3D Sierra Leone, a dutch nonprofit organization, is providing customized 3D printed prostheses to patients in the West African country, with the support of SHINING 3D, a Hangzhou-headquartered 3D scanner and printer manufacturer.
3D Sierra Leone is dedicated to improving the lives of people in Sierra Leone that undergo amputations but are without access to relevant medical care. In line with its goal, the NPO is using 3D printing to create different types of prostheses for patients in the country. In order to scan the patient’s stump and produce an accurate, personalized device, 3D Sierra Leone is leveraging the EinScan Pro 2X Plus handheld 3D scanner from SHINING 3D, before 3D printing the relevant prostheses.
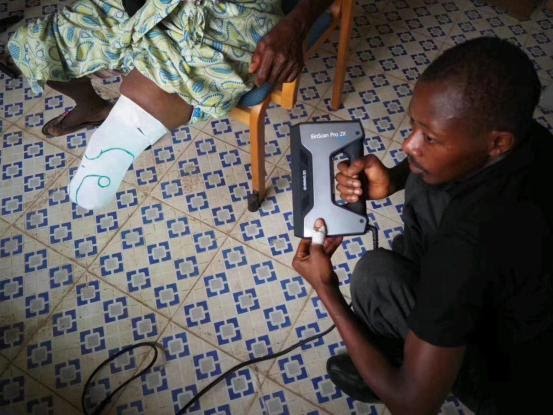
Providing prostheses with 3D printing
In Sierra Leone, a large number of amputations are carried out due to complex wounds caused by traffic accidents, serious infections and the delayed patient presentation to the hospital. Additionally, many amputees also lost their limbs during the Sierra Leone Civil War (1991-2002).
A majority of amputees in the country are without access to prostheses due to a lack of knowledge, availability of materials, trained staff and high costs, which can exact a physical and mental toll on the individual. 3D Sierra Leone explains that, with a prosthesis, many amputees can feel more at home in the society that they live in, overcoming issues of jealousy, insecurity, and depression.
In response, 3D Sierra Leone identified 3D printing as a useful and essential tool for manufacturing locally relevant medical aids for people in the country, such as braces, splints and prostheses, at a reasonable cost. The organization is therefore collaborating with the Technical Medicine course at the University of Twente, and under the guidance of the 3D lab at the Radboud University Medical Centre, to set up a 3D lab in the Masanga Hospital in Sierra Leone.
The 3D Lab is operated by Technical Medicine students from Dutch Universities TU Delft and University of Twente, who collaborate with local physiotherapists and prosthetic specialists. The lab is run with a focus on collaboration and knowledge exchange between the local population and Dutch researchers. 3D Sierra Leone also has plans to include Sierra Leonean students in the project in order to create a training place for the local population.
A sustainable process to support the local population
Manufacturing on Demand
3D Sierra Leone’s process for designing and manufacturing customized prostheses is focused on sustainability, in order to ensure the devices are affordable for the local population and the project can be carried out by the local population itself. As such, prostheses production has been made as standardized and simple as possible, and can thus be completed in a short amount of time.
Initially, the patient’s stump is scanned using the EinScan Pro 2X Plus, which takes around 20 minutes to include preparation of the scanner and clinical inspection of the stump. A design of the prosthesis is then produced in around 30 minutes using Meshmixer software, before 3D printing of the device takes place. Additional prosthesis parts, like feet, are made from locally sourced wood. After a number of physiotherapy sessions, an aesthetic cover is made, so that the prosthesis looks like a real leg.
Four case examples in the 3D Sierra Leone project have been shared using the method above, with the approval and authorization of the parties and their families, in the American Journal of Tropical Medicine and Hygiene (Vol. 102, No. 4, pages 905-909). The first two case studies are examples of arm prostheses that have been used by the patients’ for both aesthetic and practical purposes. One of the case studies details an arm splint 3D printed to support the healing of burned contractures around the joint of a child. The splint was important to ensure the burns could heal without contracting, which would limit the joint’s ability to move. Finally, the fourth case study pertains to an orthotic brace for a child with a condition known as kyphoscoliosis, an abnormal lateral curvature of the spine.
3D printing has proved a useful tool for providing necessary medical devices and supplies in areas with limited access to them, particularly in regards to prostheses, which can be difficult to source. For example, in 2017, the Enable Community Foundation (ECF) used 3D printing to create prostheses for people in Haiti in order to address the large number of upper-limb (UL) amputees in the country.
In Syria, 3D printing is also being used to provide prostheses as traditionally manufactured devices are hard to source and deliver to the country amid the ongoing Civil War. Syria Relief, a UK-based charity working in Syria, has pleaded with the UK’s Department for International Development (DFID) to provide funding for 3D prosthetics for children in the country.
* This article is reprinted from 3D Printing Industry. If you are involved in infringement, please contact us to delete it.
Author: Anas Essop
Leave A Comment