An M1 Metal AM System from Dutch company MX3D is going to be installed at the Additive Manufacturing Campus of BMW Group in Munich, Germany. With the M1 Metal AM System, BMW Group has acquired one of the most advanced setup the market has to offer with respect to Robotic Wire Arc Additive Manufacturing (WAAM). This will allows the company’s engineers to explore the potential of this highly flexible and productive method of metal additive manufacturing.
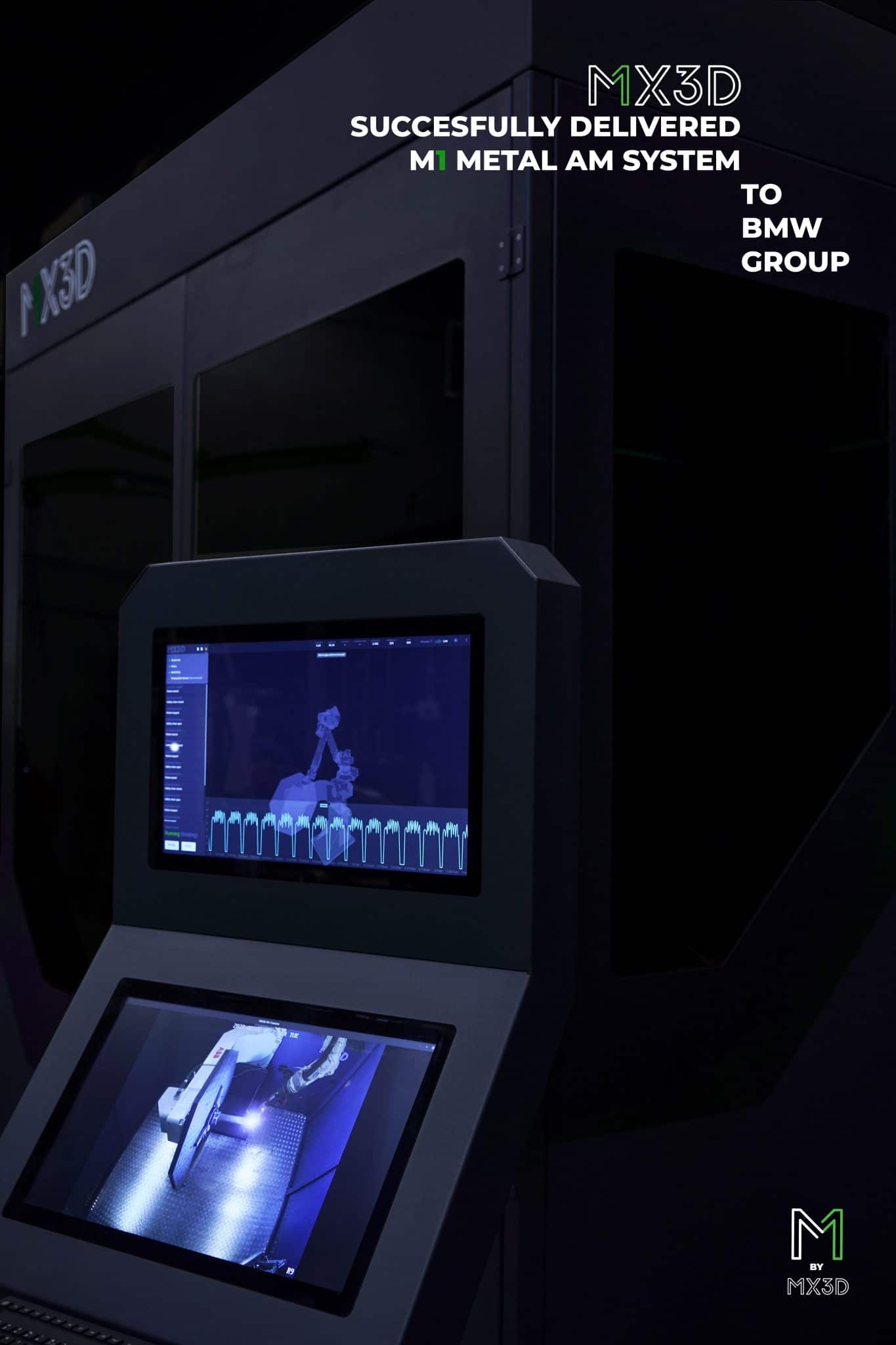
“The BMW Group’s M1 acquisition shows that the founding mission of MX3D – to scale up and industrialize 3D metal printing, in order to make it available to high impact industries – is becoming a reality. Exciting!” Commented Gijs van der Velden, CEO, MX3D.
Manufacturing on Demand
While BMW Group’s AM Campus is going to primarily conduct research on the system, it is very significant that the M1 systems is now going to be implemented in the automotive segment, as it is one of the very first public cases of WAAM technology adoption by a large automotive manufacturer. MX3D previously targeted high-visibility experimental projects, such as the very first and unique metal pedestrian bridge installed in Amsterdam, and subsequently found relevant business opportunities in the maritime segment, where larger parts are more common and unit production numbers are usually much lower.
WAAM technology does have potential for adoption in the production of automotive chassis components however the examples seen up to this day have been limited to experimental and conceptual projects. Another possible use in the automotive segment is, of course, for manufacturing of near net shape metal tools and dies for metal casting.
The MX3D M1 Metal AM System offers a turnkey WAAM solution to start printing large-scale metal components with every weldable alloy. This setup integrates MetalXL, MX3D’s dedicated WAAM solution providing users the full printing workflow from design to print in one go, including advanced process control, monitoring and analytics. MX3D delivers the M1 Metal AM System and MetalXL solution worldwide, adapting the system to each customer’s manufacturing needs.
* This article is reprinted from 3D Printing Media Network. If you are involved in infringement, please contact us to delete it.
Author: Davide Sher
Leave A Comment