Topology optimization provides solutions to the most common engineering issues. Learn what it is, how it works, and why should it be used!
Less Is More
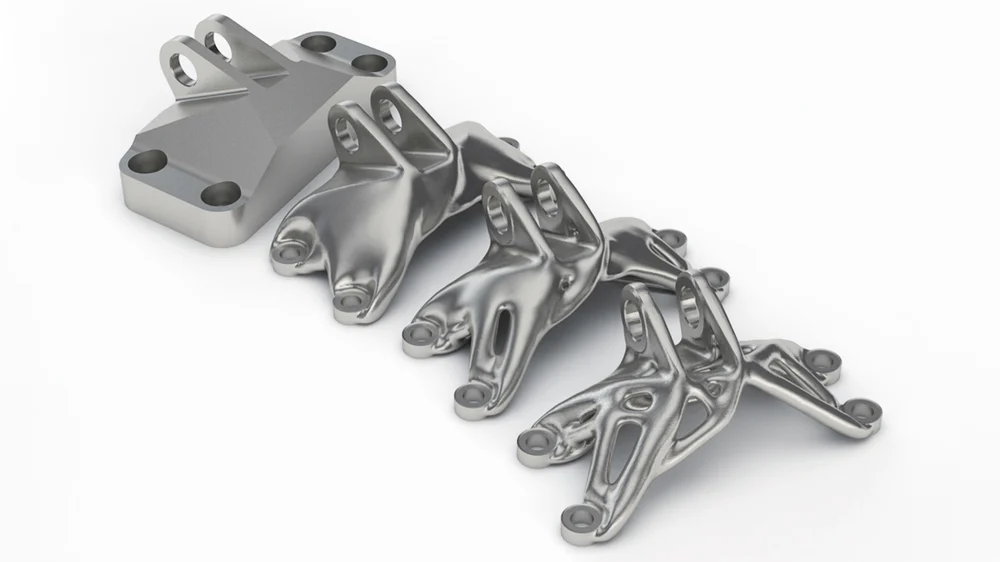
Plain and simple, topology optimization (TO) is the algorithmic process of optimizing a mechanical component or part, usually through material reduction. This is calculated according to the mechanical stresses the part will be subjected to during regular function. TO can be categorized as a subfield of the broader field of structural optimization.
TO is all about performance and efficiency. It mathematically solves one of the most common engineering problems there is: how to make a part strong enough while using the least amount of material, thereby reducing costs. For this reason, it’s used across many industrial sectors, but especially in the aerospace industry where weight reduction is essential.
In the 3D printing world, topology optimization is the design tool behind those oddly shaped components you might have noticed. Until very recently, TO was available only through costly software programs intended for professional applications. With the growing impact of the open-source and maker movements, some of these tools are now much more accessible.
In this article, we’ll provide an in-depth exploration of topology optimization tools, including real-life applications, and some popular software programs that make use of this method. But first, let’s get a deeper understanding of how TO works its magic.
How It Works
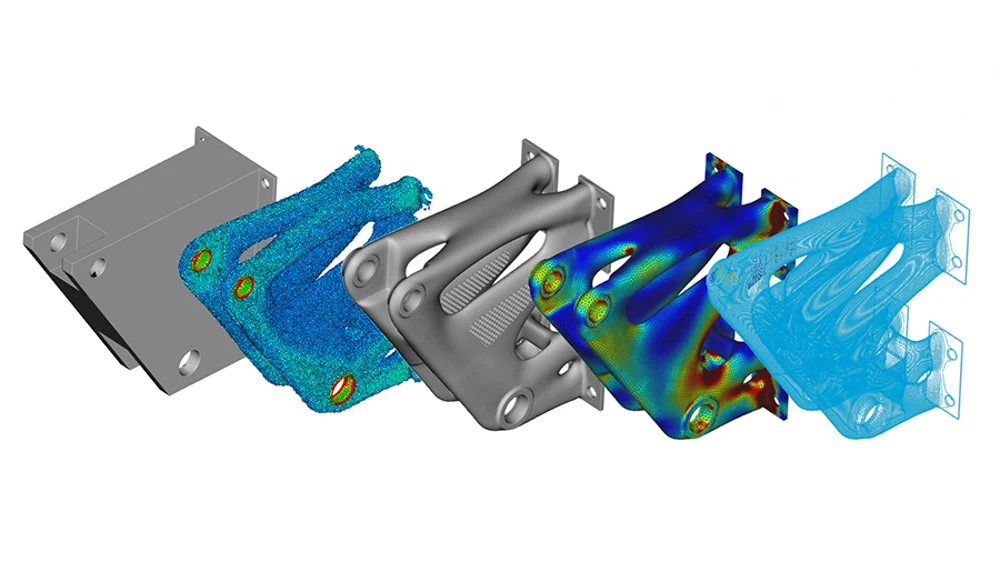
While there are many different topology optimization methods, perhaps the most practical are FE-based techniques. FE stands for finite element, which relates to the finite element method (FEM), yet another powerful numerical method widely used for mathematical and engineering problems. It’s the foundation of the computer-aided engineering (CAE) simulation software we know and use today.
In practical terms, TO makes use of finite element analysis (FEA) simulations to assess which areas of an object are not structurally crucial. The initial FEA simulates the stress distribution of an object submitted to external forces (previously inputted by the user). With these results, TO algorithms can verify which sections of the object are less subject to internal stresses and therefore potentially able to be removed.
The algorithm is constantly evaluating the structural stress distribution as it removes material, in order to assess the resulting effects. This is done through many individual steps until stable geometries are obtained according to the loadings and boundary conditions set up previously.
Topology optimization tools are generally used in a two-phase design process. The first run is usually performed to provide a glimpse of the optimal geometry and guide the user in the direction of the best design possible. The second run is more assertive in terms of final part detailing. This approach has proven to be very time-efficient, though time is only one of many advantages of this process.
Advantages
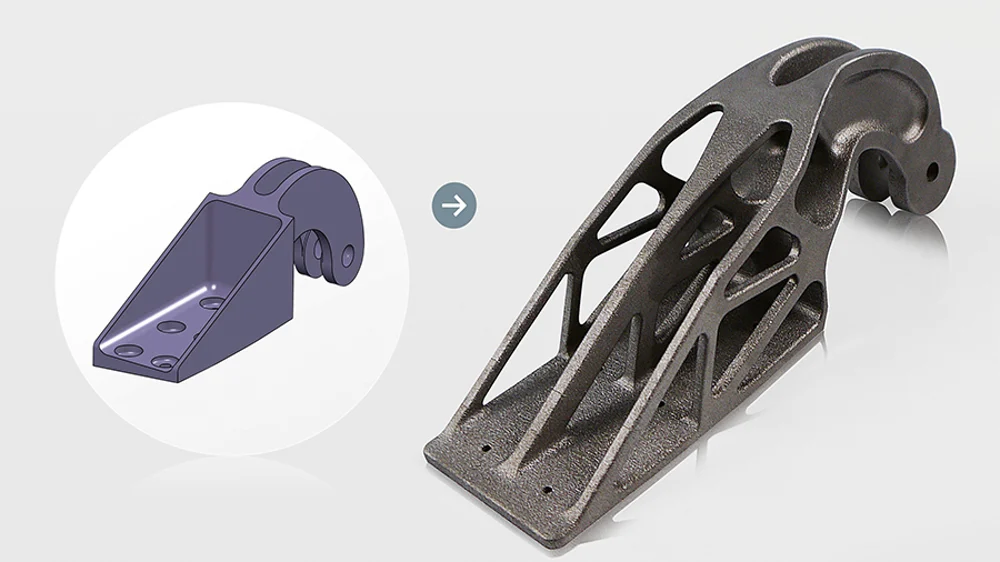
Now that we understand a bit more the hows, let’s turn out attention to the whys: What are the true advantages of using topology optimization?
Material Reduction
Every mechanical part or component potentially weighs more than it needs to unless it’s been topologically optimized. Lightweight structures not only reduce material costs but also limit manufacturing resource consumption. Generally speaking, lighter moving parts generate less friction and require less energy to be put in motion. Plus, the supply chain is also benefited, as lighter parts are easier and cheaper to transport.
Shortened Design Process
Topology optimization methods dramatically reduce the engineering costs associated with new parts and product development. The automated process is capable of producing considerably better-performing parts in a fraction of the time an experienced design team would be able to. That said, TO is only a numerical tool that still requires a significant amount of human expertise to use.
Maximum Performance
The optimal design of a given part is often not intuitive and usually involves complex and organic shapes. Topology optimization algorithms don’t consider aspects like aesthetics and violate common design rules (such as uniform thickness) in favor of performance. TO also makes the use of new manufacturing processes like additive manufacturing and 3D printing.
Truly, topology optimization goes hand in hand with 3D printing. The complex geometries resulting from TO methods are only capable of being produced through additive manufacturing processes, while traditional design practices aren’t able to make the best use of the design freedom provided by these new processes. It follows that with advancements in industrial additive manufacturing processes, topology optimization has been getting more attention.
Software
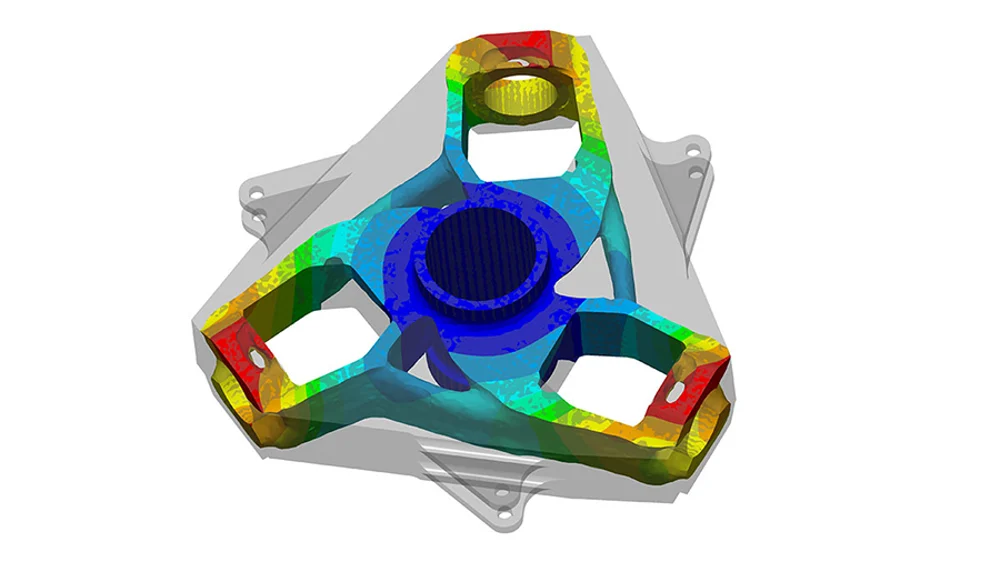
All the intricate calculations involved in topology optimization are run through specific software that usually requires a 3D FEA platform to work with. These tools can be either stand-alone programs or CAD-integrated modules.
One of the pioneers of TO capability is Altair’s OptiStruct module for Hyperworks. The tool was first commercially available in 1994, and had the General Motors Powertrain division as its first customer. Another major player in topology optimization is Dassault Systèmes, now responsible for multiple TO modules such as Tosca and ATOM for Abaqus.
Some popular CAD programs like Solidworks and Creo have built-in structure optimization tools in their simulation modules. These tools, although not as robust as the capabilities of stand-alone TO software, do present great auxiliary tools that provide meaningful insights to the designer during development.
Autodesk’s Fusion 360, an old friend to 3D printing users, also has built-in topology optimization features. The good news is that Fusion 360 is completely free for students, hobbyists, and startups generating less than $100,000 per year, making TO capabilities accessible to many.
Aerospace Applications
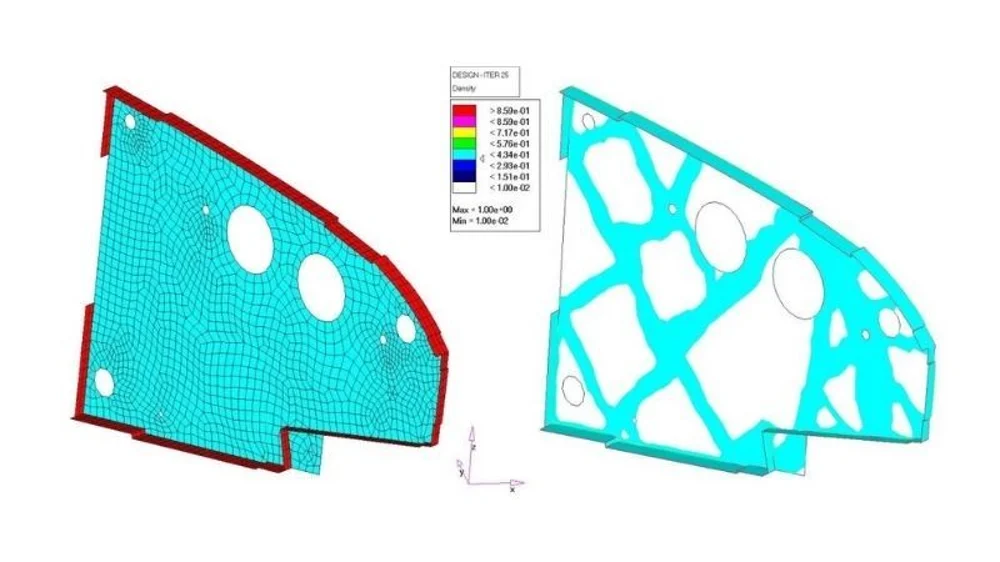
We couldn’t end without exploring a real-life application of TO. While the automotive sector has probably the largest number of topologically optimized parts around, let’s instead look at an example from the aerospace industry, where mechanical parts are subjected to much higher stresses and harsher conditions.
The design process of the Airbus A380 droop nose ribs is well known among engineering enthusiasts, as it was the first major application of topology optimization. This wing-structure part was optimized in collaboration with Altair, and is said to have saved over 500 kg per aircraft.
The optimization followed the two-phase process we described previously, and, interesting enough, the major weight savings were reportedly achieved during the first preliminary run. Other aerospace examples include the Airbus A320 nacelle hinge bracket, responsible for heavy-lifting during regular operations.
Now, the next time you catch a flight, you’ll know that those weird-looking parts are both purposefully designed and actually saving a huge amount of weight.
Source: https://all3dp.com/2/topology-optimization-simply-explained/