Scientists from London’s Institute of Cancer Research (ICR) and the Royal Marsden Hospital have used 3D printed tungsten disks within a gamma camera for higher resolution medical imaging.
Gamma cameras are used to conduct functional scans of the brain, thyroid, lungs, liver, gallbladder, kidneys and skeleton. This medical imaging technique captures traces of radiation emitted by injected pharmaceuticals within cancer patients.
The 3D printed tungsten disks have been used to replace the lead components found in such devices. As detailed in the study published in , the tungsten parts performed better for eliminating unwanted radiation, creating a clear final image.
“Gamma ray radiation is very powerful so you need heavy shielding to produce a clear image,” explained Dr. Jonathan Gear, Clinical Scientist in the Joint Department of Physics at the ICR and The Royal Marsden, and lead author of the study.
“Most gamma-ray cameras use thick lead, but denser materials like tungsten could be as effective while letting more useful radiation pass through to produce higher quality images.”
3D printing tungsten
Found in the earthly mineral wolframite, tungsten is an inorganic, non-natural, rare metal compound. It is extremely dense and maintains the highest melting point of all metals, that is 3422 °C. With its beneficial material properties, including high tensile strength and high corrosion resistance, its use in additive manufacturing continues to be explored.
Manufacturing on Demand
The 3D printed tungsten shields, known as collimators, integrated into gamma cameras by the ICR team were produced by Wolfmet a brand of M&I Materials, a Manchester-based specialist of industrial materials. Wolfmet created the shields using an EOS M280 3D printer using Selective Laser Melting (SLM).
A honeycomb structure of holes was used in these components to allow the adequate amount of radiation through to create an image while blocking unwanted radiation so the image is sharp. Dr. Gear added, “Our research shows that 3D printed tungsten could be used in gamma cameras, offering greater flexibility in the sorts of designs that could be used in the future.”
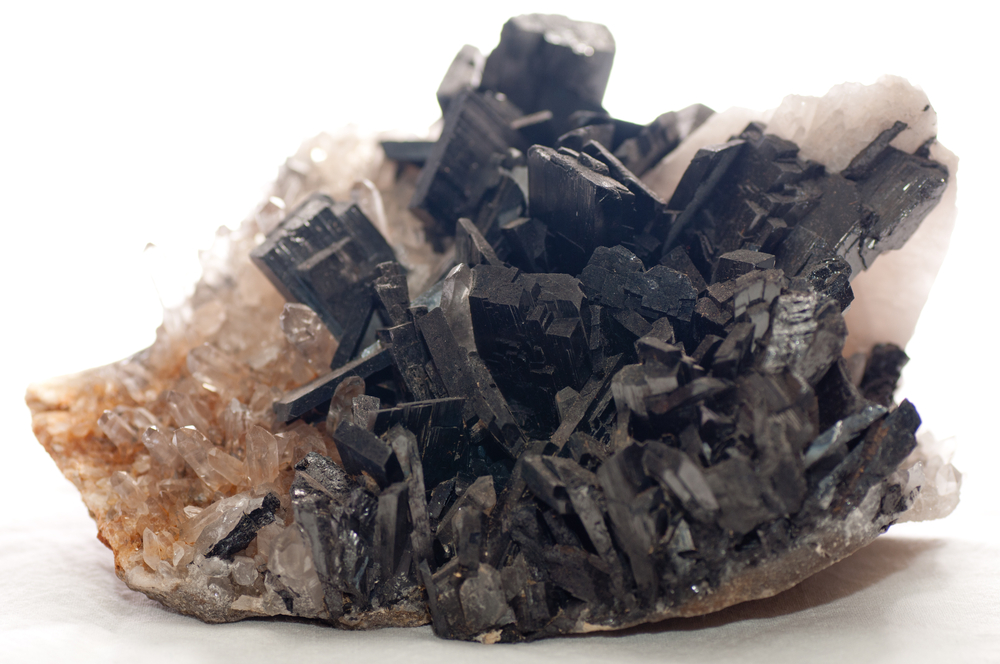
The 3D printed tungsten shields were 20% thicker than standard lead gamma camera collimators. The measured attenuation of a gamma beam using such shields was also seen to be lower than the value determined from the National Institute of Standards and Technology (NIST).
With a reduction in the strength of gamma radiation, the IRC researchers have concluded that tungsten collimators are feasible and superior to its lead alternative. Also with the use of additive manufacturing, the collimator can have a bespoke collimator design within gamma cameras.
“” is co-authored by Jonathan I. Gear, Jan Taprogge, Owen White and Glenn D. Flux.
* This article is reprinted from 3D Printing Industry. If you are involved in infringement, please contact us to delete it.
Author: Tia Vialva
Leave A Comment