A research team from the US Department of Energy’s Argonne National Laboratory has successfully scaled up the recycling of an important medical isotope using 3D printed parts. The new additively manufactured parts make the laboratory’s original recycling process – invented in 2015 – faster, more reliable and less costly, enabling the method to potentially be used on an industrial scale.
Molybdenum-99
Radiologists use molybdenum-99 (Mo-99) to detect and diagnose heart disease, bone decay and various rare cancers. Enriched molybdenum, which is crucial for the production of Mo-99, typically costs about $1000 per gram to procure. Mo-99 manufacturers, until now, have been unable to cost-effectively recycle enriched molybdenum on a large scale. The Argonne team expects their novel 3D printed apparatus to increase the efficiency of the recycling process, allowing producers to yield more Mo-99 from their expensive enriched molybdenum reserves.
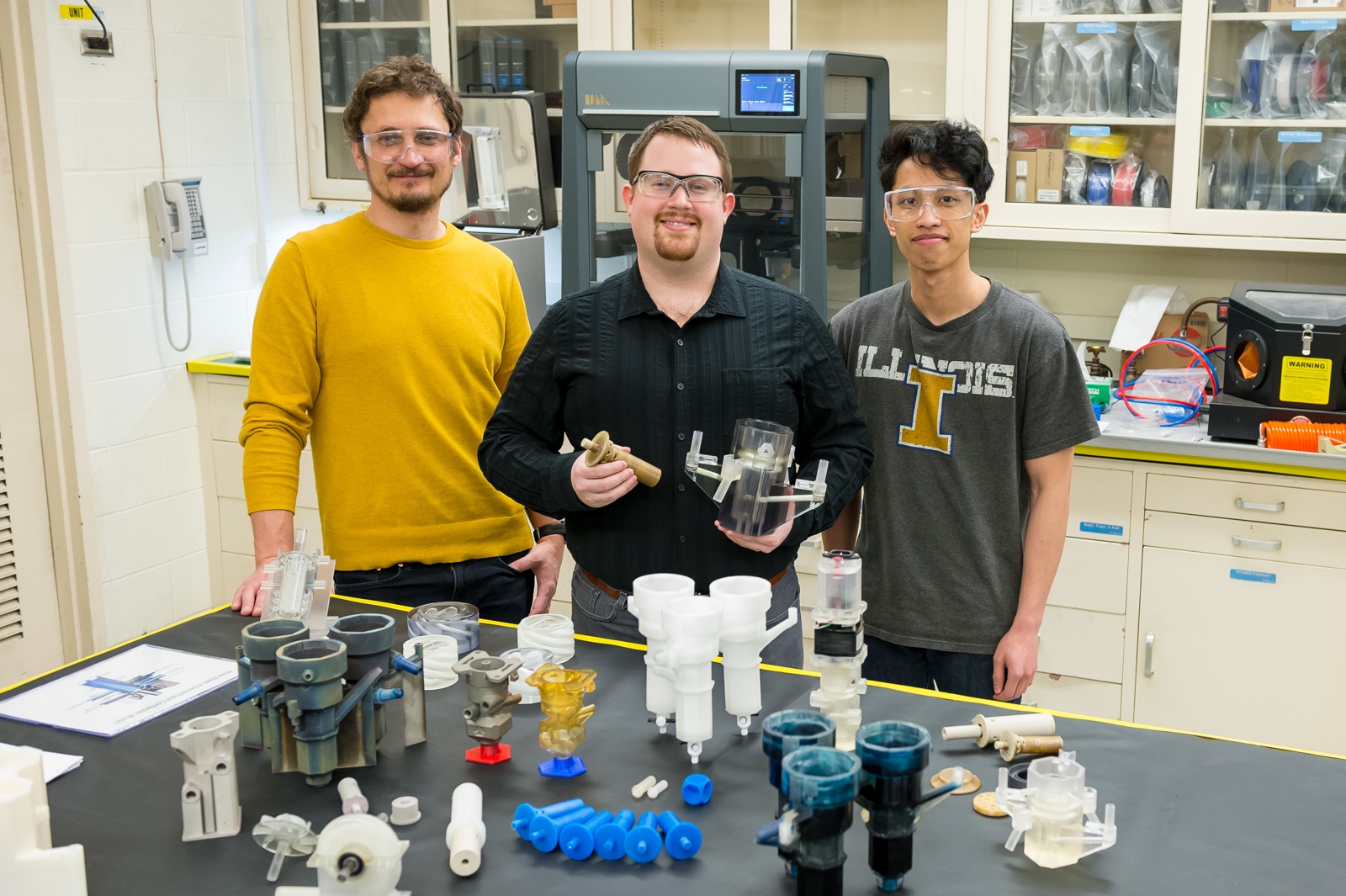
Using 3D printing to recycle enriched molybdenum
The project was led by Mo-99 program manager Peter Tkac, whose team first discovered the recycling of enriched molybdenum. In the original process, the team turned the used enriched molybdenum, along with a cocktail of chemicals, into an acidic solution. The enriched molybdenum was then purified in multiple stages using funnels and test tubes – a process that proved tedious.
Tkac, in a press release, stated: “Our original method would have been very difficult to automate.”
A whole year later, Tkac began working with Peter Kozak, a fellow scientist at Argonne National Laboratory, and others to automate the original process. The funnels and test tubes used to contain and transfer the corrosive chemicals used in the process were replaced with 3D printed acrylic contactors. The research team claimed that it was these contactors that made the recycling process faster and more cost-efficient.
“We printed each contactor as one piece with streamlined features and fewer external connections,” explained Kozak. “This allows us to push the liquid through the system as quickly and reliably as possible.”
While the new apparatus effectively separated the enriched molybdenum from contaminants such as potassium, the team found the 3D printed acrylic corroding after 15 hours of operation due to the low pH hydrochloric acid.
Manufacturing on Demand
Kozak adds, “Our experiment was successful, but if you want to move into full production, you need a material that will survive a lot longer than that.”
The move to PEEK efficiency
The research team eventually decided to use polyether ether ketone (PEEK), a durable polymer known for its chemical resistance. Upon trialing 3D printed PEEK contactors, however, the team found the material to shrink significantly during the fabrication process, resulting in warping. To counteract this, the Argonne scientists altered the printer’s fan speeds and temperatures, and eventually successfully 3D printed PEEK contactors that were stronger and more flexible than the original acrylic parts. The end result was a quicker and more cost-effective enriched molybdenum recycling system with the capability to withstand harsh chemical conditions for extended periods of time.
The findings of the project are detailed in a paper titled ‘’, in the paper titled ‘Demonstration of the MOEX Process Using Additive-Manufacturing-Fabricated Annular Centrifugal Contactors’, in the Journal of Solvent Extraction and Ion Exchange. . It is co-authored by Peter Kozak, Peter Tkac, Kent Wardle, Alex Brown & George Vandegrift.
PEEK has been the focus of many medical devices in the past due to its desirable mechanical and chemical properties. FossiLabs, a US-based medical 3D printing start-up, has previously produced 3D printed bone-like scaffolding structures using a porous PEEK material. The bone-like structures are designed to be used within long-term implantable medical devices.
Elsewhere, in Shanghai, a medical device manufacturing firm, has designed and fabricated a PEEK exoskeleton called BioNEEK that provides support for a range of knee problems. The knee brace features a damper designed to absorb shocks that would otherwise be exerted directly on the knee joint.
* This article is reprinted from 3D Printing Industry. If you are involved in infringement, please contact us to delete it.
Author: Kubi Sertoglu
Leave A Comment