During a recent online webinar, Lamborghini’s Edoardo Trabace, Procurement Lead at Automobili Lamborghini, Jacopo Bardocci, R&D Lead for Additive Manufacturing at Automobili Lamborghini, Gabriele Grezzana, R&D Engineer at Automobili Lamborghini, and Norik Elchibegian, Director of Enterprise Partnerships at Carbon, discussed the importance of reducing time to market and the power of internal partnerships to push forward innovation and make better parts faster.
The procurement team at Lamborghini identified Carbon’s Digital Light Synthesis as a valid method to digitally manufacture vehicle components. In 2019, the R&D team at Lamborghini redesigned a variety of parts to produce lightweight, durable, end-use components with EPX 82 material including a textured fuel cap and an air duct clip for the Lamborghini Super SUV, the Urus.
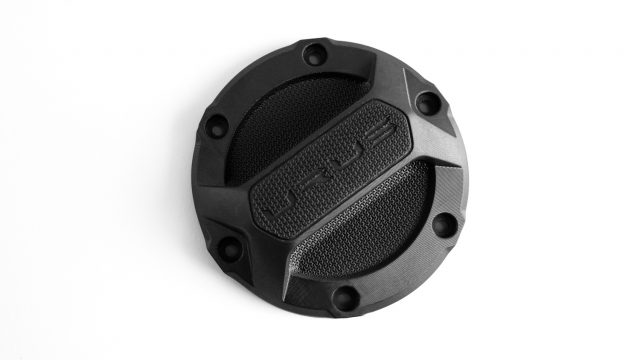
After seeing the success of the initial parts produced and the advantages of digital production, the procurement and R&D teams partnered together once again and made the business case for the expansion of their 3D printing capability. The Sián FKP 37, Lamborghini’s first hybrid production car, now features digitally manufactured central and lateral dashboard air vents.
In total, 20,000 series parts were 3D printed by Lamborghini in 2020, of which 5,000 were Urus fuel caps. This part presented some of the biggest challenges, as it is in direct contact with the customer and thus needs to provide an ideal experience in line with Lamborghini’s luxury and quality level. The part was highly iterated in just a matter of days through 3D printing in order to obtain the ideal shape and texture.
Manufacturing on Demand
For the Sian FKP 37, Lamborghini’s top-of-the-line hybrid model, only 60 air vent units were made (only 60 units of the car were produced). In this case, it took only two weeks to go from the initial idea to the final part installed in the car. Finally, the new Huracan STO now features a unique 3D printed bracket to hold carbon fiber parts in place. Another unique 3D printed final part 3D printed for the Huracan STO is a special key used to open the front bonnet. This is a part that is given to the client, along with the car key.
For the future, Lamborghini plans to produce parts internally and also evaluate and standardize the viability of each 3D printing process for every part that could potentially be serially 3D printed. The idea is to use the production cell of each technology as a validator and decide if it makes sense to scale.
You can find the latest information and market data on all the key technologies and stakeholders in the automotive additive manufacturing segment in 3dpbm‘s (free to view online or download) AMFocus2021 Automotive eBook.
* This article is reprinted from 3D Printing Media Network. If you are involved in infringement, please contact us to delete it.
Author: Davide Sher
Leave A Comment