South Korean pharmaceutical company HK inno.N has announced plans to use artificial 3D printed skin to test new autoimmune and skin disorder drugs.
Working with 3D bioprinting firm T&R Biofab, HK inno.N plans to fabricate a series of tissues with precisely-tailored characteristics. Leveraging the 3D printed flesh, the companies will conduct in-depth research into the effectiveness of different skin disease medications. If the evaluations are successful, the additive tissues could be utilized as a future replacement for animal testing in the medical and cosmetics industries.
“We will not only use artificial skin to verify the efficacy of medicines for skin diseases, but we will also conduct active research between the two companies so that it can be applied to research on health functional foods and cosmetics materials,” said Koh Dong-hyun, Head of the HK inno.N Research Institute, speaking to the Korean IT Times.
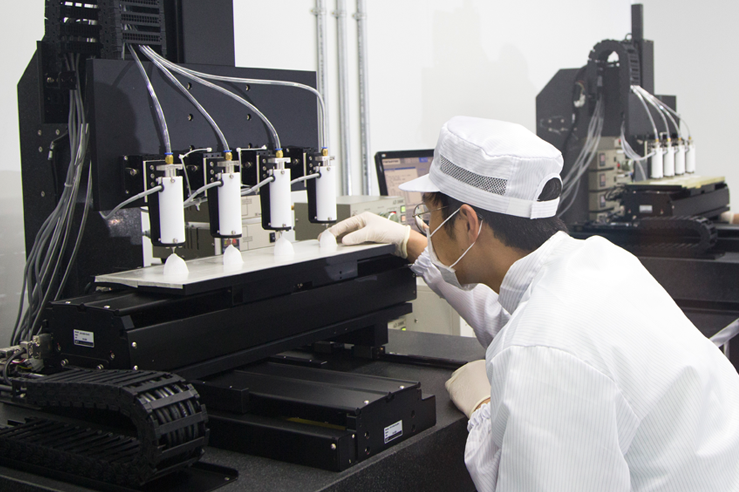
T&R Biofab’s 3D bioprinting technology
Based in the Korean city of Seoul, T&R Biofab was founded in 2013 by a team from Pohang University of Science and Technology (POSTECH). Leveraging their joint-expertise, the researchers acquired the patents for their 3D bioprinting technology from the university and launched a venture firm to commercialize their additive creations.
Seven years on, the company now conducts wide-reaching tissue regeneration research and designs medical devices for transplantation with applications in orthopedics, plastic surgery, and dentistry. T&R is also developing its patented deCelluid bio-ink, which reportedly enables the creation of extracellular membranes (ECMs) and the bioprinting of tissue-specific skin, liver, bone, or cartilage tissues.
In April 2019, T&R Biofab patented its 3D bioprinting technology for creating artificial skin. The firm’s additive manufacturing technique involves fabricating both the dermal and epidermal layers of skin cells using a porous 3D structure. Later that year, T&R advanced its methodology further, developing a new multi-nozzle bioprinting system, allowing it to create complex cell structures in a shorter amount of time.
As T&R’s technology has progressed, the pharmaceutical firm has entered into a number of partnerships with the aim of expanding its applications. Working with fellow biotechnology business SCM Life Science, T&R is researching and developing a range of 3D printed cell patch products, including new formulations for cell therapy.
More recently in May 2020, the company was selected by the South Korean Ministry of Health and Warfare to lead a stem cell and regenerative medicine commercialization project. The program, with a reported budget of 825 million South Korean won, is studying the responses of stem cell-derived human heart cells when exposed to experimental drugs. Now, having signed a deal with HK Inno. N, T&R Biofab will deploy its bioprinting expertise to test the effects of skin disease medication as well.
The deal between HK Inno. N and T&R Biofab
In order to begin the research project immediately, HK Inno. N, formerly known as CJ Healthcare, signed a Memorandum of Understanding (MoU) with T&R Biofab on August 25 2020. The agreement sets out a joint R&D program based around the “evaluation of drugs and functional materials using 3D bioprinting artificial skin.”
During the joint-study, HK Inno.N plans to deploy T&R Biofab’s 3D bioprinting technology to fabricate structures that function in a similar way to actual skin. T&R’s flesh-based models reportedly make it possible to measure skin elasticity, aging index, and protein expression amongst other features. 3D printing also allows the fabricated skin to be customized in a way that meets HK inno.N’s precise needs and enables the firm to find more efficient ways of testing the experimental drugs.
Manufacturing on Demand
Overall, by deploying T&R’s bioprinting expertise, HK Inno. N is aiming to develop new skin therapy treatments for patients suffering from autoimmune diseases. According to Yoon Won-soo, CEO of T&R Biofab, the companies’ cooperation could expand further into research involving health-functional foods and cosmetics materials.
“This collaboration with HK Inno.N will be a meaningful step toward full commercialization of our 3D printed skin and related drug screening technologies,” said Yoon Won-soo in a statement. “We will complete innovative products that can be effectively used in industrial sites such as cosmetics and new drug development.”
Continuing research into 3D bioprinted tissues
Developing optimized bio-inks for 3D printing tissue scaffolds is one of the hottest research topics in additive manufacturing right now, with numerous researchers developing their own formulations.
Engineers from New Jersey-based Rutgers University have designed a new customizable bio-ink for 3D printing scaffolds. Consisting of hyaluronic acid and polyethylene glycol, the gel can be tailored once mixed with other inks, to fabricate a range of human tissues.
Researchers from the South African University of Witwatersrand, assessed the safety and efficiency of existing 3D printed bio-inks. The scientists found that the development of a new type of bio-ink was required, in order to enable the larger-scale adoption of multicellular bioprinting.
A research team from ETH Zurich have created a Universal Nanocarrier Ink (UNI) platform that could enable the production of new biofunctional inks. By incorporating polymers into their UNI formulation, the Zurich team was able to fabricate a number of stabilized scaffolds with enhanced strength via secondary cross-linking.
* This article is reprinted from 3D Printing Industry. If you are involved in infringement, please contact us to delete it.
Author: Paul Hanaphy
Leave A Comment