Nylon is known as a strong and versatile material. Read on to learn about nylon 3D printing and how parts are created with FDM, SLS, and MJF.
A Tough Nut to Crack
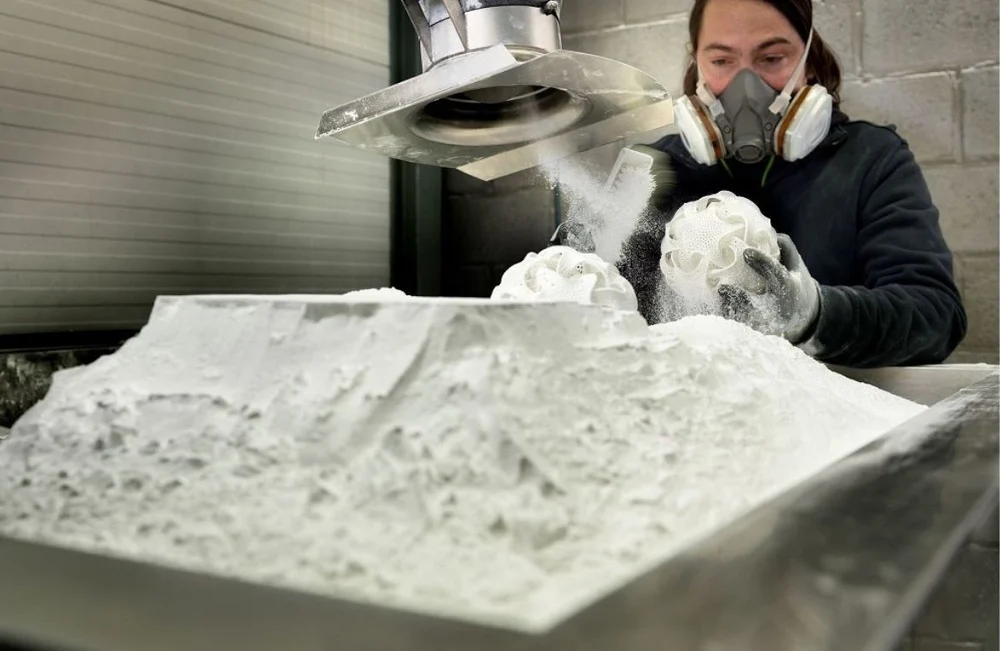
Nylon is a synthetic polymer formed from polyamides, which are polymers linked with amide bonds. When it comes to 3D printing, nylon is often considered an “advanced” material, as printing requires some skill and specialized machinery. Nylon can be 3D printed either from powder or filament.
PHYSICAL PROPERTIES
Despite being slightly tricky to 3D print, the effort is rewarded by the material’s properties. Nylon is a popular choice in industrial 3D printing as it’s strong, durable, and abrasion-resistant. If printed thin enough, it can provide decent flexibility while maintaining toughness.
Nylon’s low coefficient of friction also means it’s well suited for making functional moving parts. Therefore, nylon is often used for making functional prototypes, living hinges, gears, and similar end-use parts.
CHEMICAL PROPERTIES
To completely understand nylon 3D printing, it’s important to know about two other properties. One, it has a high melting point, and two, it’s hygroscopic, meaning it loves to absorb moisture. This second property can be an advantage, but also has its cons. While the surface of a printed part allows paint to adhere very well, it also absorbs moisture from the air, which can eventually affect the performance of a part.
In this article, we’ll be going deeper into nylon printing and the different technologies that you can print it with. Let’s get started!
Technology Choices
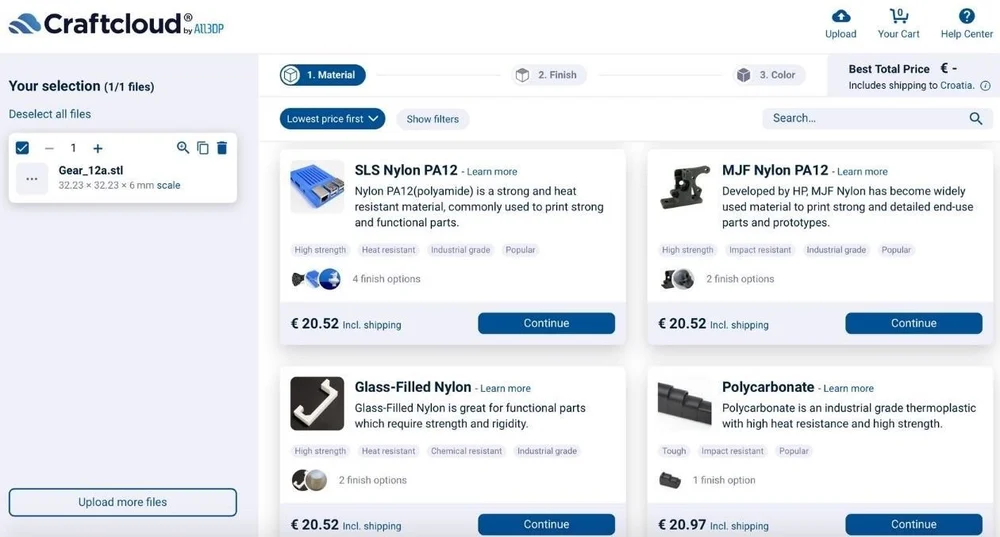
Nylon 3D printing can be achieved with fused deposition modeling (FDM) using nylon filament, or with selective laser sintering (SLS) or Multi Jet Fusion (MJF) using nylon powder. Below, we’ll explain the differences between these technologies, how they’re used to create nylon parts, and the pros and cons of each.
If you need parts 3D printed in nylon but don’t have the setup to do it yourself, check out FacFox, a 3D printing service marketplace. Craftcloud connects you with 3D printing partners all around the world, giving you a choice of technologies and finishes. Once you upload a design and input your requirements, the instant quote generator will display the best prices and fastest delivery times so that you can choose your supplier.
In the case of printing with nylon, beyond the usual FDM options, there are suppliers printing with SLS and MJF as well as PA 12 and glass-filled nylon powders. So now, let’s learn what all that means!
FDM
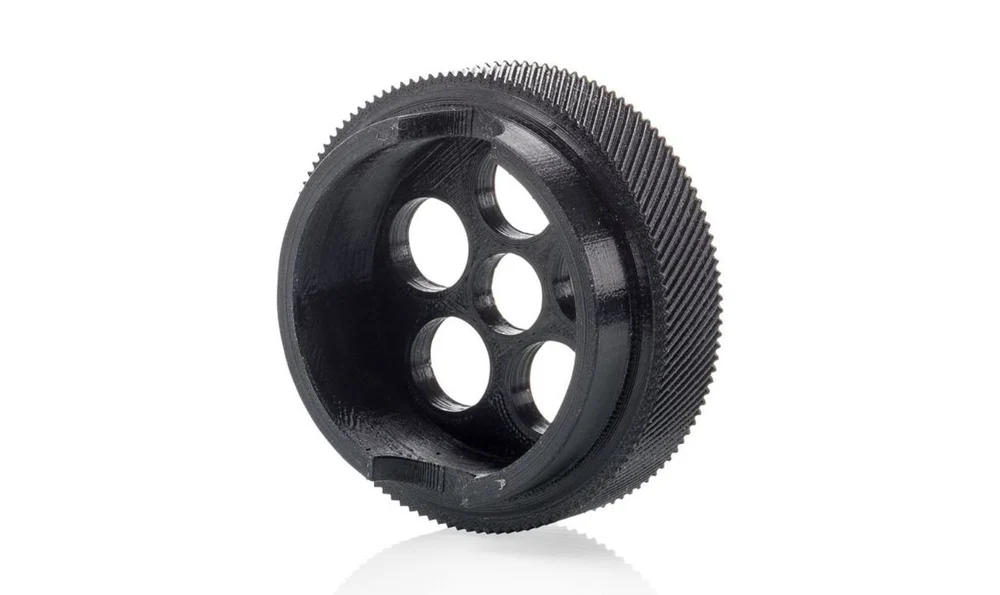
3D printing with nylon can be expensive to get into because MJF and SLS printers, as well as the powders they use, are far from cheap. Luckily, it’s possible to 3D print nylon using an FDM printer paired with special nylon filament.
FDM 3D printers use filaments, which are melted and then extruded through a nozzle onto the build platform in layers, until the part is complete. While 3D printing nylon on an FDM printer is much more accessible than SLS or MJF, the quality of an FDM-printed nylon part is not as impressive.
Firstly, not all FDM printers can handle nylon filament with ease. It’s important to have a quality (all-metal) hot end that can handle temperatures above 250 °C. Apart from that, nylon is also prone to warping, so bed adhesion is an issue of its own.
Nylon filament comes in different variations, the most common being PA 6 and PA 66. Both of these have the standard nylon properties of strength, abrasion resistance, and low coefficient of friction, but come with one substantial flaw: high moisture absorption.
Storage & Printing
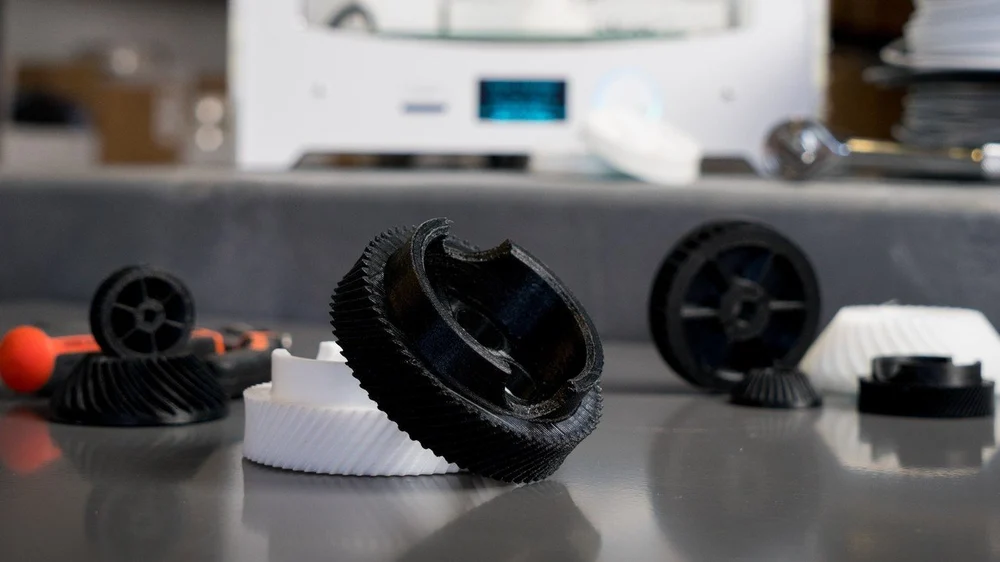
High moisture absorption can have a negative impact on the filament in the form of degradation. When degraded, filament starts to lose its properties, and nylon filament can start to degrade in a matter of hours. To prevent such a scenario, proper storage is crucial.
A simple plastic airtight container is a good solution when the filament is not being used, but what to do when printing? The ideal solution is a storage unit with humidity control, which also allows the filament to get into the extruder. If it’s too late, and your spool has already absorbed too much moisture, it might be able to be saved if you properly dry your filament.
Once you’ve got the storage figured out, it’ll be time to start printing with nylon filament. Although it always depends on the exact printer and material you’re using, and you should always consider the manufacturer’s recommended settings, here’s an overview of basic nylon printing settings:
- Nozzle temperature: 240-290 °C
- Bed temperature: Up to 65 °C
- Bed surface: PVA glue stick, Magigoo, Garolite, 3DLac
- Print speed: 25-50 mm/s
- Fan speed: 0-50%
- Enclosure: Recommended, but not necessary
Working with nylon is a bit difficult with an FDM printer, but if you have the equipment, the material is well suited to SLS and MJF.
SLS
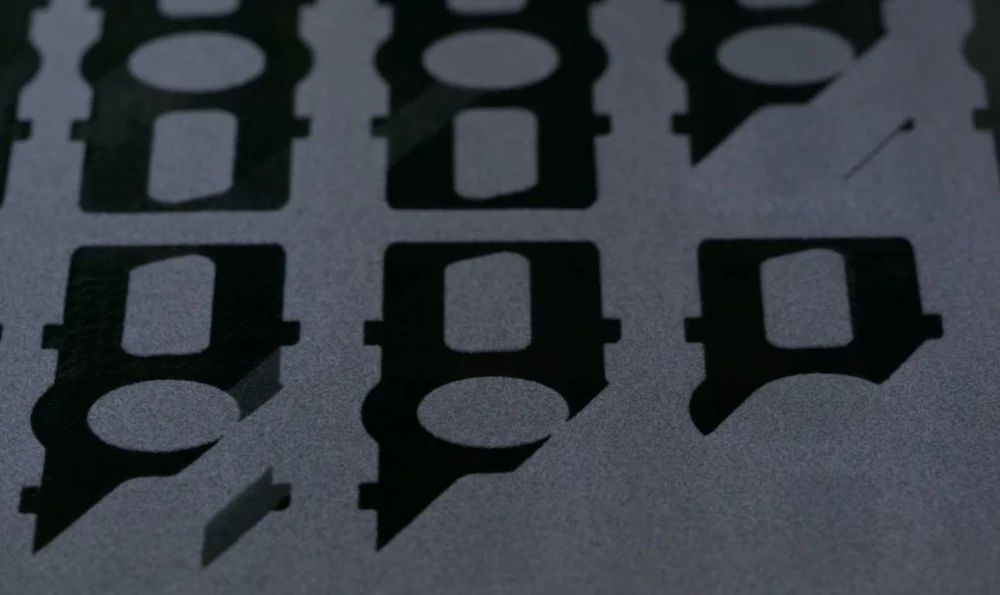
SLS uses a laser to sinter a powder, layer by layer, until the part is complete. There are different types of laser sintering technologies – there are adaptations for metal and glass – but most SLS 3D printers are oriented towards polymers.
MATERIALS
One of the main materials used with SLS is nylon, specifically PA 11 and PA 12 nylon powders. PA 11 powders are used for parts that require UV and impact resistance, while PA 12 is preferred for enhanced part strength and stiffness. There are also reinforced PA powders, also known as nylon composite powders, which usually contain either glass, aluminum, or carbon fiber particles in addition to nylon.
ADVANTAGES
When complete, parts are completely surrounded by unsintered powder, which also acts as support for the sintered parts. Luckily, with SLS it’s possible to re-use up to 50-70% of that unsintered powder for future prints. From a sustainability perspective, this is an advantage over FDM, as any material extruded as supports generally won’t be converted back into filament for re-use.
Compared to FDM, SLS is more suited for 3D printing with nylon. Nylon is great for making functional parts, and SLS both has the ability to produce complex functional parts and gains strength from using powder rather than filament.
DISADVANTAGES
The downside to SLS is the cost associated with it. Industrial SLS 3D printers often come with price tags north of $200,000. The good news is that in recent times we’ve seen more affordable solutions come to the market such as Formlabs’s Fuse 1 desktop SLS machine priced at circa $10,000. For the powders, expect to pay at least $60 per kg.
MJF
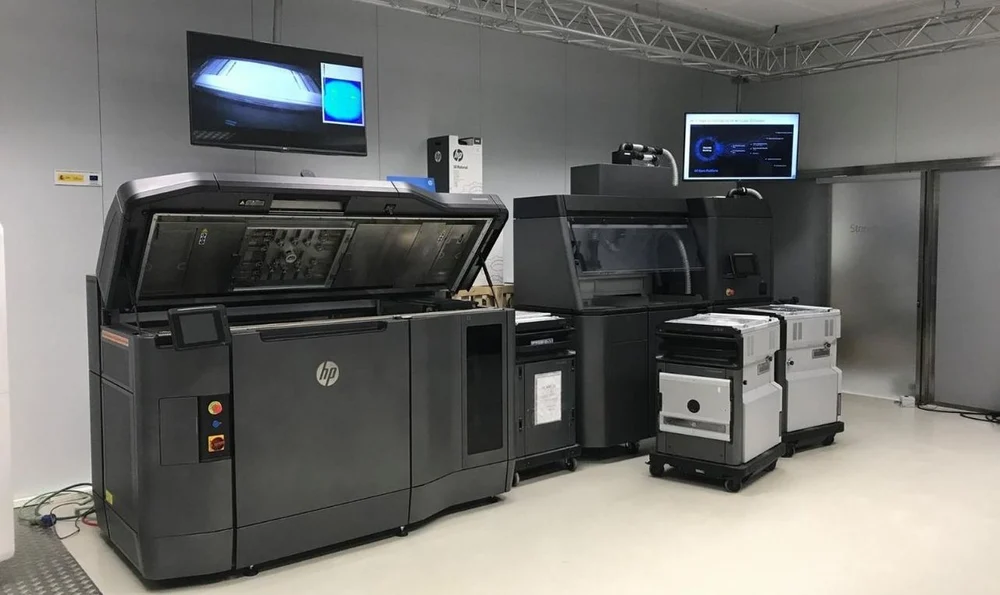
MJF is a unique powder sintering technology developed by Hewlett Packard and launched in 2016. MJF is similar to SLS, but also shares a thing or two with binder jetting.
HOW IT WORKS
Both MJF and SLS start the printing process in the same manner. A layer of powder is distributed onto the build platform before the sintering begins. However, whereas in SLS the laser would then start sintering, MJF introduces an extra step to the printing process in the form of chemical agents.
A fusing agent is sprayed on top of each fresh layer of powder, precisely where the future layers will be sintered. The fusing agent is there to help the powder absorb the energy from the printer’s heat source. While SLS uses a high-powered laser, MJF relies on a high-powered infrared light as a heat source. The infrared light paired with the fusing agent speeds up the sintering process, making MJF generally faster than SLS.
ADVANTAGES
Although both technologies are able to produce some phenomenal details on parts, MJF edges in front of SLS when it comes to details on prints. This is partly thanks to a detailing agent, which helps make edges as sharp as possible by slightly reducing the fusing potential at the very edge of a part.
After the printing is done, you’ll be able to recycle the non-sintered powder, just like with SLS. However, MJF enables even more powder to be reused, even up to 80%. Although it very much depends on the exact machines you compare, MJF machines are comparably priced with industrial SLS machines but have faster print times with potentially greater detail.
Source: https://all3dp.com/2/nylon-3d-printing-how-to-get-nylon-3d-printed/