Imagine you are on the battlefield-the supply line of the combat unit is under attack, and the threat of being cut is looming.
Enter 3D printing technology-fortunately, you have deployed files of 3D models, some printers and a lot of powdered materials. Potentially, you can now 3D print your own repair parts on demand.
Experts say that the latter can free front-line troops from logistical challenges and make them more mobile in the rapid and comprehensive operations envisaged for future wars, and can greatly save costs.
This is why Wichita State University in Kansas separates Army Black Hawk helicopters one by one. The head of the Aviation and Missile Command told Breaking Defense that they are carefully scanning each component to create a detailed three-dimensional model that can be used for 3D printing.
AMCOM Chief Major General Todd Royar explained: “We are currently disassembling the UH-60 Lima machine.” “[For each] component, they are scanning it and 3D modeling it And put them into CAD [computer-aided design] files…we will start to retrieve them in a few months.”
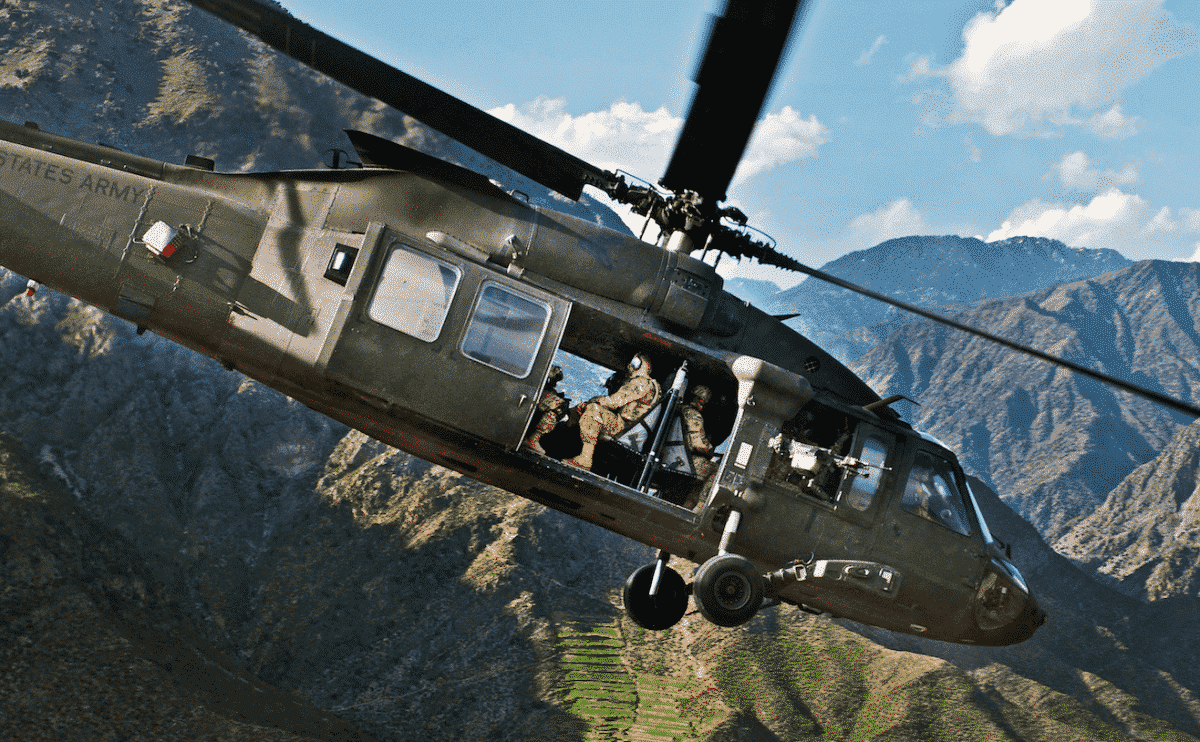
How many different components does the “Black Hawk” UH-60L model have?
Royar said: “We expect to probably get about 20,000 structural parts from it.” According to Breaking Defense, “we will study it and evaluate each product” to see if it can be safely and economically replaced with a 3D printed version.
Many industries have benefited from 3D printing, including the aerospace industry, and aircraft now have 3D printed parts all over the fuselage. Several air forces have followed suit, and corresponding army units are now doing the same for combat vehicles.
However, although the 3D printer is simple enough for school children to use, if you want to print a part that will stagnate in battle or flight, you can’t just stare at the original part and guess the size, “Broken Defense” reported.
Now, companies that use modern digital design technology will certainly make 3D models of their new parts, and usually share these models with the government.
For example, TACOM has data files for new infantry squad vehicles and plans to 3D print certain parts as a proof of concept, according to Breaking Defense. However, there are no digital models for a large number of older parts, some of which date back decades.
To create a model that does not exist, you need to use a dedicated scanner-some are handheld, some are mounted on a robotic arm-to map each part to three dimensions.
TACOM Commander Brigadier General Darren Warner explained that this is only the first step in a complex process. General Tacom is responsible for managing the Army’s new Advanced Manufacturing Center of Excellence at Iwashima Arsenal.
According to the Breaking Defense report, you must research and analyze parts to identify which parts are suitable for 3D printing, because not all parts are suitable.
For example, some components may be subjected to too much pressure, so that it is better to use traditional “subtractive” manufacturing methods to process from a single solid metal block, rather than additive manufacturing, which stacks objects layer by layer.
They may also need to be made of special materials that a 3D printer cannot handle or undergo special treatment. Or they may be too large to produce a usable printer.
Other parts may be possible, not just an engineering one, breaking the Ministry of Defense report so there is an analysis of economic factors-printing but cheap, making the old-fashioned way.
Once the appropriate parts are determined, it is necessary to prove that the 3D printed version is safe and reliable. The generals stated at a press conference that this is one of the most demanding and time-consuming parts of the process, especially for aircraft that must meet Army and FAA flight safety standards.
“Once you have a 3D model, it’s relatively easy to print things,” said Royar, the Army’s airworthiness certification agency, “but it’s difficult to make sure it meets the eligibility criteria.”
As for cost savings, “Popular Mechanic” reported that the US Air Force will save millions of dollars, and pilots can use simple tools invented by serving pilots to avoid the tedious work of crawling in the fuel tank.
The pressurized leak detection cup can reduce the number of hours required to detect fuel tank leaks by as much as 75%, saving more than one million dollars per year for this service. Most importantly, the new tool is 3D printed, and the production cost is only $15.
The US Air Force, which has an aging Cold War aircraft fleet, is particularly vulnerable.
According to Wired, the average lifespan of Air Force aircraft is 23 years. Every quarter, the military department sees that 10,000 parts requests have not been met, even though it is willing to pay high fees to replace parts that once cost a few cents-try to provide $10,000 for the C-17 Globemaster III toilet seat.
Talk about flushing the money on the toilet. By the way, the price of a 3D printed toilet seat cover is $300.
The US Air Force has also 3D printed the first metal parts of its jet engine.
According to “Popular Mechanics”, the replacement parts are made for the engine that powers the B-52 Stratofortress bomber. It will keep the aircraft in flight until the new engine is installed on the aging jet in the late 2020s. .