Sierra Leone was nominated for an award by the World Health Organization (WHO) for its work in 3D printing prosthetics for the West African nation’s amputees, while scientists at the University of Bristol have developed an artificial fingertip that allows amputees to ‘feel’ objects through prosthetic limbs.
* This article is reprinted from 3D Printing Industry. If you are involved in infringement, please contact us to delete it.
Author: Hayley Everett
Leave A Comment