For many of the 422 million people around the world living with diabetes, glucose monitoring is a necessary, and uncomfortable, daily chore requiring a painful pinprick to test the blood. Newer technologies, like the FreeStyle Libre, offer continuous monitoring, but the system still requires that a 5mm rigid metallic needle be driven into the skin. While not as bothersome as the fingertip lance, it’s still uncomfortable for the patient. Aiming to develop a solution that’s more comfortable for the user, the AIT – Austrian Institute of Technology – partnered with DirectSens and In-Vision to launch the NUMBAT research project. NUMBAT aims at leveraging high-resolution DLP 3D printing to create an array of polymeric microneedles for minimally invasive—and less painful—continuous glucose monitoring (CGM).
The success of the NUMBAT proof-of-concept opens the door for the development of personalized microneedle arrays and even shows promise for other applications, including intradermal drug delivery.
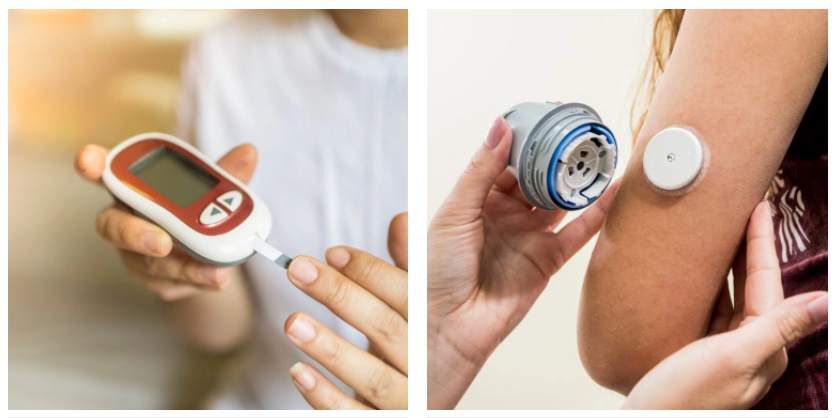
A more comfortable approach to continuous glucose monitoring
Based on previous research literature, the AIT team understood that the microneedle solution they envisioned would require three components: the microneedles themselves, metallization to enable the definition of the electrodes for the electrochemical measurements, and a biofunctionalization layer—a surface modification enabling the glucose detection with direct electron transfer to the electrode.
All of this would be placed on a flexible foil that, when applied to the skin like a patch, would monitor glucose level in real-time in the dermal interstitial fluid, just below the skin surface without reaching nerves or blood vessels.
AIT quickly determined that a conventional metallization process would suffice, but the biofunctionalization and microneedles would require a novel approach. Traditional finger-prick glucometers use glucose oxidase, which enables the generation of a signal in the presence of glucose in the blood sample. However, in order to transport the electronic signal to the electrode, the glucometers also require partially toxic mediators, which are a limiting factor for minimally invasive applications.
To solve that problem, AIT partnered with DirectSens, a pioneer in third-generation biosensors. The DirectSens technology provided the safe, direct electron transfer enzyme biofunctionalization required for the novel surface modification and microneedles AIT envisioned. This allowed the team to lower the voltage required to operate the NUMBAT biosensors, therefore reducing interferences and enabling longer-life performance.
The microneedles challenge
With the biofunctionalization problem solved, next, it was on to the microneedles. Because the team was aiming for extremely small needles— just 500 microns or 0.5 mm high with a 2-micron wide tip — they knew producing such fine projectiles would be challenging with conventional technology.
Traditional micro-injection molding, for example, would not be flexible in terms of customizing the microneedle layout and would stymie experimentation. While this might work in a production environment, during trials, each attempt would require the creation of a new high-precision mold, which would add time, costs, and complexity to the research process. Meanwhile, AIT knew that TPP 3D printing technologies would be too slow and much more expensive.
Manufacturing on Demand
DLP delivers speed, flexibility & precision
AIT settled on DLP-based micro-stereolithography printing as the best solution to deliver the flexibility required—both in the substrate material and in experimentation. To create the micro-stereolithography 3D printer, AIT partnered with In-Vision, which provided its Firebird UV DLP Projector equipped with a custom lens design. With a 2-micron pixel-pitch and a 2560×1600 native resolution, the Firebird projector provided the precision and customization to achieve NUMBAT’s specifications.
“The high resolution of the light engine was the critical factor”, said Giorgio Mutinati, senior research engineer, molecular diagnostics, in the Center for Health and Bioresources at AIT. “With its 2-micron pixel resolution and optical design, the projector was beyond the state of the art that we needed to enable and further the development process”.
In-Vision also collaborated with the AIT team to build the printer and provide and help program the software required. “In addition to the projector, the In-Vision LabView-based software was a core part of the project,” Giorgio said. “In-Vision worked with us to build up the system within our specifications and continue to support us in this project”.
New potential in microneedles technology
With NUMBAT having reached Technology Readiness Level 4, the team is ready to demonstrate the feasibility of the technologies at the biosensor level but is also formulating new project plans to further explore the printing technology they’ve developed. Prospects include developing a microneedle patch for other biomarkers such as lactate, incorporating biofunctionalized sensors for multiple biomarkers in the same patch, or even including hollow needles for drug delivery to create a closed-loop solution.
“The high-resolution capabilities of this printer give us so many options, and we’re looking for partners to further exploit this technology through additional research on needles and various needle geometries”, Giorgio said. “The competitive speed and flexibility of the technology open the door to many new and novel applications”.
* This article is reprinted from 3D Printing Media Network. If you are involved in infringement, please contact us to delete it.
Author: Andrea Gambini
Leave A Comment