This is the Airbus concept cabin vision launched by Airbus in 2011. It sounds full of Marvel, but with the development of technology, it is slowly becoming a reality.
Airbus has collaborated with New York construction companies The Living, Autodesk, and APWorks to develop the world’s largest metal 3D printed aircraft component, the Bionic Partition. The partition is a slender and important partition wall separating the crew and passengers. The fixed position of the emergency stretcher and the folding and fixed position of the flight attendant seat are integrated. The structure is complex and versatile, and the manufacturing process is full of challenges.
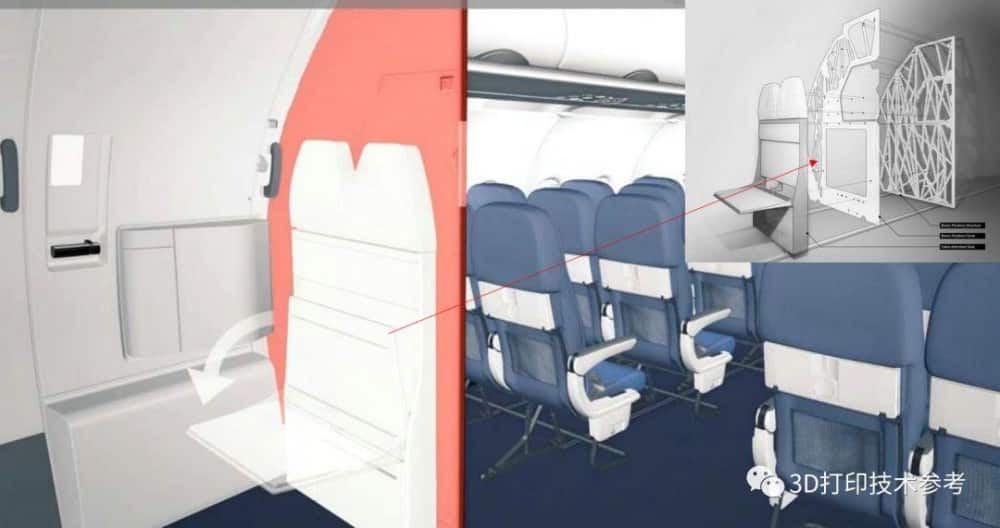
The designer has made a bionic design for the structure of the partition and used advanced materials for metal 3D printing. Compared with the traditional partition, the weight is reduced by 45%, and the strength and function are more powerful. The reduced weight can save fuel and reduce carbon emissions by more than 1 million tons per year.
The design of the partition structure simulates the growth of cells and bones, connecting all interface points to the main structure of the aircraft. The structures in each partition are connected to each other, and these biological-based designs are tested by computers to finally create unique structures. The initial goal of the design team was to reduce the weight by 30% and ensure performance. By using a bionic design, the weight was reduced to 45%.
In the design of weight reduction, it is necessary to set strength constraints. The design team obtained more than 10,000 design arrangements of the partition structure through software simulation, and relied on big data analysis to reduce the number of design iterations, and finally determined the structure with the best performance.
After deciding to manufacture, Airbus used three different 3D printing systems to complete the manufacturing: Concept Laser M2, EOS M290 and EOS M400 (for very large parts). The staff divides the entire isolation structure into multiple components, selects a printer with a suitable molding space according to the size of the components, and then produces them at the same time. Create a complete partition to print at least seven batches.
The entire structure is divided into 116 components, all of which have connectors. After the final splicing is completed, the staff is impressed by its light-weight and strong strength.
The person in charge of the project pointed out that the isolation structure in the past was almost impossible to achieve weight loss, and today the bionic design and 3D printing can easily reduce the weight of components.
Current metal printers can only print small aircraft parts. The larger molding space means that larger parts can be printed . Airbus’s goal is to use the bionic design to achieve 3D printing of the cockpit and even the entire aircraft. Now that the technology is changing with each passing day, it may not be possible in the future.
Although equipment, materials, and processes constitute the three elements of 3D printing, many cases show that design will be the key to future 3D printing technology.