Fused Deposition Modeling (FDM)
Print your FDM parts with fast turnaround and wide variety of plastic materials as fast as 1 day!
FDM 3D printing service starting at only $20!
Overview: How FDM 3D printing works?
The Basics Of FDM 3D Printing
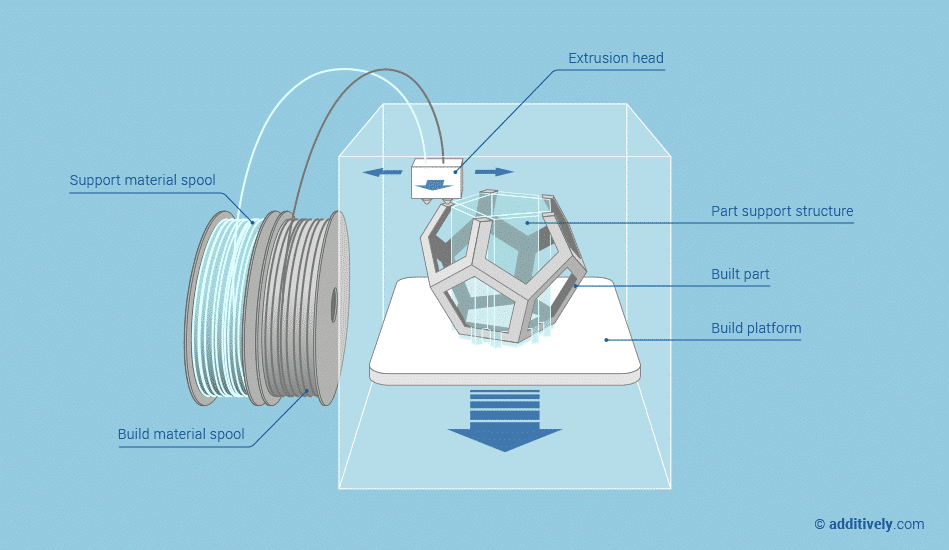
Click to enlarge
In FDM, a spool of filament is loaded into the printer and then fed to the extrusion head, which is equipped with a heated nozzle. Once the nozzle reaches the desired temperature, a motor drives the filament through it, melting it.
The printer moves the extrusion head, laying down melted material at precise locations, where it cools and solidifies (like a very precise hot-glue gun). When a layer is finished, the build platform moves down and the process repeats until the part is complete.
After printing, the part is usually ready to use but it might require some post-processing, such as removal of the support structures or surface smoothing.
Benefits Of FDM 3D Printing
Fused deposition modeling can build fully functional parts in standard plastics. However, they have anisotropy in the z-direction (vertical direction) and a step-structure on the surface.
Fused deposition modeling works with standard materials, for instance, ABS/PA/PC. Therefore, parts have good mechanical properties and are durable over time. Parts can be post-processed as any plastic part produced with conventional manufacturing.
Benefits Of FDM 3D Printing With FacFox
At FacFox, we have 2 levels of FDM printers: Lab-level and Industrial-level.
Lab-level FDM 3D printer is suitable for experimental projects that don’t require high accuracy/great mechanical properties or highly detailed surfaces, we can print PLA material at the largest volume of 1200 x 1200 x 1500mm.
Our Industrial-level FDM 3D printers, on the other hand, allow you to make 3D printed parts and prototypes in a wide range of high-performance engineering materials like ABS, PA, PC, ULTEM. We use the state-of-the-art Stratasys Fortus printer with a max build volume of 1000 x 800 x 500mm.
Prototypes made using this service can be used for engineering testing or even actual end-use products. You can also have metal 3D printed parts made using our DMLS 3D printing service.
Features of FDM 3D Printing
Advantages
Drawbacks
FDM 3D Printing Processes
Printers & Parameters – Printers: Stratasys Fortus Series, custom made FDM printers. – Maximal build volume: 914 x 610 x 914 mm(Fortus 900mc) – Minimum feature size: 0.2 mm Restrictions – Minimum layer thickness: 0.1 mm – Typical surface finish: 50 鈥 100 microns RA – Accuracy: (+/- 0.1-0.2% for industrial-level) Pre-build planning Important decision on design is the orientation and support structures. This depends on: – Geometry: Optimize it to reduce supports and layer lines. – Areas that need great smoothness or post-processing
Available Materials
Available Finishes
The finish option with the quickest turnaround. Which normally includes:
- Removal of support: Supports are dissolved/manually removed after printing. This is usually straightforward, however, it might require some extra effort to remove supports for聽 parts with complex geometric features. Regions with removed supports might have rougher surfaces than those that don’t.
- Painting
- Epoxy Coating
- Don鈥檛 see the finish you need? Submit an RFQ with ‘Suggest’ option, we鈥檒l look into a finishing process for you.
FDM 3D Printing Applications
FDM is ideal for producing form / fit and functional prototypes for testing in standard materials like PLA/ABS.Prototypes
The heat tolerance and great mechanical properties of industrial FDM materials let end parts like jigs, fixtures, brackets be produced directly.End Parts
FDM can be applied to make small batched products with varied requirments, ideal for small businesses that wishes to test the market’s reaction to thier newly developed products.Customized Products