Lincotek Additive has taken another step in its development program by increasing its production capacity to meet customer demand. The company is adding further EOS M400-4 additive machines in its brand new, state-of-the-art Additive Production Center for the aerospace and industrial sectors in Switzerland and obtained EN9100:2018 certification for its quality management system.
In the meantime, the Lincotek Group has also closed a deal with The Equity Club (TEC) to invest in the company and become a minority shareholder. The new funding will be used to strengthen Lincotek’s international presence, expand the range of technologies and services offered and become a fully integrated player in its areas of interest. This operation will provide Lincotek with an investment capacity of over 200 million euros. The Antolotti family will maintain control of the group with over 75% of shares.
AM remains a key area of development for Lincotek. The company’s Swiss facility, developed with the mindset of an industrial set-up, is applying lean manufacturing and best industry standards as it reaches the end of its first year of production. The new investment will allow the experienced Lincotek Additive team to offer customers a reliable and sophisticated additive supply chain with an even faster response. With productive and high-quality additive processes and efficient Additive Manufacturing (AM) production management, this will also mean impressive cost efficiency.
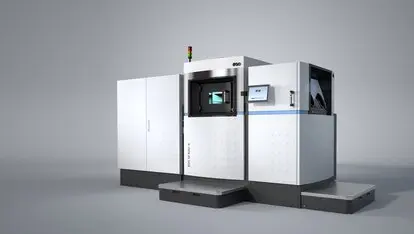
The EOS M400-4 features a large build volume (400 x 400 x 350 mm XYZ) and its higher productivity rate, with 4 x 400W lasers will enable Lincotek to produce larger IGT or Aviation parts.
Manufacturing on Demand
The Swiss plant is designed to scale up production and development work in AM helping, customers to build or expand their serial production. Besides the AM systems, a high-temperature vacuum furnace has been installed, specifically designed for the heat treatment of additively manufactured Ni-base superalloys. A fully equipped metallography lab is available, along with other analytic equipment, such as a fully automated GOM cell, to develop, qualify and produce AM components. The main focus for the facility from a materials point of view is the superalloys used for high-temperature applications, such as HASTELLOY X and IN939. More advanced alloys, including IN738, are currently under development.
Located between Zurich and Baden, Lincotek Additive takes advantage of a strong network of experienced suppliers in the area. In addition, the proximity to the French and Italian plants of the Group leads to a very close and efficient collaboration, contributing to best-in-class contract manufacturing services from powder to ready-to-market parts.
“As Lincotek Additive, we are able to offer our customers a real Contract Manufacturing alternative in serial AM. This is enhanced by end-to-end capabilities – coatings and precision machining, for example, if needed. We strongly believe in building a reliable partnership based on a collaborative model offering unique, and customer-focused supply chain solutions,” said Winfried Schaller, CEO of Lincotek Group.
A highly experienced team helps to complete the picture. With the structure and support of the wider Group, being active in the Additive Manufacturing field since 2006, Lincotek Additive can count on around 30 Additive Printing Units globally and profound knowledge of producing reliable and high-quality additive parts. In its development team in Switzerland alone, Lincotek can count on more than 40 years of collective experience in the IGT business and 30 years of AM experience, offering customers unique development capabilities and a partner to rely on.
* This article is reprinted from 3D Printing Media Network. If you are involved in infringement, please contact us to delete it.
Author: Davide Sher
Leave A Comment