Resin isn’t the most durable material, but read on for how resin’s 3D print strength compares to other materials. It might surprise you!
It’s a given that resin 3D printing produces highly detailed and accurate parts with very nice surface finishes. At the same time, it’s slowly being used for more diverse applications because there’s a greater variety of resins available. Still, when tough and functional parts are required, resin printing isn’t usually the go-to technology.
Why is that? Well, it’s true that most standard resins are relatively brittle compared to other 3D printing materials and aren’t recommended for stressed parts or outdoor use, although there are tough and durable resins on the market specifically formulated for stronger applications, and they can be really strong.
In this article, we’ll look more into these tough 3D printing resins and show you just how strong they can really be.
Strong but Sweet

While FDM 3D printing technology can use traditional industrial plastics like ABS and polycarbonate (PC), resin 3D printers require special photopolymer resins that harden (cure) under UV light. Most 3D printing resins are either epoxy-based or acrylate-based, the latter being used more often in desktop printers.
A lot of people think of resin 3D printed parts as fragile and most suitable for ornamental and prototyping applications rather than functional and load-bearing components. But this is only true if the resin isn’t properly selected. That being said, if you’re buying a generic resin for a tough job, it won’t give you the strength that you’re looking for.
Examples of super-strong resin can be found in a wide variety of industries. There are castable resins for making jewelry and 3D printing in the field of dentistry to produce mouth guards, crowns, and surgical guides. There are also high-temperature resins that are suitable for different industrial applications and even resins that can produce rubber-like parts.
Let’s turn our focus to the strongest resins available and find out how tough they actually are compared with other FDM 3D printing materials.
Strength in Numbers
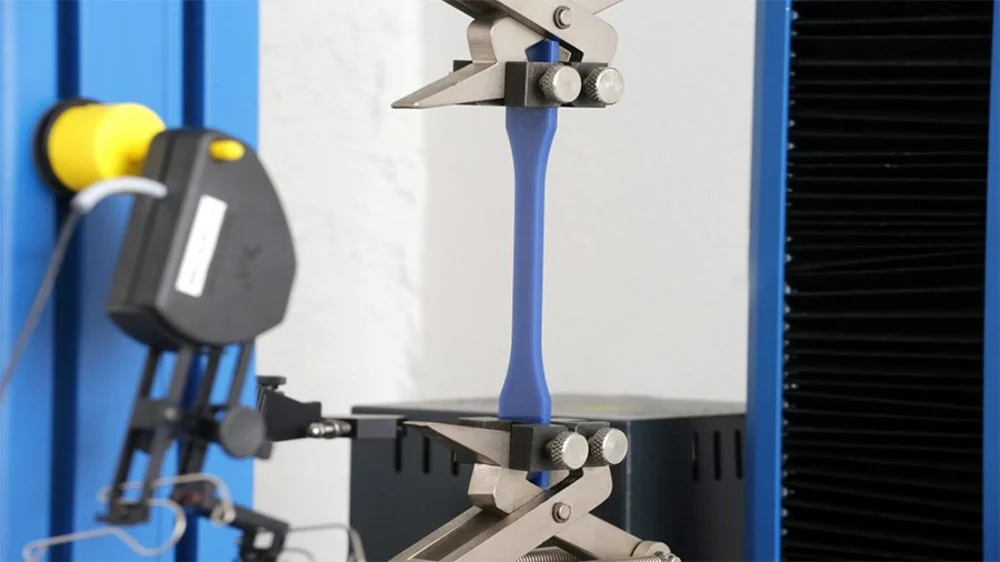
Let’s start by briefly going over a mechanical property that strongly relates to material strength. Tensile strength is defined as the maximum stress that a certain material can withstand while being stretched before breaking.
As the definition suggests, tensile strength values are usually measured by a pull test that follows strict international procedures, so the results can be used worldwide. The higher the tensile strength, the stronger the material is considered to be because of how much stress it can withstand.
Now, for the resins. First, let’s look at how standard 3D printing resins compare to resins marketed as tough. Then, we’ll compare these tougher resins to common FDM materials like ABS, PLA, and PETG.
Standard vs. Tough Resins
The standard resin selected as our reference was Anycubic’s colored UV resin since their Photon series of printers is one of the most popular on the market.
From the graph above, it’s clear how much stronger the tough resins are compared to the standard. In fact, the three resins that are chosen for this comparison – the Formlabs Tough 2000, eSun’s Hard-Tough, and Siraya Tech’s “Blu” – show almost double the tensile strength compared to Anycubic’s resin. (Formlabs’ tough resin line, including the 2000, is proprietary and can only be used with the latest Formlabs printers.)
Just because the resin is tough, it doesn’t mean that prints made from these resins will be twice as strong as if they were printed with a standard resin. Other factors like model design and print settings play important roles in the final print’s strength, which we’ll discuss in more detail later.
Nonetheless, comparing tensile strength is a straightforward way to determine which material is stronger, and from the numbers supplied by the manufacturers, it’s clear that these resins are much tougher than the standard. But how do these tough resins hold up against other plastics used by FDM 3D printers?
Tough Resins vs. FDM Materials
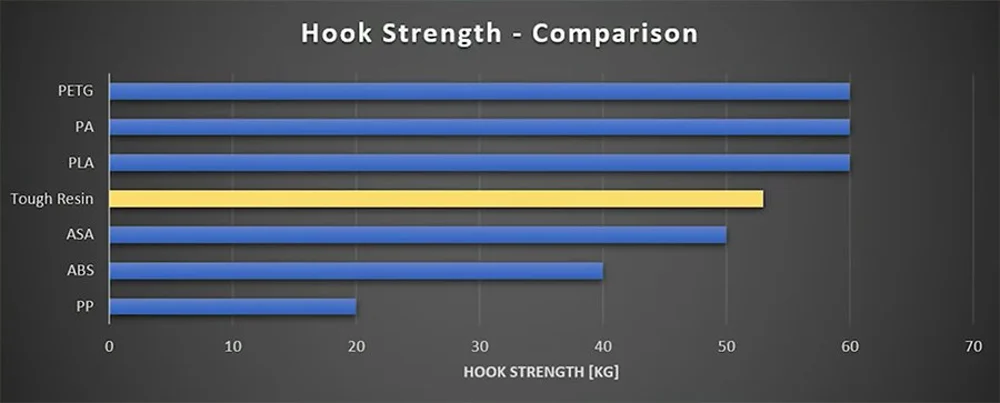
To answer this question, we’re turning to Stefan Herman from the CNC Kitchen YouTube channel, who has developed a testing method in which a 3D printed hook is stretched until breakage, simulating a tensile strength pull test.
Stefan’s been consistently testing different materials with this method, and the results are shown in the graph above. In a video where he tests the Siraya “Blu” resin, Stefan found that Siraya’s tough resin was stronger than some FDM materials like ABS and ASA.
More Than Material
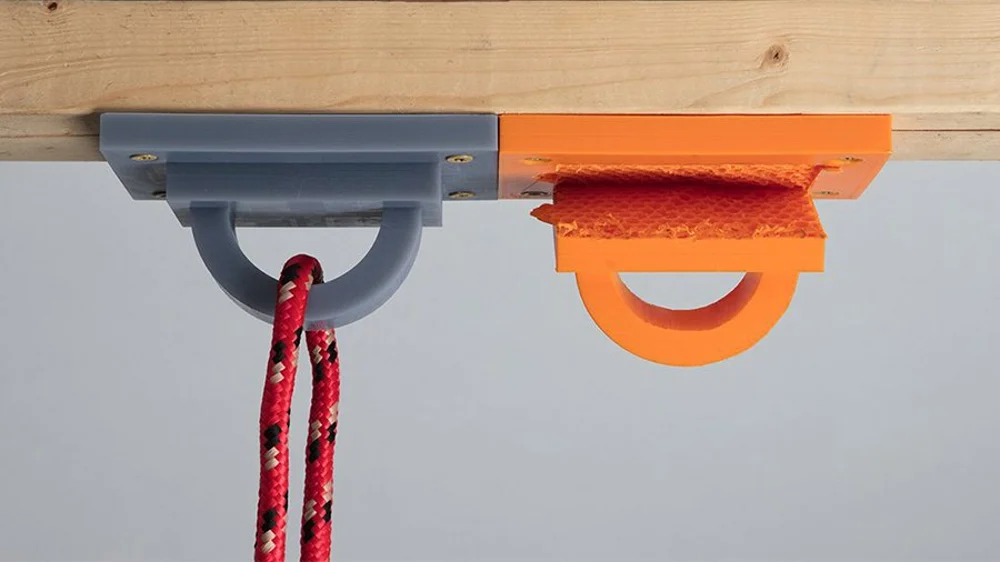
Although the material properties greatly determine the toughness of a given print, there are other important factors that can affect mechanical performance.
Design & Geometry
The way a print is designed greatly influences its strength. For example, a certain component can be strengthened by allocating more material to the regions where stress will be concentrated. The design freedom allowed by 3D printing means computational tools like topology optimization, which automates this process, are frequently used.
3D Printing Parameters
The way the part is fabricated also relates to how well it can withstand external forces. In a 3D printing context, this is determined by the printing settings defined during slicing. It’s well known that larger layer heights have a strong influence on FDM’s part strength, and this is also true for resin 3D prints.
While it’s a fairly common procedure in resin printing to hollow models in order to save material, this doesn’t apply to functional parts. Most FDM slicers include several infill density and pattern options to reduce material and printing times, yet these are rarely seen in slicers for resin printing. Still, third-party slicer ChiTuBox does include these features, which provide the possibility of increasing toughness while still optimizing material usage.
Anisotropic vs. Isotropic
Anisotropy is when an object or material’s physical property has a different value when measured in different directions. This happens in 3D printing when objects printed by FDM technology display varying physical properties depending on the part’s build direction. More specifically, lower adhesion is created between layers on the Z-axis, which causes a lower pull strength when compared to the X- or Y-axis. As you can see in the image above, when weight is applied to an FDM print that isn’t oriented or modeled in such a way that takes anisotropy into account, it can break.
When it comes to resin printing, however, the opposite is true because resin is isotropic. During his testings with Siraya’s Blu, Stefan Herman verified this by showing experimentally that the parts are equally strong regardless of the build direction. Formlabs also came to the same conclusion, which is discussed in their article about SLA printing’s isotropic property.
Hard Stuff
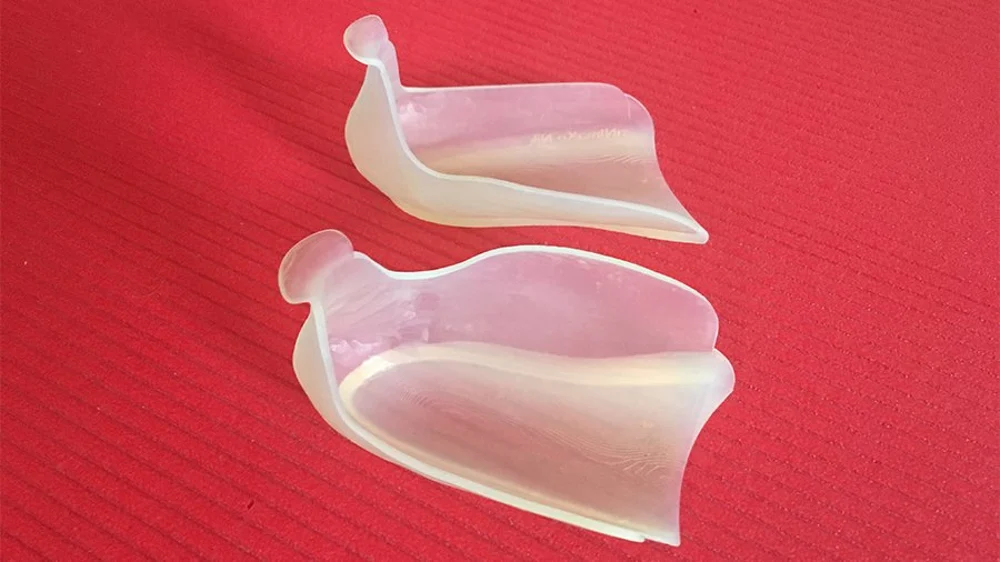
Given all that we’ve learned, we hope it’s clear that by choosing the right resin, SLA 3D printing can produce prints just as strong as FDM can.
To illustrate this conclusion, here’s an inspiring example of how resin can produce strong, functional, and detailed parts in the world of orthotics. You can also check out our article on the most promising orthotics projects.
Slovenian Matej Vlašič’s son Nik was born with cerebral palsy and couldn’t stand or walk without assistance. Mr. Vlašič created custom-made ankle-foot orthoses (AFOs) for Nik and used a Formlabs resin 3D printer to print them into reality. After around a year of development, the final design allowed Nik to walk within a few days.
Like many orthotic devices, AFOs must be strong enough to provide support while withstanding the full body’s weight during motion. Mr. Vlašič used Formlabs’ durable resin, which proved to be both tough and comfortable, even for long periods of usage.
From this success, Mr. Vlašič founded the company Animake. He and his team provide diagnostic treatment and 3D printed orthotic devices that help other children in need of custom AFOs.
Best Options
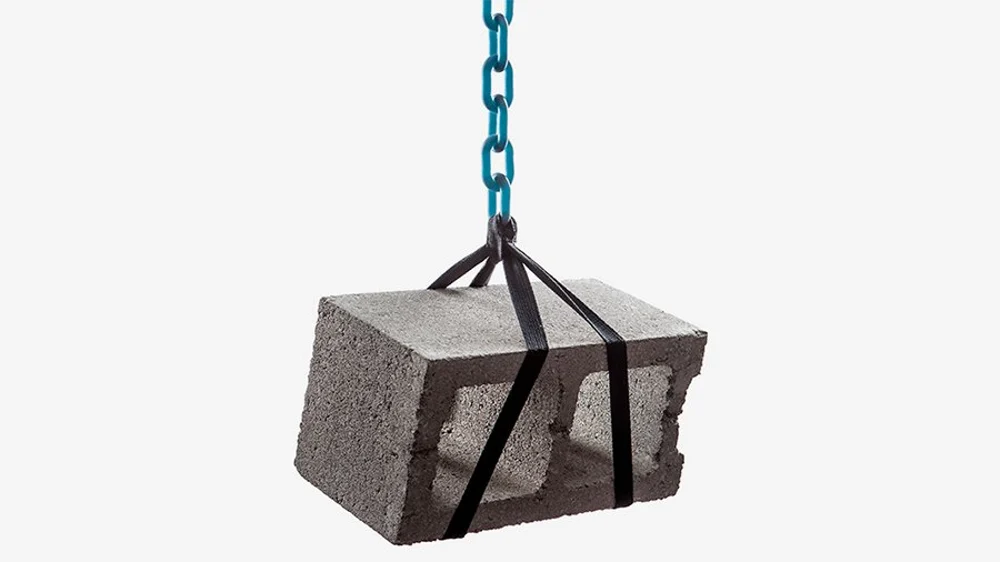
Source: https://all3dp.com/2/sla-3d-printing-how-strong-is-resin/