At the beginning of March, an overwhelmed hospital in Brescia, Italy raised the alarm that they were in lack of the breathing tubes. The respiratory valve is a kind of consumable accessory of the CPAP Hood System, which is essential for the life-saving coronavirus treatments.
The valves along with the intensive care machine were usually supplied by the manufacturing company Intersurgical. But their Managing Director Charles Bellm stated that due to medical manufacturing regulations, they could not produce the accessory on time.
Hearing about the hospital was seeking for alternatives for the valves, an Italian startup 3D printing company Isinnova immediately joined the battle with the unprecedented health crisis.
Cristian Fracassi and Alessandro Romaioli, the founder of Isinnova, brought the 3D printers they possessed to the hospital. As the manufacturer Intersurgical declined to share the blueprint, Romaioli and Fracassi had to reverse-engineer the valve and redesign one.
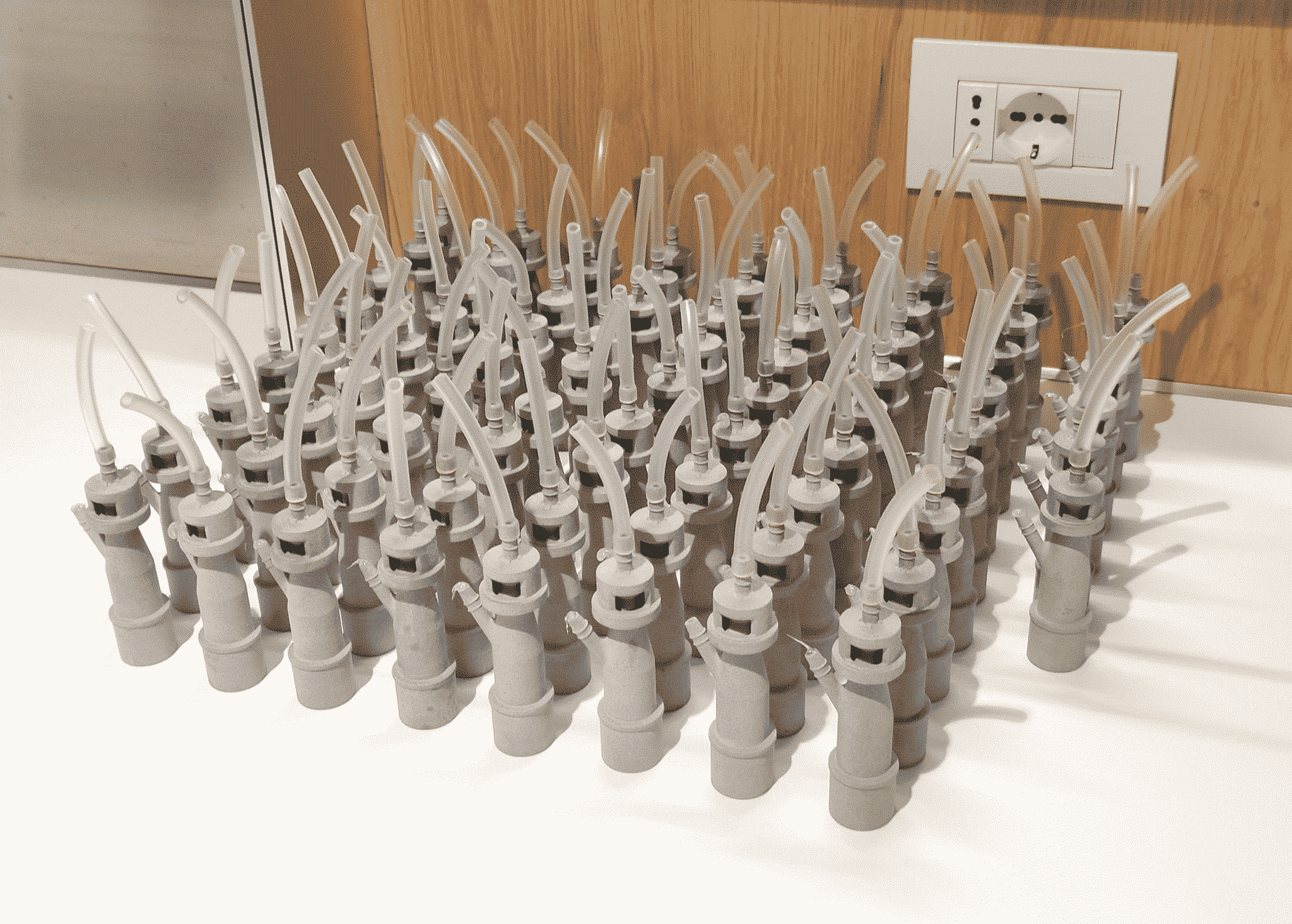
Thanks to their aid, more than 10 patients have been saved. The valves alone used to cost a few euros, but it only take one euro to make one through 3D printing.
The valve can only be reused for several times after sterilization. Isinnova planned to print one hundred more copies but they were not sure how long they can last.
Words soon reached other 3D printing companies around the world and many were willing to lend a helping hand. Facfox, one of the largest online 3D printing service provider, also swiftly join the volunteer project.
Unlike Isinnova, FacFox selects SLA Generic Resin and prints with Stereolithography(SLA) machine for the following reasons:
- The SLA Generic Resin has a lower cost than SLS and MJF nylon.
- Compared with FDM plastic and MJF, SLS nylon, SLA Generic Resin part has better airtightness and water tightness. FDM printed part has relatively large gaps between plastic layers, and nylon powder sintered structures also have tiny gaps. There is a risk that they will leak under high-pressure.
- Compared with FDM, SLS, and MJF, the SLA printed part has a smoother surface and less dust. It’s also easy to be cleaned and installed.
- After the resin is printed, there will be a UV post-curing process. That is to say, the printed part goes through sterilization during this procedure, thus the safeness and cleanness are further guaranteed.
FacFox has printed 30 packs of valves, 4 pieces in one pack, which are sent to Italy as a donation. Their CEO Edi is in close communication with the Italian volunteer group and prepares the subsequent batch of production.
“We have no intention of profit on this situation, we are not going to use the designs or product beyond the strict need for us forced to act, we are not going to spread the drawing.” said Fracassi. It’s the commonsense of those 3D printing manufacturers.
FacFox claims that they will be quick-response if any other hospital is seeking for help. They are also collaborating with other 3D printing manufacturers in China to help to supply appliances in the quarantine.