The following is a preview of an interview conducted by 3dpbm with General Motors. Look out for the full story in our upcoming Automotive AM Focus 2021 eBook.
For over a century, Detroit-based General Motors (GM) has been a key pioneer and player in the global automotive sector. Today, GM holds the title of being the United States’ biggest automotive manufacturer, followed by Ford Motor Company and Fiat Chrysler. As one can imagine, it has not maintained this leading position by resting on its laurels. No, the company has had to continually innovate and stay up-to-date with changing trends, both on the consumer and manufacturing sides.
It is no surprise therefore that GM is a keen adopter of additive manufacturing. The technology, whose applications are growing rapidly across many industries, has always had a special place in the automotive industry: initially just for prototyping and now also for tooling and end-use production.
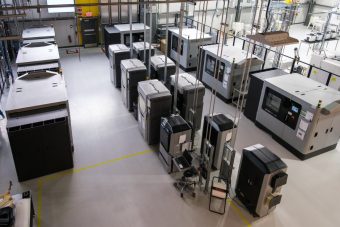
GM has been exploring the use of 3D printing for automotive production for over a decade and is now aiming to fully integrate the technology as an essential tool in its production toolbox. To better understand the company’s perspective on additive and its potential, we caught up with Ali Shabbir, Engineering Group Manager for Product Applications, and Dominick Lentine, Engineering Group Manager for Manufacturing Applications.
Manufacturing on Demand
Manufacturing matchmaker
Part of Shabbir’s mandate at GM is identifying the right type of manufacturing technology for specific production applications, matchmaking of sorts. In other words, he and his team find automotive applications where it makes technical and commercial sense to use additive manufacturing, and then identify which AM technology is best for the job.
“We holistically evaluate all the technologies that we typically use for our production applications—which can be parts or tools. Processes that have higher throughput and integral isotropic material properties are typically better suited in the plastics space. For instance, we are using HP’s Multi Jet Fusion technology for Cadillac V-Series HVAC ducts. The selective laser sintering process that we also have in-house at the Additive Industrialization Center [which opened its doors in December 2020] would be well suited to that type of application as well. On the metal side, we are using laser powder bed fusion to produce parts like electrical brackets.”
Shabbir goes on to emphasize GM’s priorities in terms of successful AM adoption. “Application selection is absolutely paramount for using AM for production components. There are certain things we need to do to ensure repeatable quality over time, but most of the challenge has to do with the identification and development of the application itself. You want to make sure that you’re not just 3D printing something because it’s cool, but that it actually makes sense, whether it’s leveraging additive-only design, or part consolidation, or lightweight. These are some of the considerations for picking the right application, and then from there you can scale.”
Lentine agrees: “Our challenge is less of a technology hurdle and more about education and awareness so that people see 3D printing as a tool in the toolbox.”
Watch this space for the full interview and learn more about GM’s AM strategy: how they are uplifting the industry through supplier partnerships and how AM is helping to usher in a new era of electric vehicle production.
* This article is reprinted from 3D Printing Media Network. If you are involved in infringement, please contact us to delete it.
Author: Tess Boissonneault
Leave A Comment