Kasto, a German sawing machine manufacturer, has joined the NextGenAM project, to support the acceleration of industrial 3D printing.
The initial project partners, Premium Aerotec, Daimler, and EOS, intend to use Kasto’s post-processing system, KASTOwin, to optimize the latter of metal 3D printing.
The KASTOwin system
Founded in 1844, KASTO has pioneered technology in sawing and storing of metal bar stock and sheet metal. With the emergence of additive manufacturing, the company has used its 170 years of experience to develop machinery capable of performing component separation reliably and efficiently.
The KASTOwin system has a cutting range of 400 mm x 400 mm. The machine is also fully enclosed to protect the ambient air from tiny particles produced by cutting the 3D printed components, and an extraction system can be connected for extra safety management.
This technology will support the NextGenAM project’s aim to develop a complete system for the production of aluminum components for the automotive and aerospace industries. A KASTOwin is currently being used in the project’s pilot production chain at Premium AEROTEC in Varel, northern Germany, a research facility developing techniques for processing metallic materials.
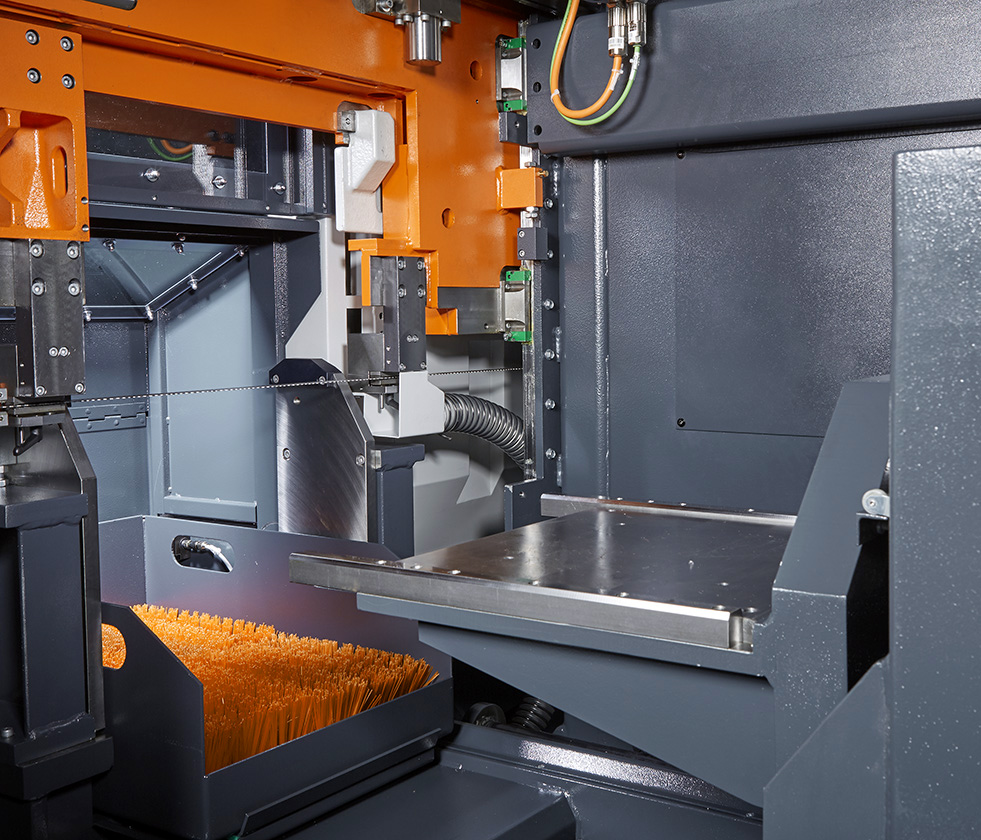
The NextGenAM project
Last year, Premium AEROTEC, a subsidiary of multinational aerospace organization Airbus Group, began collaborating with EOS and Daimler to develop a 3D printing powered smart factory otherwise known as the “next generation of additive manufacturing (AM)” i.e., NextGenAM.
Following this, earlier this year, the project established its first pilot plant, comprising of various EOS M 400-4 four-laser system for industrial metal 3D printing, to develop a complete production cell for additive manufacturing aluminum components. This pilot plant will lead to automated industrial 3D printing processes, enabling technology for larger batches of serial production.
“We are taking a significant step towards achieving cost-effectiveness in metal 3D printing throughout the process chain,” said Jasmin Eichler, Director of Research Future Technologies, Daimler AG.
“The project lays the cornerstone for the future realization of larger quantities in the automotive series production process – with the same reliability, functionality, longevity, and economy as for the components from conventional production.”
Submit your nominations for the 2019 Industry Awards here.
Also, for all the latest 3D printing news, subscribe to the Industry newsletter, follow us on Twitter, and like us on Facebook.
Make your next additive manufacturing career move or hire new talent. Search and post Jobs on our free jobs service.
Featured image shows the KASTOwin bandsaw, turning device, and horizontally acting blade that separates 3D printed components from theirs build platform and allows them to fall into a container. Photo via KASTO.
Leave A Comment