Chinese medical 3D printing provider Huaxiang Group has been granted landmark clearance from the country’s National Medical Products Administration (NMPA) for a novel 3D printed spinal implant.
Produced using Farsoon’s Selective Laser Melting (SLM) technology, the firm’s porous fusion cages are the first orthopedic grafts of their kind to gain the highest level of Chinese state approval. 3D printing the bone-like parts allows them to be tailored to the needs of each patient, and their certification could now allow medics to better treat illnesses such as spinal degeneration, fractures, and deformities.
“This is a groundbreaking day for metal 3D printing in the Chinese medical market.” said Li Xinghua, Head of Marketing at Huaxiang. “I’m grateful for joining such a strong team and industry AM leader Farsoon for this journey. We are very proud to contribute our efforts to future patient-tailored spinal implant surgeries with the application of SLM.”
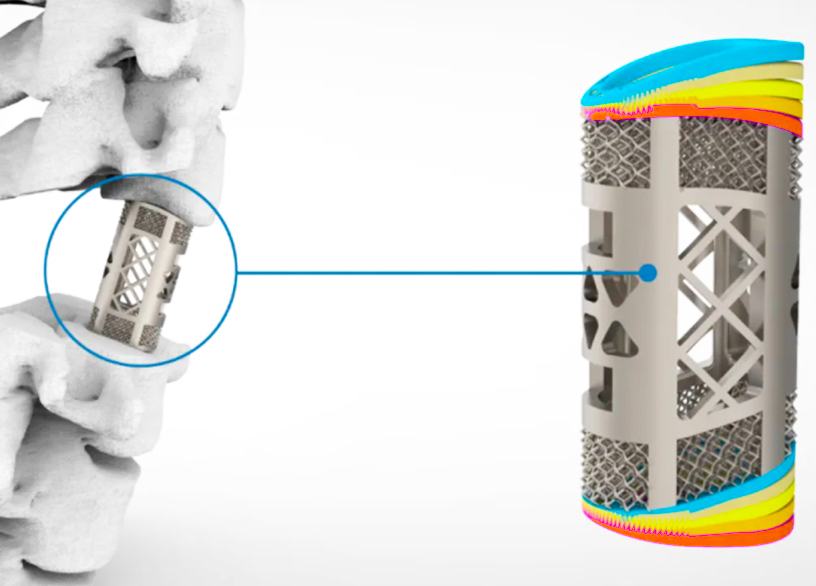
Huaxiang’s medical portfolio
As a private Chinese firm, precise details about Huaxiang’s business ambitions are relatively sparse. From what we know, the company was founded in 2014 and has a supply chain that covers material R&D, 3D printing, software and post-processing, allowing it to create clinical parts for China-based doctors and hospitals to order.
In its relatively short time as a bureau, Huaxiang has opted to partner with the industry’s more established firms to create novel medical devices. For instance, at the height of the pandemic, the company worked with Levhoss and Farsoon to develop open-source safety goggles, and produced thousands of them for the Red Cross Society of China.
Since then, Huaxiang has continued to work with Farsoon, optimizing its FS3300PA polymer for medical applications, including surgical planning and 3D printing operational tools. In its most recent project, the company has now used a Farsoon system to optimize its spinal implants, and allow them to gain a milestone clinical approval from the NMPA.
In China, clinical devices are classified using a similar model to that of the U.S, in which products are rated from class I (lowest risk) to class III (highest risk). Until now, the NMPA hadn’t approved any LPBF 3D printed implants for class III applications, but having certified Huaxiang’s graft, China’s market could now be opened to a new range of additive manufactured medical products.
An optimized bone-like implant
The Huaxiang Group has been working with a surgical team based at a University of South China hospital to develop its implant for some time. Led by Dr Wang Wenjun, the medics have steadily iterated 30 different aspects of the graft’s design, including its mechanical properties and biocompatibility, before recently reaching their final product.
Having conducted 108 different patient trials, the porous device was eventually recognized by the ‘3D Printing Technology Application of Personalized Implant Device’ project. The program, consisting of China’s leading research institutes and additive experts, identified the implant’s market potential, giving it the credibility needed to gain NMPA approval.
Manufacturing on Demand
The device itself features a unique latticed surface, similar to that seen in the trabecular bone, and its pore size, porosity and elasticity can all be customized by changing the print settings of Farsoon’s printer. In doing so, medics can potentially reduce the stress on the implant, promote bone growth, increase its long-term stability, and ultimately mold the graft into a patient-specific anatomical match.
Adopting Farsoon’s SLM technology has also allowed Huaxiang to reduce the device’s lead times, going from waiting months on-end, to producing them on-demand. In future, Farsoon anticipates that its 3D printers will have further applications in this area, and now intends to showcase the implants at TCT Asia, with a view to attracting new clinical clientele.
The global additive implant industry
While titanium spinal implants maybe just taking off in China, there’s already an established market for such devices elsewhere in Europe and North America.
Medical device manufacturer Nexxt Spine, for instance, has been using GE Additive’s Concept Laser 3D printers for the last two years to produce its MATRIXX porous titanium implants. The devices feature a unique ‘cellular scaffolding,’ that’s specifically designed to accelerate the body’s natural healing process.
The U.S-based FDA has also been quicker to approve additive implants, regularly certifying devices such as Pensylvanian firm Centinel Spine’s 3D printed bone grafts. The vertebrae-stabilizing implants, which received 510(k) clearance in 2018, are designed to be X-ray transparent, making them easier to see during surgery.
Elsewhere, dedicated firms like 4WEB Medical have built-up large spinal portfolios, and it recently added a new Stand-Alone Anterior Spine Truss System to its range. The device features a novel locking system, which prevents it from moving during procedures, and provides surgeons with greater operational confidence.
.
* This article is reprinted from 3D Printing Industry. If you are involved in infringement, please contact us to delete it.
Author: Paul Hanaphy
Leave A Comment