Today, additive manufacturing (AM) offers unprecedented possibilities for the design and production of functional parts. However, to fully exploit the design complexity offered by the technology, design software, like topology optimization, is needed.
Topology optimization makes the production of stronger, lightweight parts possible. Today’s article will explore how topology optimization, coupled with 3D printing, can help engineers to reimagine their approach to designing and producing parts.
What is topology optimization?
Topology optimization is a generative design technique that optimizes the geometry of an object using mathematical calculations.
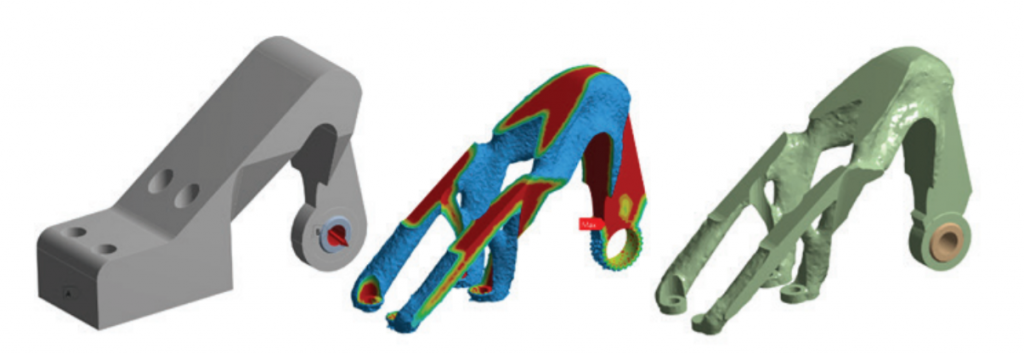
This allows the software to identify areas where the material can be removed without sacrificing part’s function or performance.
In this way, topology optimization helps to create the best possible structure of a given part.
The benefits of topology optimization
A faster design process
Topology optimization software helps to speed up the part development and design process by automatically iterating the design until it creates an optimised geometry.
By factoring performance requirements into the design right from the start and automating the design generation process, it’s possible to come up with an innovative design much faster, ultimately speeding up the design cycle.
Lighter and stronger parts
Perhaps the biggest advantage of using topology optimization is the ability to enhance part performance by reducing its weight and optimizing its strength.
By adding or removing the material in places, defined by a set of parameters, topology optimization tools allow engineers to explore endless design options and find the best possible lightweight, yet resilient, structure of a given part.
Lighter parts are sought after by many industries. In aerospace, for example, lightweight components can significantly reduce aircraft fuel consumption, while in motorsports they can radically improve racecar performance.
Additionally, the lighter the part, the less material that has been used to produce it, which brings down manufacturing costs.
Combining topology optimization and 3D printing
Traditional manufacturing approaches are often limited in their ability to produce topologically optimized designs. Such designs often feature complex shapes, that are usually impossible or cost-prohibitive to produce using machining or injection molding.
3D printing, on the other hand, is capable of producing intricate shapes without the added cost of complexity. This makes 3D printing the best technology to make the most of topologically optimized designs.
Topology optimization in practice
The combined use of topology optimization and 3D printing can be found in industries such as automotive, aerospace and medical.
Aerospace
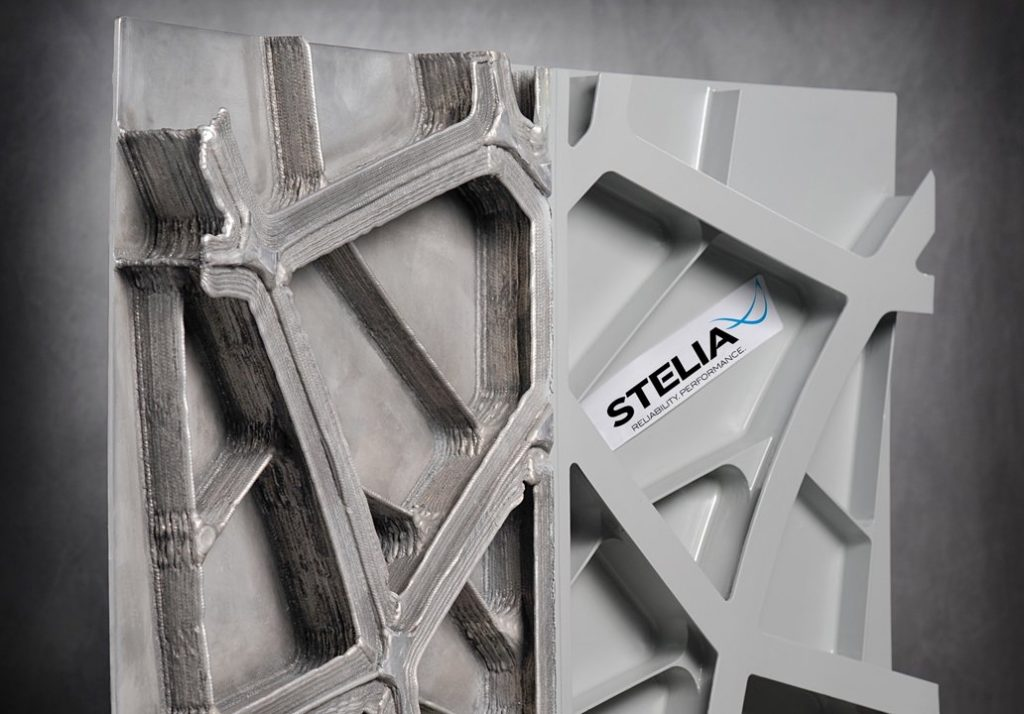
Optimized and additively manufactured components prove to be highly valuable in cutting down costs for launching satellites and space vehicles.
A good example is that of aerostructure manufacturer STELIA Aerospace, which has used topology optimization to produce aeroplane fuselage panels.
Thanks to topology optimization, designers and engineers from STELIA have been able to create stronger aircraft fuselage panels, with enhanced stability. There is also an added ecological benefit, with the topology-optimized design leading to less material waste.
Medical
Another industry to benefit from topology optimization is medical. Functionally optimized structures open new opportunities for the production of implants that mimic a patient’s bone stiffness and density.
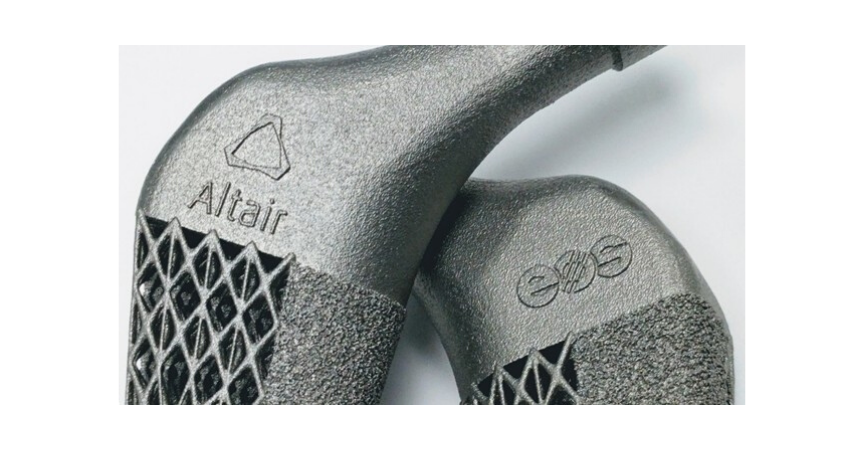
By inputting parameters like size, weight, and the expected load the implant would bear, topology optimization software was used to create a new design for a hip implant. The optimized design distributes stress and strain in a more efficient way than a generic implant.
Furthermore, topology optimization software helped to determine where the material could be replaced with lattice structures to make the implant lighter.
When tested, the optimized implant offered an endurance limit increased to about 10 million cycles. This means that the hip implant could endure jogging from Los Angeles to New York and back – twice.
Automotive
In 2018, BMW released its iconic i8 Roadster car, featuring an award-winning 3D-printed metal roof bracket.
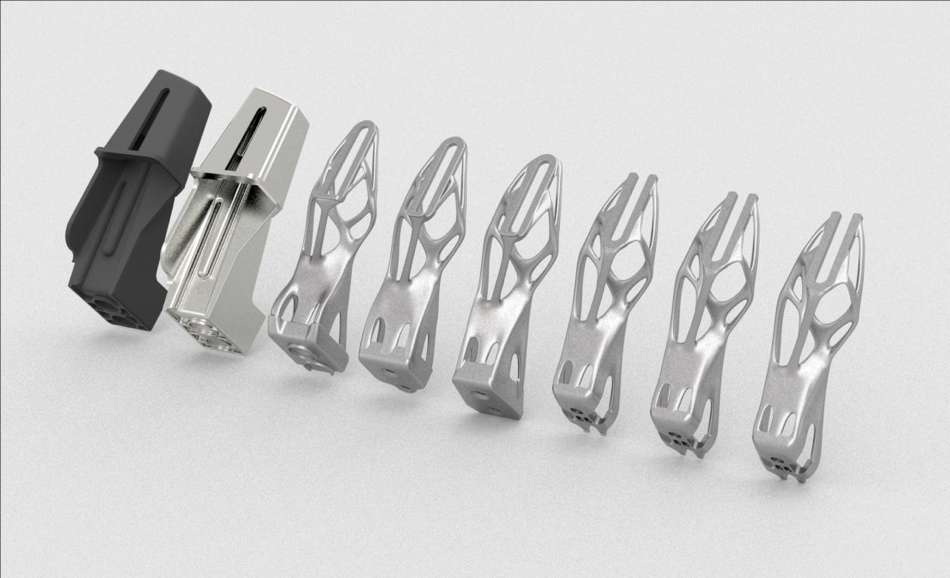
By using the software, engineers were able to input parameters like the weight, the size of the component, and the load it will take. The software then generated a design that optimized the material distribution of the part.
The design achieved by the engineering team was impossible to cast. The team found that the only way to make this design possible was through metal 3D printing.
Thanks to Selective Laser Melting (SLM) technology, engineers created a metal roof bracket that is 10 times stiffer and 44 percent lighter than the conventional alternative.
Examples of topology optimization software for 3D printing
Many IT companies providing design and simulation software for 3D printing are also developing design solutions with topology optimization capabilities. In this section, we’ll take a look at some of the promising offerings in topology optimization for 3D printing.
Altair Inspire
Altair is a global technology company that provides software and cloud solutions in the areas of product development, high-performance computing and data analytics.
What it can do
Altair Inspire offers a number of topology options including optimization objectives, stress and displacement constraints, acceleration, gravity, and temperature loading conditions.
The topology optimization software also observes manufacturing process constraints. For example, it enables design for AM with overhang shape controls to help reduce overhangs to create more self-supporting structures.
Ansys Mechanical
ANSYS is a provider of simulation software and design tools for mechanical engineering. ANSYS provides designers with an automated topology optimization tool integrated with its full suite of multiphysics software.
What it can do
Topology optimization in Ansys Mechanical allows you to take into account multiple static loads combined with optimizing for natural frequencies (modal analysis), as well as satisfy requirements for minimum material thickness. In addition to that, the software is designed to easily validate optimization results, speeding up the design process.
ParaMatters CogniCAD
The field of design and CAD software also contains a handful of startups hoping to transform the market. ParaMatters, founded in 2016, has developed generative design software, CogniCAD.
What it can do
CogniCAD reportedly offers a highly automated workflow based on in-house developed topology optimization, high-resolution finite element analysis and computational geometry.
It provides a variety of loading conditions, design goals and constraints that help to ensure the design is suitable for 3D printing.
nTopology nTop Platform
Founded in 2015, nTopology offers design software. In last May, the company released its design software, Element, which provides design analysis, lightweighting and optimization tools.
What it can do
In terms of topology optimization tool, nTop Platform allows users to apply multiple loading conditions and optimize for a variety of performance criteria including stress, displacement and stiffness.
Once the design has been optimized, the tool enables automated conversion of topology optimization results in editable geometry. According to the company, this can save you time and effort by providing a fast and repeatable process without the need for manual geometry reconstruction.
Topology optimization: a new design approach
Topology optimization software for AM has seen remarkable progress over the last few years. Both large software companies and startups are developing advanced solutions to push the boundaries of design for 3D printing.
Thanks to these advancements, companies within a range of industries are now able to take advantage of greater design freedom, faster design cycles and enhanced part performance.
Moving into the future, the capabilities of topology optimization software for AM will continue to evolve, unlocking new, powerful possibilities.
Source: https://amfg.ai/2018/04/19/topology-optimisation-additive-manufacturing/