It’s that time of the year for CES 2016, the innovation-filled electronics tradeshow that is kicking off this week in Las Vegas, Nevada. Though I’m sure there will be plenty of great products and ideas spread all throughout the convention floor, attendees may also want to keep an eye on the sky for the JB-9, a functional jet turbine powered backpack created by JetPack Aviation. For over 40 years now, lead designer Nelson Tyler and his team at JetPack Aviation have been working towards perfecting the design behind the once mythical JetPack, and it turns out that 3D printing may hold the key to its eventual success.
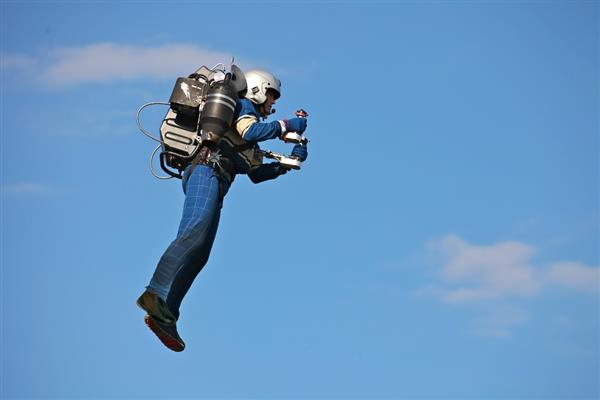
Thanks to the Southern California-based Airwolf 3D and their AXIOM 3D printer, JetPack Aviation has been able to improve both the overall function and practicality behind their jet turbine backpacks. Take the JetPack’s tank for instance, which once cost between $5,000 to $12,000 to prototype with a traditional 5-axis CNC machine. With Airwolf 3D’s AXIOM printer and top-quality ABS filament, the cost behind the JB-9’s tank was suddenly reduced from the thousands to just $400. “Airwolf 3D’s latest AXIOM 3D printer was the key enabling technology to allow us to rapidly prototype our new JetPack fuel tank prior to committing to actual tooling” stated Nelson Tyler, the lead designer at JetPack Aviation.
By implementing this AXIOM desktop 3D printer in their manufacturing process, JetPack Aviation has become the latest example of a company to utilize 3D printing for tooling and prototyping. Switching over from traditional modeling foam or aluminum into ABS, the team behind the JB-9 was able to produce and protect their large ABS-based tooling pieces with WolfBite adhesive, produced by Airwolf 3D to ensure the proper bonding of their ABS material. All in all, the AXIOM 3D printer has allowed the JetPack Aviation team greater flexibility and lower costs, proving that even desktop-grade printers have a place in industrial endeavors.
“The application of low cost desktop 3D printers allows small or startup companies to make large tooling for composite layups, patterns for casting and rotomolding, vacuum forming tools, and even low volume production injection molds, previously the exclusive domain of large or very specialized manufacturing organizations,” said Miodrag Micic, the professor of engineering design technology at Cerritos College.
Airwolf 3D and JetPack Aviation will be showcasing their 3D printed JetPack components at CES 2016 on January 7th, though it remains to be seen whether or not someone will be flying around the convention center or not. The next JetPack model, the JB-10, is already said, through early testing, to be able to reach 10,000 feet in altitude and 100 mph in speed, leaving me to personally wonder what other ways Airwolf 3D’s printer has helped to make this once-fantastical JetPack technology a physical reality.
Leave A Comment