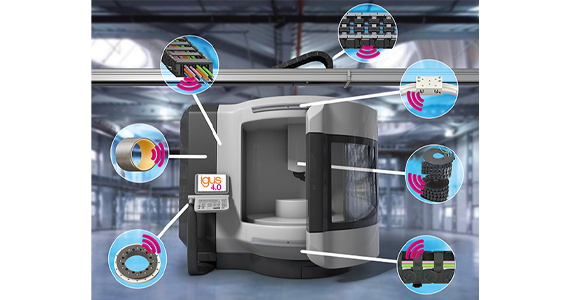
Igus, a provider of specialized polymer components and material solutions, announced that its researchers have developed a method to print sensors into friction components to signal the need to replace the sensor long before failure. Now, if an overload is expected or the wear limit is approaching, the component can provide a warning and use its printed sensor layer to develop inherent predictive maintenance features. This layer technology called “isense” can continuously measure changes in resistance and can be 3D printed using specially developed conductive materials that adhere to the friction wires or powders of the igildur material product line.
In 2014, the company has launched the world’s first 3D printing friction filament, which claims 50 times the wear resistance of traditional 3D printing filament materials. Its igildur material series is not only designed to significantly improve durability, wear-resistance and self-lubrication, but it can also be precisely configured and accurately estimated the service life of components made of these materials. Igildur material is also FDA certified and can be used in food, cosmetics and beverage applications. It has been proven to reduce the cost of 3D printed plastic fixtures by 85% and reduce manufacturing time by 70% compared to traditional aluminum fixtures. They also do not require lubrication or maintenance to operate continuously, are lighter than other materials used in such applications, and can be 3D printed to meet the complex shape requirements of any design.
The service life of such parts can be accurately estimated using free online tools, and is suitable for sliding bearings, spherical bearings, gears, cables, bars, slewing bearings, screw systems and other parts. Since each igildur material is composed of basic polymer materials, fillers and fibers, and microscopic solid lubricants, the composition and performance of the material can be configured and controlled. When Igus introduced special products for fuse manufacturing and laser sintering, this brought an additional advantage: polymer moving parts with better printing performance, wear and abrasion resistance. Last year, we reported how the company made high-temperature 3D printing easier to obtain and use. Otherwise, it would be difficult to do this with materials such as PEEK, PEKK and PEI. It has made the design of the high-temperature 3D printer developed by its R&D team and the files are available online.
The isense technology can currently be used to produce smart bearings, linear carriages, screw nuts, chains or cable systems, etc.
The use of components made of this “smart plastic” material provides users with a way to automate predictive maintenance or establish a seamless Industry 4.0 connection network for local or large-scale individual components. This will reduce machine or operation downtime and provide a cost-effective, flexible 3D printing solution for predictive part maintenance. Using the multi-material 3D printing developed in-house by the company, isense’s special materials can be used for 3D printing. Currently, sensor technology can be used for two use cases: potential overload detection and wear limit detection. Usually, these signals are communicated via a built-in LED light or a readout display unit connected to the module, indicating the need for replacement or preventive maintenance.
By using igus’ 3D printing services, companies can order smart components in a cost-effective manner within three days. These companies hope to integrate affordable sensor technology into high-wear or mobile components or products. Currently, the company has launched isense technical services and is undergoing beta testing to provide free samples to selected customers.
This cost-effective solution for a wide range of industrial applications is the key to applying 3D printing to smart components, parts supply chains, and parts repair or replacement. It can not only be used to design and directly manufacture such parts, but also can be used in combination with digital twin technology and integrated sensors, thereby making real-time predictive maintenance and performance optimization of individual parts possible, as we have also seen, highly-specialized components with GE and Siemens. We have also seen 3D printed sensors built into parts or structures to measure and track performance. Previously, Optomec showed how to use its Aerosol Jet technology to install 3D printed strain sensors directly onto turbine blades.
Leave A Comment