3D printing technology is a cutting-edge innovation that can create complex and customized objects layer by layer from digital models. In recent years, 3D printing technology has been widely applied in various fields, especially in surgery and medical industry. 3D printing technology can provide personalized and precise solutions for patients with different needs and conditions, and improve the quality and efficiency of surgical procedures and outcomes.
In this post, we will share with you three cases of metal 3D printing applications in surgery and medical industry, which demonstrate the advantages and potential of this technology. These cases are:
- Case 1: A new type of 3D printed porous tantalum metal device for spinal fusion surgery without bone grafting
- Case 2: A novel surgery using 3D printed porous vertebral fusion device for spinal cord compression
- Case 3: A successful revision surgery using 3D printed porous artificial acetabulum for hip joint prosthesis failure
Case 1: A New Type of 3D Printed Porous Tantalum Metal Device for Spinal Fusion Surgery without Bone Grafting
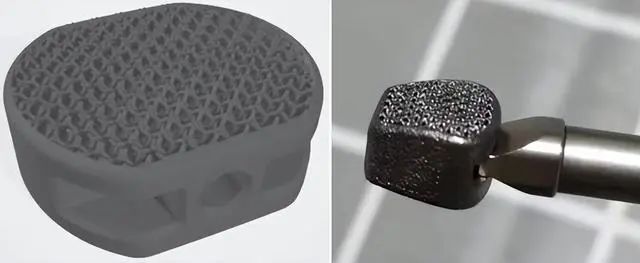
Spinal fusion surgery is a common treatment for spinal diseases, but it often requires bone grafting from the patient or a donor. This can cause complications such as infection, rejection, and pain. A team of orthopedic surgeons in China has developed a new solution: a 3D printed porous tantalum metal device that can fuse with the spine without bone grafting.
The device is designed to mimic the natural structure and elasticity of bone, and to stimulate bone growth into its pores. This way, the device can achieve a close and firm attachment with the vertebrae, and avoid stress shielding and non-fusion problems that may occur with traditional materials such as PEEK or titanium alloy. The device also eliminates the need for a bone grafting chamber, which reduces the surgery time and cost.
The team has successfully implanted the device in two patients with cervical and lumbar spine diseases, respectively. The patients recovered well and showed significant improvement in their symptoms. The team has applied for an invention patent and obtained a product registration certificate for the device. They plan to continue developing personalized 3D printed spinal implants that can benefit more patients with spinal diseases.
Case 2: A Novel Surgery Using 3D Printed Porous Vertebral Fusion Device for Spinal Cord Compression
A patient with severe spinal cord compression due to cervical disc herniation underwent a novel surgery in Sichuan, China. The surgery involved removing part of the affected vertebra and implanting a 3D printed porous vertebral fusion device (artificial vertebra). This was the first time such a device was used in the southwest region of China.
The device was personalized based on the patient’s imaging data and designed to fit the shape of the vertebral endplate. The device had a porous structure that mimicked the natural bone and stimulated bone growth. The device also had a curved surface that increased the contact area with the endplate and avoided stress concentration. The device provided good stability, bone integration, and physiological curvature restoration for the spine.
The surgery was performed by a team of neurosurgeons who cooperated with a technical team of medical 3D printing experts. The surgery went smoothly and the patient recovered well. The surgery was a new exploration of 3D printing technology in neurosurgery and a step towards precision surgery for spinal diseases.
Case 3: A Successful Revision Surgery Using 3D Printed Porous Artificial Acetabulum for Hip Joint Prosthesis Failure
Mr. Luo, 60 years old, suffered from hip joint pain and limited mobility for a long time. He had an artificial hip joint implanted 20 years ago, but it was severely worn out and displaced, causing bone loss and spinal cord compression around the acetabulum. He needed a revision surgery to replace the damaged prosthesis and restore his hip function. He came to Chengdu First Orthopedic Hospital for help.
Director Yin Yi and his team from the Department of Joint Surgery decided to use 3D printing technology to assist in the surgery. They used the patient’s imaging data to design and print a customized porous artificial acetabulum that matched the patient’s anatomy and biomechanics. They also simulated the surgery on a computer and in vitro to ensure accuracy and smoothness.
The team successfully performed the revision surgery with the 3D printed prosthesis. The prosthesis had good contact and stability with the bone, and stimulated bone growth and integration. The surgery restored the physiological curvature and function of the hip joint. Mr. Luo recovered well after the surgery and was able to walk and move freely.
Conclusion
These cases show how 3D printing technology can create metal implants that are more compatible, stable, and functional than traditional methods. 3D printing technology can also reduce the risks of complications, infections, and rejection, and shorten the recovery time and cost for patients. Moreover, 3D printing technology can enable personalized design and simulation based on the patient’s anatomy and biomechanics, ensuring a better fit and function of the implants.
We hope these cases can inspire you to explore the possibilities of 3D printing technology in surgery and medical industry. If you are interested in metal 3D printing services, we recommend you to check out FacFox, a leading online platform that provides high-quality and affordable metal 3D printing services. FacFox has a team of professional engineers and technicians who can help you with your metal 3D printing projects, from design to production.
FacFox also has a variety of metal materials to choose from, such as titanium, stainless steel, aluminum, copper, etc. Whether you need metal implants for medical purposes or metal parts for industrial applications, FacFox can meet your needs and expectations. Visit their website at https://www.facfox.com/ to learn more about their metal 3D printing services and get a free quote via info@facfox.com today.
Leave A Comment