Industrial 3D printer manufacturer Desktop Metal’s healthcare subsidiary Desktop Health has expanded its dental technology portfolio to offer binder jet 3D printing capabilities to dental laboratories.
Launching with chrome cobalt for use in dental applications, the company’s Shop System is now available for preorder by dental labs for the production of custom bridges, crowns, partial dentures, and surgical guides.
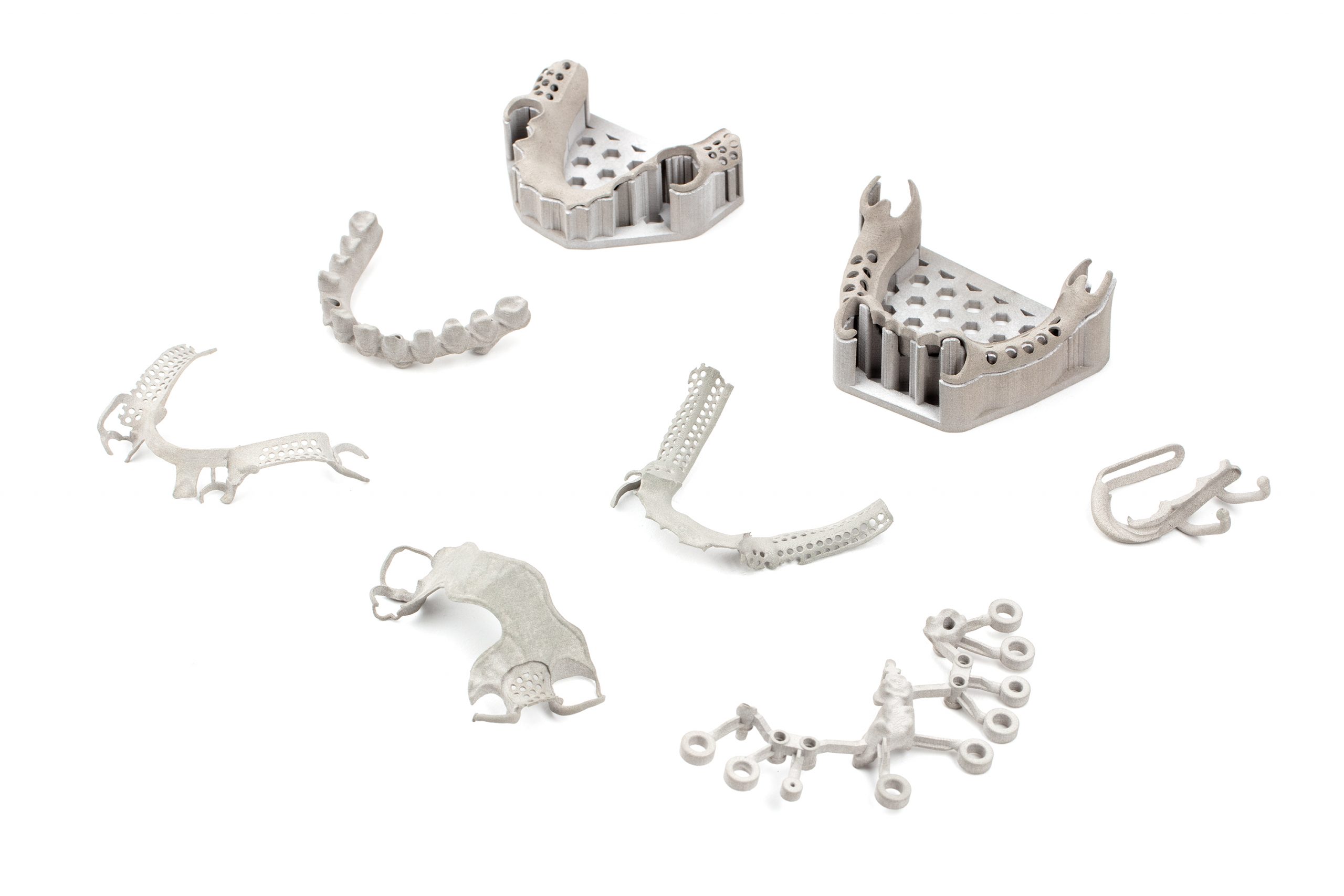
“We are excited to introduce the Shop System and chrome cobalt for binder jetting to the dental community, expanding our suite of best-in-class 3D printing solutions from photopolymers to metals,” said Michael Jafar, President and CEO of Desktop Health. “We are uniquely positioned by offering dental labs not only a leading photopolymer platform, but also a turnkey solution to produce metal appliances and surgical guides with superior surface finish in higher production volumes compared to laser-based 3D printing systems.”
Desktop Health’s increasing capabilities
Desktop Health was launched in March 2021 with a specific focus on the development of 3D printed healthcare products. The business addresses the needs of dental and medical clients thanks to the technologies of its parent firm, particularly those which it has recently acquired.
Since Desktop Metal’s $300 million acquisition of EnvisionTEC, the company has a ready-made means of accessing the growing 3D printed dental, jewelry, and biofabrication markets.
The firm also recently gained FDA 510(k) clearance for 3D printing dental prosthetics with its Flexcera Base resin, and last month bought the rights to PhonoGraft, a 3D bioprinting technology with the potential to regenerate the aural tissues of patients with hearing loss.
Now, through making its binder jetting technology with chrome cobalt accessible to dental labs, it appears the business is continuing to ramp up its activities in this area.
The Shop System’s capabilities for dental applications
First unveiled in 2019, the Shop System began being produced in volume and shipped to customers around the globe towards the end of last year. The metal binder jetting system was designed for the production of serial batches of complex, end-use metal parts quicker and cheaper than can be delivered by conventional manufacturing techniques.
The system’s capabilities have now been extended to dental labs in order to provide mass customization opportunities for dental applications, while eliminating the labor costs of machine programming required for CNC milling, a typical manufacturing process for producing metal dental components. As such, the Shop System is reportedly capable of printing up to 32 partial dentures in less than four hours in comparison to the “nearest competitive system”, which produces up to 10 partial dentures in around nine and a half hours.
Manufacturing on Demand
Metal parts printed on the platform are also fully supported in the powder bed and feature hand-removable sintering setters, in order to significantly reduce labor time and costs of post-processing parts printed on laser-based systems. Coupled with the machine’s high throughput capabilities, the reduced post-processing requirements could potentially drive down part costs for custom dental applications to as low as one third of the cost of similar parts produced on laser-based printing systems.
“3D printing of metal parts for dentistry can finally see an efficient solution with binder jet technology from Desktop Health,” said Christopher M. Silvoy, Diplomate of the International Congress of Oral Implantologists (ICOI). “The Shop System allows a simple and safe process for producing accurate appliances with an extremely well integrated system and workflow. With a large build volume and fast build times, the system provides an opportunity to eliminate outsourcing, increase quality of outcome, and potentially change dentistry.”
Binder jetting dental appliances
Desktop Health claims its Shop System has all the software, hardware, and materials a dental lab needs to begin producing dental appliances via binder jetting. The system’s easy-to-use software interface enables parts to be produced at the push of a button, while its engineered powders and default processing parameters are optimized to ensure part quality and repeatability.
The machine features variable build sizes of up to 16 liters and a high-speed single pass print carriage that enables the production of metal parts up to 10 times faster than legacy 3D printing technologies. This benefit will aid dental technicians in amplifying their existing throughput with up to hundreds of customized parts per day.
The system will also enable dental technicians to print dense, complex parts with incredibly fine detail and surface finish “right out of the furnace”. The single pass printhead features 1600 native DPI to deliver 400 percent higher resolution than legacy binder jetting systems. Meanwhile, a 5x nozzle redundancy on the printhead enables greater reliable print quality.
Desktop Health’s Shop System is now available to dental labs. Chrome cobalt has been qualified for the system and will become commercially available pending FDA clearance. 3D printed and polished removable partial denture framework. Photo via Desktop Health.
* This article is reprinted from 3D Printing Industry. If you are involved in infringement, please contact us to delete it.
Author: Hayley Everett
Leave A Comment