Researchers at the University of Messina have formulated a lightweight foam concrete that can more efficiently 3D print building structures without the need for any formwork. Unlike traditional lightweight foam concrete, this new material (3DPC) has a high viscosity, so it can maintain its shape in a “melted” or “fresh” state. After extensive testing, the team also found that the compressive strength of this specially formulated concrete is higher than that of conventional concrete (CC), making it potentially industrially useful.
Lightweight foam concrete
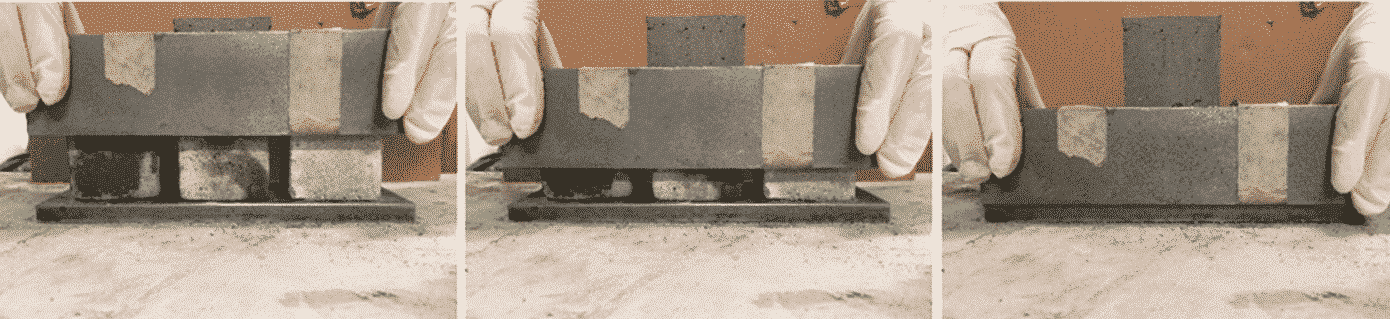
Foamed concrete refers to a low-density cement material that has been injected with a foaming agent to increase air. The presence of air bubbles in the mixture tends to give the concrete some special (but surprisingly useful) properties, such as lightweight, thermal insulation, sound absorption, and fire resistance, all of which are extremely needed in the construction industry. However, the lightweight nature of foam concrete does have its shortcomings. Traditional foam concrete usually shows low mechanical strength and instability, making it unsuitable for any actual building.
Messina (Messina) researchers must use three different types of commercially available cement to formulate their new lightweight 3DPC mixture, which uses Foamin C as a blowing agent.
The study found that there are two different ways to compare 3DPC and CC. The first involves comparing the dimensional stability of two concretes in the fresh state (squeeze test), and the second involves the battle of compressive strength.
Six cube specimens with a height of 4.5 cm were formed from the two fresh cements. Leave the cube for up to 40 minutes, then measure and record the “slump” of the two materials. The researchers concluded that their specially formulated 3DPC is more viscous than standard CC and can retain its shape indefinitely, and CC eventually flattens out. Therefore, the new concrete can be 3D printed without any formwork, and can fully support itself until the curing process is completed.
Next, another set of similar specimens was cured in various media to make their compressive strengths contradict each other. At all dry densities (400 – 800kg / m³), the team’s 3DPC on average exhibited higher compressive strength than CC, allowing it to withstand the pressure on the building walls.
More details of this study can be found in the paper entitled “3D Printable Lightweight Foam Concrete and Comparison with Classical Foam Concrete in Fresh State Characteristics and Mechanical Strength”. It was co-authored by Devid Falliano, Dario De Domenico, Guiseppe Ricciardi, and Ernesto Gugliandolo.
The specific 3D printing has begun to arouse serious attention from companies and research institutions. Engineers at Purdue University have begun researching ways to 3D print concrete wind turbine parts for offshore use. If successful, these low-cost parts will be shipped 30 miles off the US coast and installed on the seabed. Elsewhere in Dubai, Twente AM launched its latest large-scale concrete 3D printer with a printing footprint of 391m³.