Elli srl is an Italian startup developing a new stylistic language in the field of furniture design, with a focus on product innovation and sustainability. Post Elli’s release of their ‘Soho’ and ‘Bryant’ pieces, and pre the release of their latest ‘Zero’ modular systems, we had the opportunity to speak with their founder, Alessio Elli, and find out more about how he has integrated AM into his world of furniture design and his ‘New Made in Italy’ philosophy.
“By training, and culture, I come from traditional Italian manufacturing, of which I have begun to see the limitations, or rather, from the creativity and production point of view – its chains and constraints,” Alessio Elli explained. “With the new needs expressed by the market – where the object goes beyond its function, by society, and based on the objectives of the UN 2030 agenda – research has shifted towards products that must be flexible, adaptable, rational, and customizable, in order to be an expression of the ‘self’, which represent ideals and values as a source of inspiration and stimulus.”
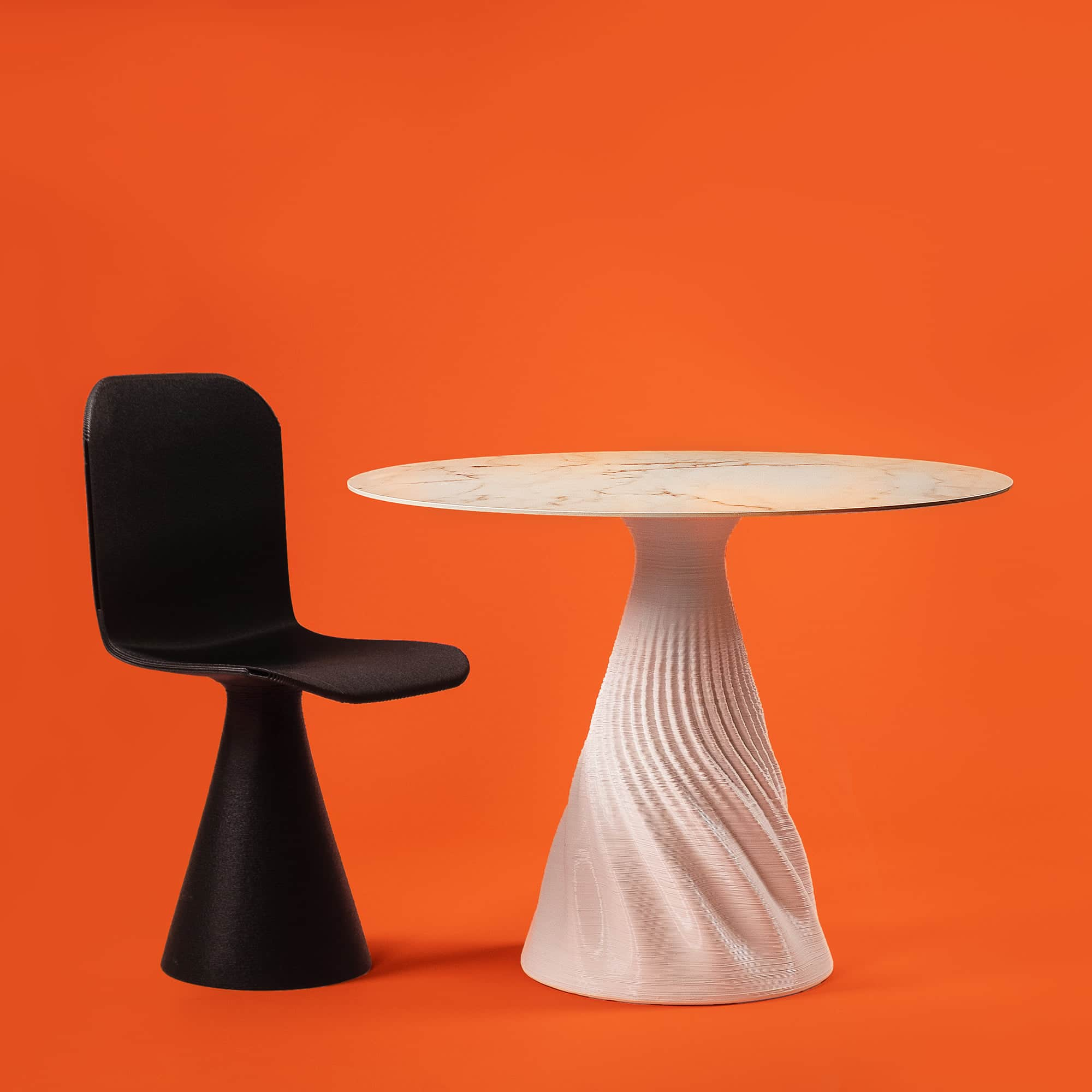
In a certain sense, the transition to additive manufacturing was simple for Elli, as he found the opportunity to realize his company’s stated vision: reinvent the way of conceiving, producing, and designing a furniture object, bearing in mind the entire life cycle of the product – from the raw material to its recovery/reuse at the end of its cycle – while still ensuring the same quality that distinguishes Made in Italy design as we know it.
AM also allows Elli to better express creative and stylistic identity. “Being able to make nature interact perfectly-imperfectly with craftsmanship and technological innovation”, he says, “allows us to create that feels human, and real, in a time in which it seems that the immateriality and intangibility of the virtual have the upper hand over everything.”
To 3D print this furniture pieces, Elli turned to a collaboration with LFAM system manufacturer Caracol. This partnership enabled Ellie to share goals and values with other companies and professionals. Both companies have sustainability as a cornerstone.
“By collaborating with Caracol we have access to their proprietary Large Scale Additive Manufacturing Robotics technology that allows us to produce very large components, Alessio Elli says. “In particular, the technology developed by Caracol makes it possible to overcome limits on size, materials, and geometric complexity; it also allows the production of components with direct printing from pellets of different materials – even from recycled sources – to create circular economic loops.
“The sustainability of our products, our circular loop, the Made & Remade option (the possibility of repurchase after 5 years, using the same quantity of material to create new products) have been enthusiastically welcomed by the main realities with which I collaborate. Technology and innovation associated with the importance of human work, are market questions – to which we give concrete, clear and coherent answers with our collections.”
Manufacturing on Demand
“What I notice from the general public (here in Italy)”, he adds, “is how enthusiasm becomes hesitation, as additive manufacturing is still seen as only suited for prototyping and testing, and not as a final product that is suitable for production, is scalable, and above all, is of value – with its own language, both in terms of content and design.”
Elli srl’s products are able to reach a transversal clientele, from the customer attracted by innovation, to the one attentive to sustainability and environmental impact, to the lover of design and the best of Made in Italy.
At the moment there is no specific distribution channel for these types of products. Elli collaborates with strong marketplaces in distributing and making known the excellence of Made in Italy furniture, communicating how to change the gaze and yardstick towards products made through additive manufacturing using recycled plastics. The value of a product is no longer represented only by the quality of the materials used, but by the lower environmental impact necessary to obtain it, and the lower environmental impact when it reaches the end of its life to recover and/or dispose of it.
“A company like ours that wants to propose a new concept of Made in Italy in continuity with our manufacturing history faces a challenge that is not simple. We must communicate and make it clear that our production and products are an expression of the same values of quality, innovation, beauty, and style typical of the most traditional Made in Italy,” Elli says.
Discussing some of the biggest challenges and benefits relative to the world of 3D printing furniture, Alessio tells us that he was initially very skeptical, seeing 3D printer as limited to ‘home printers to make small gadgets of low value and nothing more’. “I think”, he now says, “that this is a bit of the original sin in the world of additive manufacturing because, until recently, it was so seen by the general public in this light, but then, once the gaze was changed, the creative judgment and value metrics typical of traditional manufacturing were reset, the change was in a certain sense simple and a world of opportunities opened up.”
From a creative point of view, the challenge for Elli was to internalize the peculiarities of additive manufacturing and find the key to enhance its characteristics. The company managed to give dynamism to the product through soft and fluid lines, reducing the materials and components that traditionally make up a furniture piece – adapting the pre-existing components with cutting-edge design and engineering solutions.
“The more I enter this world”, Alessio Elli concludes, “the more I appreciate its advantages today and the enormous potential and opportunities for the near future; using recycled, raw material and transforming it into objects of this quality and design, reducing the time needed from prototyping to the market (finished product), cost containment, eliminating waste during production and reducing spaces dedicated to production are advantages very important. Economic and environmental issues also defined the design and function of a piece of furniture – clearly evident in our new ‘Freedom’ collection – as well as the possibility of customizing the product on several levels while keeping the ‘extra’ costs for this tailor-made service contained.”
* This article is reprinted from 3D Printing Media Network. If you are involved in infringement, please contact us to delete it.
Author: Edward Wakefield
Leave A Comment